YB4包裝機輪輪體的銑右端臺階面夾具設(shè)計及加工工藝工裝設(shè)計【含5張CAD圖帶過程、工序卡片】
【需要咨詢購買全套設(shè)計請加QQ1459919609】圖紙預(yù)覽詳情如下:
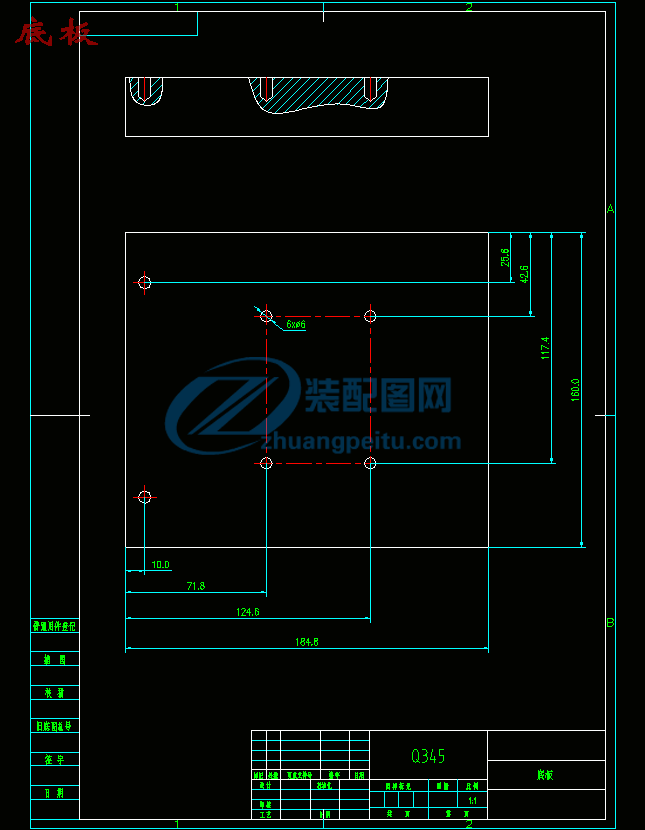
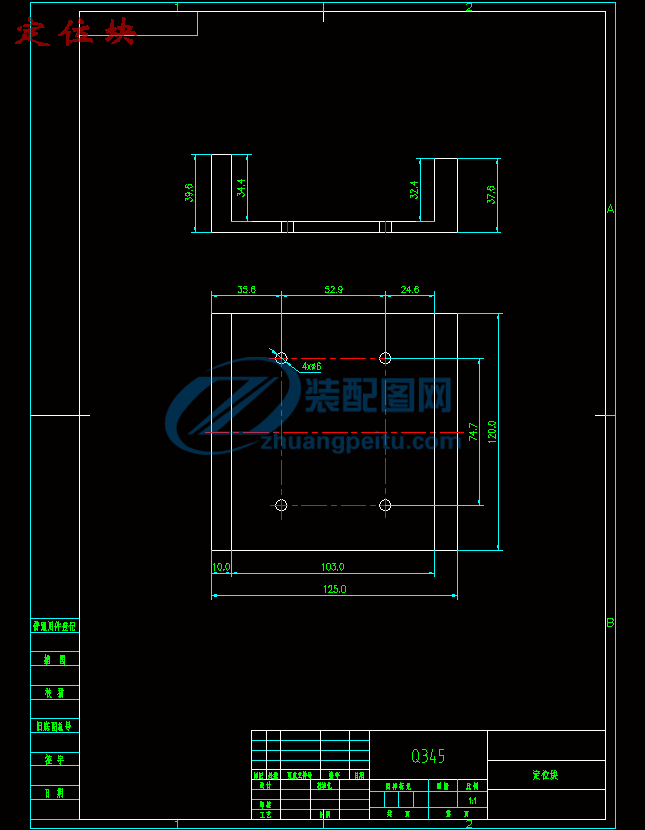
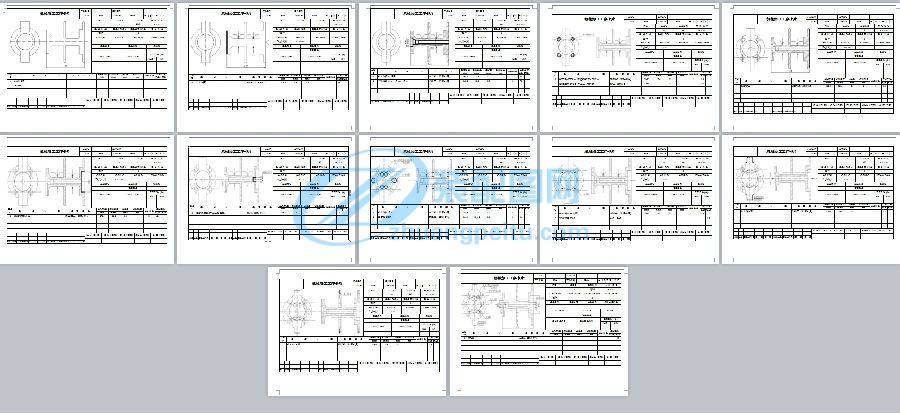
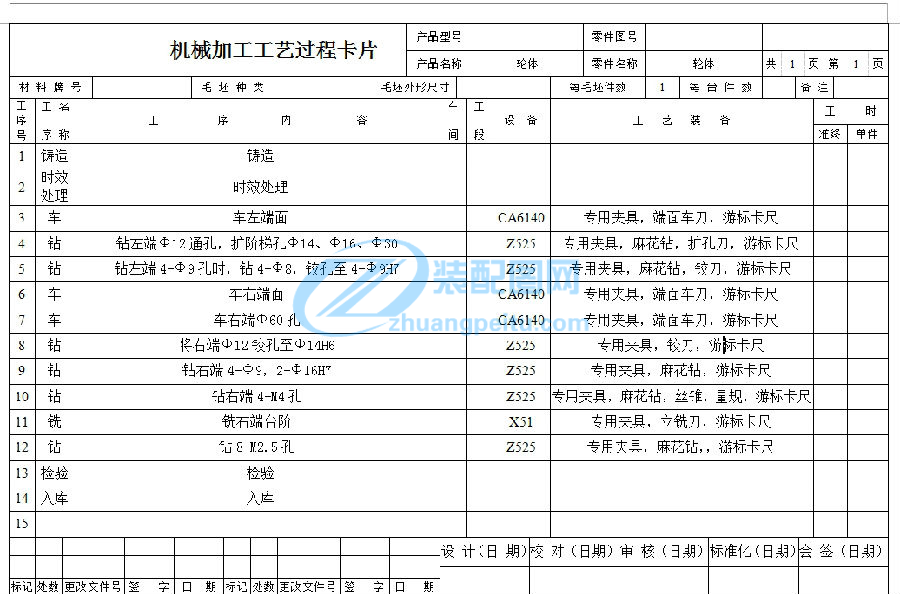
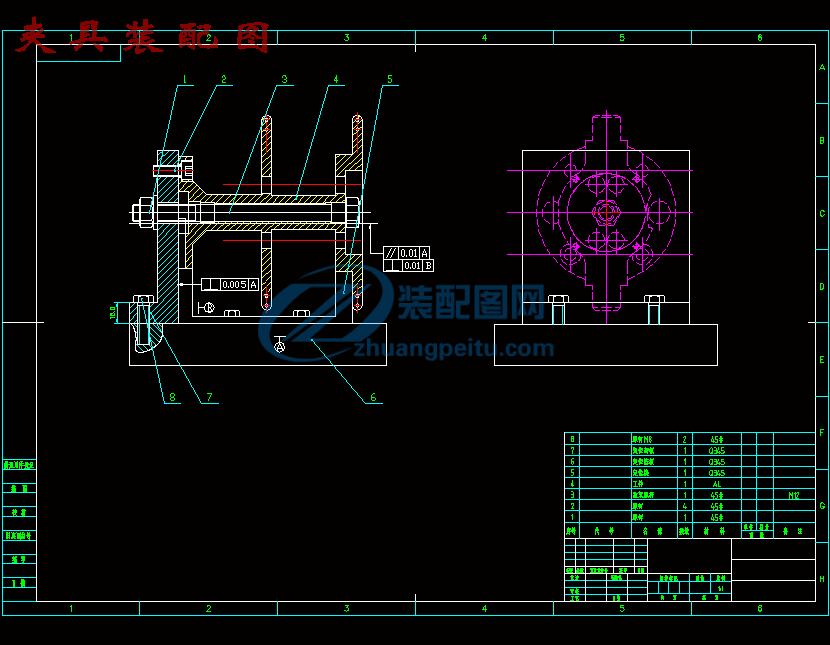
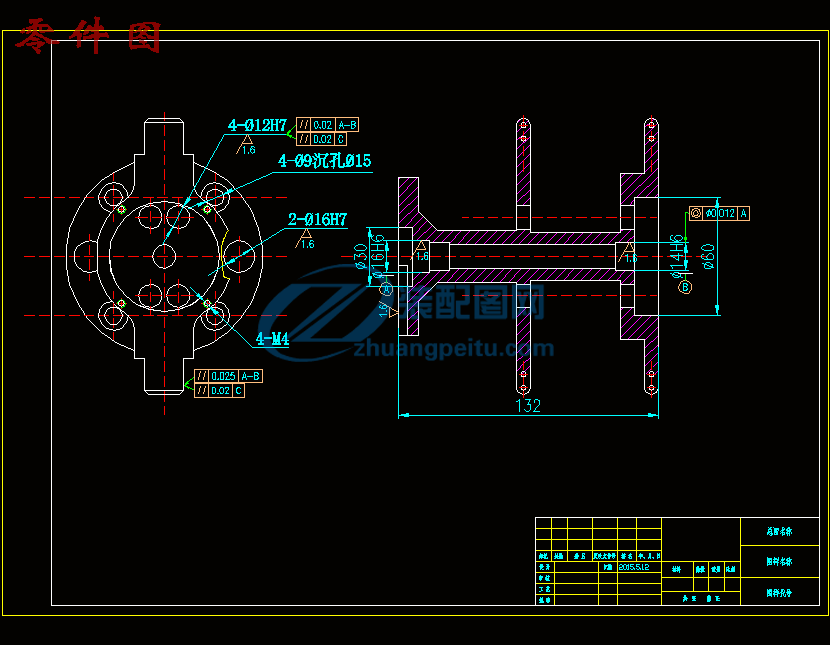
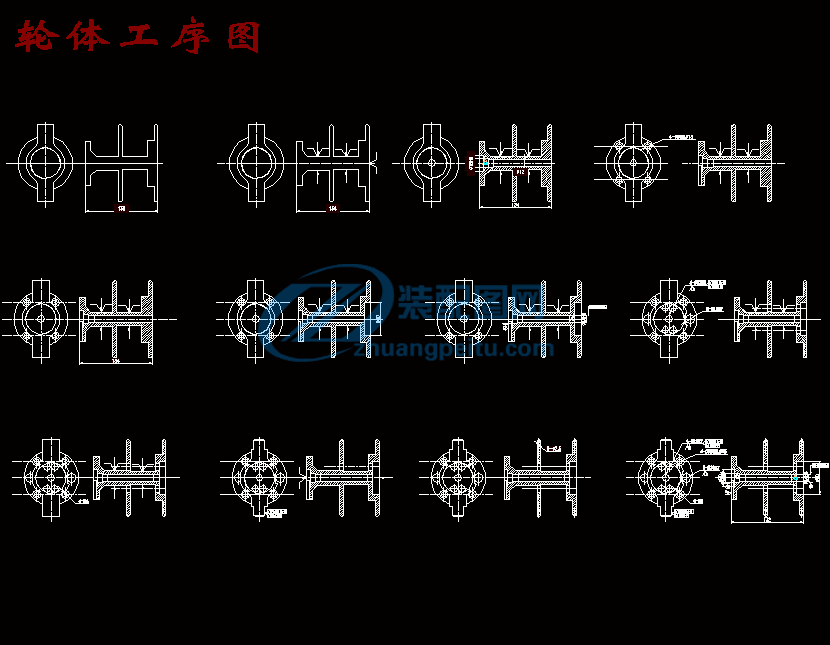
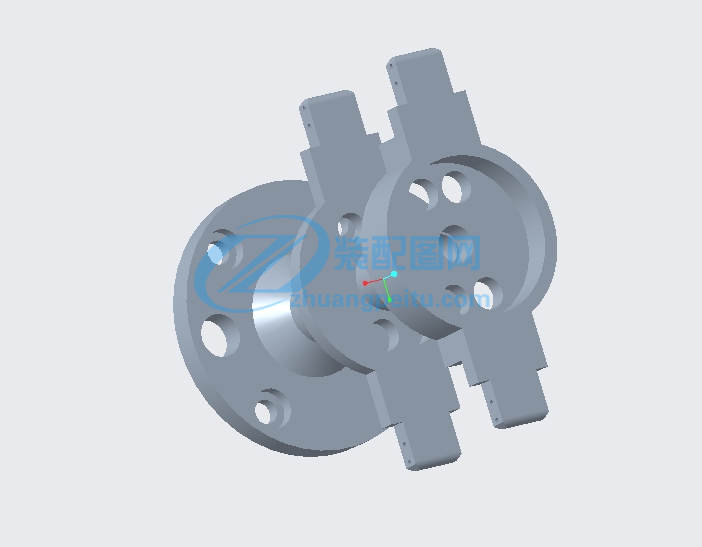
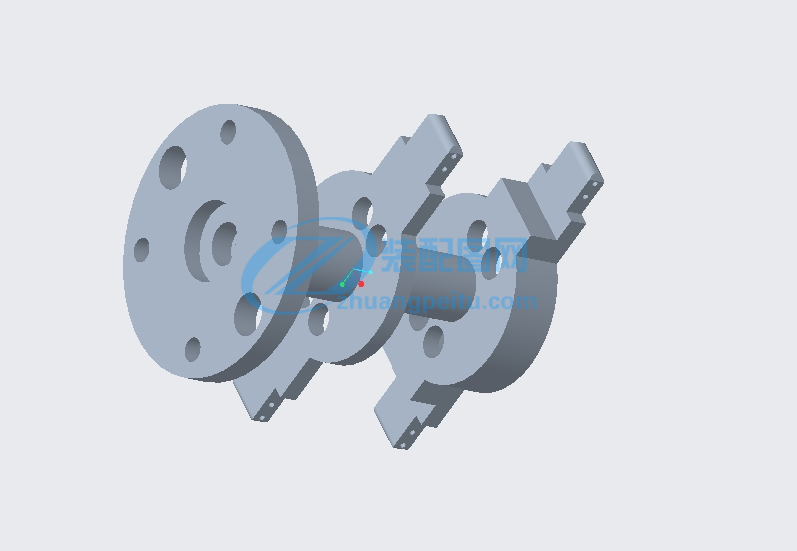
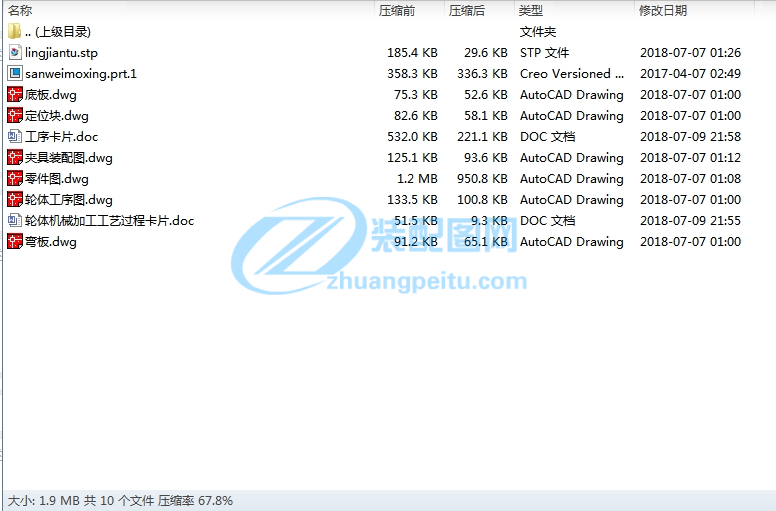
自動化夾具的規(guī)劃系統(tǒng)的發(fā)展 摘要:夾具是一個很重要的工業(yè)步驟。計算機輔助夾具設(shè)計技術(shù)在涉及制造規(guī)劃中迅速發(fā)展。自動化的夾具外形設(shè)計系統(tǒng)發(fā)展成被用來挑選自動組合夾具元件和把它們合適的放在裝配關(guān)系的位置上。在這篇論文里,一個自動化夾具設(shè)計系統(tǒng)只是呈現(xiàn)了夾具在基于工件幾何和可操作性上,夾具表面和位置都是自動化的。夾具的可及性、表面特征準確、夾具穩(wěn)定所面臨的主要問題都在夾具規(guī)劃中這個系統(tǒng)的開發(fā)在這篇論文里,夾具規(guī)劃和實施例被提出來了。 關(guān)鍵詞:精確度;夾具;夾具規(guī)劃;定位1.介紹夾具是一個重要的工業(yè)生產(chǎn)活動在工業(yè)周期中。計算機輔助夾具設(shè)計被廣泛應(yīng)用在CAD/CAM 中 [1]。CAFD 的發(fā)展對于減少交貨時間,制造運轉(zhuǎn)和審核的制造過程中的有很大的貢獻 [2]。CAFD在柔性制造系統(tǒng)(FMS)和計算機集成制造系統(tǒng)(CIMS)中扮演了一個很重要的角色 [3]。圖1 夾具設(shè)計制造系統(tǒng)圖1概括了活動在夾具設(shè)計制造系統(tǒng),它們包含三個主要領(lǐng)域:設(shè)置規(guī)劃,夾具規(guī)劃、夾具結(jié)構(gòu)設(shè)計 [4]。目標規(guī)劃,是決定設(shè)置機構(gòu)的數(shù)量,定位及發(fā)展方向的工件在每個設(shè)置,在每個加工面的也占有一席之地。夾具規(guī)劃定位和夾緊點了工件表面上。夾具結(jié)構(gòu)設(shè)計的任務(wù)是選擇夾具元件和把它們安置在貼合位置然后夾緊工件。一個自動組合夾具結(jié)構(gòu)設(shè)計系統(tǒng),在選定的工件摸具的表面和夾緊位置上,夾具單元和放置在自動生成位置協(xié)助夾具組件裝配關(guān)系上被廣泛的應(yīng)用發(fā)展 [4,5],本文論述了夾具規(guī)劃當夾具工件表面及位置時自動選擇的內(nèi)容。對夾具設(shè)計以往已經(jīng)出版了的文獻分析中,只有綜合夾具規(guī)劃系統(tǒng),是主要用于產(chǎn)生夾具計劃還沒有發(fā)展工業(yè)領(lǐng)域中的應(yīng)用。前期工作包括:自動測定方法的夾具定位和夾緊源自數(shù)學模型 [6];一種算法選擇的定位和夾緊的職位提供最大限度的機械杠桿作用 [7];基于運動學分析夾具的計劃 [8,9];一個夾具的等級和精度等級建立在夾具夾緊能力的分析上;在夾具設(shè)計中,自動選擇中安裝要考慮到定位誤差因素夾具設(shè)計[11],而且最后結(jié)合2D幾何夾具計劃系統(tǒng) [12]。在我們先前的研究中,夾具的特點 [13],夾具的精度 [14,15],幾何約束 [16],和夾具可及性表面 [17]都被研究過了。設(shè)置規(guī)劃和夾具設(shè)計的整體結(jié)構(gòu)被提出來了 [18]。在這篇論文里,當工件模型和設(shè)置規(guī)劃信息輸入系統(tǒng)時,自動夾具規(guī)劃體系,夾具設(shè)計在夾具的表面和關(guān)鍵點中被定義了。2.夾具設(shè)計的基本要求在工程實踐中,夾具設(shè)計的規(guī)劃是由許多因素組成的,包括工件的幾何信息和公差,設(shè)置規(guī)劃信息,就像加工特征,機床,和每個位置的刀具,在每個位置對于工件所產(chǎn)生的影響以及可夾緊的元件,確保一個夾具在一個合適的位置能夾緊,所以生產(chǎn)過程中可以根據(jù)國家標準而且必須滿足以下夾具要求來進行設(shè)計。1.當工件被固定住的時候,工件的自由度必須完全約束住。2.在當前的設(shè)置中要滿足加工精度的要求。3.夾具設(shè)計穩(wěn)定在抵制外部的影響力及力矩平衡。4.夾具表面和位置可以被可夾具元件輕易地通過5.在工件與夾具之間沒有干擾,以及在夾具和刀具之間。在本研究中,我們首先關(guān)注4個條件。夾具的計劃是基于以下進行考慮:1.盡管工件幾何是復(fù)雜的,但是在工業(yè)生產(chǎn)中,當工件是固定的時在大多數(shù)夾具設(shè)計、平面和圓柱表面(內(nèi)部和外部)被作為定位,夾緊表面,是靠著多方面的這些特性的測量。在本研究中,平面和圓柱表面都使用在夾具的計劃中。2.許多數(shù)控機床、特別是加工中心,可以用來在一個設(shè)置中做不同的作業(yè)。在大多數(shù)情況下,刀具軸機床是固定的。在考慮夾具穩(wěn)定性時、定位表面最好是反向正常的,還是垂直于刀具軸。鎖緊特征、法線方向應(yīng)符合,還是垂直于刀具軸,所以在夾具設(shè)計,應(yīng)該是與定位器夾緊力相反。3.給表面加工,都應(yīng)該有從尺寸和公差及其他的測量數(shù)據(jù)作為定位及發(fā)展方向的參考。在夾具規(guī)劃里、高精度的表面作為優(yōu)先選擇,作為定位表面,方便于,后面的加工誤差縮小,而且所要求的加工特征更方便實現(xiàn)。4.在夾具規(guī)劃中,在一個步驟里,超過一個工件表面是必須選擇用來夾緊和定位的,用來限制一個工件的自由度。因此,除了結(jié)合個人表面的條件以外,以可用的定位表面來結(jié)合現(xiàn)狀對于工件的精確定位是很重要的。5.因為夾具和定位器與工件有接觸,在保障夾具穩(wěn)定中,這些點的分布在夾具中起著至關(guān)重要的作用。6.一種可行的夾具設(shè)計,夾具表面必須要被與夾具元件所接觸。有效的使用夾具表面應(yīng)該是大得足以容納功能表面的夾具和定位器的表面。除了考慮夾具表面,在表面上的一些潛在的可接觸點對于決定最終的夾具點分布也是很重要的。3. 夾具表面裝置的概念已經(jīng)被廣泛的應(yīng)用于設(shè)計和制造業(yè),一個經(jīng)過機器加工的工件可以看作是諸如位面,步幅,多格行置地紙架,插槽和空洞的裝置的結(jié)合。在一個特殊的運轉(zhuǎn)裝置中,用來固定工件的裝置可以定義為定位裝置或者是表面定位。事實上,大部分的定位裝置都是二維圓柱形的曲面。根據(jù)夾具的功能,夾具的表面可以分類為定位,夾和合支撐夾具。與設(shè)計和制造業(yè)的家居裝置不同,夾具表面是從屬方向定位。他們在制造過程中不扮演相同的角色。一整套的表面裝置可以用于裝置組合中的夾具表面,但是可能不用于夾具本身或者在其他裝置組合中有不同功能的夾具。夾具裝置的概念允許與夾具幾何學有關(guān)的夾具需求。在一個基礎(chǔ)特征的家具模型中的裝置信息也可以直接用來表示夾具設(shè)計的目的。對于制造裝置來講,需要描述一個夾具裝置的信息包含幾何學和非幾何學的方面。前者包括型號,形狀和空間參數(shù),也包括工件的定位和方向。厚著包括表面裝飾,水平面精確和加工裝置和表面操作性的關(guān)系。3.1 夾具曲面的離散化在大多數(shù)的夾具設(shè)計中,夾具裝置,尤其是定位表面,是曲面和圓柱形表面。為了估計夾具表面裝置的可行性和夾具表面的決定性定位目標,一個備用夾具表面被抽象化為有著相同間隔的網(wǎng)格排列的離散的點 T。如果 T 足夠小,離散的抽樣點將會大部分的持續(xù)。為了讓抽樣算法變得普遍化,一個在表面外部邊框的長方形矩陣用于取樣區(qū)域。因為在大多數(shù)情況下,初始定位表面是垂直于其他定位表面,尤其是在動態(tài)反應(yīng)的夾具設(shè)計中,定位表面被看作是底部定位,頂部夾緊和側(cè)別定位,側(cè)邊加緊表面。對于有著標準方向 Z 的底部定位/頂部夾緊的表面,外部邊框的長方形區(qū)域的兩邊必須要平行于 X 軸,其他的兩個邊必須與這兩個邊垂直的平行于 Y 軸。對于底部定位/ 夾緊的表面,必須有2個邊平行于 z 軸,盡管其他的兩個邊必須垂直于前面兩條。圖形2展示了有著表面外部邊框長方形矩陣區(qū)域的備用抽樣定位表面的抽樣。Z 軸在表面定位備用系統(tǒng)中的正常這一猜想,在外部邊框長方形矩陣的內(nèi)部的重要之處可以表示為:x = Xmin + T ? u, u = 1,2, %, Nuy = Ymin + T ? v, v = 1,2, %, Nv (1)這些是在 X 和 Y 軸中的點 nu 和 nv ,分別的是Nu = int [(Xmax- Xmin)/T] and Nv = int [(Ymax - Ymin)/T]。圖2 一個夾具表面外邊框矩形的抽樣3.2 可及性表面的可及性夾具表面的可及性是一種無論夾具表面是否是夾具組成的一部分的衡量標準。三個主要因素必須考慮:1.夾具的幾何表面涉及有效面積和形狀的表面。2.法線方向上阻塞工件幾何形狀或者圍繞著夾具的幾何區(qū)域的表面。3.為達到夾具元件的功能,夾具元件的尺寸和形狀。在實際情況中, 工件的一個平面有復(fù)雜的形狀且法線上或者其他區(qū)域有完整或者局部的阻礙。因此需要,一個模型應(yīng)該全面反映這些事實以便一個合理的可及性與價值可廣泛應(yīng)用于個個夾具表面。表面可及性被定義為建立于在表面上每一個有效的采樣點的可及性的統(tǒng)計值,PA由兩部分組成:SIA 和NRA。SLA 符合大部分的夾具點中的單獨的可及性,然而NRA反映了夾具點的可延長性。SLA的一個樣本點以來于三個標簽的基礎(chǔ)上,標簽s1 用于表明無論方形網(wǎng)格標簽的中心是在夾具里面,表面或者外面,中心目前的采樣點就在里面,在,或在和家具的表面。三個離散值被指定代表它的地位,那就是,0、1、2,分別。如果存在在表面正常的方向和周圍采樣點上阻塞性工件幾何成型,會影響采樣點的可及性。舉個例子,在圖3中所看到的,在工件的一個表面上,采樣點p1是不是可以因為并沿工件底部位置的阻塞性幾何學的發(fā)展方向,P2 無論它周圍是不是有阻礙都無法進入。在表面法線方向,自動的評估是否存在的障礙物,一個虛擬的體積是在表面法線方向被由方形測試網(wǎng)格轉(zhuǎn)化成固體。通過使用一種檢測方法兩種固體實體之間是否有干擾,如圖3(b) 中所示的阻礙被確認。這種擠壓方法是方形網(wǎng)格標簽在側(cè)面定位和夾緊表面上有一點不同,這個面上方形網(wǎng)格標簽起初沿著底部定位方向,然后伸直標簽是沿著側(cè)面定位和夾緊表面上被擠壓成型,如圖4所示。屬性標簽s2是用來記錄檢查的結(jié)果在采樣點阻塞的結(jié)果。當這些受阻被檢測到,s2 = 1,否則,s2 = 0的圖片標簽。Detected, s2 = 1, otherwise, s2 = 0。檢測到,s2 = 1,否則,s2 = 0的圖片標簽。 如果發(fā)現(xiàn)測試網(wǎng)格上面采樣點不阻礙,其個體可觸性很大程度上取決于測試表面和夾具元件,由屬性標簽s 3表示,s3的定義公式是AreaI是接觸面積,T是邊長。在此基礎(chǔ)上三個屬性標簽,也是采樣點的p u、v 可以賦予一個數(shù)值根據(jù)以下規(guī)則:圖3. 阻塞檢查在樣本的有效點底部表面定位。 (@pi意味著被點Pi沿著其可接觸的方向執(zhí)行擠壓成型。 )圖4 阻礙在樣本點在邊緣定位或者夾緊表面時的檢查如果側(cè)面定位/夾緊而且 s1 ≠ OutsideOuterLoop則 在v反映了影響的重點的高度一邊定位/裝夾。在采樣點的周圍區(qū)域也會影響其可及性。在一個夾具的表面,當前的采樣點與周圍的其他采樣點的位置關(guān)系可以用3*3地圖來表示,在P c是當前采樣點的地方用一個離散型(u, v)來表示,P 1~P8是8個周圍點, 他們的位置如圖5所表示。NAR在當前點P u,v 可以使用公式:由于F k和kth周圍有接近關(guān)系的因素,可以建立在SLA的基礎(chǔ)上確定以及測量(s1, s2,s3) 。在底部定位或者頂部定位時,當側(cè)面定位或者夾緊時,一個有效的采樣點,一旦SLA,NRA同時知道, PA也能根據(jù)方程式被計算出來:圖 5. 在3 X 3方位圖中的當前點P c和8個相臨樣本點P 1~P8 從 SLA 和 NRA 定義 SIA 在射程為 0~ 1,NRA 的范圍為-1 ~ 1。因此,PA 必須在范圍-1~ 2。當 PA 是少數(shù)非零系數(shù),采樣點嚴重阻礙一種可行的夾具點。整體可訪問性(OA)家具表面的定義是通過值的總和檢驗樣本點,即:由于整體可及性是通過表面上,樣本點的可及性影響來判斷的,這些信息關(guān)于有效面積和形狀復(fù)雜的表面在模型上所展示。一般來說,模型,滿足標準的表面以較大的可及性數(shù)值比較小的可及性數(shù)值更加滿足要求。3.3 夾具精度的總體性特征最重要的任務(wù)之一是為夾具加工工件保證公差要求。特征的準確性被他們的公差和表面處理。一般來說,公差的功能分為兩種類型:尺寸精度和幾何公差。尺寸公差的大小表達關(guān)系的兩個特點的工件。如果有一個特征尺寸公差嚴格對加工特征,這意味著特征可以使用作為操作數(shù)據(jù)可能,即定位表面的設(shè)定?;跀?shù)據(jù)的特點是是否有需要,這次的公差可以進一步分成形式公差和位置公差。形式公差是只有特色的有關(guān)本身指定允許幾何變化特點。個人特征的適用性的夾具的數(shù)據(jù)。位置公差是相同的重要性夾具尺寸公差的計劃,因為它代表之間的一種關(guān)系的特點。為了評估特征的準確性和有效利用時間的方法在即可規(guī)劃、廣義精度等級是應(yīng)用于特征這次調(diào)查的定義是:都是重要因素。Tg ??(w1Td + w2Tp) * (w3Tf + w4Tr) (10)Td,p,Tf的尺寸精度等級,位置公差等級和形式分別公差等級。T r是公差等級等同于表面光潔度,w 1, w2, w3, and w4都是重要因素。這多個操作 “*”代表了一個主導的關(guān)系的地方一個零值可導致最后的結(jié)果,而經(jīng)營“+”代表著一個相對薄弱的關(guān)系偏好。T d,T p、T f,與 Tr可以通過陰影算法 [11,18] 中描述。4.自動化設(shè)備的發(fā)展規(guī)劃系統(tǒng)概述夾具計劃系統(tǒng)自動的展現(xiàn)為圖6。程序為夾具規(guī)劃可以是分開的到五個階段,包括輸入、分析、計劃、驗證、輸出。輸入的數(shù)據(jù)包括一個工件CAD模型含有幾何和寬容的信息特點和工藝設(shè)定工件,規(guī)劃信息包括特點和加工機床類型的特殊設(shè)置。這些數(shù)據(jù)可以提取也從CAD數(shù)據(jù)庫和用戶交互地通過了計算機輔助設(shè)計系統(tǒng)。分析涉及候選人的提取夾具相關(guān)信息的特點,精度和評價訪問夾具的特點。在這一研究中,平面和圓柱表面都考慮夾具的目的。任務(wù)的規(guī)劃,是決定自動主要定位方向,選擇最優(yōu)定位/夾緊表面和分在當前的設(shè)定。算法規(guī)劃發(fā)展的底(頭)和側(cè)定位/夾緊安排。精確定位是主要的原因,以確保,工件的加工精度。一旦定位/夾緊方案,確定相應(yīng)的夾具單元對夾具產(chǎn)生的分,均可使用夾具結(jié)構(gòu)設(shè)計系統(tǒng)(Fix-Des)發(fā)展以前 [19]。一個綜合項目被發(fā)展出來,為了最后的夾具設(shè)計,明確夾具元件的累計公差和工件精度的影響。圖6 夾具設(shè)計的步驟夾具設(shè)計的輸出量是一個在格式化的夾具設(shè)計中的夾具表面或者點用于夾具結(jié)構(gòu)設(shè)計。盡管夾具設(shè)計是建立在一些優(yōu)化規(guī)則上生成的,替代夾具設(shè)計也提供了進一步優(yōu)化或用戶證明。4.1 基本定位方向的定良分析在設(shè)備設(shè)計中,通常有3個參考定位的表面,那些表面決定工件的位置和方向?;径ㄎ槐砻媸侵饕ㄎ换鶞拭?,為了決定在當前的設(shè)置中立體位置和工件的方向,和約束工件3個自由度。基本定位表面是垂直于其他表面的,尤其是被用來應(yīng)用在模塊花夾具中。一般案例,基本定位表面可以是一個單獨的面或者是在同意方向上的多個在同一個或不同高度的面。基本定位表面的通常方向被稱為基本定位方向,需要在夾具規(guī)劃中第一個被決定。它應(yīng)該平行或垂直機床的刀具軸。假定工具軸是Vt=(Vx,V y,V z)。這些面與普通方向平行或與工具軸垂直,這些面被提取于工件模型中,他們的分類如下:Sfn代表一組表面,在基本定位方向上的法線方向上;f i(Vi,T gi,A i)代表法向矢量V i,廣義的精度等級T gi和一個可用區(qū)域 Ai;N f是這組里特點的數(shù)目的集合;Ns是這組里的特點數(shù)。如果基本定位方向是由V1(V1 x,V1 y,V1 z)和V1∈{V i}所決定的,以下指標是用于鑒定V i是否有按優(yōu)先順序排列:WA和WT1 是表面的重量因素和精確度, ,maxSA是這組區(qū)域里的最大限度的面,maxST是總體性的精度等級特征的最大值。如果得到In_V1,那么相應(yīng)的正常向量在基本定位方向上被確定。4.2底部定位和頂部定位的規(guī)劃夾具規(guī)劃在這個階段的任務(wù)是決定合適的主要位置和在表面上的定位點的分布,夾緊面和點與基準方向一致,在圖7中表示。圖. 7 垂直方向的一個夾具規(guī)劃程序所有基準面的集合能被表示為: Fi(Vi,T gi,C i)由一個正常向量 Vi,一個廣義精度T gi,等高線C i而且這個公式里Nf代表集點。當包含多個平面的時候,這些平面投射在基準方向上,形成了一個虛擬平面,通過他們的邊界實體就像線段和弧線。當這些面在離散點上被取樣的時候,一個外界區(qū)域在虛擬平面生成了。因為定位點不能太過于接近工件的外邊沿。矩形區(qū)域的大小被還原成向向它的中心邊界移動。最終定位點的投影將要在這個新區(qū)域被確定。然而,也有一些點可能是在表面之外,檢測是否是這個點標準算法是在一個特定的區(qū)域里。在基準定位方向中,3個方向上必須被約束3個自由度。3個點畫成一個3角形,而且工件的中心,為了保證定位的穩(wěn)定性,重心應(yīng)該在3角中被確定。最理想的定位方案由下面因素決定:1.三角形區(qū)域越大越好,公式:當S=0.5*(l1+l2+l3),而且l 1,l 2,l 3是三角形三條邊長。2.工件重心到三角形三個邊緣的距離要盡可能的大,公式為:這里 Di 是三角形的邊緣到工件重心的距離。3.位面廣義精度上的定位點的位置要盡可能的高(公差值要盡可能的?。?。公式為:4.三個定位點的可及性要盡可能的。公式為:這里 ACCi,A CCj,A CCk,是定位點的可及性。5.定位點的均衡應(yīng)該盡可能的一致。公式為:當上訴因素的值被獲得時,證明指數(shù)被用來定義最優(yōu)定位點,其中最小值是:這里 Ws,W T2,W C1,和 WH 分別是夾具穩(wěn)定性,精確度,可及性和統(tǒng)一高度的重力因素;maxTA,maxTL,和 maxTT 是所有垂直定位的標準因素。一旦確定了最后的定位點,包含了與三個定位點相對應(yīng)的定位表面。值得注意的是通過使用一個或更多的程序能被選擇作為主要定位條件。夾具類型的選擇主要涉及到加工方向上的力和可夾緊裝置的表面。加緊表面的確定基于以下的幾點因素:1,表面相對于底部表面定位。2,表面就是當前的加工表面。3,如果表面被投射進定位三角區(qū)域?qū)⒅睾稀?,在裝夾的時候表面是容易處理的。一旦夾緊表面被確定,最優(yōu)夾緊點被選中以至于夾緊力就是對一個方向的底定位器或者在底定位三角形。在上訴步驟后,產(chǎn)生了所有可行的對底部定位和對頂部定位的夾緊計劃并且被優(yōu)先確定。每一個夾緊計劃的文件包含了夾緊信息,例如,夾具功能,定位夾緊表面,表面位置和定位夾緊點的坐標。4.3側(cè)定位夾緊規(guī)劃在水平方向的夾緊計劃包括側(cè)定位和夾緊計劃。側(cè)定位是用來確定非主要的定位點與定位表面。側(cè)定位最普遍的方法是標準的 3-2-1 定位原理。在這樣的情況下,側(cè)定位計劃選擇兩條相互垂直的邊作為第二和第三定位表面,并且這些邊分別包含了兩個和一個定位表面。當設(shè)計一個夾緊裝置時這些夾緊方案是優(yōu)先的用來控制定位精度,因為其是在不同自由度上是獨立約束的。然而,在很多情況下,是非常困難的去發(fā)現(xiàn)這種相互垂直的定位夾具設(shè)計。一個非常普遍的情況,有時柱面和不、垂直的邊也被用來作為定位表面。這三個側(cè)定位點分布在三個不同的表面。在這項研究中提供了解決情況,包括標準的 3-2-1 情況作為有限的解決方案。為了選擇合適的側(cè)定位表面,一般情況下,考慮到廣義的精度等級,可及性價值和候選表面形狀。這些負荷側(cè)邊定位原理的的特性被表示為:這里 fi(V i,T gi,A cci,C i)是一個一般向量 Vi,一般精度等級 Tgi,一個可及性 Acci和輪廓 Ci 的特性; Nf 是特性的數(shù)量。為了限制來自于主要定位的剩余的三個自由度,需要多個加工表面來作為側(cè)定位。如上所訴,除了個別表面的情況,結(jié)合現(xiàn)狀,候選加工表面在工件定位時也是一個重要的因素。對于這兩種定位特點,有許多組合能被使用在側(cè)定位中。以下是部分優(yōu)先組合的列表:1. 互相垂直得兩個位面2. 不垂直的兩個位面3. 三個位面4. 一個位面和一個柱面5. 兩個柱面6. 一個位面和兩個柱面,顯示在圖8中?;谶@些組合的類型,特征群體能夠建立表示為:圖8 包含了6種類型,1號為兩個垂直面,2號為兩個非垂直面,3號為兩個非平行面,4號為一個圓周面跟兩個平面相交,5號為兩個圓周平面,6號為一個平面跟兩個圓周面。LHCm={fi|i=1,2or1,2,3,f i ∈LH} , (21)m=1, 2,…… ,Nm在這個公式里面,f i起著主導作用,N m為一個數(shù)集。每個特征組里面包含了兩到三個特征,衡量特征組的標準包含以下幾點:1.特征組合形式,一重量系數(shù),HF,被指定到不同定位面的組合類型中,如果特征組包含了兩個垂直面,則為最優(yōu)先選擇,如果包含了三個圓周面,則相反。2. 特征組的廣義精度等級劃分。廣義上的特征組通常都被用于所有的特征當中,HT=Ti的總和,在特征組里面, Ti是廣義的精度等級,而 i是1,2,3的數(shù)。3.特征組的重要性。在特征組里面,沒個面的重要性都有被考慮,HC={Acci|i=1,2or3} ,在所選的水平面特征中, Acci是極重要的。當以上的參數(shù)都被包含進去時,下面的公式則可以用于確定最好的基準面。In_Hl=HF+WT3*HTi/maxHT+WC2*HCi,Ns>i>l (22)在公式里面,W T3和W C2是分別的并且可以達到的重量系數(shù),而maxHT是標準系數(shù)。當定位基準平面分類于每個組中時,定位高度就會被確定。預(yù)期結(jié)果是所有的定位元件,跟夾具一樣,都被放置在同一個高度,或者定位點的高度差為最小。圖9. 工件模型和側(cè)交叉定位平面一旦定位高度被確定,有效的定位基準平面在2D直線與圓弧或者圓之間,這些2D定位區(qū)域能直接在CAD加工模型中反映出來。圖 9所顯示的是一個定位高度的橫截面。在2D線性片段中,定位點的位置是確定的,建立在不同的表面跟點上面,要想解決定位問題,必須滿足兩個條件 [16],第一,在正常加工過程中,定位的基準平面是不會絕對平行的。第二,當給出一個含糊不清的工作位置時,三個基準點是不會重合于一點的。對于通用夾具的穩(wěn)定性來說,當這個平面為基準面的對立面時,面夾具就比較適合,當在決定夾緊面與定位點的時候,一個完整的解決方案就會被提出。圖10顯示的是面夾具的定位選擇過程。圖. 10 在水平方向夾具規(guī)劃的一個程序.5. 實例和結(jié)論Fix-Des是一個夾具設(shè)計系統(tǒng),它的發(fā)展結(jié)合了 CAD系統(tǒng)和自動化設(shè)備配置系統(tǒng)。CAD系統(tǒng)作為平臺,適用于提供系統(tǒng)與輸入必要信息,F(xiàn)ix-Des是用來產(chǎn)生夾具結(jié)構(gòu)設(shè)計用于Fix-Planning的輸出。圖11具體體現(xiàn)了系統(tǒng)菜單顯示8功能模塊。SysSetup被用來在執(zhí)行任務(wù)計劃之前初始化系統(tǒng)。系統(tǒng)初始化的一個例子被顯示在圖12,規(guī)劃條件在定制的地方被設(shè)置,如夾緊類型、最小面積為定位器的高度和最低位置定位器在水平位置和影響著垂直位置的主要因素是先后順序。文件是用來從CAD數(shù)據(jù)庫讀取工件規(guī)格的,是用來儲存夾具外形設(shè)計的夾具方案的。LocatingDir是為了確定工件主要定位的方向??杉靶允菉A具的特點和目的中的輔助功能。該算法對于側(cè)面和底部定位/夾緊在水平定位,水平夾緊,垂直定位和垂直夾緊的模塊中固定。當夾具設(shè)計完成的時候,結(jié)果優(yōu)先也被顯示出來。圖11 整體的Fix-Planning系統(tǒng)圖12 系統(tǒng)初始化的例子標簽1 可及性分析的結(jié)果(BL –底部定位;SL –邊上定位;SC –邊上夾緊;TC –頂部夾緊) 。例如工件在圖9(a )中在 F46表面上所執(zhí)行的加工步驟。標簽1中顯示了后補加工面的易用性評估,而且圖13顯示,在后補加工面的底部定位中可及性點的分布。在水平和垂直方向,夾具規(guī)劃的結(jié)果如圖14??赡芙Y(jié)果并不是一定的。在圖14中表示夾具結(jié)構(gòu)設(shè)計中,替補計劃一樣是不可少的。圖15顯示了夾具的設(shè)計。在例子中所見,夾具表面和點的自動化選擇建立在很多因素的考慮中,包括精度等級,夾具穩(wěn)定性還有夾具表面可及性。在系統(tǒng)中,工件的幾何信息直接從CAD模型中引出,機構(gòu)的設(shè)計信息被輸入,而且平面和圓柱表面都被視為夾具表面。夾具表面組織建立了垂直和水平的計劃。替代方案提供了進一步的優(yōu)化和使用準確。在使用先前的發(fā)展系統(tǒng)Fix-Des時,接觸點也被自動確定,為了夾具結(jié)構(gòu)設(shè)計而被輸出。該系統(tǒng)的應(yīng)用程序?qū)е聹p少交貨時間的偉大計劃,因此也會響應(yīng)在生產(chǎn)設(shè)計中對于制造系統(tǒng)的能力的增強的改變。圖 13. PA是在以底部面F23 定位時,樣本點的靜態(tài)值(a)在F23表面上樣本點的分布。 (b)PA是在面F23 上所有樣本點的靜態(tài)值。圖14(a) 水平定位/裝夾的例子。 (b) 垂直定位例子。 (c )對應(yīng)垂直定位的垂直夾緊的例子。圖15 夾具結(jié)構(gòu)設(shè)計的最后結(jié)果。 (a)2D俯視圖。 (b)3D消除隱藏線視圖。參考文獻[1]. A. J. C. Trappey and C. R. Liu, “A literature survey of fixturedesign automation”, International Journal of Advanced Manufacturing Technology, 5(3), pp. 240–255, 1990.[2]. Y. Rong and Y. Zhu, “Computer-aided modular fixture design and management in computer-integrated manufacturing systems’, Japan-USA Symposium on Flexible Automation, Kobe, Japan, 11–18 July, pp. 529–534, 1994.[3]. B. S. Thompson and M. V. Gandhi, “Commentary on flexible fixturing”, Applied Mechanics Review, 39(9), pp. 1365–1369,1986.[4]. Y. Rong and Y. Bai, “Automated generation of modular fixture configuration design”, Journal of Manufacturing Science and Engineering, 119, pp. 208–219, May 1997.[5]. Y. Bai and Y. Rong, “Modular fixture element modeling and assembly relationship analysis for automated fixture configuration design”, Journal of Engineering Automation, 4(2), pp. 147–162,1998.[6]. Y. C. Chou, V. Chandru and M. M. Barash, “A mathematical approach to automatic configuration of machining fixtures: analysis and synthesis”, Journal of Engineering for Industry, 111, pp. 299–306, 1989.[7]. E. C. De Meter, “Selection of fixture configuration for the maximization of mechanical leverage”, Manufacturing Science and Engineering, ASME WAM, New Orleans, LA, 28 November–2 December 1993, PED-4, pp. 491–506, 1993.[8]. R. J. Menassa and W. DeVries, “A design synthesis and optimization method for fixtures with compliant elements”, Advances in Integrated Product Design and Manufacture. ASME WAM, PED-47, Dallas, TX, 25–30 November, pp. 203–218, 1990.[9]. M. Mani and W. R. D. Wilson, “Automated design of workholding fixtures using kinematic constraint synthesis”, 16th NAMRC, pp. 437–444, 1988.[10]. S. K. Ong and A. Y. C. Nee, “A systematic approach for analysing the fixturability of parts for machining”, ASME WAM, San Francisco,CA, 12–17 November 1995.[11]. J. R. Boerma and H. J. J. Kals, “Fixture design with FIXES: the automated selection of positioning, clamping and support features for prismatic parts”, Annals CIRP, 38, pp. 399–402, 1989.[12]. R. C. Brost and K. Y. Goldberg, “A complete algorithm for synthesizing modular fixtures for polygonal parts”, IEEE Transactions on Robots and Automation, 12(1), pp. 31–46, 1996.[13]. Y. Rong, J. Zhu and S. Li, “Fixturing feature analysis for computeraided fixture design”, Intelligent Design and Manufacturing, ASME WAM, New Orleans, LA, 28 November–3December, PED-64, pp. 267–271, 1993.[14]. Y. Rong and Y. Bai, “Machining accuracy analysis for computeraidedfixture design”, Journal of Manufacturing Science and Engineering,118, pp. 289–300, August 1996.[15]. Y. Rong, W. Li and Y. Bai, “Locator error analysis for fixturing accuracy verification”, Computer in Engineering, Boston, MA, 17–21 September, pp. 825–832, 1995.[16]. Y. Wu, Y. Rong, W. Ma and S. LeClair, “Automated modular fixture design: geometric analysis”, Robotics and Computer-Integrated Manufacturing, 14, pp. 17–26, 1998.[17]. J. Li, W. Ma and Y. Rong, “Fixturing surface accessibility analysis for automated fixture design”, 26th NAMRC, Atlanta, GA, 19–22 May 1998.[18]. Y. Rong, X. Liu, J. Zhou and A. Wen, “Computer-aided setup planning and fixture design”, International Journal of Intelligent Automation and Soft Computing, 3(3), pp. 191–206, 1997.[19]. W. Ma, Z. Lei and Y. Rong, “Fix-Des: a Computer-aided Modular Fixture Configuration Design System”, International Journal of Advanced Manufacturing Technology, 1988; partially presented at ASME Computer in Engineering Conference, Sacramento, CA,14–17 September 1997, DETC97/CIE-4281.[20]. Y. Wu, Y. Rong, W. Ma and S. LeClair, “Automated modular fixture design: accuracy analysis and clamping design”, Robotics and Computer-integrated Manufacturing, 14, pp. 1–15, 1998; partially presented at ASME IMECE, Dallas, TX, 16–21 November 1997.外文翻譯原文Development of Automated Fixture Planning SystemsW. Ma, J. Li and Y. RongDepartment of Mechanical Engineering, Worcester Polytechnic Institute, Worcester, MA, USAFixturing is an important manufacturing activity. The computeraided fixture design technique is being rapidly developed to reduce the lead time involved in manufacturing planning. An automated fixture configuration design system has been developed to select automatically modular fixture components and place them in position with satisfactory assembly relationships.In this paper, an automated fixturing planning system is presented in which fixturing surfaces and points are automatically determined based on workpiece geometry and operational information. Fixturing surface accessibility, feature accuracy, and fixturing stability are the main concerns in the fixture planning. The system development, the fixture planning decision procedure, and an implementation example are presented in the paper.Keywords: Accuracy; Clamping; Fixture planning; Locating1. IntroductionFixturing is an important manufacturing activity in the production cycle. A computer-aided (or automated) fixture design (CAFD) technique has been developed as part of CAD/CAM integration [1]. The development of CAFD contributes to the reduction of manufacturing lead time, the optimisation of manufacturing operations, and the verification of manufacturing process designs [2]. CAFD plays an important role in flexible manufacturing systems (FMS) and computer-integrated manufacturingsystems (CIMS) [3].Figure 1 outlines the activities for fixture design in manufacturing systems which include three major aspects: set-up planning, fixture planning, and fixture configuration design [4]. The objective of set-up planning is to determine the number of setups, the position and orientation of the workpiece in each setup, and also the machining surfaces in each set-up. Fixture planning determines the locating and clamping points on workpiece surfaces. The task of fixture configuration design is to select fixture components and place them into a final configuration to fulfil the functions of locating and clamping theworkpiece. An automated modular fixture configuration design system has been developed in which, when fixturing surfaces and points are selected on the workpiece model, fixture units are automatically generated and placed into position with the assistance of fixture component assembly relationships [4,5]. This paper deals with fixture planning when the fixturing surfaces and positions on the workpiece are selected automatically.Fig. 1. Fixture design in manufacturing systems.Previous papers on fixture design analysis have been published,but a comprehensive fixture planning system which can be used to generate fixture plans for industrial applications hasnot been developed. Previous work includes: a method for the automated determination of fixture location and clamping derived from a mathematical model [6]; an algorithm for theselection of locating and clamping positions which provide the maximum mechanical leverage [7]; kinematic analysis based fixture planning [8,9]; a fixturing grade and dependency grade based fixturability analysis [10]; automated selection of set-ups with consideration of tolerance factors of orientation errors in fixture design [11], and finally a geometric analysis based 2D fixture planning system [12]. In our previous research, fixturing features [13], fixturing accuracy [14,15], geometric constraints [16], and fixturing surface accessibility [17] have been studied. A framework has been developed for set-up planning andfixture design [18]. In this paper, an automated fixture planning system, Fix-Planning, is presented where fixturing surfaces and points are determined when the workpiece model and set-up planning information is input to the system.2. Basic Requirements of FixturePlanningIn engineering practice, fixture planning is governed by a number of factors, including workpiece geometric information and tolerance; set-up planning information such as machining features, the machine tool and cutting tools to be used in each set-up; initial and resulting forms of the workpiece in each set-up; and available fixture components. To ensure that the fixture can hold the workpiece in an acceptable position so that the manufacturing process can be carried out according to the design specifications, the following conditions should be satisfied for a feasible fixture plan.1. The degrees of freedom (DOF) of the workpiece are totally constrained when the workpiece is located.2. Machining accuracy specifications can be ensured in the current set-up.3. Fixture design is stable to resist any effects of external force and torque.4. Fixturing surfaces and points can be accessed easily by available fixture components.5. There is no interference between the workpiece and the fixture, and between the cutter tool and the fixture.In this investigation, we focus on the first four requirements.Fixture planning is carried out based on the following considerations:1. Although the workpiece geometry can be complex in industrial production, in most fixture designs, planar and cylindrical surfaces (internal and external) are used as the locating and clamping surfaces because of the ease of access and measurement of these features when the workpiece is fixed. In this investigation, planar and cylindrical surfaces are used in fixture planning.2. Many CNC machines, especially machining centres, can be used to perform various operations within one set-up. In most cases, the cutting-tool axis of the machine tool is fixed. When considering fixturing stability, the locating surfaces are preferably those with normal directions opposite to, or perpendicular to, the cutting-tool axis. For clamping features, the normal directions should be in line with, or perpendicular to, the cutting-tool axis, because, in fixture design, clamping forces should be against locators.3. For the surfaces to be machined, there should exist datum surfaces which serve as position and orientation references from which other dimensions and tolerances are measured. In fixture planning, surfaces with high accuracy grades should be selected preferentially as locating surfaces so that the inherited machining error is