【溫馨提示】壓縮包內(nèi)含CAD圖有下方大圖片預(yù)覽,下拉即可直觀呈現(xiàn)眼前查看、盡收眼底縱觀。打包內(nèi)容里dwg后綴的文件為CAD圖,可編輯,無水印,高清圖,壓縮包內(nèi)文檔可直接點(diǎn)開預(yù)覽,需要原稿請自助充值下載,所見才能所得,請見壓縮包內(nèi)的文件及下方預(yù)覽,請細(xì)心查看有疑問可以咨詢QQ:11970985或197216396
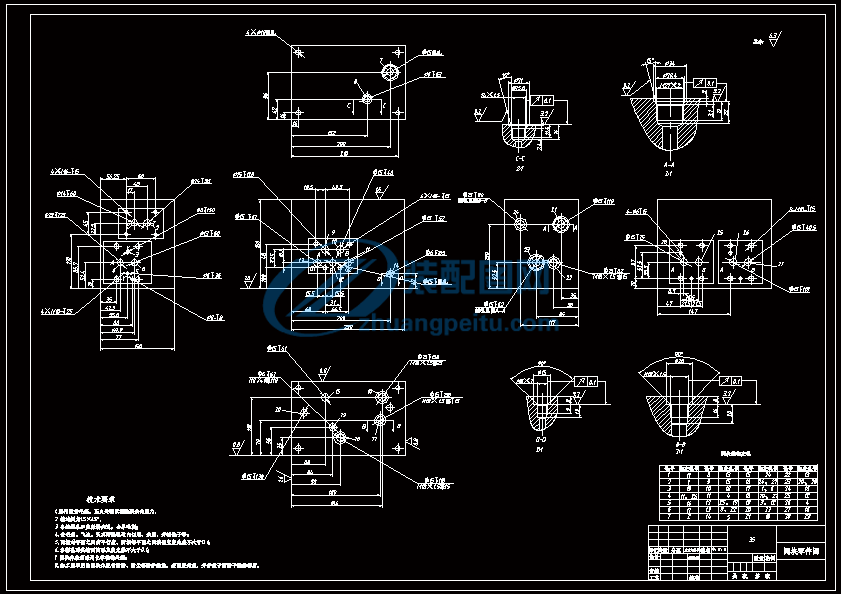

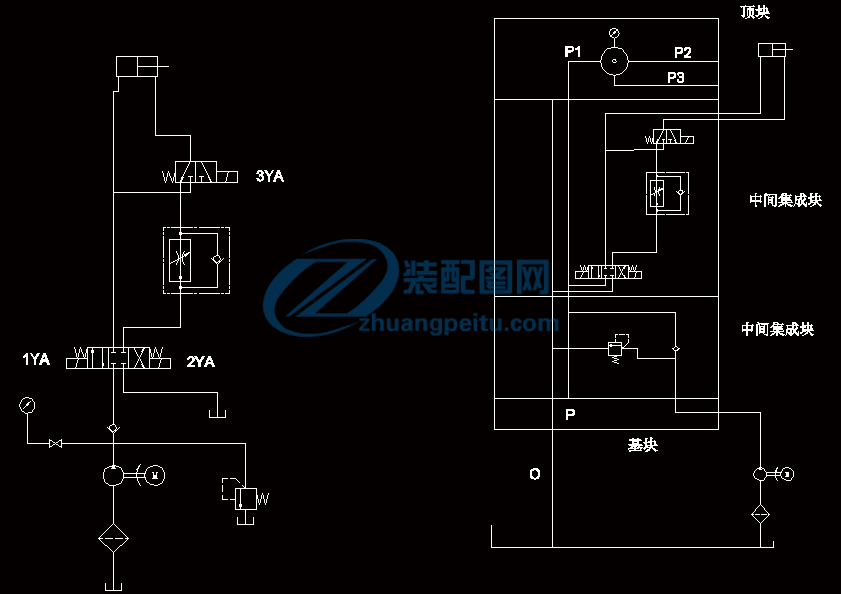
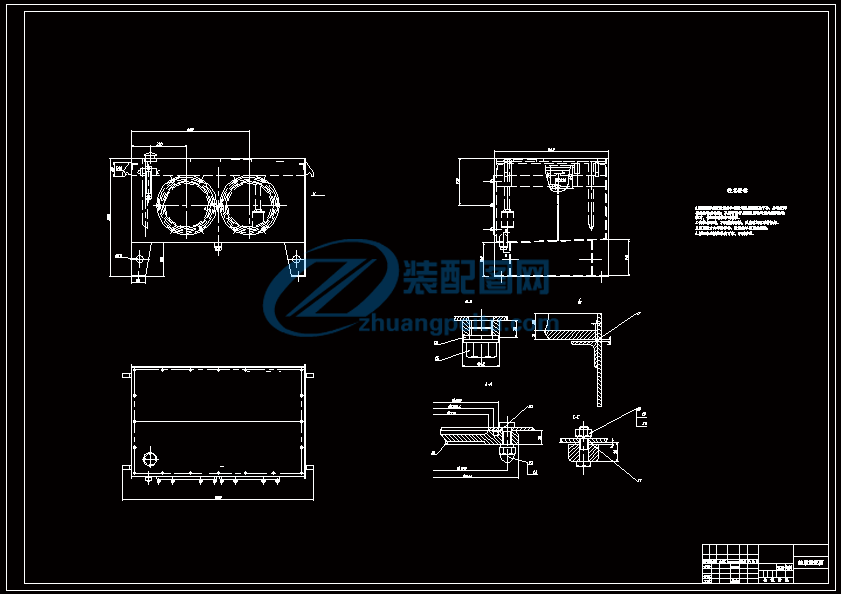
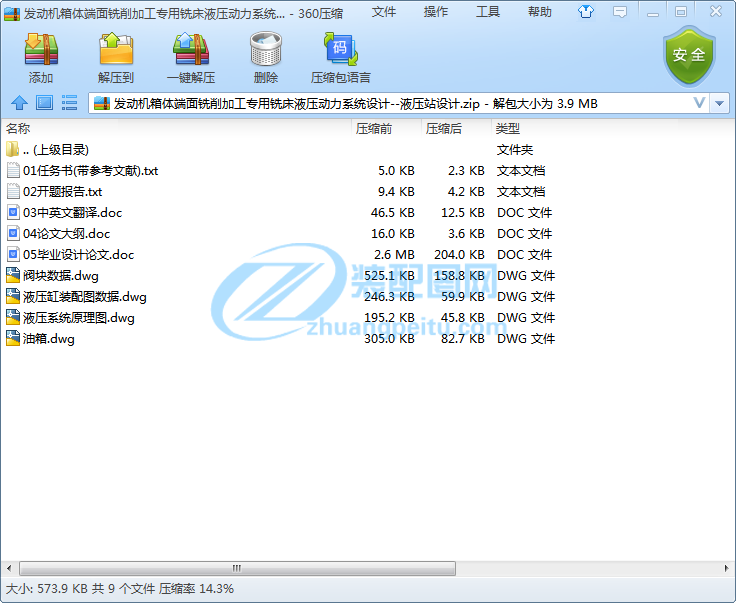
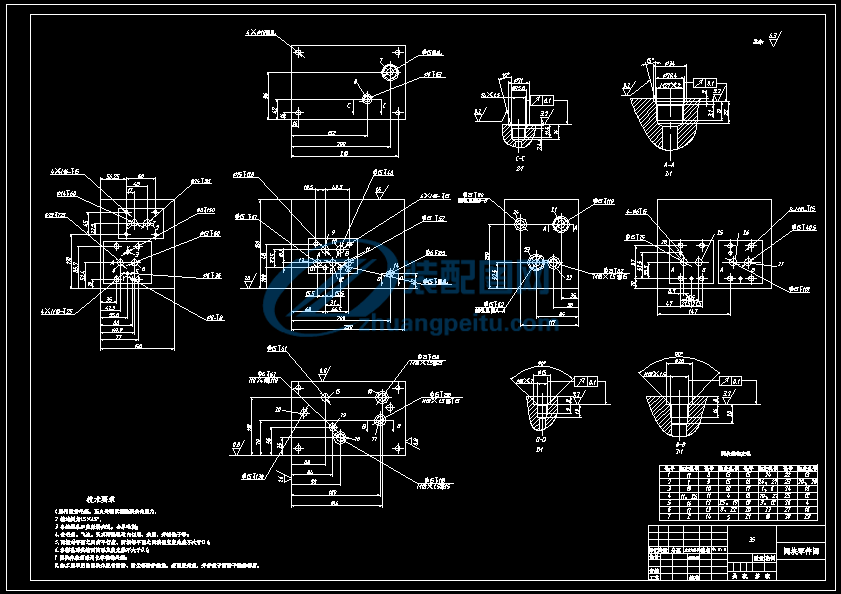
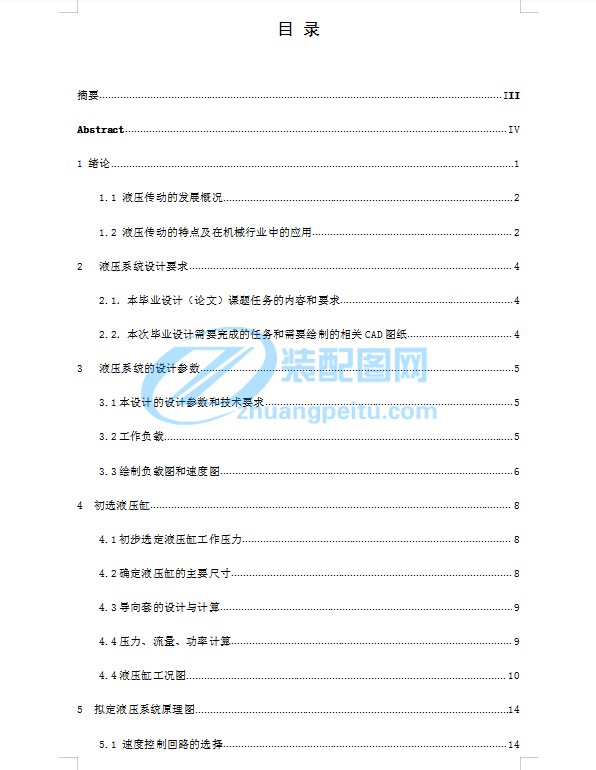
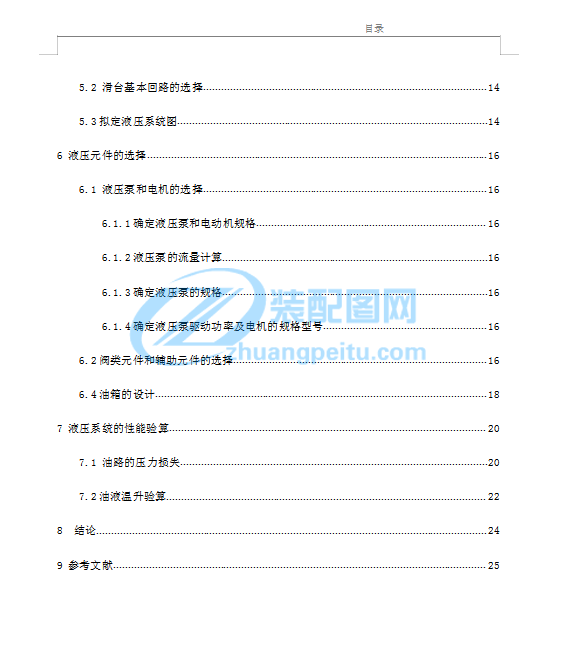
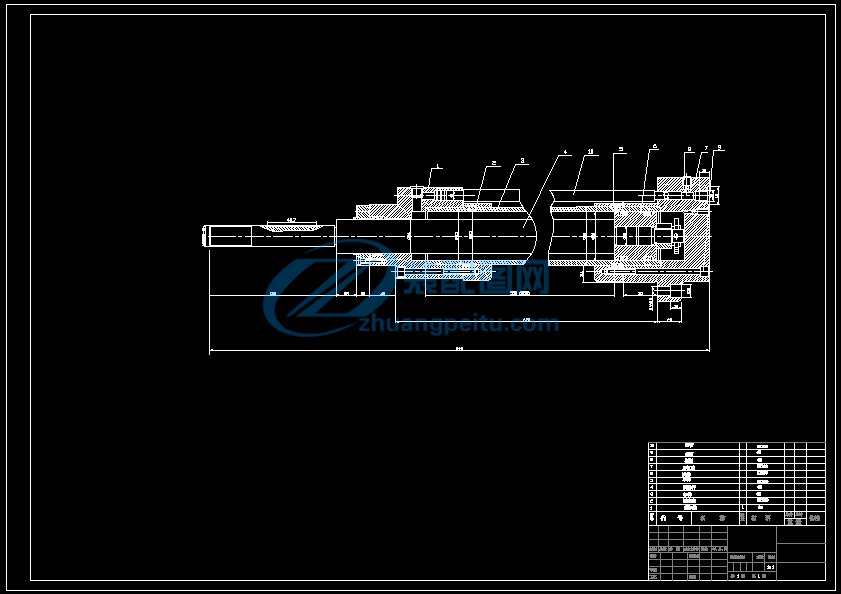
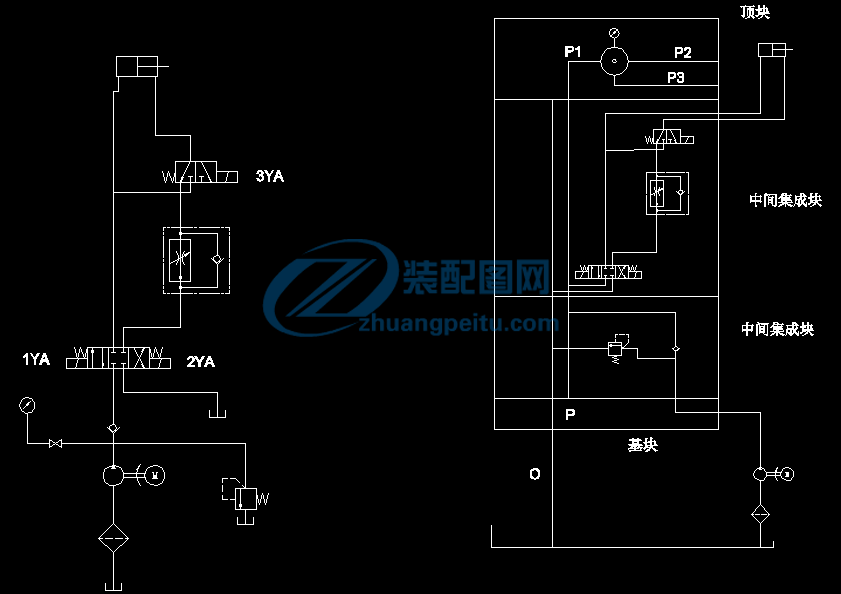

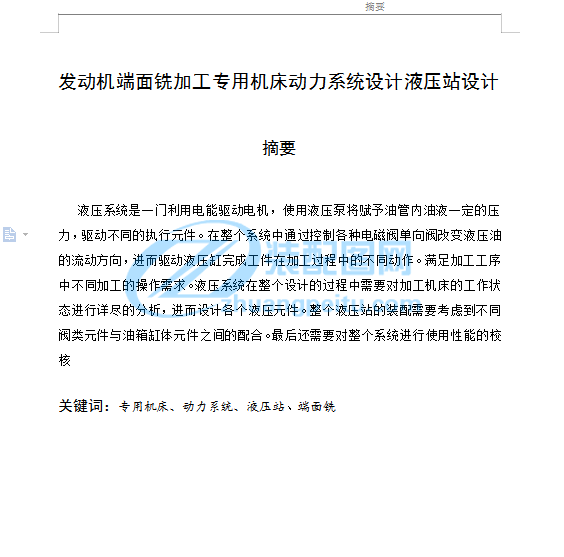
畢 業(yè) 設(shè) 計(論 文)外 文 參 考 資 料 及 譯 文
譯文題目:MACHINE TOOL AUXILIARY FUNCTION HYDRAULIC SYSTEM
學(xué)生姓名:
?! I(yè):
所在學(xué)院:
指導(dǎo)教師:
職 稱:
An auxiliary-function hydraulic system is provided for a computerize-d numerical control (CNC) machine tooling unit.
Hydraulic power is provided for locking collet or chuck to an open or closed position and providing an affirmative collet-open and/or collet-closed signal to communicate the collet position to the host computer.
The tailstock can be brought gently forward to contact a workpiece and can be returned rapidly to the home position, with a break- Away pressure feature being employed to overcome initial static friction. A pressure switch indicates that the tailstock is in position against the workpiece. A spindle brake applies braking to the spindle to stop the same from high speed either on command or in the event of system failure. In the latter case, braking occurs prior loss of pressure to the collet closer cylinder. Also, a turret clamp locks and unlocks a tool changer turret.
MACHINE TOOL AUXILIARY FUNCTION
MACHINE TOOL AUXILIARY FUNCTION
HYDRAULIC SYSTEM
BACKGROUND OF THE INVENTION
This invention relates to hydraulic systems which are employed in automatic machining equipment. The present invention is more particularly directed to a hydraulic system for a machining device which has a rotary spindle that has an openable and closable collet of chuck, a tailstock slide that contacts and supports a workpiece in the collet or chuck, a tool selection turret, and a spindle brake, all of which are hydraulically actuated and all of whose conditions can be hydraulically monitored. Preferably, the machining device can be a computerized numerically controlled (CNC) machine tool, of which there are several well known designs.
CNC machinery equipment enjoys the advantages of fast machine cycle times, high precision, consistent dimensional accuracy, flexibility of operation, and ease in programming to machine any specific workpiece
automatically into a finished, machined product.
Generally, the machining equipment has an enclosure or cabinet, which holds the machining tools and also confines any metal dust or by-product, and also maintains an even temperature to preclude loss of accuracy due to thermal expansion.
Within the cabinet there is a spindle which holds acollet, chuck, or jaw into which a workpiece or part is secured for a machining operation. The collet is automatically opened and shut. A spindle brake is automatically applied when required to halt rotation of the spindle. A tailstock slide moves hydraulically between a home position remote from the associated workpiece,and a forward position with the tailstock against and supporting the workpiece. A turret clamp prevents the turret from rotating out of position when a tooling operation is carried out, but is moved to an unclamp position when it is necessary to rotate the turret to bring another
tool into position.
The machine tool industry has long sought a simple, but reliable hydraulic system that performs the necessary functions, and also provides positive signals to indicate collet open and closed condition, spindle brake actuation, tailstock position and system pressure. Control and signal of the tailstock is especially important so that the tailstock can be brought with gentle but firm pressure against the workpiece to permit handling of light, fragile parts as well as heavy, lengthy, or bulky workpieces. However, until this invention, no completely suitable hydraulic system has been provided for automated machining equipment.
OBJECTS AND SUMMARY OF THE
INVENTION
Accordingly, it is an object of this invention to provide a modular hydraulic system for an automated ma-chine tool unit which avoids drawbacks of the prior art.
It is a more specific object of this invention to provide a hydraulic system which automates power and control of critical machine functions in a CNC machining device.
It is a more particular object of the invention for the hydraulic system to provide total hydraulic power on demand; automated control of tailstock forward and home movement; provision of tailstock-in-position signal to communicate to the CNC host computer that the tailstock is in contact with the workpiece; collet-open and collet-closed signals to communicate to the host computer that the collet is in its respective open or closed position; application of spindle brake pressure automatically to stop the spindle from high speed, even in the event of system failure ;brake-on signal to communicate to the host computer that the spindle brake is being applied; and automatic turret clamp/unclamp to lock or unlock the turret for tool selection and automatic signaling that hydraulic pressure exists.
In addition, it is an object of this invention for the hydraulic system to include tailstock speed control and break-away pressure features, as well as increased movement speed to the home position for faster cycle time.
In accordance with one aspect of this invention the hydraulic assembly has a hydraulic circuit that includes a reservoir, a hydraulic pump, a pressure supply line carrying pressurized hydraulic fluid from the pump, a return line carrying fluid to the reservoir, an accumulator for coupled to the supply line for storing a quantity of the fluid substantially at the pressure of the pump.
When the hydraulic system is powered up, the variable speed pump senses the immediate demand of pressure and flow. The variable-speed system pump delivers maximum flow to bring system pressure up to full capacity, then reduces output automatically to maintain set pressure. In addition, the pump charges a hydraulic accumulator which supplements instantaneous system power demands which the pump could not satisfy on its own. The system pressure is communicated to a circuit manifold, which also connects to the tank or reservoir.
A tailstock cylinder assembly has a cylinder coupled to the tailstock slide, the cylinder being double acting, with first and second hydraulic ports or connections, and a tailstock valve coupled between the first and second ports and the supply and return lines. The tailstock valve is preferably actuable from a neutral position to either of a forward position or a home position. A tailstock pressure regulator between the supply line and the tailstock valve provides reduced hydraulic pressure through the valve to the cylinder. A pressure sensor coupled to the first hydraulic port senses the hydraulic pressure on the cylinder. This sensor detects a pressure drop that indicates the tailstock has contacted the workpiece, and then supplies a tailstock-in-position signal to the computer.
A bypass valve selectively bypasses the tailstock pressure regulator momentarily to overcome static friction. Also an adjustable orifice between the tailstock valve and return line controls the travel speed of the tailstock slide to the forward position, but can be bypassed to permit rapid travel to home.
A pair of pressure detectors are also associated with a hydraulic cylinder used to open and close the collet .Here a collet valve is actuable to move between a collet-open and a collet-closed position. The pressure detectors respectively give positive signal indications when the cylinder reaches the end of its travel to communicate to the computer that the collet is fully opened or closed.
The spindle brake is also cylinder actuated, In the preferred embodiment, the spindle brake employs a single acting cylinder that is pressure-closed and spring-opened. Here also, a pressure detector at the hydraulic port to the brake cylinder gives an affirmative indication that the brake is being applied. In this embodiment, a brake valve has a normal condition in which pressure is applied from the supply line to the valve, and an actuated condition in which pressure is relieved and the cylinder is coupled to the return line. Thus, pressure is applied to the spindle brake when the valve is not actuated. This means that if there should be a system failure, the brake valve will return immediately to the unactuated brake-closed condition, and hydraulic pressure will continue to be applied from the accumulator to the brake cylinder. This halts spindle rotation prior to the time that pressure to the collet cylinder is lost.
The tailstock function station has an independent pressure regulator to enable control of tailstock force over a wide range. This enables handling of light, fragile workpieces as well as heavy, lengthy and bulky workpieces. The tailstock function also employs a two-speed selector to enable a rapid-approach, slow-down-before-contact, feature. This allows faster cycles, while keeping contact shock on the workpiece minimized. At low tailstock pressures inherent friction in the mechanism will prevent the tailstock accelerating. This friction is overcome by application of high pressure. The high pressure bypass valve is first energized, then returns to low pressure until contact is made on the workpiece. The pressure sensors detect when the tailstock slide has made contact with the workpiece, regardless of workpiece length or pressure requirements. Contact is detected by a sudden drop of pressure in the return flow from the hydraulic cylinder which powers the slide. The pressure drop is caused by the slide stalling against the workpiece, so that flow stops. The absence of flow as a result, the return across a sensing orifice under the speed control valve causes return-side pressure to drop off. In the preferred embodiment, a pressure switch changes state and signals that the tailstock slide is no longer in motion, i.e., that the tailstock is therefore in position.
The collet function station has an independent pressure regulator to make available a wide range of chucking forces. The hydraulic valve that controls the collet open and collet-closed modes has mechanical memory to ensure that the collet does not change state after cower shut-down or power-up.
The spindle brake is engaged by de-energizing the brake valve, which is a solenoid valve. Hydraulic pressure is communicated to the brake pad which then grabs the disk or rotor, thereby stopping and locking the spindle. The brake will engage even in the event of a power loss, as the energy charged in the hydraulic accumulator will communicate to the brake pad and stop the spindle.
A lubrication system automatically lubricates the high speed spindle bearings. This system uses some of the return system fluid to lubricate without using any additional power from the main system. A clear Teflon capillary tube ties into the main system fluid return and communicates up to the spindle bearing housing. The small hydraulic pressure forces just enough fluid up to the bearing. The clear capillary permits quick, visual inspection of lubricating fluid flow.
To ensure a cool, consistent operating hydraulic system temperature, an auxiliary pumping system is employed to circulate hydraulic fluid to a forced-air heat exchanger. The heat exchanger is located and mounted remotely. All hydraulic connectors and hose are furnished as an integral part of the hydraulic assembly. The hose is simply routed to the heat exchanger and connected to the hose ends. The heat exchanger forced air fan and motor are powered from a pre-installed cable.
While the present invention has been described in detail with respect to a single preferred embodiment, it should be understood that the invention is not limited to that precise embodiment, rather, many modifications and variations would present themselves to those of skill in the art without departing from the scope and spirit of this invention, as defined in the appended claims.
Tailstock: support consisting of the movable part of a lathe that slides along the bed in alignment with the headstock and is locked into position to support the free end of the workpiece
Accumulator: An energy saving device of hydraulic and pneumatic system. It in the appropriate timing of the transformation of the energy system for compression energy and potential energy stored, when the system needs and compression energy and potential energy change is a hydraulic or pneumatic energy release, to fill supply system. The moment when the system pressure increases, it can absorb the energy of the whole system, to ensure the normal pressure
一種輔助功能液壓系統(tǒng)可以用來實現(xiàn)計算機(jī)對機(jī)床工具單元的數(shù)字化控制。液壓可以為機(jī)床上的鎖緊夾頭或者卡盤完成打開或者閉合提供動力,也可以向機(jī)床的控制系統(tǒng)實時的反饋夾頭是出于打開還是關(guān)閉的狀態(tài)信息。
因為液壓系統(tǒng)的分離壓力特性克服了初始靜態(tài)摩擦的影響,機(jī)床的尾架可以快速平穩(wěn)的移動到目標(biāo)位置裝夾工件然后快速的返回初始位置。壓力轉(zhuǎn)換器可以顯示出尾架相對于工件的位置狀態(tài)信息。主軸制動器適用于不管是主軸在高速運(yùn)動的狀態(tài)下還是發(fā)生了系統(tǒng)故障實現(xiàn)一樣的制動效果。在后一種情況下,制動發(fā)生在夾頭的壓力損失前更接近缸。同時,轉(zhuǎn)塔卡緊裝置鎖緊然后解鎖刀具轉(zhuǎn)塔。
機(jī)床輔助功能
液壓系統(tǒng)
研究背景
本發(fā)明有關(guān)于應(yīng)用在自動化機(jī)床設(shè)備上的液壓系統(tǒng)。本發(fā)明特別針對具有旋轉(zhuǎn)的機(jī)械加工裝置的液壓系統(tǒng),這種機(jī)加工裝置可以實現(xiàn)主軸夾頭卡盤自動開啟和關(guān)閉,滑動底座上工件的裝夾,自動換刀和主軸制動,所有這一切都是液壓驅(qū)動的。這些機(jī)床單元的狀態(tài)可以通過液壓進(jìn)行實時監(jiān)測。加工設(shè)備最好是計算機(jī)數(shù)控(CNC)的機(jī)床,其中有幾個著名的設(shè)計。
數(shù)控機(jī)械設(shè)備具有快速機(jī)械周期、高精度、操作靈活、易于編程等優(yōu)點(diǎn),可自動將任何特別的毛坯加工成所需要的零件。
一般來說,機(jī)械加工設(shè)備擁有一個附件或者說是機(jī)柜,用來存放加工工具,也可以用來存放加工過程中產(chǎn)生的金屬廢屑和副產(chǎn)品。同時可以實時控制溫度避免由于熱膨脹而造成的精度損失。
機(jī)柜的主軸裝有彈簧夾頭和卡盤用來裝夾工件和保證機(jī)加工操作的安全。彈簧夾頭的打開和關(guān)閉是能夠有機(jī)床系統(tǒng)自行控制。當(dāng)主軸需要緊急制動時主軸可以制動控制。尾座在液壓的驅(qū)動下在裝夾工件的初始位置與目標(biāo)位置之間移動并支撐工件。轉(zhuǎn)塔夾緊裝置可以防止取用刀具時轉(zhuǎn)塔滑離工作位置,但是當(dāng)?shù)端枰D(zhuǎn)動到取刀的位置是夾緊裝置會處于張開狀態(tài)。
機(jī)床制造行業(yè)一直在尋求一個簡單但可靠的液壓系統(tǒng),來執(zhí)行必要的功能,同時還能準(zhǔn)確快速的提供彈簧夾頭打開還是關(guān)閉,主軸制動,尾架的位置和系統(tǒng)壓力的狀態(tài)的信息。尾架的控制和狀態(tài)信息的反饋尤其重要,因此尾架必須能夠平穩(wěn)的移動對工件施加穩(wěn)定的壓力確保不管是較輕的已損壞的還是沉重的過長的工件都能進(jìn)行加工。然而,直到這項發(fā)明的出現(xiàn),沒有完全適合的液壓系統(tǒng)已經(jīng)能夠滿足自動化加工設(shè)備的需求。
本發(fā)明的目的和概述
因此,本發(fā)明的目的在與提供一個模塊化的液壓系統(tǒng)的自動化機(jī)床單元,規(guī)避現(xiàn)有技術(shù)中的一些不足。更直接目的是為功率控制精度要求較高的數(shù)控加工設(shè)備提供一個可靠的液壓系統(tǒng)。本發(fā)明尤其能保證機(jī)加工過程中所需要的全液壓功率并且能自動控制尾架移動到目標(biāo)位置和回到初始位置;向機(jī)床的控制系統(tǒng)反饋尾架與工件的連接狀態(tài),將彈簧夾頭的松開或者夾緊的狀態(tài)信息反饋給機(jī)床的控制器,確保夾頭處于操作需求的狀態(tài);當(dāng)主機(jī)發(fā)出制動信號時,液壓系統(tǒng)自動制動主軸在主軸高速運(yùn)轉(zhuǎn)的狀態(tài)下即使是機(jī)床出現(xiàn)了故障;當(dāng)需要換刀時回轉(zhuǎn)刀塔的夾頭會自動解鎖方便刀具的選擇。
此外,本發(fā)明的目的也在于提供一個能夠便捷的控制尾架移動,并且能使尾架在較短的時間里返回參考點(diǎn)。
根據(jù)本發(fā)明的目的該液壓系統(tǒng)組件包含一個油箱,一個液壓泵,一個加壓泵,一根回油管將液壓油回收到油箱,一個蓄能器與回油管相連用是蓄能器內(nèi)外壓力相等。當(dāng)液壓系統(tǒng)運(yùn)作時,變速泵能夠快速的滿足系統(tǒng)對壓力和流量的需求。變速泵輸送最大流量使系統(tǒng)壓力達(dá)到要求壓力值,然后減少流量使系統(tǒng)自行維持穩(wěn)定的壓力。此外,該泵還控制了一個液壓蓄能器,當(dāng)液壓泵不能滿足系統(tǒng)壓力需求時用來補(bǔ)足系統(tǒng)的瞬時壓力需求。系統(tǒng)的液壓油通過回油管與油箱或者蓄油池相連。尾座油缸具有氣缸連接到車尾滑板,一個雙作用缸與第一和第二液壓端口相連接,同時在第一和第二液壓端口之間裝有一個尾座閥用來控制液壓油供應(yīng)和回流。尾座閥最好是在尾架移動的正方向與機(jī)械坐標(biāo)系參考點(diǎn)之間。尾座壓力調(diào)節(jié)器在供油管與尾座閥之間降低液壓閥到油缸之間的液壓。第一個液壓端口上裝有壓力傳感器,用來監(jiān)測油缸的液壓壓力值。當(dāng)傳感器檢測到壓力下降時,表明尾座已接觸到工件,然后相控制核心反饋一條尾座已到達(dá)目標(biāo)位置的信號。
旁通閥選擇性地繞過尾座壓力調(diào)節(jié)器暫時克服靜摩擦。同時尾座閥和回油管之間的調(diào)節(jié)閥可也控制尾座移動到目標(biāo)位置的速度,并且能繞過它快速回到參考點(diǎn)。
一對壓力監(jiān)測器與液壓缸相連用來打開和關(guān)閉夾頭。在這里夾頭部位的閥門控制著夾頭的打開還是關(guān)閉。壓力監(jiān)測器分別給予計算機(jī)準(zhǔn)確的信號顯示滾筒達(dá)到其最大行程,夾頭是完全開啟或關(guān)閉。主軸的制動動作也是由液壓缸驅(qū)動,最好的設(shè)計是,主軸制動器采用一個具有壓力關(guān)閉和彈簧打開的獨(dú)立運(yùn)作液壓缸。在這里同樣也是,在主軸制動液壓缸的液壓端口的壓力監(jiān)測器會給出一個肯定的指示,該制動器正在應(yīng)用。在這個案例中制動閥具有一個標(biāo)準(zhǔn)狀態(tài),在該條件下,供油管的壓力被施加到閥上,以及在該壓力被解除的驅(qū)動條件下,油缸與回油管路連接。因此,壓力被施加到主軸制動時,該閥處于不作用狀態(tài)。這意味著,如果有系統(tǒng)出現(xiàn)故障,制動閥將立即返回到非驅(qū)動制動封閉條件,液壓將繼續(xù)從蓄能池作用于制動缸。這樣就能在夾頭處液壓缸的壓力不足停止主軸之前的轉(zhuǎn)動。
尾座功能站有一個獨(dú)立的壓力調(diào)節(jié)器確保尾座力控制在一個很大的范圍里。這樣就可以處理輕,易碎的工件以及沉重的,冗長的和笨重的工件。尾座功能站裝備有二速度選擇器能夠快速的接近工件,并且具有能在接觸之前停下來的特征。使得運(yùn)動的時間更短同時確保接觸工件的沖擊力最小化。當(dāng)尾座壓力較低時固有的摩擦機(jī)制將防止車尾加速。這種摩擦可以用來克服高壓。高壓旁通閥首先通電,然后返回低壓,直到接觸工件。在尾座接觸到工件時壓力監(jiān)測器將會檢車到不管弓箭的長度和壓力的需求。一旦監(jiān)測到接觸到工件壓力會立刻變小液壓油回流到油缸從而停止尾座的滑動。壓力的減小是于相對工件的滑動停止,因此,液壓油停止流動。由于不作為結(jié)果,在速度控制閥上的感應(yīng)口的回流導(dǎo)致返回側(cè)壓力下降。在優(yōu)選實施例中,壓力開關(guān)狀態(tài)的改變和信號的輸出,指示車尾滑板不再是運(yùn)動的,即尾座到達(dá)了目標(biāo)位置。
夾頭功能站有一個獨(dú)立的壓力調(diào)節(jié)器使得夾頭的夾緊力可以在一個很大的范圍里調(diào)節(jié)。控制夾頭的開或者關(guān)閉的液壓閥能夠自行記憶之前的狀態(tài)確保在失去動力之后不會改變夾頭的狀態(tài)。
主軸制動采用電磁式的斷電制動閥實現(xiàn)。液壓壓力傳遞到制動盤上,然后鎖緊盤或轉(zhuǎn)子,從而制動和鎖定主軸。即使在能量缺失的狀態(tài)下該制動器將利用蓄能器中的能量確保完成主軸和轉(zhuǎn)盤的制動。
機(jī)床的潤滑系統(tǒng)能夠自行對高速轉(zhuǎn)動的主軸軸承進(jìn)行潤滑。該系統(tǒng)利用了一些系統(tǒng)的回流液壓油,不使用任何額外的系統(tǒng)能量來進(jìn)行潤滑。一個透明的聚四氟乙烯毛細(xì)油管連接到主系統(tǒng)回油管并流向主軸軸承托架完成潤滑。這個袖珍的液壓油管的壓力剛好能夠?qū)⒂洼斔偷捷S承處。透明的毛細(xì)油管允許快捷形象的監(jiān)測到潤滑的效果。
為保證整個系統(tǒng)冷卻、持續(xù)運(yùn)作的液壓系統(tǒng)的溫度,采用輔助泵系統(tǒng)將液壓油與空熱氣循環(huán)進(jìn)行熱交換。熱交換器安裝于較遠(yuǎn)的地方。所有液壓接頭和軟管均是整個液壓組件的一個組成部分。軟管一般與熱交換器相且連接到軟管端部。驅(qū)動熱交換器的風(fēng)扇和電機(jī)由預(yù)先安裝好的電纜供電。
雖然已經(jīng)詳細(xì)通過案例描述了該發(fā)明的細(xì)節(jié),大家應(yīng)該會發(fā)現(xiàn)不局限于單一的按照本案例實施,一些小的地方的改動或者變化將會發(fā)揮更大的作用。
尾座;支持由一個車床,沿床身滑動主軸與可動部分和鎖定位置支撐工件的自由端
蓄能器:液壓氣動系統(tǒng)中的一種能量儲蓄裝置。它在適當(dāng)?shù)臅r機(jī)將系統(tǒng)中的能量轉(zhuǎn)變?yōu)閴嚎s能或位能儲存起來,當(dāng)系統(tǒng)需要時,又將壓縮能或位能轉(zhuǎn)變?yōu)橐簤夯驓鈮旱饶芏尫懦鰜?,重新補(bǔ)供給系統(tǒng)。當(dāng)系統(tǒng)瞬間壓力增大時,它可以吸收這部分的能量,以保證整個系統(tǒng)壓力正常