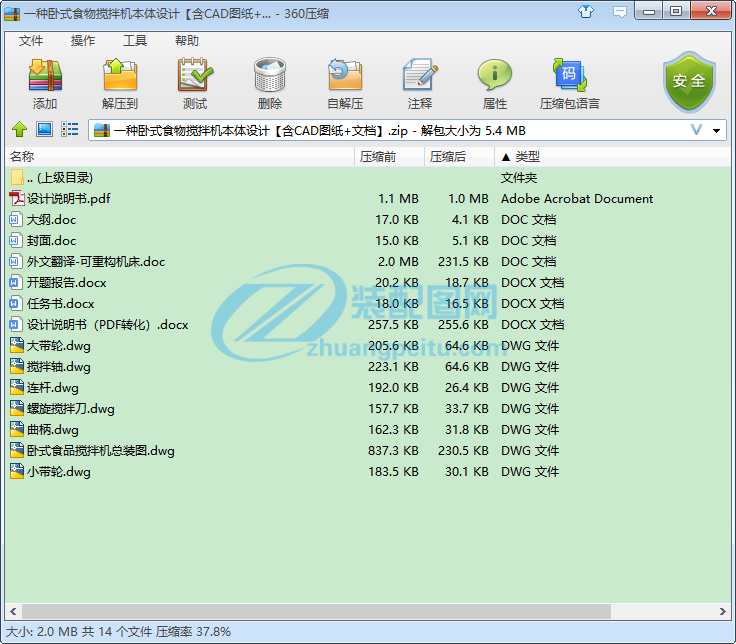
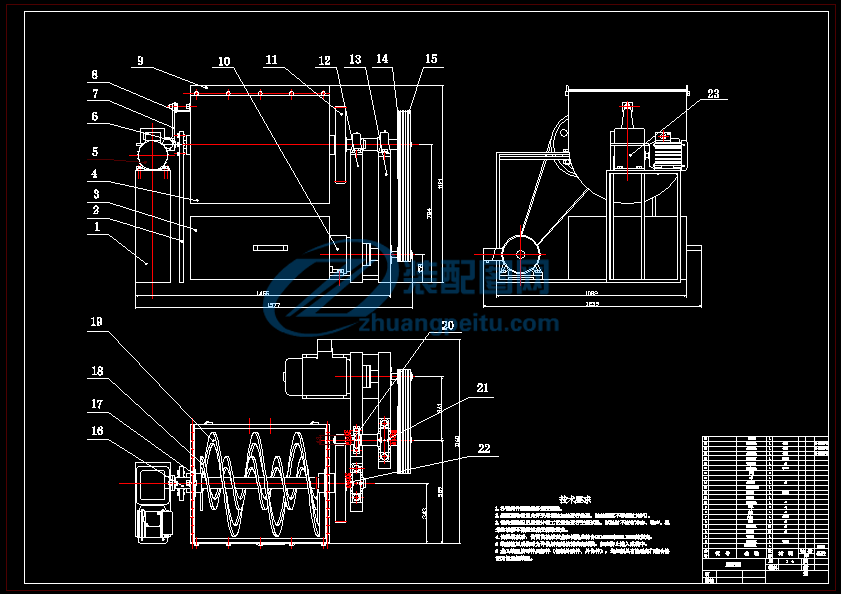
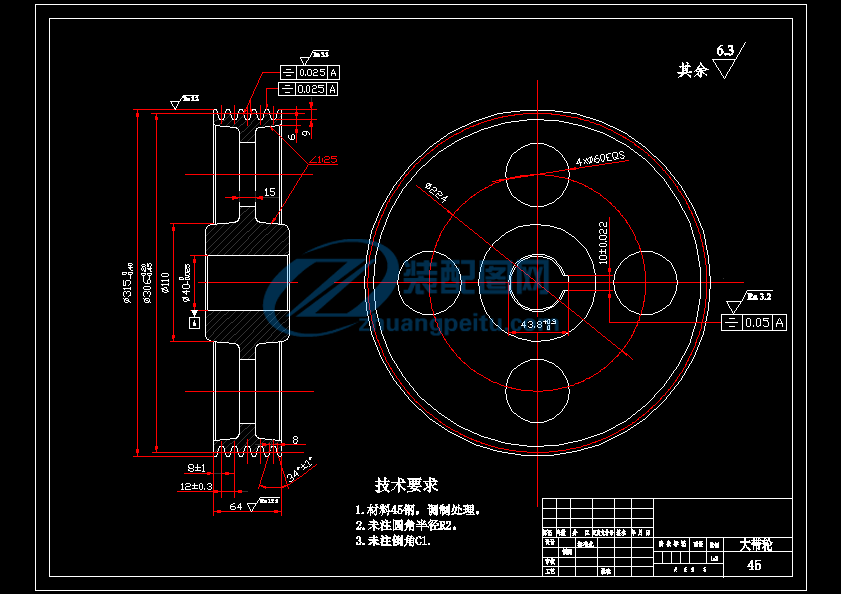
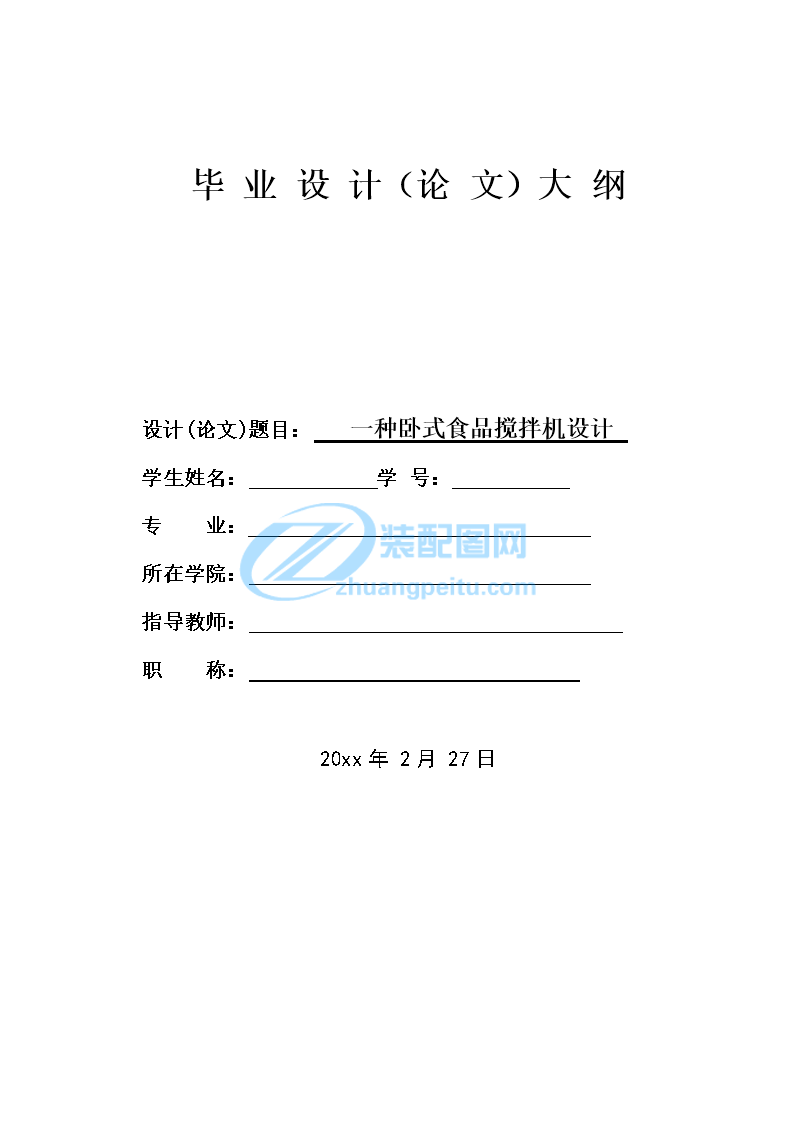
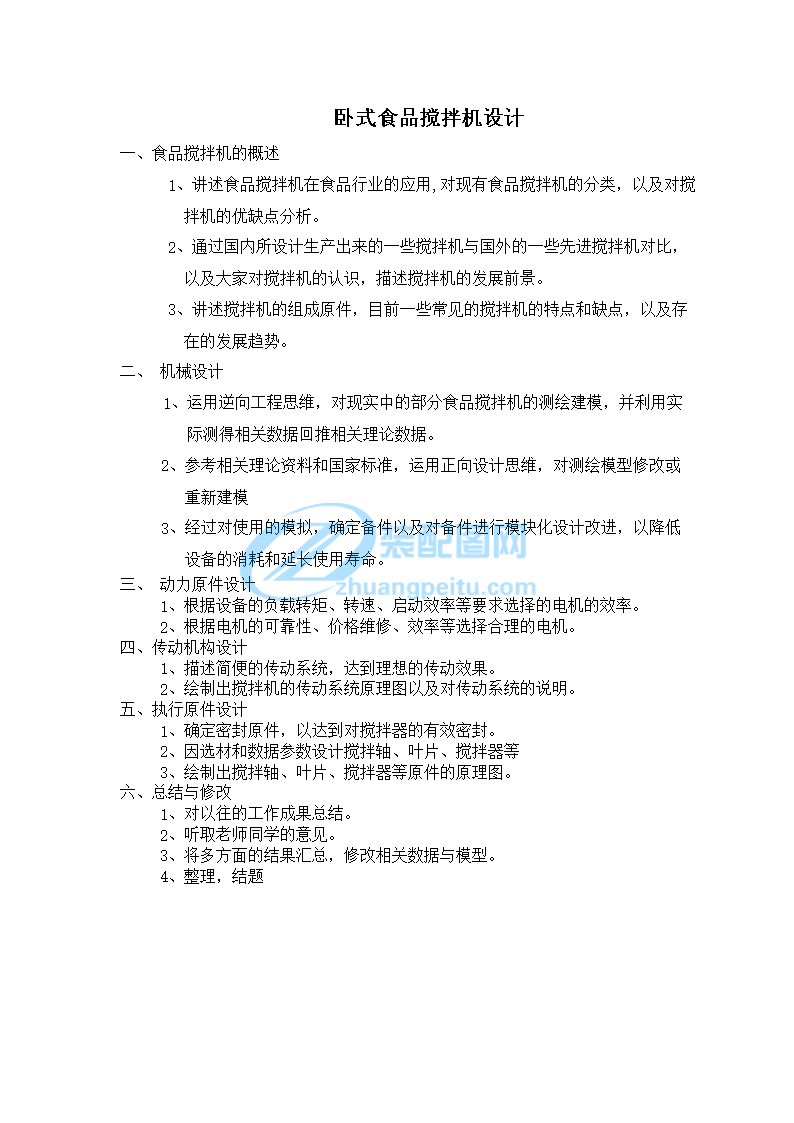
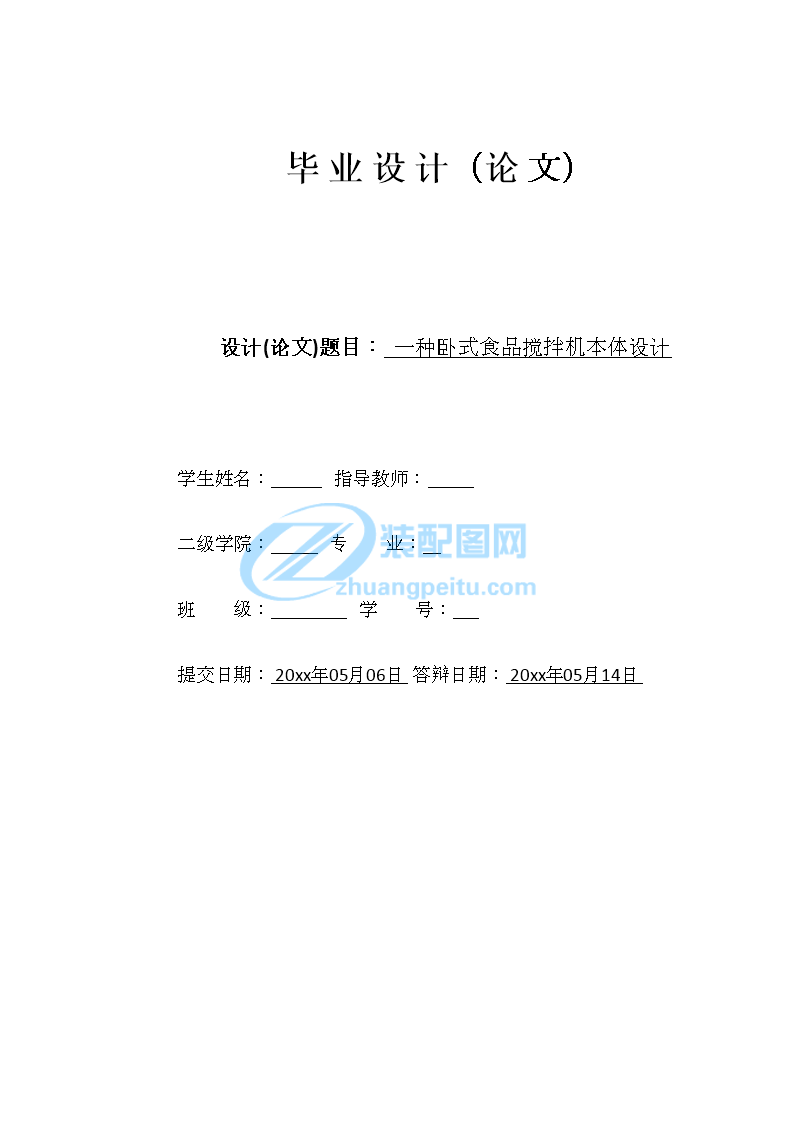
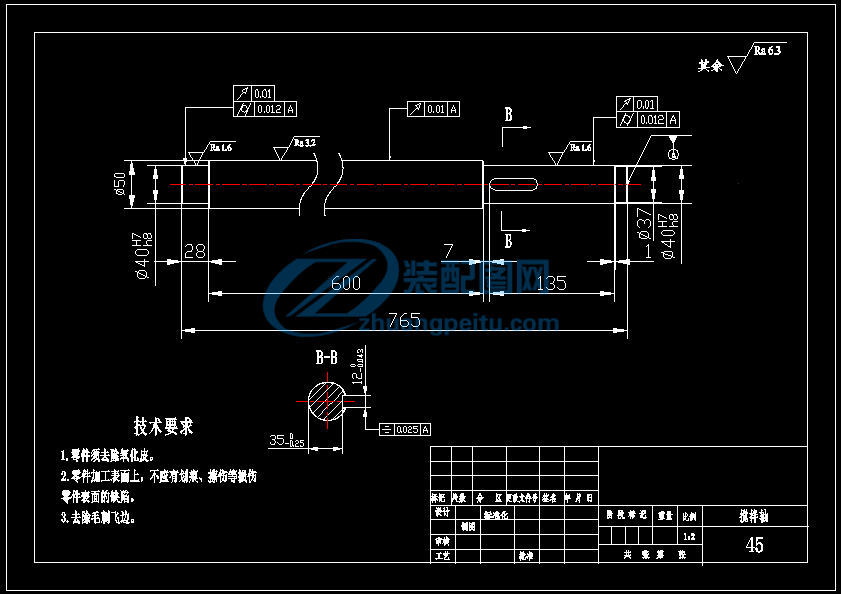

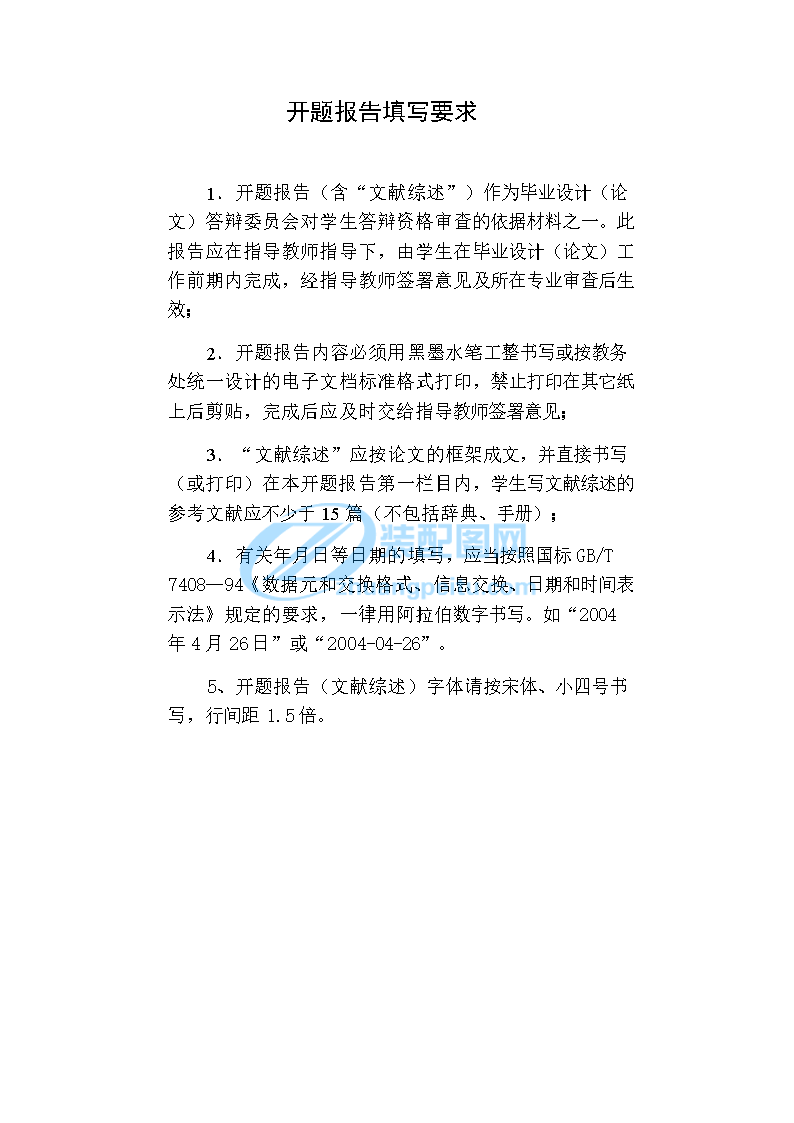
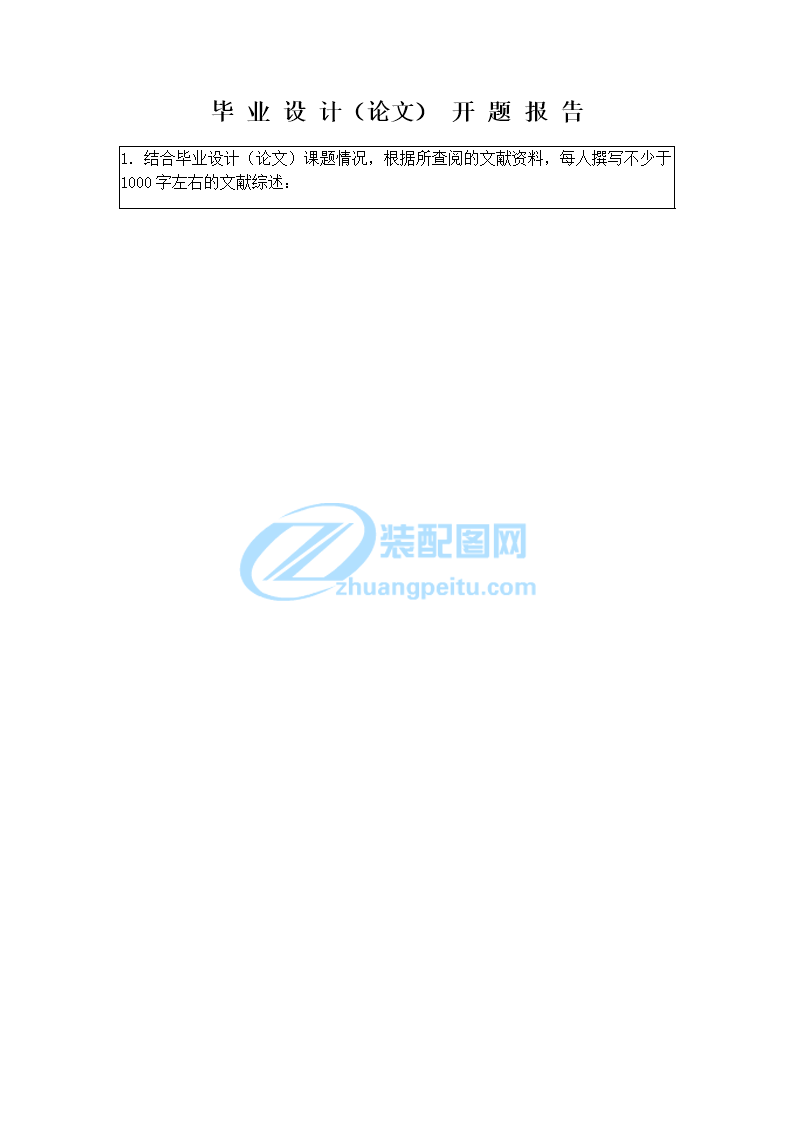
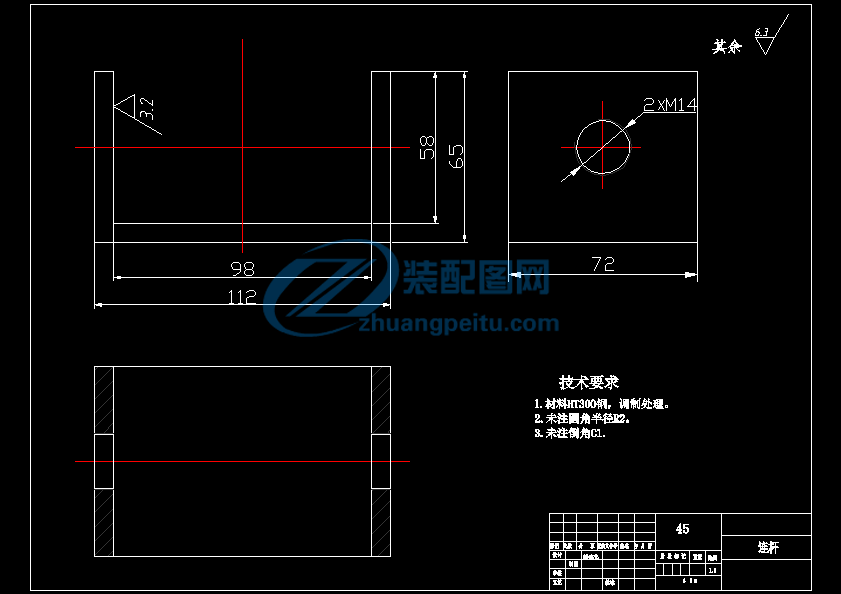
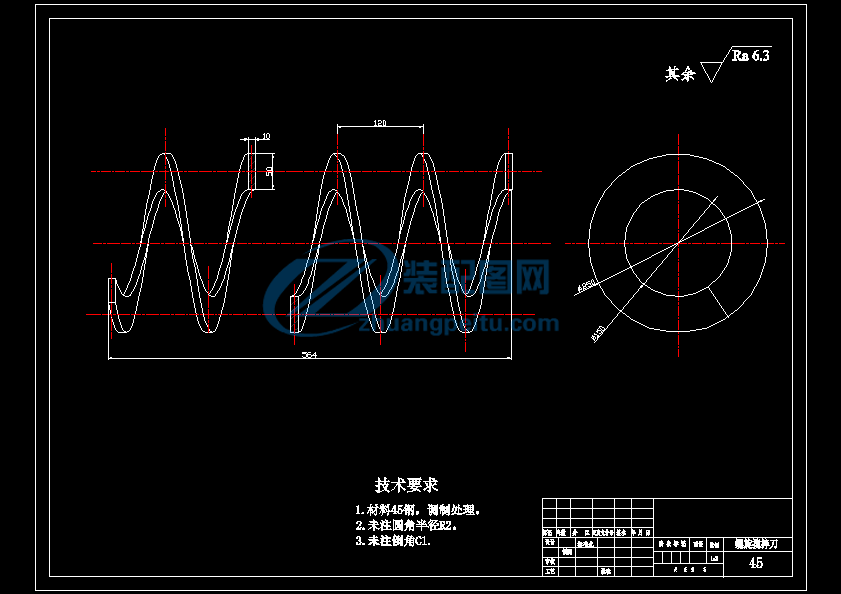
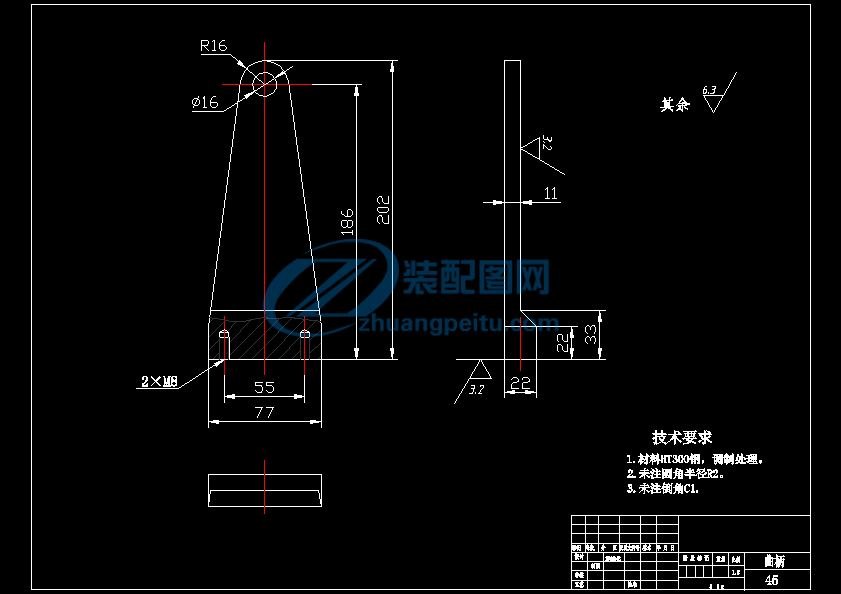

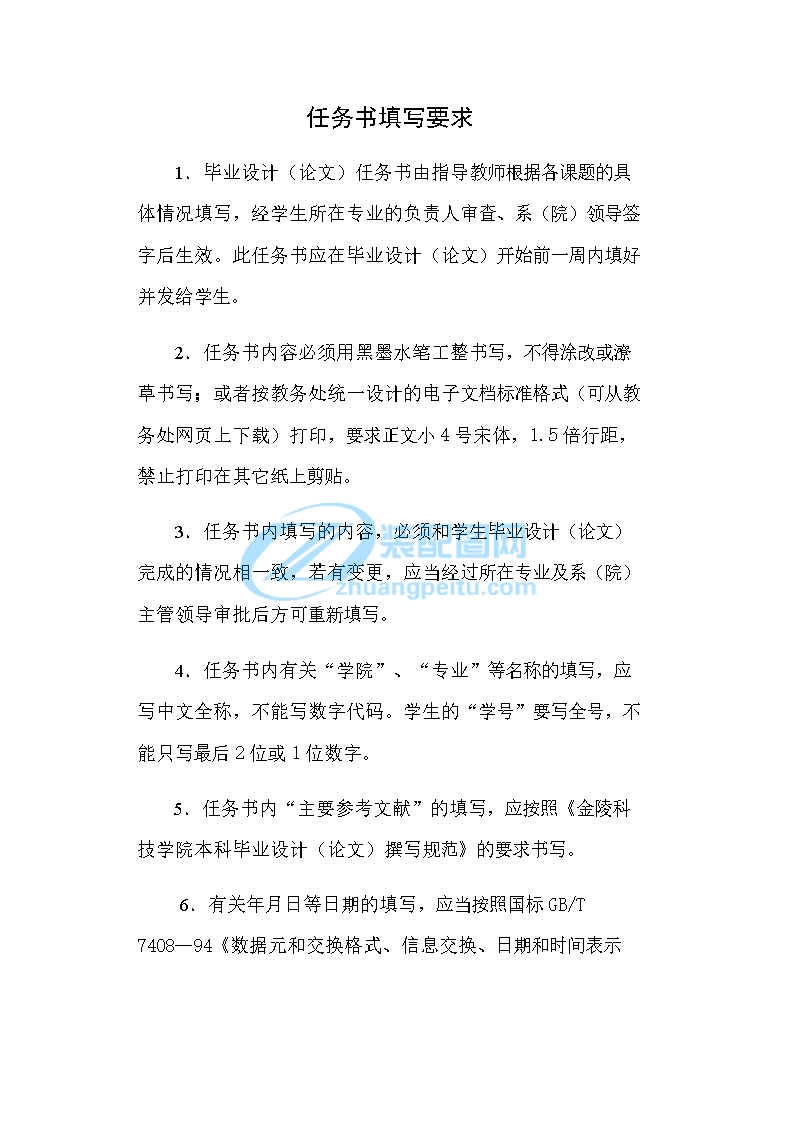
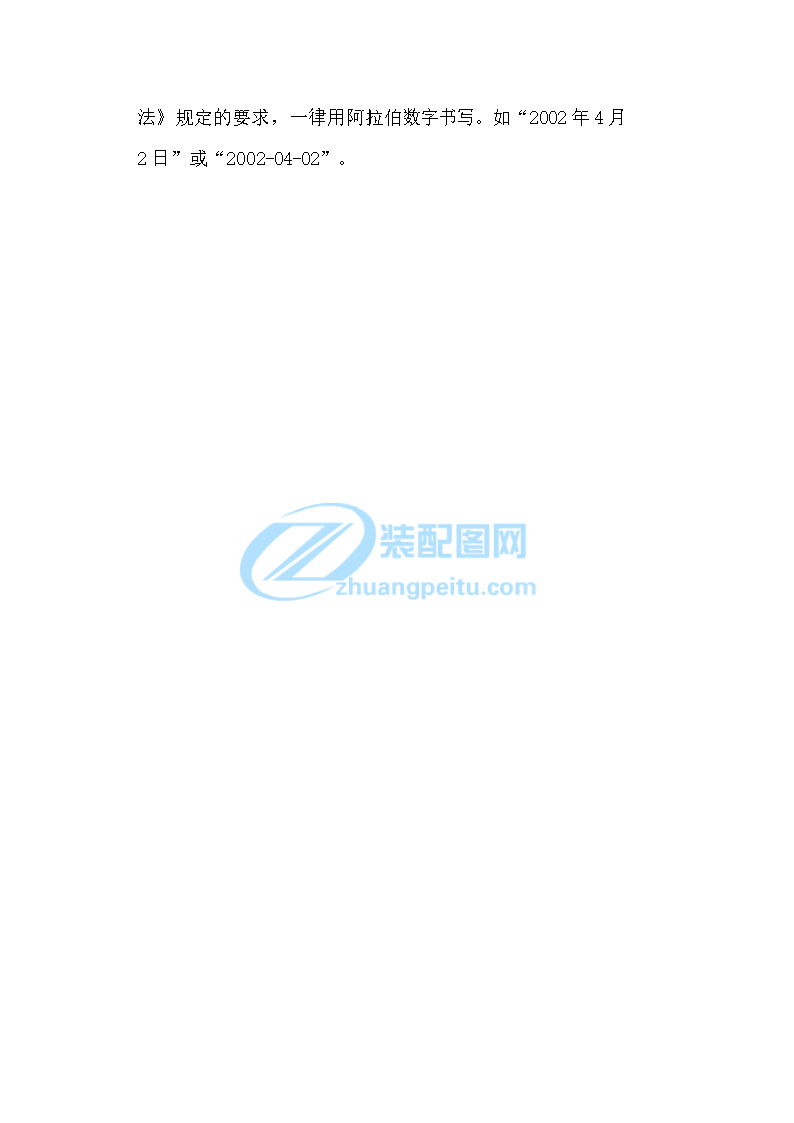
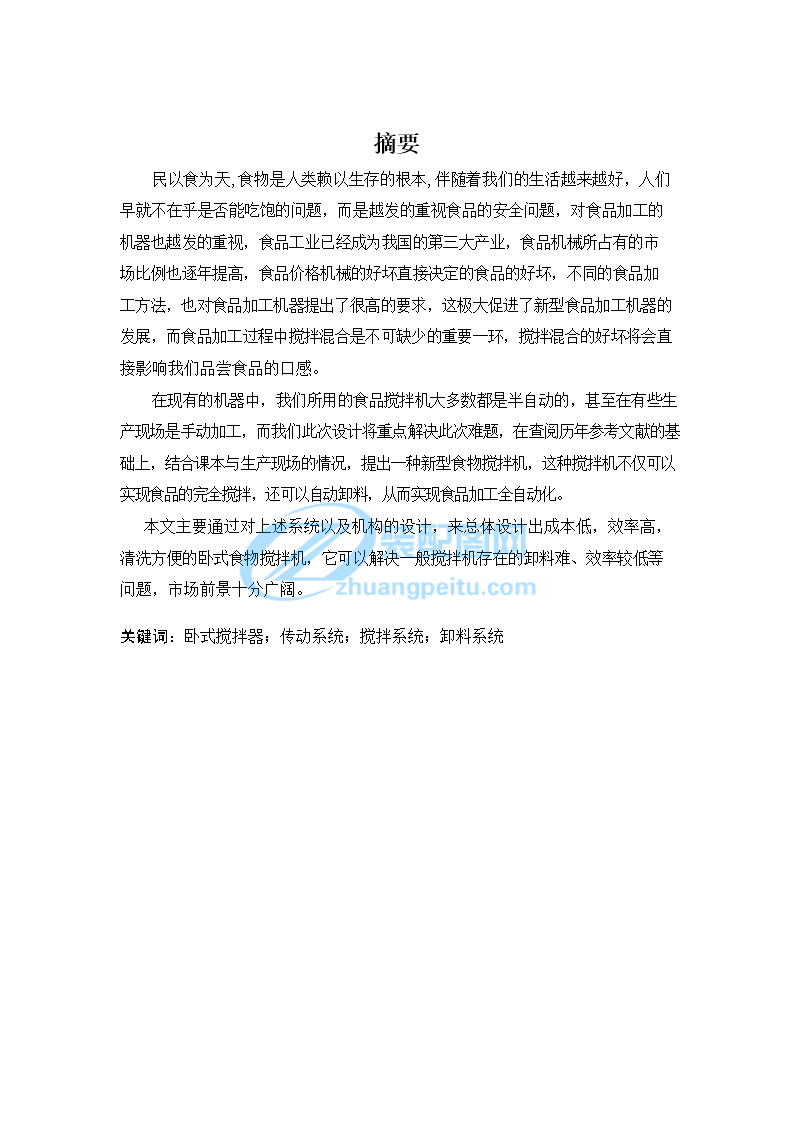
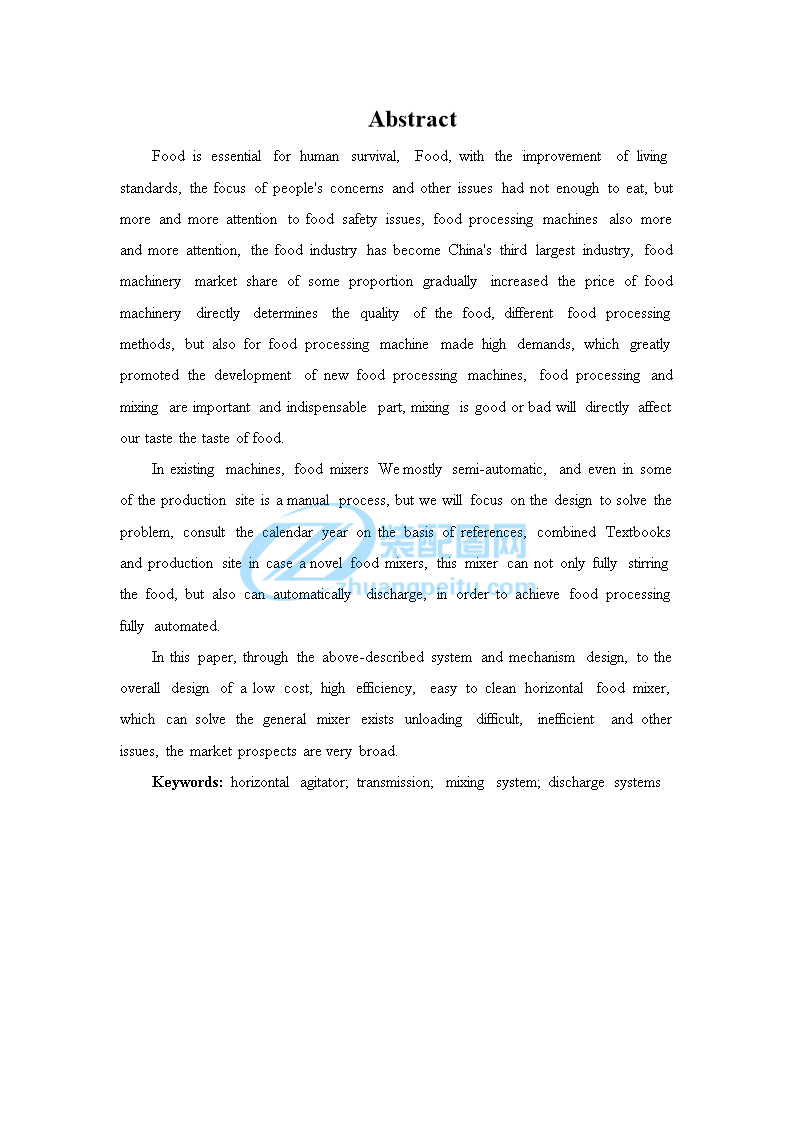

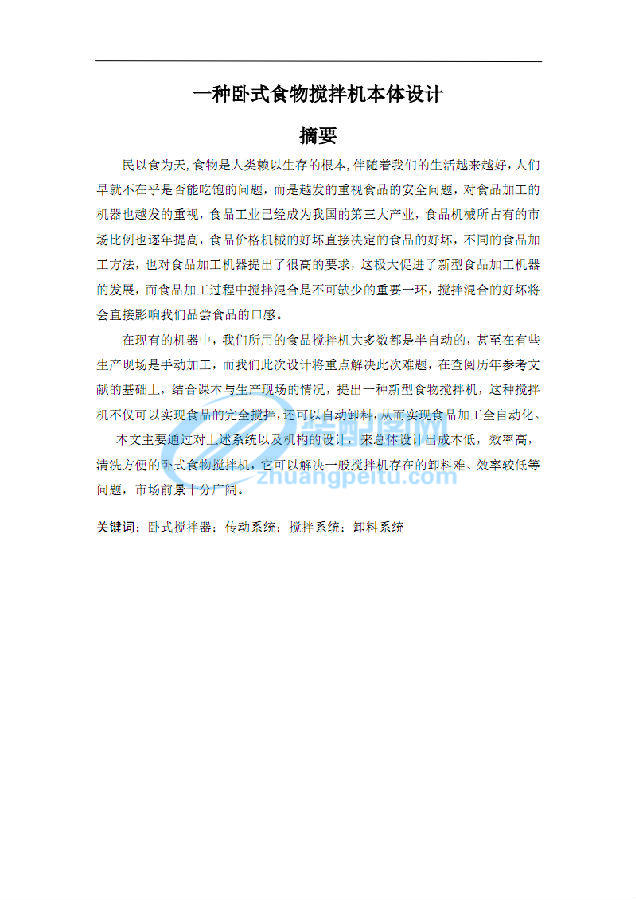
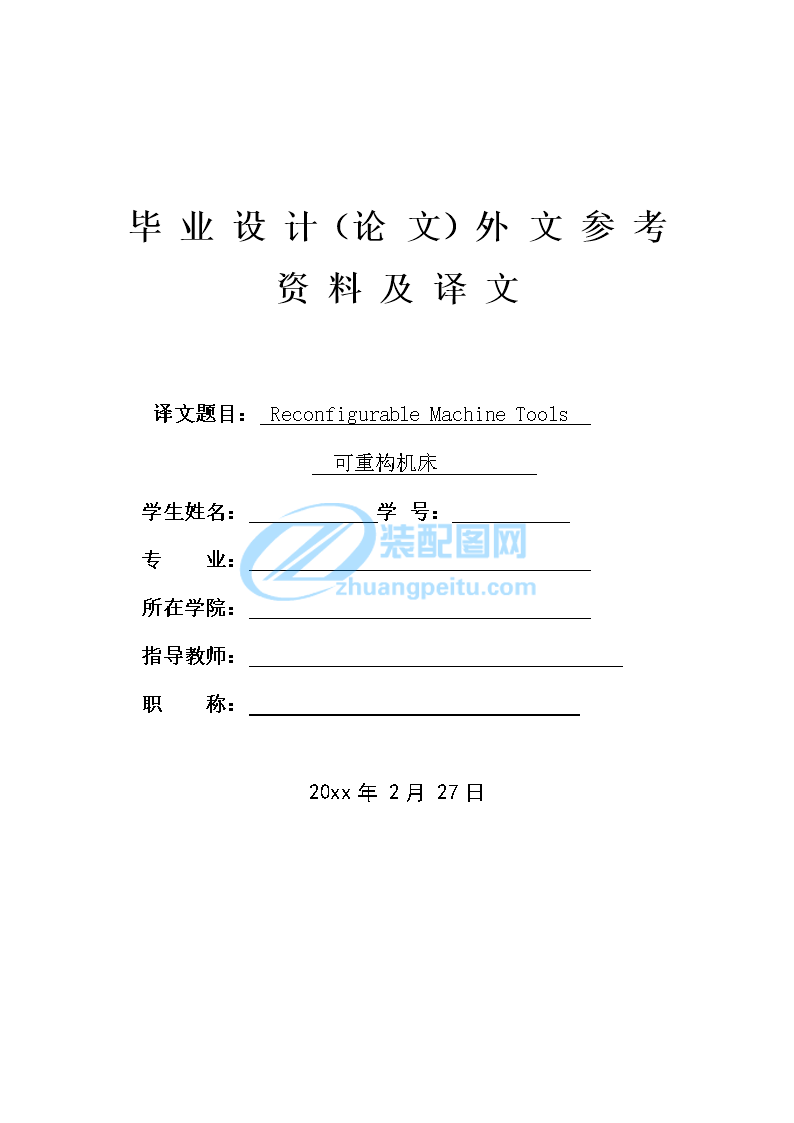
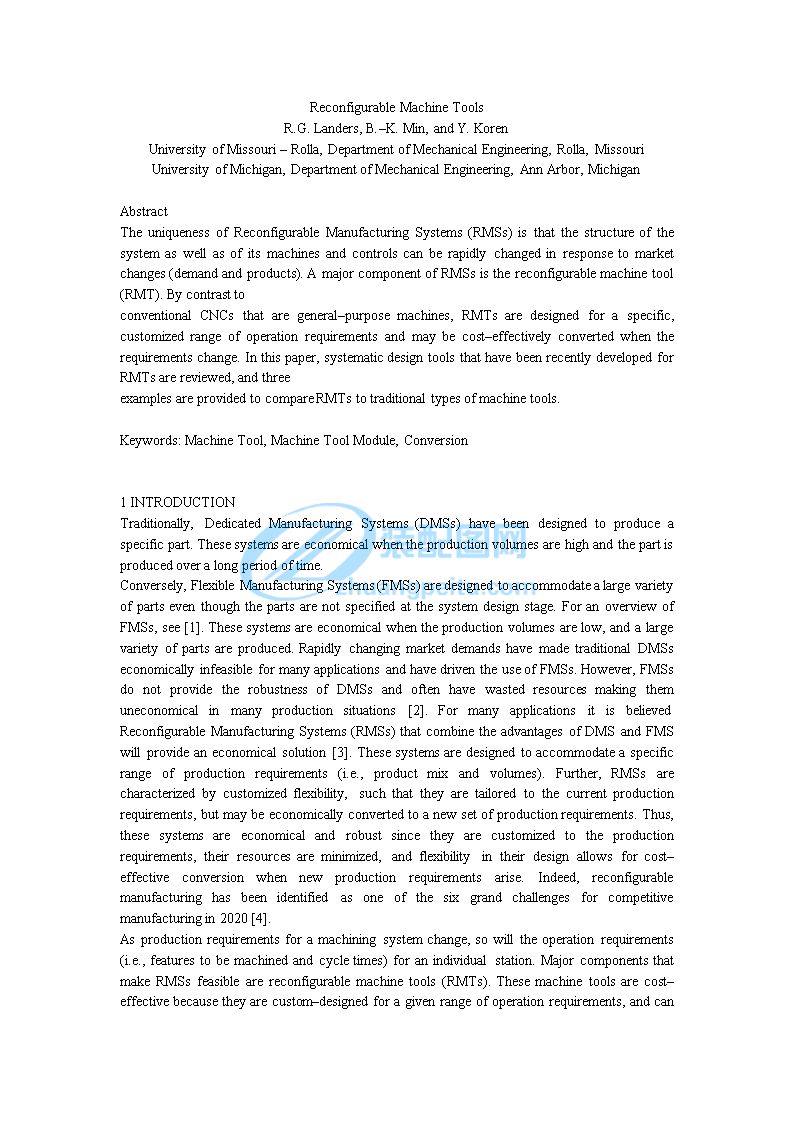
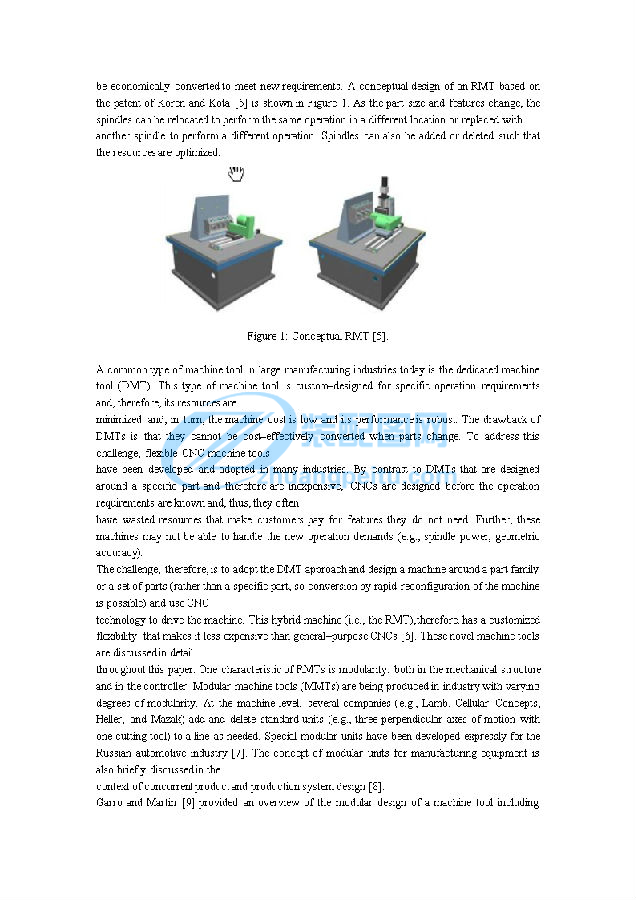
畢 業(yè) 設 計(論 文)外 文 參 考 資 料 及 譯 文
譯文題目: Reconfigurable Machine Tools
可重構機床
學生姓名: 學 號:
專 業(yè):
所在學院:
指導教師:
職 稱:
20xx年 2月 27日
Reconfigurable Machine Tools
R.G. Landers, B.–K. Min, and Y. Koren
University of Missouri – Rolla, Department of Mechanical Engineering, Rolla, Missouri
University of Michigan, Department of Mechanical Engineering, Ann Arbor, Michigan
Abstract
The uniqueness of Reconfigurable Manufacturing Systems (RMSs) is that the structure of the system as well as of its machines and controls can be rapidly changed in response to market changes (demand and products). A major component of RMSs is the reconfigurable machine tool (RMT). By contrast to
conventional CNCs that are general–purpose machines, RMTs are designed for a specific, customized range of operation requirements and may be cost–effectively converted when the requirements change. In this paper, systematic design tools that have been recently developed for RMTs are reviewed, and three
examples are provided to compare RMTs to traditional types of machine tools.
Keywords: Machine Tool, Machine Tool Module, Conversion
1 INTRODUCTION
Traditionally, Dedicated Manufacturing Systems (DMSs) have been designed to produce a specific part. These systems are economical when the production volumes are high and the part is produced over a long period of time.
Conversely, Flexible Manufacturing Systems (FMSs) are designed to accommodate a large variety of parts even though the parts are not specified at the system design stage. For an overview of FMSs, see [1]. These systems are economical when the production volumes are low, and a large variety of parts are produced. Rapidly changing market demands have made traditional DMSs economically infeasible for many applications and have driven the use of FMSs. However, FMSs do not provide the robustness of DMSs and often have wasted resources making them uneconomical in many production situations [2]. For many applications it is believed Reconfigurable Manufacturing Systems (RMSs) that combine the advantages of DMS and FMS will provide an economical solution [3]. These systems are designed to accommodate a specific range of production requirements (i.e., product mix and volumes). Further, RMSs are characterized by customized flexibility, such that they are tailored to the current production requirements, but may be economically converted to a new set of production requirements. Thus, these systems are economical and robust since they are customized to the production requirements, their resources are minimized, and flexibility in their design allows for cost–effective conversion when new production requirements arise. Indeed, reconfigurable manufacturing has been identified as one of the six grand challenges for competitive manufacturing in 2020 [4].
As production requirements for a machining system change, so will the operation requirements (i.e., features to be machined and cycle times) for an individual station. Major components that make RMSs feasible are reconfigurable machine tools (RMTs). These machine tools are cost–effective because they are custom–designed for a given range of operation requirements, and can be economically converted to meet new requirements. A conceptual design of an RMT based on the patent of Koren and Kota [5] is shown in Figure 1. As the part size and features change, the spindles can be relocated to perform the same operation in a different location or replaced with
another spindle to perform a different operation. Spindles can also be added or deleted such that the resources are optimized.
Figure 1: Conceptual RMT [5].
A common type of machine tool in large manufacturing industries today is the dedicated machine tool (DMT). This type of machine tool is custom–designed for specific operation requirements and, therefore, its resources are
minimized and, in turn, the machine cost is low and its performance is robust. The drawback of DMTs is that they cannot be cost–effectively converted when parts change. To address this challenge, flexible CNC machine tools
have been developed and adopted in many industries. By contrast to DMTs that are designed around a specific part and therefore are inexpensive, CNCs are designed before the operation requirements are known and, thus, they often
have wasted resources that make customers pay for features they do not need. Further, these machines may not be able to handle the new operation demands (e.g., spindle power, geometric accuracy).
The challenge, therefore, is to adopt the DMT approach and design a machine around a part family or a set of parts (rather than a specific part, so conversion by rapid reconfiguration of the machine is possible) and use CNC
technology to drive the machine. This hybrid machine (i.e., the RMT),therefore, has a customized flexibility that makes it less expensive than general–purpose CNCs [6]. These novel machine tools are discussed in detail
throughout this paper. One characteristic of RMTs is modularity: both in the mechanical structure and in the controller. Modular machine tools (MMTs) are being produced in industry with varying degrees of modularity. At the machine level, several companies (e.g., Lamb, Cellular Concepts, Heller, and Mazak) add and delete standard units (e.g., three perpendicular axes of motion with one cutting tool) to a line as needed. Special modular units have been developed expressly for the Russian automotive industry [7]. The concept of modular units for manufacturing equipment is also briefly discussed in the
context of concurrent product and production system design [8].
Garro and Martin [9] provided an overview of the modular design of a machine tool including interactions with the environment (e.g., operators and other machines) and the determination of control modules. Zatarain et al. [10]
developed a method to analyze the dynamic stiffness of a machine tool using pre–calculated component information. The notion of reconfiguration, however, extends beyond a customized-assembly of modular elements. That is,
reconfigurable systems are: (i) modular in their construction and therefore can be reconfigured by swapping modules as needed, (ii) convertible: individual modules can be repositioned or re-oriented without changing the topological characteristics of the machine. This level of reconfigurability is helpful in making quick, on-line changes to accommodate certain changes in the product family. Thus, reconfigurable machine tools can be
designed to provide different levels of reconfigurablity and the design process starts with a thorough understanding of peculiarities (geometry, processes, tolerances, cycle time, reconfiguration time) of a given family of products to be machined. Since the machine is designed around a part family, the reconfigurable machine offers customized flexibility at lower cost; that is the right kind of flexibility without any wasted-flexibility. Three methodologies are discussed in a subsequent section. A systematic methodology for the kinematic synthesis of RMTs starting from a mathematical description of the machining tasks [11], a methodology to evaluate the dynamic stiffness of RMTs [12], and one that evaluates machine dynamic errors using module information [13].
In this paper are also provided three example operation scenarios, each with different types of operation requirements, to illustrate the characteristics of RMTs and the differences between RMTs and other types of machine tools (i.e., dedicated, CNC, and modular).
2 MANUFACTURING REQUIREMENTS
The dominant production requirements for large machining systems are (1) mix (i.e., set of parts to be produced), and (2) volume (amount produced per unit time of each part) as well as changes in the part set and volumes over the life–time of the machining system. A variety of factors will influence the change in part sets and volumes over time including tightening government
regulations, increasing (decreasing) customer demands, etc. These factors may result in slight design modifications in the parts being produced, the introduction of new parts, the phasing–out of current parts, or the increase (decrease) in the volume of each part. Similarly, the operation requirements for a machine tool consist of (1) the set of features that are produced and (2) the cycle time (i.e., time to complete the operation for one part) of each operation as well as changes in the feature sets and cycle times. Changes in the production requirements directly effect the operation requirements. A feature set may be altered (e.g., tolerance increased, hole enlarged), added or subtracted, or the required cycle time may be increased or decreased. The relationship between the production and operation requirements and the various types of machining systems and machine tools is shown in Table 1 and
elaborated below.
Table 1: A comparison of three systems.
Dedicated machining systems (DMSs) are designed fornarrowly defined production requirements (typically onepart at a fixed volume) that are assumed to remainconstant over the life–time of the machining system. Thesesystems are comprised of dedicated machine tools(DMTs), each of which is custom–designed to machine aspecific set of features (often a single feature) at a
constant cycle time. Therefore, while DMSs are tailored to their productionrequirements and, thus, are robust andinexpensive, they cannot cost–effectively accommodatechanges in production requirements. Similarly, DMTs aretailored to specific operation requirements and, in general,cannot cost–effectively accommodate changes in theoperation requirements. If the volume sharply increases,the DMS may not be able to accommodate the increase
and another system will need to be built or the saleopportunity will be lost. A slight design change to the part may trigger the need to modify one or more DMTs. Asthese machine tools are not designed such that they maybe cost–effectively converted, the redesign and ramp–up of a modified (or entirely new) DMT will often be too costly.Further, the introduction of an entirely new part will requir the design of an entirely new machining system.
Flexible manufacturing systems (FMSs) are designed for loosely defined production requirements that are assumed to significantly change in an unknown manner over time. Since the production requirements are not well defined, FMSs often contain excessive capability, and the customer pays for unneeded capabilities. General–purpose Computer Numerical Control (CNC) machine tools are the building blocks of FMSs. Loosely defined production requirements at the system level translate into loosely defined operation requirements at the machine level. As a result, CNCs often contain excessive functionality (e.g., a five–axis CNC may use only two axes in a given operation, or only 6 tools of a 24–tool magazine may be utilized). Further, since CNCs are typically not designed for a specific set of operations, extensive testing must be performed to ensure the quality requirements will be met in the entire machine envelope. Increases in volume typically require additional CNCs.
Reconfigurable Machining Systems (RMSs), which are designed for a specific range of production requirements, cost–effectively combine the most attractive features of DMSs and FMSs: robust performance and the ability to
accommodate new production requirements [14]. Reconfigurable Machining Systems contain a combination of DMTs and CNCs, and incorporate, where appropriate, RMTs that are designed to produce specific sets of features for specific ranges of cycle times. Some operation requirements will be constant over the life–time of the machining system and, thus, DMTs will be the appropriate choice for these operation requirements. Some operation requirements will change dramatically in an unknown manner over the life–time of the machining system and, thus, CNCs will be the appropriate choice for these operation requirements. Since RMTs are designed for specific sets of features and ranges of cycle times, RMTs are tailored to the initial operation requirements and, when operation requirements change, RMTs may be cost–effectively converted such that they are customized for the new requirements.
3 RMT CONTROL REQUIREMENTS
The control components (hardware and software) of DMTs are customized for the DMT’s requirements and, thus, do not contain unnecessary complexity and are correspondingly robust. However, these components cannot be cost–effectively upgraded. Typical CNC controllers posses comprehensive architectures to provide processing flexibility; however, not all of the built–in functionality may be used. Thus, unnecessary costs are incurred due to software development, installation, and especially in maintenance and diagnostics. Further, similar to its mechanical components, CNC controllers posses control hardware resources (e.g., data acquisition boards, motor drives) that are often underutilized. For both DMTs and CNCs, the control components are not modular and, thus, are not scalable nor upgradable and new technology (e.g., advanced geometric compensation) cannot be cost–effectively integrated.
Controllers for RMTs must be based on the concept ofopen–architecture [15–17]. In open–architecture control,the software architecture is modular and, thus, hardwarecomponents (e.g., encoder) and software components(e.g., axis control logic) can be easily added or removed,and the controller can be cost–effectively reconfigured.The RMT controller modularity allows the controller to becustomized to its current operation requirements and, thus,be robust and reliable, while maintaining the ability to bereconfigured when requirements change or newtechnology becomes available.
Reconfiguration requirements introduce several new challenges for RMT controllers. The first challenge is the reconfiguration of the controller architecture that is required when the physical machine tool is reconfigured or new technology is integrated. Unlike DMT or CNC controller architectures, the RMT controller architecture is dynamic. For example, the addition of a linear axis to a one–axis RMT may require the integration of an interpolator software module. Another challenge is the control of RMTs with multiple tools working independently (as in Figure 1) and RMTs with axes in non–orthogonal
configurations (see the Second Example below). Strategies have been developed for the interpolation and control of RMTs with axes in non–orthogonal
configurations. Another challenge is the integration of heterogeneous software and hardware components (e.g., fieldbus protocols, control signals, electrical contacts) that are developed by different vendors at different times. This will require standard software and electrical interfaces or the development of special components that interface custom devices to standard interfaces.
To handle the challenge of cost–effective reconfiguration of RMT controllers, work on a software tool known as a control configurator is being developed and is currently being applied to a prototype RMT (see the First Example).
The controller (Figure 2) is composed of a configuration tool, a simulation tool, and a common HMI. The configuration tool is used to reconfigure the software whenever the prototype RMT structure is reconfigured (i.e., a linear axis is added or deleted). The tool allows the user to reconfigure the controller via a graphical user interface and generate the required software for the PC–based open architecture controller. The real–time simulation tool simulates the dynamics and discrete events of the electromechanical components and the machining process. This simulation is connected to the actual machine tool controller; thus, the user is able to evaluate
and debug the controller without operating the real machine whenever the controller is reconfigured.
Figure 2: Structure of prototype RMT controller.
4 RMT MECHANICAL REQUIREMENTS
For a machine tool to meet the productivity and quality demands of an operation, it must fulfill a variety of requirements including the ability to produce the specified motions and satisfy the part tolerance specifications. To produce the required motions, the machine tool’s kinematic capabilities must be examined. To meet the part tolerance requirements, the mechanical sources of error (e.g., component geometric error, assembly errors, thermal
deformation) must be examined. The following discusses two CAD/CAM tools that have been developed for RMT mechanical design.
Kinematic Viability. One requirement in the design of a machine tool is kinematic viability (i.e., the machine tool must be able to perform the motions required to produce the feature set). For a DMT, the minimum required degrees
of freedom (DOF) is designed given the feature set to be machined. The kinematic configuration, therefore, is limited. For a CNC, the entire machine tool, (typically 3–5 axes), is designed before the required set of operations is known. Therefore, CNCs typically have the required DOF for any operation; however, for many operations, the CNC possesses extra DOF creating wasted resources and unnecessary complexity.
Similar to a DMT, the DOF of an RMT is designed after the operation set has been determined; however, the change in operation requirements, in addition to the initial operation set, must also be considered. As the operation
requirements change, the DOF requirements may also change and, thus, the RMT will need to be mechanically modular to adapt to these changes. However, RMTs will not be general–purpose modular machine tools; instead, they will be designed with the minimal amount of required modularity. This amount will be dictated by the range of operations that are required of the machine tool and the frequency of the change in these operations.
A methodology (Figure 3) has been developed to determine the RMT kinematic requirements automatically [11]. The machining operation is transformed into a task matrix (i.e., a homogeneous transformation matrix [HTM]) that contains the necessary motion requirements for the machine tool. The functional requirements of the machining operation are used to generate graph representations of candidate machine tools. A graph gives the overall topology of the machine tool and structural and kinematic functions are assigned to various portions of the graph. A library of machine tool modules (e.g., spindles, slides) containing structural and kinematic information for
each module via HTMs, as well as connectivity information, is examined. Modules are assigned to various portions of the graph. The product of their HTMs is compared to the task matrix. If these matrices are equal, then the machine tool is kinematically viable. In this manner, all possible configurations can be determined. The viable configurations will be further reduced by other criteria (e.g., DOF, static and dynamic stiffness, thermal growth characteristics). This methodology also determines which modules must be added or deleted for each part in the part family. A CAD/CAM machine tool design package called PREMADE has been developed to assist the machine tool
designer in implementing these algorithms.
Figure 3: RMT kinematic design methodology.
Structural Stiffness. One of the most critical design criteria for machine tools is structural stiffness. Static deflections cause geometric errors, and chatter may result if the dynamic structural characteristics are not properly designed. Based upon the designer’s experience, DMTs are designed to have the required stiffness characteristics for a spe