


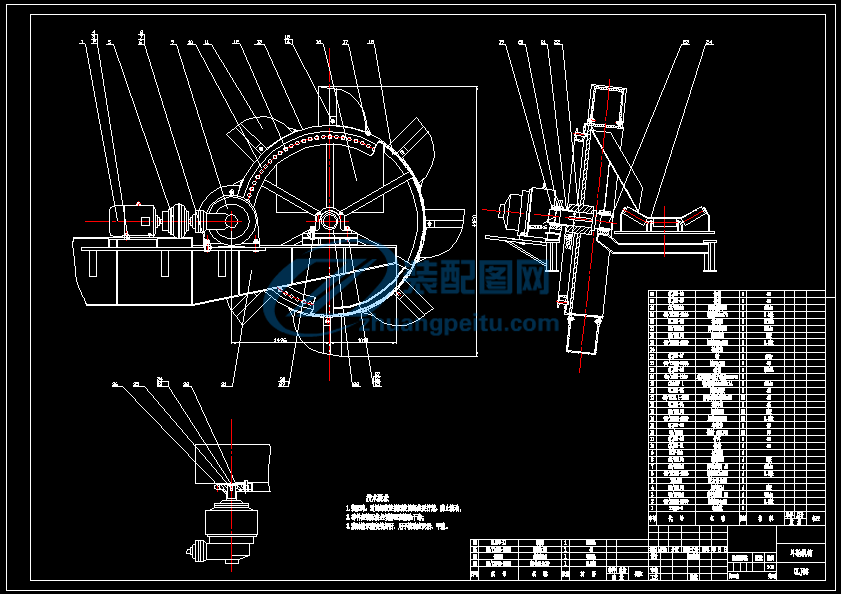
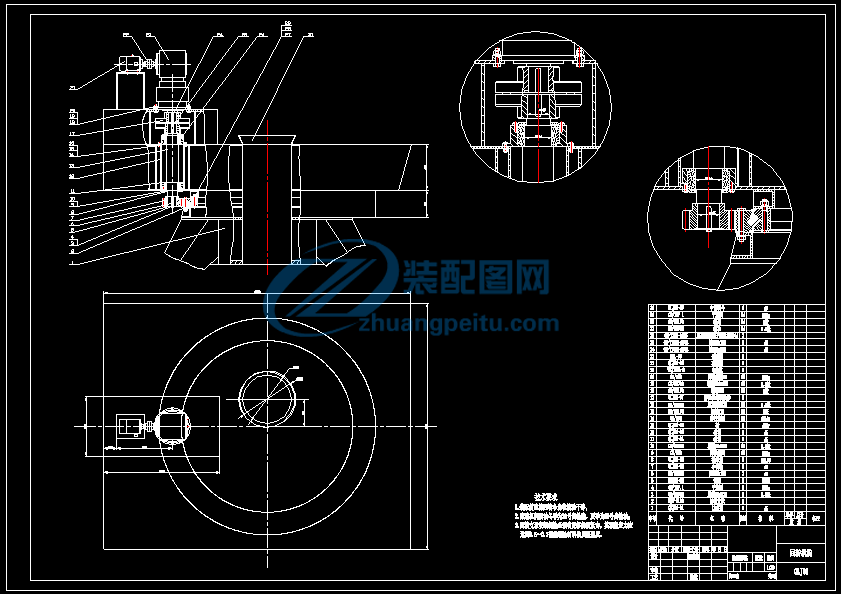
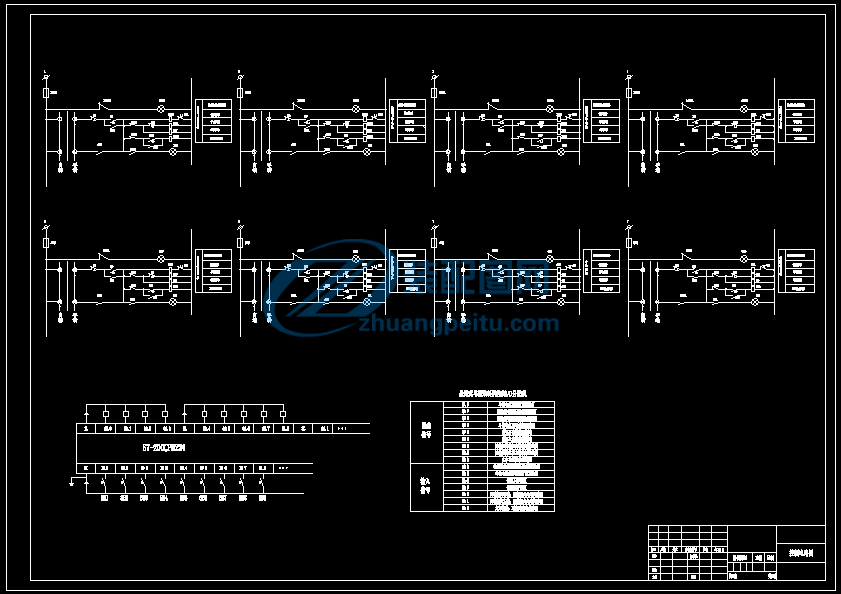





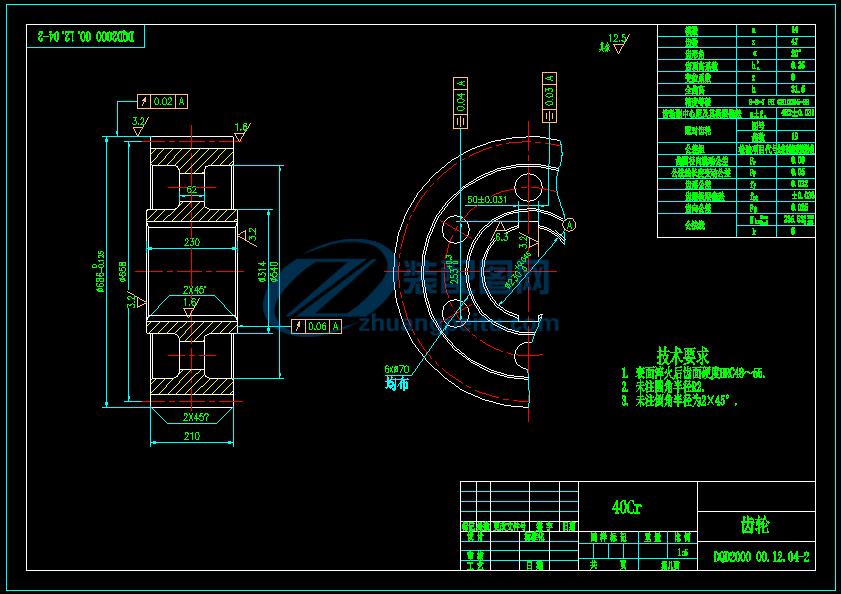
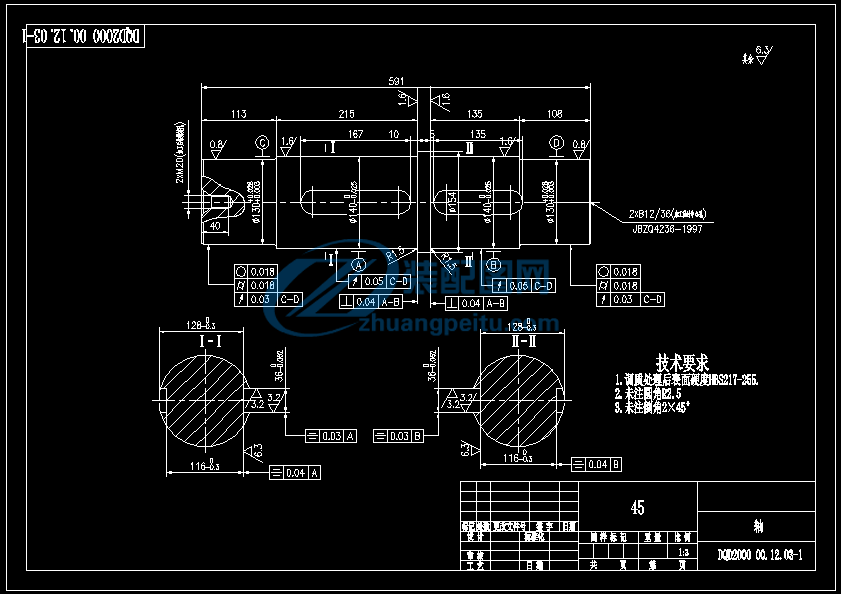
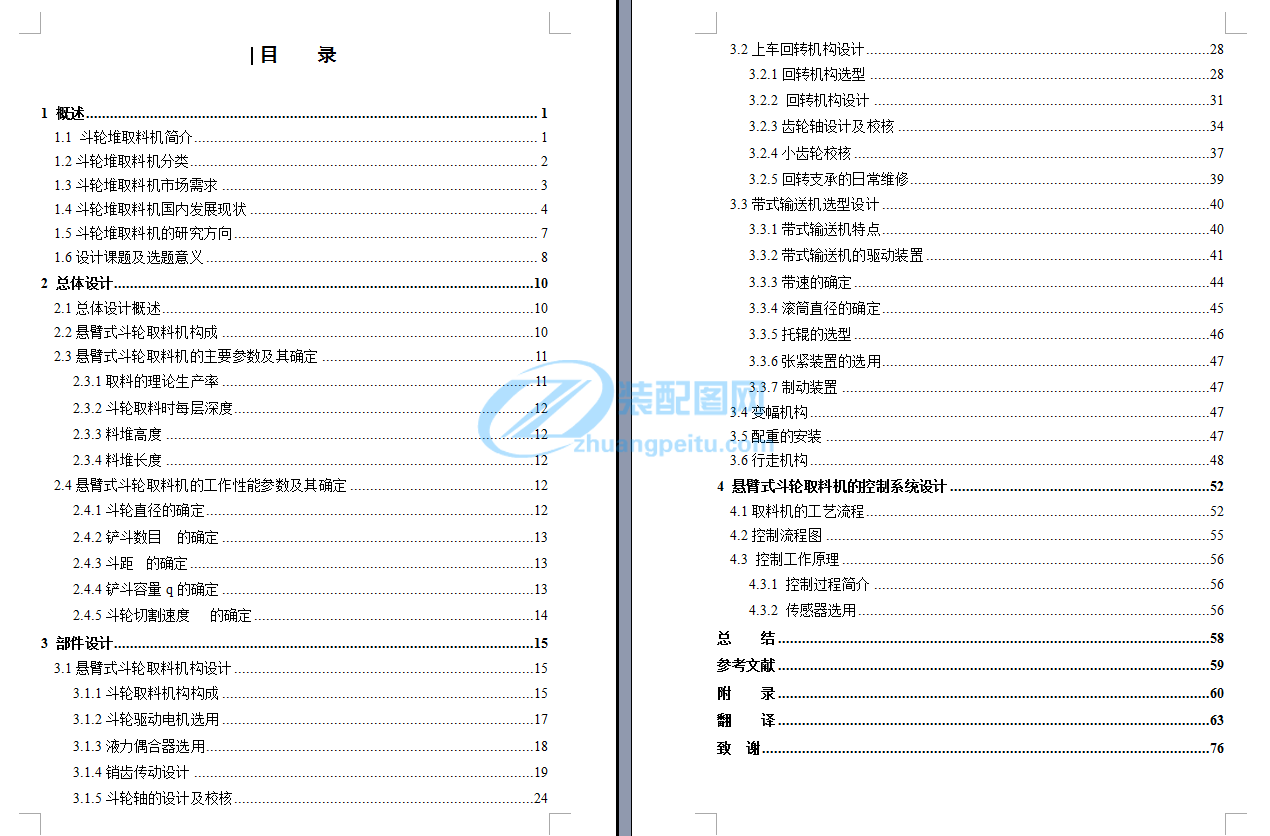
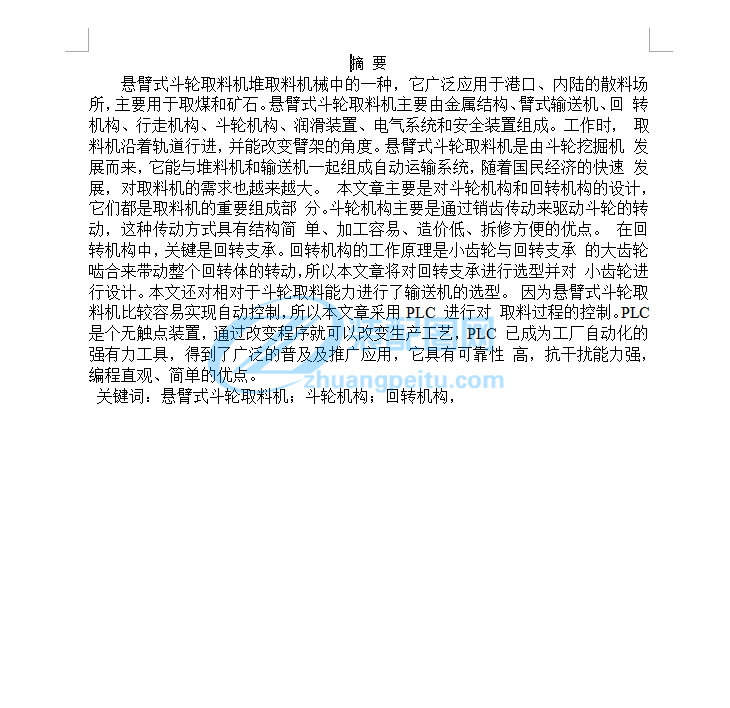
翻 譯原文Motorized Pulleys Solve Harsh Environmental Problemsat North American Ship Loading TerminalsKeywords: Motorized Pulleys, Ship Loaders, Bucket Wheel Stacker Reclaimers, Conveyor Belts1 AbstractThis paper presents design and operational challenges faced by three different ship loading facility operators, one handling export coal on the Gulf of Alaska and two handling taconite iron ore pellets on the North American Great Lakes. Extreme temperatures and abrasive materials, coupled with a need for compactness, made internally-powered and hermetically-sealed Motorized Pulleys the optimal design choice for driving ship loader and bucket wheel reclaimer conveyor belts.Originally a European idea, the Motorized Pulley was slow in gaining acceptance in North America in the twentieth century.However, the internally-powered conveyor belt drive has recently become more popular,especially where ambient conditions, material handled, or compact equipment design make exposed drives difficult to integrate and operate.2 IntroductionWhat do Seward, Alaska; Superior, Wisconsin; and Escanaba, Michigan have in common? Each is the location of a major rail-to-ship bulk storage and transfer facility, owned and operated by a railroad company. Each is located on water north of 45oN latitude, where winter temperatures can drop to –40o F (-40oC) and humidity reach nearly 100%. And each handles abrasive and/or corrosive material. One other important feature is common to these facilities.the Rulmeca Motorized Pulley. Rulmeca’s internally-powered and hermetically-sealed Motorized Pulley was selected to upgrade key drives on shiploader and bucket wheel reclaimer conveyor belts.This paper will review each facility’s layout, throughput, and particular challenges and it will explain why designers selected Motorized Pulley technology. These successful applications will help explain the growth in acceptance of Motorized Pulley technology in North America, especially in harsh environments.3 Motorized Pulley TechnologyThe Motorized Pulley concept was developed in the 1950’s to provide a reliable means of driving belt conveyors. Equipment designers quickly discovered that enclosing the drive’s motor and gearbox within a hermetically-sealed and oil-filled pulley shell not only made the drive compact, it also greatly improved the drive’s reliability and service life.Fig. 1: Rulmeca Motorized Pulley encloses motor and gearbox within hermetically-sealed oil-filled shell to protect moving components from harsh environment while saving space.Compactness, reliability, long service life, and limited maintenance requirements made the Motorized Pulley a popular conveyor drive for bulk handling equipment designers in Europe. Large machinery such as bucket wheel reclaimers, ship loaders, and tunnel boring equipment soon had Motorized Pulleys installed as original equipment. And plant operators began replacing worn exposed conveyor drives with Motorized Pulleys at facilities handling materials such as fertilizer, sand & gravel, steel, ore, and wood products.Each Motorized Pulley consists of an AC squirrel-cage induction motor, directly coupled to a helical/spur gearbox,mounted on a fixed(non-rotating) shaft, and hermeticallysealed within the cylindrical pulley shell.Today’s Motorized Pulley incorporates a wide array of powers and speeds as well as optional features ,such as built-in mechanical backstops, anti-condensation heaters, and electro-mechanical brakes.4 Allouez Dock #54.1 Synopsis of UpgradeBurlington Northern Santa Fe Railroad(BNSF) recently completed the overhaul of two of three 40 year old crawler-mounted bucket wheel reclaimers at the company’s rail-toship transfer terminal for taconite pellets located near Superior, Wisconsin.4.2 Objective of UpgradeThe objective of the upgrade was to reduce high maintenance expense while improving system reliability in the stockpile area. The upgrade included structural changes, replacement of on-board diesel engines, and the installation of RulmecaMotorized Pulleys. The challenge for BNSF operations was to keep the 40 year old machines working efficiently in spite of the fact that the machines’ manufacturerhad gone out of business more than 20 years ago. The original conveyor drives were a unique combination of components including AC motors, planetary gearboxes and pulleys mounted between the carrying and return strands of belt. Since original equipment manufacturer’s parts were no longer available and since the conveyor drives were non-standard, BNSF was forced to custom-build parts, an expensiveand time-consuming process. Engineering Design Services recommended Rulmeca Motorized Pulleys because: (1) they are compact and would fit within the reclaimers’ structure, (2) Rulmeca Motorized Pulleys and replacement parts are readily available, and (3) Rulmeca has a long successful track record of supplying conveyor drives for bucket wheel reclaimers.4.3 Operating DataAs summarized in Table 2, Allouez Dock #5 consists of an 87 acre (0,3 km2) facility providing 5.5 million tons of storage capacity in a stockpile area 3.5 miles (5,6 km) from the dock and 72,000 tons of storage in the dock silos. A conveyor system, 5.7 miles (9,2 km) in length, links the 2 rail car unloaders, the 3 stacker reclaimers, and the ship loader. Taconite pellets usually arrive in BNSF trains of 150 cars [each 35 feet (10,7 m) long “H-1” type at 1,800 ft3 (51 ) capacity] and are loaded into special lake 3mvessels. Up to 185 car trains can haul 20,000 tons of taconite pellets, at a gross train weight of 27,000 tons. Winter temperatures can reach –30o F (-34oC). Typically, ice does not cover all of Lake Superior, but near-complete sheets of ice, from a few inches to several feet thick, do form in the harbor area of Superior and St. Louis Bays. As early as mid-November and persisting as late as early May, ice in the Soot Locks or the harbor ends the shipping season. Frozen blocks of pellets can be found in the stockpiles as late as August and September. The 75 BNSF employees at Allouez Dock #5 unloaded 537 trains or 79,201 cars in 2003.4.4 Motorized Pulley ExperienceEngineering Design Services and Rulmeca engineers first presented the Motorized Pulley upgrade concept for the bucket wheel reclaimers to BNSF personnel in 1995, suggesting a “Dual Drive” arrangement for the tail conveyor due to its requirement of 200 HP (150 kW). Allouez Dock had been maintaining the bucket wheel machines without the assistance of the original equipment manufacturer for more than 10 years in 1995. However, the dual drive concept was relatively new at that time and eight years would elapse before the first bucket wheel reclaimer was upgraded. By 2003 original gearbox rebuilds had gotten very expensive. That year three Model 800H Motorized Pulleys, with 31.5 inch (800 mm) diameter and 57 inch (1400 mm) face width were purchased. BNSF operations personnel installed them in 2004. Each Motorized Pulley provided 120 HP (90 kW) at a belt speed of 768 fpm (4 m/s) on a power supply of 460V/3ph/60Hz, generated by the newly-installed on-board diesel generator. The compact design minimized structural modifications and greatly simplified the “Nested Dual Drive” configuration beneath the tail conveyor. The successful upgrade of the first machine encouraged BNSF to upgrade a second Bucket Wheel Reclaimer, completed in 2005, using three 100 HP (75kW) Rulmeca Motorized Pulleys. The third and final set of Motorized Pulleys was delivered July 2006. Engineering Design Services not only assisted BNSF personnel with initial design to insure a smooth retrofit, Roger Meittunen also traveled to the Rulmeca Motorized Pulley factory in Germany to observe final assembly of the first three Motorized Pulleys and obtain aftermarket service training on the Model 800H units to insure long-term success of the Motorized Pulleys at Allouez Dock.Fig. 2: 4,000 TPH Bucket Wheel Reclaimer in its second season after the 2004 Motorized Pulley upgrade. Note one Motorized Pulley beneath the boom conveyor and two under the tail conveyor.5 Escanaba, Michigan5.1 Synopsis of UpgradeThe Escanaba Ore Dock transfers 8 MTPY of taconite pellets from rail to lake vessels at the Lake Michigan terminal. The Chicago and Northwest Railroad replaced two worn-out Motorized Pulleys on the their bucket wheel reclaimer in 1985, after approximately 15 years of service, when the original Motorized pulley manufacturer went out of business. John Kirkegaard Maskinfabrik A/S supplied the replacement known as “JOKI Motorized Pulleys,” now called Rulmeca Motorized Pulleys. The two 40 inch (1 m) diameter 200 HP (150 kW) Motorized Pulleys are still in service after more than 20 years.5.2 Objective of UpgradeThe objective of the upgrade was to secure reliable drives for the 4000 TPH reclaimer boom and tail conveyors from an established Motorized Pulley manufacturer with readily available replacement parts. JOKI had been an established brand for 30 years at that time.Fig. 3: Traveling ship loader loads pellets into 64,000 DWT lake vessel at 4,000 TPH, filling it injust 16 hours.Fig. 4: Bucket Wheel boom is hydraulically luffed and transfers 4,000 TPH of taconite pellets on a 60 inch (1,5 m) wide belt at 715 FPM (3,6 m/s).5.3 Motorized Pulley ExperienceThe Rulmeca Motorized Pulleys installed on the bucket wheel reclaimer in 1985 are still in service and have now outlasted the original 16 year old pulleys by five shipping seasons. They have enabled the Escanaba Ore Dock to transload more than 150 million tons of taconite pellets during their service life.Fig. 5: Drawing shows unique double end housing arrangement on “drive side” of 200 HP (150 KW) Motorized Pulley. Development of different designs and more powerful Motorized Pulleys is in progress at Rulmeca FAA GmbH6 ConclusionThe long service lives promised by large Rulmeca Motorized Pulleys at three major transloading facilities with harsh operating conditions demonstrate the value of Motorized Pulley technology. There are now more than 130,000 Motorized Pulleys, 1 HP (0,75 kW) and larger, in service in North America. Including fractional HP Motorized Pulleys, there are nearly 1 million units in service. A proven design, which hermetically seals its drive system within a compact and oil-filled pulley shell, and a reliable source of supply and after market service will enable conveyor operators and system designers to take advantage of Motorized Pulley technology in North America and the rest of the world for many years to come.中文譯文電動(dòng)滾筒克服北美船運(yùn)裝載終端的惡劣環(huán)境問(wèn)題關(guān)鍵字: 電動(dòng)滾筒, 船運(yùn)裝載機(jī), 斗輪堆取料機(jī), 傳送帶1 概要這篇論文介紹了三個(gè)不同船運(yùn)裝載操作工所面臨的設(shè)計(jì)和操作上的挑戰(zhàn),一個(gè)在阿拉斯加海灣裝載用于出口的煤,另兩個(gè)在北美五大湖裝載鐵礦石。極端的溫度、具有腐蝕性的原料, 再加上需要良好的密封性,這些都使得具有內(nèi)在動(dòng)力而且密封性良好的電動(dòng)滾筒成為驅(qū)動(dòng)船運(yùn)裝載機(jī)和斗輪堆取料機(jī)傳送帶的最佳選擇。最初,電動(dòng)滾筒是一個(gè)歐洲人的想法,在二十世紀(jì)的北美已經(jīng)慢慢接受了它。然而,具有內(nèi)在動(dòng)力的傳送帶驅(qū)動(dòng)器近來(lái)變得很流行,特別是在那些因?yàn)橥庠诃h(huán)境、原料性質(zhì)或者設(shè)備需要緊湊的設(shè)計(jì)使得暴露在外面的驅(qū)動(dòng)機(jī)無(wú)法融入設(shè)備而且會(huì)運(yùn)轉(zhuǎn)困難的地方。2 緒論西華德、阿拉斯加州,瑟譜雷爾、威斯康星州,埃斯科拿巴、密歇根州有什么共同點(diǎn)呢?每一個(gè)地方都是主要的鐵路-船運(yùn)的中轉(zhuǎn)貯料場(chǎng)所,而且都有由鐵路公司擁有和操作的中轉(zhuǎn)設(shè)備;每一個(gè)地方都坐落在北緯45o的水平線上,那里冬天的溫度能降到零下40oC而且濕度接近100% ;每個(gè)地方都處理那些有腐蝕性的原料。另一個(gè)重要特征是它們都擁有陸美嘉電動(dòng)滾筒,陸美嘉的電動(dòng)滾筒因具有內(nèi)在動(dòng)力而且密封性良好被選用來(lái)升級(jí)驅(qū)動(dòng)貨運(yùn)船與斗輪堆取料機(jī)傳送帶的驅(qū)動(dòng)機(jī)。這篇論文介紹每個(gè)設(shè)備的設(shè)計(jì)、生產(chǎn)量還有一些特殊的挑戰(zhàn),它將解釋為什么設(shè)計(jì)人員選擇電動(dòng)滾筒技術(shù),這些成功的應(yīng)用將幫助我們解釋北美地區(qū)特別是有惡劣環(huán)境的地區(qū)為何越來(lái)越多的應(yīng)用電動(dòng)滾筒技術(shù)。3 電動(dòng)滾筒技術(shù)電動(dòng)滾筒技術(shù)這一概念是在十九世紀(jì)五十年代為了給驅(qū)動(dòng)帶式輸送機(jī)定義而發(fā)展起來(lái)的。裝置設(shè)計(jì)者很快發(fā)現(xiàn)將驅(qū)動(dòng)器的馬達(dá)和變速箱嵌入一個(gè)具有良好密封性并且充滿油的皮帶輪罩里不僅可以使驅(qū)動(dòng)器緊湊,而且它能大幅提高驅(qū)動(dòng)器的可靠性和工作壽命。圖 1: 陸美嘉電動(dòng)滾筒將馬達(dá)和變速箱嵌入嵌入一個(gè)具有良好密封性并且充滿油 皮帶輪罩里為了在惡劣環(huán)境中保護(hù)移動(dòng)部件同時(shí)節(jié)省空間。緊湊、可靠、長(zhǎng)時(shí)間服務(wù)壽命和有限的維護(hù)要求使電動(dòng)滾筒成為歐洲散裝運(yùn)輸設(shè)備設(shè)計(jì)者喜歡的輸送機(jī)驅(qū)動(dòng)器。大型機(jī)械設(shè)備像斗輪堆取料機(jī)、船用裝載機(jī)和隧道挖掘設(shè)備使電動(dòng)滾筒能像原先設(shè)備一樣被安裝,而且設(shè)備操作者開始在運(yùn)輸散料諸如化肥、沙石、鐵礦石和木材制品時(shí)用電動(dòng)滾筒替換舊的且暴露在外的輸送機(jī)驅(qū)動(dòng)器。每個(gè)電動(dòng)滾筒把一個(gè)鼠籠式交流感應(yīng)電動(dòng)機(jī),直接連接在一個(gè)螺旋式齒輪變速箱,安裝在一根固定的軸上并將柱形皮帶輪罩密封好?,F(xiàn)在的電動(dòng)滾筒包括一組動(dòng)力和速度設(shè)備還有其它附加設(shè)備諸如機(jī)械支持物、加熱器、電動(dòng)機(jī)械剎車等。4 Allouez 5號(hào)碼頭4.1 升級(jí)計(jì)劃圣達(dá)菲北部布林頓鐵路公司最近大修兩臺(tái)近40年歷史的斗輪堆取料機(jī),它們放在離瑟譜雷爾、威斯康星州不遠(yuǎn)的地方,平時(shí)用來(lái)將鐵路運(yùn)輸?shù)蔫F礦石轉(zhuǎn)至船上。4.2 升級(jí)目的這次升級(jí)目的是為了減少高額的維護(hù)費(fèi)用同時(shí)提高在散料場(chǎng)地工作時(shí)的系統(tǒng)可靠性,這次升級(jí)包括對(duì)結(jié)構(gòu)的改進(jìn)、船上柴油機(jī)的替換和陸美嘉電動(dòng)滾筒的安裝。這次BNSF公司的改進(jìn)計(jì)劃所面臨的問(wèn)題是使這些有40年歷史的機(jī)器能有效的運(yùn)轉(zhuǎn)起來(lái),盡管這些機(jī)器的生產(chǎn)商在20多年前就已經(jīng)倒閉。原先的傳動(dòng)機(jī)驅(qū)動(dòng)器是一個(gè)由好幾個(gè)部件組成的獨(dú)特設(shè)備,它包括交流電動(dòng)機(jī)、變速箱和安裝在運(yùn)輸與回程帶之間的滑輪。由于原先的設(shè)備制造廠商的一些部件不能用了,而且輸送機(jī)的驅(qū)動(dòng)器不是標(biāo)準(zhǔn)的,BNSF公司不得不定制這些部件,這是個(gè)即費(fèi)時(shí)又費(fèi)錢的過(guò)程。工程設(shè)計(jì)維護(hù)公司建議使用陸美嘉電動(dòng)滾筒有以下理由: (1)它們簡(jiǎn)潔緊湊適合于取料機(jī)的結(jié)構(gòu);(2)陸美嘉電動(dòng)滾筒和取代部分很好用;(3)陸美嘉公司早已成功推出各種用于斗輪堆取料機(jī)的輸送機(jī)驅(qū)動(dòng)器,技術(shù)較成熟。4.3 運(yùn)行數(shù)據(jù)Allouez 5號(hào)碼頭包括87英畝擁有五百五十萬(wàn)噸儲(chǔ)存能力的場(chǎng)地,它離碼頭大概3.5英里的路程,還有擁有七萬(wàn)兩千噸儲(chǔ)存量的碼頭筒倉(cāng),輸送系統(tǒng)有5.7英里長(zhǎng),包括兩輛軌道卸載車,三臺(tái)堆取料機(jī),還有貨船裝載設(shè)備。150輛車容量的鐵礦石通常先裝在BNSF公司火車?yán)?,然后再裝進(jìn)貨船里,能達(dá)到185輛車容量的火車可以拖動(dòng)兩萬(wàn)噸的鐵礦石,在加上火車自身重量總重量可以達(dá)到兩萬(wàn)七千頓。那里冬天的溫度能達(dá)到零下34度,雖然冰沒有覆蓋整個(gè)湖,但是有相當(dāng)一部分已覆蓋,厚度從幾英寸到幾英尺。最早從十一月中旬一直可以到五月初,湖上的冰使得船運(yùn)無(wú)法進(jìn)行,可能到了八九月份還能在堆料場(chǎng)里找到冰塊,BNSF公司的75個(gè)員工在2003年卸了537次火車和79201次汽車。4.4 關(guān)于電動(dòng)滾筒的經(jīng)驗(yàn)1995年,工程設(shè)計(jì)維護(hù)公司和陸美嘉的工程師首次向BNSF公司提出電動(dòng)滾筒升級(jí)概念,提出為了達(dá)到150KW的動(dòng)力要求而且在尾部輸送機(jī)處采用雙電動(dòng)機(jī)排列。Allouez 碼頭 在沒有原來(lái)設(shè)備制造廠商的幫助下自己維護(hù)斗輪堆取料機(jī)已經(jīng)有十年多的時(shí)間了,然而,在那時(shí)作為新的概念的雙電動(dòng)機(jī)到2003年把第一臺(tái)斗輪堆取料機(jī)升級(jí)完已經(jīng)花了八年的時(shí)間,原先的變速箱改造已經(jīng)變得很昂貴了,那時(shí)購(gòu)買了三個(gè)直徑800㎜寬1400㎜的800H型電動(dòng)滾筒, BNSF公司的實(shí)施人員在2004年才安裝上它們,每個(gè)電動(dòng)滾筒提供90 kW的動(dòng)力,此動(dòng)力由安裝在船上的柴油機(jī)產(chǎn)生,可以使皮帶以4 m/s的速度運(yùn)行。這緊湊的設(shè)計(jì)減小了結(jié)構(gòu)修改量,大大簡(jiǎn)化了尾部輸送機(jī)底下雙電動(dòng)機(jī)的結(jié)構(gòu)。第一臺(tái)機(jī)器的成功升級(jí)促使BNSF去升級(jí)第二臺(tái)斗輪堆取料機(jī),第二臺(tái)也已經(jīng)在2005年完成,用了三個(gè)75kW的陸美嘉電動(dòng)滾筒,第三臺(tái)電動(dòng)滾筒于2006年7月交貨。工程設(shè)計(jì)維護(hù)公司不僅幫助BNSF設(shè)計(jì)人員進(jìn)行初始設(shè)計(jì),而且Roger Meittunen親自拜訪了位于德國(guó)的陸美嘉電動(dòng)滾筒工廠,觀察第一批三個(gè)電動(dòng)滾筒的最后裝配,得到了800H型的售后服務(wù)訓(xùn)練,使得在 Allouez 碼頭的電動(dòng)滾筒能長(zhǎng)期成功的工作。圖 2: 在 2004 年電動(dòng)滾筒的升級(jí)后, 4000 噸每小時(shí)的斗輪取料機(jī)已工作兩個(gè)季度,注意輸送機(jī)下面的一個(gè)電動(dòng)滾筒還有尾車輸送機(jī)下面的兩個(gè)電動(dòng)滾筒。5 埃斯科拿巴, 密歇根5.1 升級(jí)計(jì)劃密歇根湖的埃斯科拿巴礦石碼頭每年將八百萬(wàn)頓鐵礦石從鐵路轉(zhuǎn)運(yùn)至湖運(yùn)船,芝加哥和西北鐵路公司在1985年替換了它們斗輪堆取料機(jī)上兩個(gè)過(guò)時(shí)的機(jī)械化輪,在15年的工作后,原先的制造廠商倒閉了,John Kirkegaard Maskinfabrik 將著名的“JOKI Motorized Pulleys”座位了替代品,也就是現(xiàn)在的陸美嘉電動(dòng)滾筒,這兩個(gè)直徑1米功率150KW 的電動(dòng)滾筒已經(jīng)工作了近二十多年。 5.2 升級(jí)目的升級(jí)的目的是為了給工作量4000頓每小時(shí)的取料機(jī)和尾部的輸送機(jī)提供穩(wěn)定的動(dòng)力,而這替換部件得從一家有經(jīng)驗(yàn)的廠商提供,JOKI 是一個(gè)有了近30年的老品牌了。圖 3: 裝船設(shè)備以 4000 噸每小時(shí)的速度裝運(yùn)礦石,可以在 16 小時(shí)內(nèi)裝滿圖 4: 斗輪的發(fā)動(dòng)機(jī)是個(gè)水壓轉(zhuǎn)舵,能以 4000 噸每小時(shí)的速度將鐵礦石轉(zhuǎn)移到 1.5 米寬的輸送帶上。5.3 感受陸美嘉電動(dòng)滾筒自從1985年安裝在斗輪取料機(jī)上起直到現(xiàn)在還在工作,已經(jīng)超過(guò)了原先的16年壽命預(yù)期,從而使得埃斯科拿巴礦石碼頭在它們的壽命內(nèi)多運(yùn)輸了150多萬(wàn)噸的鐵礦石。圖 5: 圖中所示為 150 kW 電動(dòng)滾筒的驅(qū)動(dòng)器兩邊兩個(gè)端蓋排列設(shè)計(jì),馬力更為強(qiáng)大的電動(dòng)滾筒正在研制。 6 結(jié)論在惡劣環(huán)境下三臺(tái)設(shè)備上所裝的陸美嘉電動(dòng)滾筒做到了曾經(jīng)的承諾-長(zhǎng)壽命,這也體現(xiàn)了電動(dòng)滾筒的價(jià)值,現(xiàn)在有130,000多臺(tái)0,75 kW 甚至更大功率的電動(dòng)滾筒在北美地區(qū)使用,包括HP型,有接近一百萬(wàn)個(gè)單元在服務(wù)。這是一個(gè)經(jīng)過(guò)考驗(yàn)的設(shè)計(jì),它因把驅(qū)動(dòng)系統(tǒng)安裝在一個(gè)緊湊并充滿油的皮帶輪罩里而且又能穩(wěn)定的提供能量,再加上售后服務(wù)使得在北美和世界其它地方的輸送機(jī)系統(tǒng)設(shè)計(jì)者越來(lái)越多使用電動(dòng)滾筒技術(shù)。