
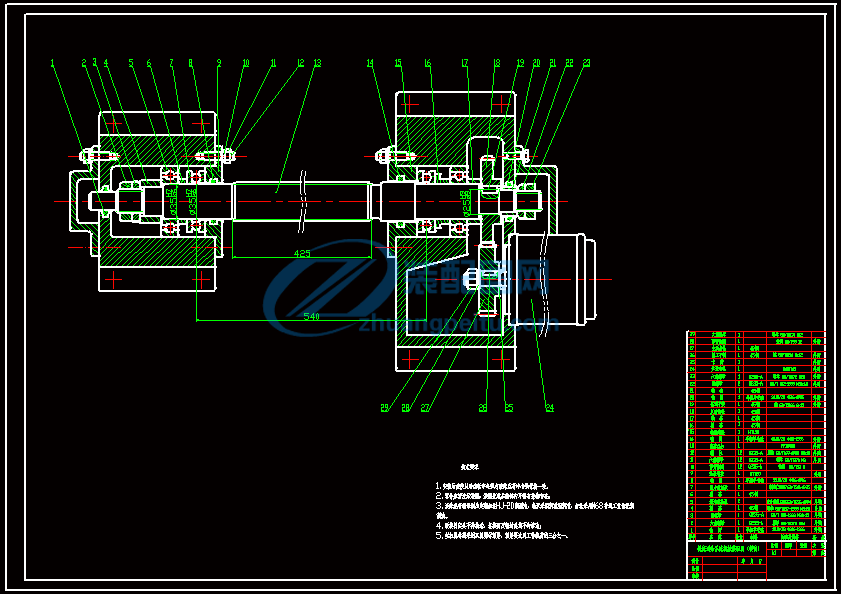

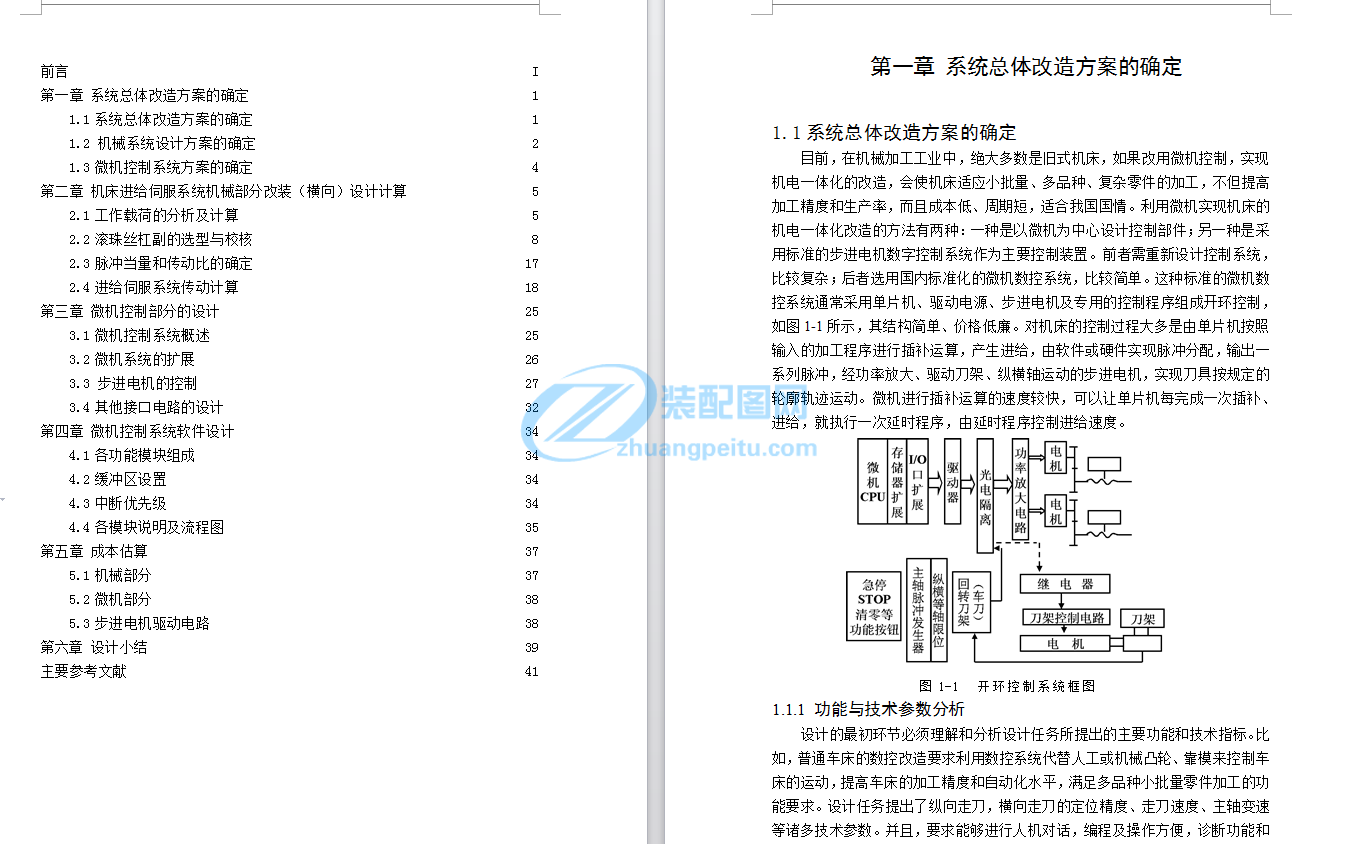


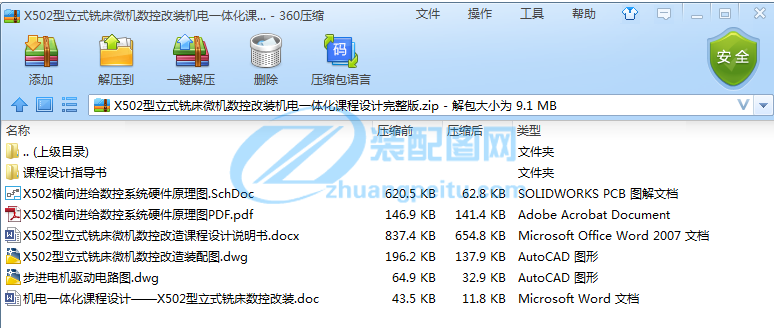
I前言一、機床數(shù)控化改造的意義與傳統(tǒng)機床相比,數(shù)控機床具有以下明顯突出的優(yōu)越性。1、通過計算機所具有的高超運算能力,瞬時準確地計算出每個坐標軸瞬時應(yīng)該運動的運動量,因此可以復(fù)合成復(fù)雜的曲線或曲面使數(shù)控機床能夠加工出傳統(tǒng)機床加工不出的曲線、曲面等復(fù)雜零件。2、通過計算機的的記憶和存儲能力,將輸入的程序進行記憶和存儲,實現(xiàn)加工的柔性自動化,從而大大的提高加工效率。3、數(shù)控機床的加工工序較為集中,能夠節(jié)省因零件工序分散而損耗的時間,縮短生產(chǎn)周期,并且可以提高零件的加工精度,從而減小誤差,也有助于提高裝配效率。4、數(shù)控機床具有較強的自動化能力,可以實現(xiàn)加工過程中的自動監(jiān)控、自動報警、自動補償?shù)榷喾N功能。5、加工過程自動化,使一個工人就能夠同時看管多臺機床,并且大大減輕工人勞動強度,節(jié)省了勞動力,降低了生產(chǎn)成本,提高企業(yè)的經(jīng)濟效益,實現(xiàn)良性的循環(huán)。6、數(shù)控技術(shù)已經(jīng)成為制造業(yè)自動化的核心技術(shù)和基礎(chǔ)技術(shù),數(shù)控機床的普及,以及使用數(shù)控機床進行加工制造,對提高勞動生產(chǎn)率具有重要意義。二、機床數(shù)控化改造的內(nèi)容機床與生產(chǎn)線的數(shù)控化改造主要內(nèi)容有以下幾點:1、恢復(fù)原功能,對機床、生產(chǎn)線存在的故障部分進行診斷并恢復(fù);2、NC 化,在普通機床上加數(shù)顯裝置,或加數(shù)控系統(tǒng),改造成 NC 機床、CNC 機床;3、翻新,為提高精度、效率和自動化程度,對機械、電氣部分進行翻新,II對機械部分重新裝配加工,恢復(fù)原精度;對其不滿足生產(chǎn)要求的 CNC 系統(tǒng)以最新 CNC 進行更新;4、技術(shù)更新或技術(shù)創(chuàng)新,為提高性能或檔次,或為了使用新工藝、新技術(shù),在原有基礎(chǔ)上進行較大規(guī)模的技術(shù)更新或技術(shù)創(chuàng)新,較大幅度地提高水平和檔次的更新改造。三、機床數(shù)控化改造的優(yōu)缺點1、減少投資額、交貨期短同購置新機床相比,一般可以節(jié)省 60%~80%的費用,改造費用低。特別是大型、特殊機床尤其明顯。一般大型機床改造,只花新機床購置費用的 1/3,交貨期短。2、機械性能穩(wěn)定可靠,結(jié)構(gòu)受限所利用的床身、立柱等基礎(chǔ)件都是重而堅固的鑄造構(gòu)件,而不是那種焊接構(gòu)件,改造后的機床性能高、質(zhì)量好,可以作為新設(shè)備繼續(xù)使用多年。但是受到原來機械結(jié)構(gòu)的限制,不宜做突破性的改造。3、熟悉了解設(shè)備、 便于操作維修購買新設(shè)備時,不了解新設(shè)備是否能滿足其加工要求。改造則不然,可以精確地計算出機床的加工能力;另外,由于多年使用,操作者對機床的特性早已了解,在操作使用和維修方面培訓(xùn)時間短,見效快。4、可在原有的基礎(chǔ)上,充分利用現(xiàn)有的條件,達到很好的經(jīng)濟性,如充分利用現(xiàn)有地基,不必像購入新設(shè)備時那樣需重新構(gòu)筑地基。5、可以采用最新的控制技術(shù)可根據(jù)技術(shù)革新的發(fā)展速度,及時地提高生產(chǎn)設(shè)備的自動化水平和效率,提高設(shè)備質(zhì)量和檔次,將舊機床改成當(dāng)今水平的機床。III前言 I第一章 系統(tǒng)總體改造方案的確定 11.1 系統(tǒng)總體改造方案的確定 11.2 機械系統(tǒng)設(shè)計方案的確定 21.3 微機控制系統(tǒng)方案的確定 4第二章 機床進給伺服系統(tǒng)機械部分改裝(橫向)設(shè)計計算 52.1 工作載荷的分析及計算 52.2 滾珠絲杠副的選型與校核 82.3 脈沖當(dāng)量和傳動比的確定 172.4 進給伺服系統(tǒng)傳動計算 18第三章 微機控制部分的設(shè)計 253.1 微機控制系統(tǒng)概述 253.2 微機系統(tǒng)的擴展 263.3 步進電機的控制 273.4 其他接口電路的設(shè)計 32第四章 微機控制系統(tǒng)軟件設(shè)計 344.1 各功能模塊組成 344.2 緩沖區(qū)設(shè)置 344.3 中斷優(yōu)先級 344.4 各模塊說明及流程圖 35第五章 成本估算 375.1 機械部分 37IV5.2 微機部分 385.3 步進電機驅(qū)動電路 38第六章 設(shè)計小結(jié) 39主要參考文獻 411第一章 系統(tǒng)總體改造方案的確定1.1 系統(tǒng)總體改造方案的確定目前,在機械加工工業(yè)中,絕大多數(shù)是舊式機床,如果改用微機控制,實現(xiàn)機電一體化的改造,會使機床適應(yīng)小批量、多品種、復(fù)雜零件的加工,不但提高加工精度和生產(chǎn)率,而且成本低、周期短,適合我國國情。利用微機實現(xiàn)機床的機電一體化改造的方法有兩種:一種是以微機為中心設(shè)計控制部件;另一種是采用標準的步進電機數(shù)字控制系統(tǒng)作為主要控制裝置。前者需重新設(shè)計控制系統(tǒng),比較復(fù)雜;后者選用國內(nèi)標準化的微機數(shù)控系統(tǒng),比較簡單。這種標準的微機數(shù)控系統(tǒng)通常采用單片機、驅(qū)動電源、步進電機及專用的控制程序組成開環(huán)控制,如圖 1-1 所示,其結(jié)構(gòu)簡單、價格低廉。對機床的控制過程大多是由單片機按照輸入的加工程序進行插補運算,產(chǎn)生進給,由軟件或硬件實現(xiàn)脈沖分配,輸出一系列脈沖,經(jīng)功率放大、驅(qū)動刀架、縱橫軸運動的步進電機,實現(xiàn)刀具按規(guī)定的輪廓軌跡運動。微機進行插補運算的速度較快,可以讓單片機每完成一次插補、進給,就執(zhí)行一次延時程序,由延時程序控制進給速度。2圖 1-1 開 環(huán) 控 制 系 統(tǒng) 框 圖1.1.1 功能與技術(shù)參數(shù)分析設(shè)計的最初環(huán)節(jié)必須理解和分析設(shè)計任務(wù)所提出的主要功能和技術(shù)指標。比如,普通車床的數(shù)控改造要求利用數(shù)控系統(tǒng)代替人工或機械凸輪、靠模來控制車床的運動,提高車床的加工精度和自動化水平,滿足多品種小批量零件加工的功能要求。設(shè)計任務(wù)提出了縱向走刀,橫向走刀的定位精度、走刀速度、主軸變速等諸多技術(shù)參數(shù)。并且,要求能夠進行人機對話,編程及操作方便,診斷功能和糾錯功能強,具有顯示和通信功能,縮短非生產(chǎn)準備時間,提高生產(chǎn)率。1.1.2 原理構(gòu)思和技術(shù)路線確定針對設(shè)計任務(wù)的主要功能和技術(shù)指標要求提出一些原理性的構(gòu)思。比如,普通車床車削螺紋時為了防止亂扣,進給與主軸旋轉(zhuǎn)之間用掛輪來實現(xiàn)嚴格的機械傳動關(guān)系,改變螺紋的螺距就需要改變掛輪。數(shù)控改造后,省掉了掛輪,要提出合理的、先進的方法來解決進給與主軸旋轉(zhuǎn)相配合的問題。要做到:主軸轉(zhuǎn)一轉(zhuǎn),車刀精確移動一個螺距;螺紋加工不能一次切削完成時,每次進刀的位置必須相同。有了原理性構(gòu)思,還要提出實現(xiàn)該功能原理的技術(shù)途徑。沒有合理的可行的技術(shù)途徑來保障,好的原理性構(gòu)思就成為空想。1.1.3 擬定總體方案功能原理構(gòu)思和技術(shù)路線確定后,對運動、布局、傳動、結(jié)構(gòu)、控制以及軟件等方面作出總體方案設(shè)計。方案可以同時作幾個,經(jīng)過技術(shù)和經(jīng)濟評價后,選擇其中一種較合理的作為最優(yōu)方案加以采用。比如,普通車床的數(shù)控化改造方案應(yīng)該在滿足改造設(shè)計任務(wù)的前提下,盡可能對普通車床作較少的改動,這樣可以降低改造成本。1.2 機械系統(tǒng)設(shè)計方案的確定在熟悉原機床的操作過程及傳動系統(tǒng)后,根據(jù)設(shè)計要求確定系統(tǒng)的機械傳動系統(tǒng)改造方案。包括電機型號的選擇,減速比的確定,齒輪模數(shù)及齒數(shù)的確定,原有絲杠及導(dǎo)軌是否要重新更換,改換成滾珠絲杠螺母副時絲杠螺母副的型號及安裝形式如何確定,導(dǎo)軌的設(shè)計方法等。X502 型銑床的外形如圖 1-2 所示。工件裝在機床的工作臺上,銑刀裝在轉(zhuǎn)3動的刀桿上,銑刀和工件相互間的位置可用縱向、橫向和升降進給機構(gòu)進行調(diào)整。機床的傳動系統(tǒng)見圖 1-3。圖 1-2 X502 型銑床外形圖 圖 1-3 X502 型銑床傳動系統(tǒng)1.2.1 傳動系統(tǒng)由四部分組成:(1)主軸旋轉(zhuǎn)運動由轉(zhuǎn)速為 1450r/min,功率為 2.2kW 的電動機經(jīng)過帶輪 1 通過三根皮帶傳到 I 軸,經(jīng)過齒輪 6、8 傳到 II 軸,通過交換齒輪 10、11 將動力傳到 III 軸,經(jīng)過滑移齒輪 12(或 14)和 15(或 16)嚙合動力傳到 IV 軸,再經(jīng)過齒輪 15 和55 動力傳到 IX 軸上,通過傘齒輪 56、57 動力傳到主軸上使主軸回轉(zhuǎn),從而使裝在主軸上的銑刀轉(zhuǎn)動進行加工,可使主軸獲得 8 種不同的轉(zhuǎn)速。(2)工作臺縱向運動工作臺縱向運動,由軸 II 通過齒輪 9 與 19 嚙合,動力傳到 V 軸,再經(jīng)過齒輪 20(19)與 21(22)嚙合,使軸 VI 轉(zhuǎn)動,再經(jīng)過齒輪 23 和 24 動力傳到VII 軸,經(jīng)過萬向接頭 26 傳到 VIII 軸,經(jīng)過換向齒輪箱內(nèi)傘齒輪 29、30 及齒輪 33、34 到傘齒輪 35、36,通過凸瓣離合器 37 與凸瓣離合器套 39 嚙合使動力傳到絲杠 40 上,絲杠再與工作臺相固聯(lián)的螺母中轉(zhuǎn)動,使絲杠帶動工作臺縱向移動,當(dāng)離合器脫開,可用手輪 43 使工作臺手搖移動。(3)工作臺橫向運動工作臺和工作臺底座,一起再升降臺導(dǎo)軌上作橫向移動。用裝在升降臺內(nèi)4橫向行程絲杠 45 傳動,橫向絲杠螺母 46 固定裝在工作臺底座上,所以當(dāng) 44 傳動 45 時,螺母 46 跟工作臺及工作臺底座一起在升降臺上橫向移動。只能由手動進給。(4)工作臺的升降運動只能手動。用套在升降軸 48 上的手柄 44 轉(zhuǎn)動傘齒輪 49 和 50,使升降絲杠 52 轉(zhuǎn)動,升降螺母 53 固定在底座上,從而得到升降移動。根據(jù)設(shè)計要求可對機械部分進行如下改動:保留原機床的主軸旋轉(zhuǎn)運動;保留原機床縱向進給的機動部分,將離合器脫開,去掉手輪 43,將手輪軸通過一對齒輪與步進電機相聯(lián),用步進電機數(shù)控系統(tǒng)控制縱向工作臺的移動;工作臺橫向運動改為通過一對齒輪與步進電機相聯(lián)的數(shù)控系統(tǒng)控制,工作臺的升降移動仍用手動。為了保證精度要求,橫向及縱向工作臺的絲杠換為滾珠絲杠副傳動。1.3 微機控制系統(tǒng)方案的確定1.3.1 微機控制系統(tǒng)的總體組成數(shù)控部分采用 MCS-51 系列的單片機控制,其典型代表有8031、8051、8075 等,其中 8031 的價格低,功能強,使用靈活等特點,比較適用于一般機床的數(shù)控改造,但由于其無內(nèi)存,必須外接存儲及 I/O 擴展芯片才可成為一個較簡單的微機控制系統(tǒng)。存儲芯片的選擇依據(jù)系統(tǒng)控制程序的大小及 CPU 的字長,I/O 擴展芯片的個數(shù)根據(jù)整個系統(tǒng)需要的 I/O 通道的個數(shù)來確定。1.3.2 軟硬件任務(wù)合理分配涉及軟、硬件任務(wù)分配的有:控制步進電機的脈沖發(fā)生與脈沖分配;數(shù)碼顯示的字符發(fā)生;鍵盤掃描管理。上述三個都可以用專用硬件芯片實現(xiàn),也可用軟件編程實現(xiàn)。用硬件實現(xiàn),編程時較簡單,但同時增加了硬件成本及故障源。用軟件實現(xiàn),可節(jié)省芯片,降低成本,但增加了編程難度。在決定用何種方法實現(xiàn)時,應(yīng)統(tǒng)籌兼顧,同時還應(yīng)根據(jù)設(shè)計者的軟、硬件方面的實際經(jīng)驗及能力。5第二章 機床進給伺服系統(tǒng)機械部分改裝(橫向)設(shè)計計算2.1 工作載荷的分析及計算根據(jù)課程設(shè)計指導(dǎo)書的分析,可知對于數(shù)控銑床來說,其切削力的計算方法有兩種,即一種方法是按切削用量計算切削力法,另一種是按主電機功率法計算切削力計算切削力法。一般來說,對于經(jīng)濟型數(shù)控銑床,可采用按主電機功率計算切削力法來計算其切削力。2.1.1 銑床的銑削抗力分析銑削運動的特征是主運動為銑刀繞自身軸線高速回轉(zhuǎn),進給運動為工作臺帶動工件在垂直于銑刀軸線方向上緩慢進給(鍵槽銑刀可沿軸線進給) 。銑刀的類型很多,但以圓柱銑刀和端銑刀為基本形式。圓柱銑刀和端銑刀的切削部分都可以看作車刀頭部的演變,銑刀的每一個刀齒相當(dāng)于一把車刀,它的切削基本規(guī)律與車削相似,所不同的是銑刀回轉(zhuǎn),刀齒數(shù)多。通常都假定銑削時銑刀受到的銑削抗力是作用在刀齒的某一點上,如圖 2-1所示。設(shè)刀齒上受到的切削抗力的合力為 F,將 F 沿銑刀軸線、徑向和切向進行分解,則分別為軸向銑削力 Fx,徑向銑削力 Fy 和切向銑削力 Fz。切向銑削力 Fz 是沿銑刀主運動方向的分力,它消耗銑床主電機功率(即銑削功率)最多,因此,切向銑削力 Fz 可按銑削功率 Pm(kW)或主電機功率 PE(kW )算出。6圖 2-1 銑 削 力 及 工 作 臺 上 的 載 荷對于現(xiàn)有機床的改裝設(shè)計,可以從已知機床的電機功率和主軸上傳動的功率反推出工作臺進給時的銑削力。若該機床的主傳動和進給傳動均用一個電機,進給傳動的功率較小,可在主傳動功率上乘以一個系數(shù)。由《機床設(shè)計手冊》查銑床傳動系數(shù) k=0.85。主傳動功率 N 包括切削功率 Nc、空載功率 Nmo、附加功率 Nmc 三部分,即: N=Nc + Nmo + Nmc??蛰d功率 Nmo 是當(dāng)機床無切削負載時主傳動系統(tǒng)空載所消耗的功率,對于一般輕載高速的中、小型機床,可達總功率的 50%,現(xiàn)取 Nmo = 0.5N,附加功率 Nmc 是指有了切削載荷后所增加的傳動件的摩擦功率,它直接與載荷大小有關(guān)??梢杂孟率接嬎悖琋mc = (1–η)Nc,所以總功率為:N=Nc + 0.5N + (1–η)Nc (KW)則: ??0.52CNk???在進給傳動中切削功率 ??0.52ctkk7上式中 k----銑床的傳動系數(shù),查《機床設(shè)計手冊》得 k=0.85η 為傳動效率,可由下式計算η= 主 軸 上 的 傳 動 功 率主 電 機 的 功 率由所給設(shè)計任務(wù)書給定的已知條件可知,主軸上的傳動功率 N=1.45 KW,主電機的功率 = 2.2 KW。則N電 機η= =0.65911.452所以: ??0.514.8.5962ctNkW????切削時作用在主軸上的扭矩為: ??0.459695092.37897ctnMNcm????上式中 n----主軸的最小轉(zhuǎn)速,由設(shè)計任務(wù)書給定條件知 n = 47.5 (r/min)切向切削力: ??9240.378.614nzMFNd?上式中 d----銑刀的最大直徑 (cm),由設(shè)計任務(wù)書給定條件知 d = 3.2 cm2.1.2 計算進給工作臺工作載荷 、 、LFVC作用在進給工作臺上的合力 F’與銑刀刀齒上受到的銑削抗力的合力 F 大小相同,方向相反,如圖 2-1 所示。合力 F’就是設(shè)計和校核工作臺進給系統(tǒng)時要考慮的工作載荷,它可以沿著銑床工作臺運動方向分解為三個力:工作臺縱向8進給方向載荷 FL,工作臺橫向進給方向載荷 和工作臺垂直進給方向載荷 FV。CF由課程設(shè)計指導(dǎo)書表 3-1“銑削加工的主切削力與其它切削分力的比值”可知,工作臺工作載荷 FL, Fc 和 FV 與銑刀的切向銑削力 Fz 之間有一定的經(jīng)驗比值。因此,求出 Fz 后,即可計算出進給工作臺的如下五組工作載荷 FL,F(xiàn) c 和FV。第(1)組:端銑 —對稱銑削=0.35 Fz=0.35× =1010.67(N))L6184.27=0.9 Fz=0.9× =2598.86 (N)VF=0.52 Fz=0.52× =1501.56 (N)C.第(2)組:端銑 —逆銑=0.75 Fz=0.75× =2165.71 (N)LF6184.27=0.55 Fz=0.55× =1588.19 (N)V=0.52 Fz=0.52× =1501.56 (N)C.第(3)組:端銑—順銑=0.22 Fz=0.22× =635.28 (N)LF6184.27=0.95 Fz=0.95× =2743.24 (N)V=0.52 Fz=0.52× =1501.56 (N)C.第(4)組:周銑—逆銑=1.0Fz=1.0× =2887.62 (N)LF6184.27=0.25 Fz=0.25× =721.90 (N)V=0.37 Fz=0.37× =1068.42 (N)C.第(5)組:周銑—順銑=0.85 Fz=0.85× =2454.48 (N)LF614.287=0.75 Fz=0.75× =2165.71 (N)V9=0.4 Fz=0.4× =1155.05 (N)CF6184.272.2 滾珠絲杠副的選型與校核2.2.1 滾珠絲杠螺母副結(jié)構(gòu)類型的選擇滾珠絲杠副是由絲杠、螺母、滾珠等零件組成的機械元件,其作用是將旋轉(zhuǎn)運動轉(zhuǎn)變?yōu)橹本€運動或?qū)⒅本€運動轉(zhuǎn)變?yōu)樾D(zhuǎn)運動,它是傳統(tǒng)滑動絲杠的進一步延伸發(fā)展。這一發(fā)展的深刻意義如同滾動軸承對滑動軸承所帶來得改變一樣。滾珠絲杠副因優(yōu)良的摩擦特性使其廣泛的運用于各種工業(yè)設(shè)備、精密儀器、精密數(shù)控機床。尤其是近年來,滾珠絲杠副作為數(shù)控機床直線驅(qū)動執(zhí)行單元,在機床行業(yè)得到廣泛運用,極大的推動了機床行業(yè)的數(shù)控化發(fā)展。這些都取決于其具有以下幾個方面的優(yōu)良特性:傳動效率高、定位精度高、傳動可逆性、使用壽命長、同步性能好。滾珠絲杠螺母副一般由專業(yè)廠生產(chǎn)并成套供貨,且都附有使用說明書,其中除列有型號、規(guī)格、螺母安裝面的結(jié)構(gòu)等外,還附有允許負載、預(yù)加負載、剛度、典型支撐方式、驅(qū)動力矩和功率等指導(dǎo)性材料供設(shè)計時參考。滾珠絲杠螺母副的設(shè)要選擇結(jié)構(gòu)類型:確定滾珠循環(huán)方式、滾珠絲杠副的預(yù)緊方式;結(jié)構(gòu)類型確定之后,再計算和確定其它技術(shù)參數(shù),包括:公稱直徑、導(dǎo)程、滾計首先珠的工作圈數(shù)和列數(shù)、精度等級等。因為所要改裝的銑床為普通銑床,精度要求并不是很高,在使用過程中不需要調(diào)整,并且加工過程中運動平穩(wěn)。根據(jù)上述實際條件,并考慮到經(jīng)濟成本問題,通過查課程設(shè)計指導(dǎo)書第三章表 3-2 和表 3-3 以及《機電液設(shè)計手冊》P669 頁表 15-27,可以初步選用“FFZ 型內(nèi)循環(huán)浮動式返向器雙螺母對旋預(yù)緊滾珠絲杠副”這種結(jié)構(gòu)類型的滾珠絲杠螺母副。它具有循環(huán)滾珠鏈最短,螺母外徑比外循環(huán)小,結(jié)構(gòu)緊湊,反向裝置剛性好,壽命長,扁圓形反向器的軸向尺寸短, ,承載能力較高;剛度高,預(yù)緊可靠,不易松弛等優(yōu)點。它主要適用于各種高靈敏、高剛度的精密進給定位系統(tǒng),是目前應(yīng)用得較廣泛的結(jié)構(gòu)。2.2.2 滾珠絲杠螺母副型號的選擇及校核步驟1、計算最大工作載荷10由設(shè)計任務(wù)書給定已知條件,可知銑床導(dǎo)軌的類型為綜合導(dǎo)軌。再查《課程設(shè)計指導(dǎo)書》第三章表 3-4 可知計算最大工作載荷 的公式為mF??'mLVFGcKf??該式中:K = 1.15;取摩擦系數(shù) f’ = 0.16(f’ =0.15~0.18) ;G 為工作臺及夾具總重量的 1/2。由設(shè)計任務(wù)書給定已知條件可計算得 G = 800x N18042??將以上數(shù)值以及先前計算所得五組工作載荷 FL,F(xiàn) c 和 FV 可得如下五組相應(yīng)的最大工作載荷 Fm 值。(1)Fm=1.15×1010.67+0.16× (2598.86+1501.56+400)= 1882.34(N)(2)Fm=1.15×2165.71+0.16× (1588.19+1501.56+400)=3048.93(N)(3)Fm=1.15×635.28+0.16× (2743.24+1501.56+400)= 1473.74(N)(4)Fm=1.15×2887.62+0.16× (721.90+1068.42+400)=3671.21(N)(5)Fm=1.15×2454.48+0.16× (2165.71+1155.05+400)= 3417.97(N)由以上計算數(shù)據(jù)可知,第(4)組算得的 值較大。故最大工作載荷為:mFFm=3671.21(N)2、計算最大動載荷 C查《機電一體化系統(tǒng)設(shè)計》P35 頁可知:最大動載荷 C 的計算公式為最大動載荷 C 可由下式計算 3wHmCLfF?上式中:各參數(shù)見《機電一體化系統(tǒng)設(shè)計》P35 頁----硬度系數(shù),選 = 1.0(HRC≥58)Hf Hf----運轉(zhuǎn)系數(shù),選 =1.0(無沖擊運轉(zhuǎn))wf wfL ----壽命系數(shù),由下式計算11601nTL?上式中:T----使用壽命(h),對于數(shù)控機床 T=15000(h)n----絲杠轉(zhuǎn)速(r/min),可由下式計算 01sVnL?上式中: ----最大切削力條件下的縱向進給速度(m/min),由設(shè)計任務(wù)書sV給定條件可知為 380(mm/min)可取最高切削進給速度的 1/2~1/3,現(xiàn)取 1/2,即= ×0.38(m/min)=0.19(m/min)sV12----所選用絲杠的基本導(dǎo)程,考慮到傳動精度的要求,可選基本導(dǎo)程為0L4、6、8 (mm)的絲杠。(1)基本導(dǎo)程為 L0=4 mm 時:= =60nTL?10VS66150.1942.754??C= =12836.74(N)342.75.37.2?(2)基本導(dǎo)程為 L0=6 mm 時:= = =28.50601nTL?01VS66150.19?C= =11213.92(N)328.5.37.2?(3)基本導(dǎo)程為 L0=8mm 時:= = =21.38 601nTL?01VS66150.198?C= =10188.52(N)32.8.37.2?12查《機電液設(shè)計手冊》P669 表 15-27 FFZ 型內(nèi)循環(huán)浮動式返向器雙螺母對旋預(yù)緊滾珠絲杠副可知,基本導(dǎo)程為 L0=4 mm 時,最大動載荷都不滿足 C1)24J -----各轉(zhuǎn)動體的轉(zhuǎn)動慣量(kg.cm )i 2n -----各轉(zhuǎn)動體的轉(zhuǎn)速(r/min)in -----電機的轉(zhuǎn)速(r/min)KJ -----電機的轉(zhuǎn)動慣量(kg.cm )m24、電機的轉(zhuǎn)動慣量的確定查《課程設(shè)計指導(dǎo)書》P30 頁表 3-10,選用電機的工作方式為三相六拍,步距角為 ,故符合電機的是:110BF003 和 110BF004。電機的轉(zhuǎn)動慣?75.0?b?量分別為:110BF003(新)型步進電機: 522146.0.4.61()mJkgkgcm????110BF004 型步進電機: 23.35、系統(tǒng)總的轉(zhuǎn)動慣量110BF003(新)型步進電機: ??211 19.86.409. ckgJmL ??????110BF004 型步進電機: 376.3mJ ??2.4.2 步進電機的計算和選用1、電機力矩的計算步進電機能正常工作所需的力矩受到多方面的影響,主要包括快速空載起動時所需力矩 、快速進給時所需力矩 、最大切削負載時所需力矩 ,起M快M切M其中快速進給時所需力矩 較小,因此在 、 兩種力矩中取其大者作為快 起 切選擇步進電機的依據(jù)。對于大多數(shù)數(shù)控機床來說,因為要保證一定的動態(tài)性能,系統(tǒng)時間常數(shù)較小,而等效轉(zhuǎn)動慣量又較大,故電機力矩主要是用來產(chǎn)生加速度的,而負載力矩往往小于加速力矩,故常常用快速空載起動力矩 作為選起擇步進電機的依據(jù)??焖倏蛰d起動時所需力矩: ??cmNMfa???0mx起最大切削負載時所需力矩:25??cmNMft ???0切電機的力矩主要是用來產(chǎn)生加速度,而負載力矩往往小于加速力矩,故常常用快速空載起動力矩作為選擇步進電機的依據(jù)。(1)空載起動時折算到電機軸上的加速力矩 max??cNtJM?????2a106namxπ=333.71(N.cm)式中: ----傳動系統(tǒng)折算到電機軸總的等效轉(zhuǎn)動慣J? ??2kgcm?----運動部件從停止起動加速到最大進給速度所需的時間(s )約為 30msat----電機最大轉(zhuǎn)速(r/min)maxn----運動部件最大快進速度,由設(shè)計任務(wù)書給定條件知axV??min/160maxV?n = = =333.33( r/min) maxpaxb360vδθ ?.75110BF003(新)型步進電機: ??cmNtaJM ???????? ?? 89.2103.6219.806n22mx1amx ?π110BF004 型步進電機: ??cNtaJ ??????? ?? 16.9803.62039.1760n2 22mx1amx ?π(2)摩擦力矩 fM26)(20'cmNiLGfMf ????式中:G----運動部件的總重量(N)----導(dǎo)軌摩擦系數(shù),取'f 16.0'?f-----齒輪總減速比i?---- 傳動鏈總效率,一般可取 ,取85.~7?8.0??則: )(1.625.801420' cmNiLGfMf ??????(3)附加摩擦力矩 0 ).(1(2200cNiLFMp????式 中 : Fp0----滾 珠 絲 杠 預(yù) 加 負 載 ( N) , 一 般 取 最 大 工 作 載 荷1/3, ??Fmp 74.123.3610???L0-----滾 珠 絲 杠 導(dǎo) 程 ( cm) , 由 前 述 cmL6.00? 0-----滾 珠 絲 杠 未 預(yù) 緊 時 的 傳 動 效 率 , 一 般 取 , 取9.0??95.?則: ????cmNM????37.895.012.80674130?(4)折算到電機軸上的切削負載力 tM).(20cmNiLFtt???----進 給 方 向 最 大 切 削 力 ( N) , 即 為 前 述 計 算 的 工 作 載 荷 、t LF