充電器外殼的注塑注射模具設(shè)計(jì)【側(cè)向抽芯機(jī)構(gòu)一模兩腔優(yōu)秀課程畢業(yè)設(shè)計(jì)含UG三維10張CAD圖紙帶任務(wù)書(shū)+開(kāi)題報(bào)告+外文翻譯】-zsmj28
充電器外殼的注塑注射模具設(shè)計(jì)【側(cè)向抽芯機(jī)構(gòu)一模兩腔】
摘 要
塑料注射模是成型塑料的一種重要工藝。通過(guò)對(duì)充電器外殼注射模具設(shè)計(jì),能夠基本地、全面地了解注射模具設(shè)計(jì)的基本原則、方法。在模具結(jié)構(gòu)設(shè)計(jì)過(guò)程中,我大膽嘗試提出各種不一樣的成型的方案,并與老師探討對(duì)方案進(jìn)行了比較。在比較的過(guò)程中,發(fā)現(xiàn)大量的問(wèn)題,也了解模具設(shè)計(jì)的要求和基本原則,最后在查閱大量書(shū)籍的幫助下完成沒(méi)一個(gè)數(shù)據(jù)的選擇。在設(shè)計(jì)中分析了常用日用品充電器的工藝特性,并介紹了ABS材料成型工藝特點(diǎn)、成型過(guò)程、開(kāi)模過(guò)程以及成型后加工工藝。同時(shí),分析了模具結(jié)構(gòu)與計(jì)算,掌握如何設(shè)計(jì)一個(gè)完整的模具生產(chǎn)結(jié)構(gòu)。通過(guò)本次設(shè)計(jì),能較為熟練的使用Auto-CAD、Pro-E等軟件進(jìn)行模具輔助設(shè)計(jì),提高自己的計(jì)算機(jī)繪圖能力。本次畢業(yè)設(shè)計(jì)充分地為今后從事模具設(shè)計(jì)行業(yè)打下了扎實(shí)的基礎(chǔ)。
本次主要設(shè)計(jì)是對(duì)充電器外殼注射模的設(shè)計(jì), 重點(diǎn)對(duì)塑件的成型原理、材料的選用和注射技術(shù)進(jìn)行分析。通過(guò)前期指導(dǎo)老師安排的任務(wù),我先對(duì)任務(wù)書(shū)進(jìn)行了分析了解,并查閱了大量的書(shū)籍、手冊(cè)和文獻(xiàn),對(duì)模具有了一定的了解并且清楚自己的所要完成的任務(wù)量。進(jìn)過(guò)對(duì)ABS充電器的了解,要滿足制品大批量生產(chǎn)、高精度、外形復(fù)雜等要求,我首先主要把時(shí)間花費(fèi)在確定所需的模塑成型方案、制品的后加工、分型面的選擇、型腔的數(shù)目和排列、成型零件的結(jié)構(gòu)等。既然以實(shí)際生產(chǎn)為目的,設(shè)計(jì)就要涵蓋了注塑模具的主要系統(tǒng)包括有注射機(jī)、澆注系統(tǒng)、排氣系統(tǒng)、冷卻系統(tǒng)、頂出系統(tǒng)、導(dǎo)向系統(tǒng)等。對(duì)于要實(shí)際生產(chǎn)的模具,我們考慮的東西還有很多,為此我積極詢問(wèn)我的指導(dǎo)老師關(guān)于現(xiàn)實(shí)工廠中模具的生產(chǎn)過(guò)程及可能遇到的問(wèn)題。設(shè)計(jì)時(shí),嘗試使用了側(cè)向抽芯機(jī)構(gòu),增加模具的復(fù)雜性以及實(shí)用性。設(shè)計(jì)時(shí)參考了以往注射模具的設(shè)計(jì)經(jīng)驗(yàn),并結(jié)合制品的實(shí)際要求,通過(guò)簡(jiǎn)化設(shè)計(jì)結(jié)構(gòu)、優(yōu)化各個(gè)系統(tǒng)性能,盡最大限度實(shí)現(xiàn)美觀、實(shí)用性高、長(zhǎng)的使用壽命、短的生產(chǎn)周期和良好的經(jīng)濟(jì)性能。
關(guān)鍵詞:塑料注射模;充電器外殼;計(jì)算機(jī)繪圖
Abstract
Injection molding is an important molding plastics. Through the design of the injection mould for the charger shell, can basically, a comprehensive understanding of the basic principles, methods of injection mold design. In the mold structural design process, I attempt to put forward a variety of different forming schemes, and the schemes are compared with the teacher discussion. In the comparison process, found a lot of problems, but also understand the mold design requirements and basic principles, finally finish without a data selection in access to a large number of books to help. In the analysis of the design process characteristics of common commodity charger, and introduces the technology characteristics, forming ABS material molding process, mold and molding process. At the same time, analyzed the mold structure and calculation, master the design of a complete mold to produce structure. Through this design, can be more skilled use of Auto-CAD, Pro-E and other software mold aided design, improve the ability of computer drawing their own. This graduation design is fully engaged in mold design industry for the future lay a solid foundation.
The main design is the design of injection mold for the shell of charger, focuses on the analysis of plastic molding principle, material selection and injection technology. The teacher assigned task, I would first of task were analyzed to understand, and access to a large number of books, manuals and documentation, to mold a certain understanding and clear the task completed their. In the ABS charger understanding, to meet the product mass production, high precision, complex shape and other requirements, I first time spent in the molding, products after processing, the selection of parting surface, cavity number and arrangement, forming part of the structure. Since the actual production, designed to cover the main system of injection mold include injection machine, casting system, exhaust system, cooling system, ejector system, guiding system. For mold to the actual production, there are many we consider something, so I actively ask may meet the production process and my teacher about the real factory mold problems. Design, try to use the side core pulling mechanism, increase the mould complexity and practicability. A reference to the design of the injection mould design experience, combined with the actual requirements of products, through the simplification and optimization of each system performance, structure design, to maximize the realization of beautiful appearance, high practicality, long service life, short production cycle and good economic performance.
Key words:Injection mould for plastic;The charger shell;computer graphics
目 錄
引言 1
1 緒論 2
1.1 模具概述 2
1.1.1 模具種類 2
1.1.2注射模具概述 3
1.1.3 模具設(shè)計(jì)中面臨的難題和要求 3
1.1.3國(guó)內(nèi)研究現(xiàn)狀 4
1.1.4國(guó)外研究現(xiàn)狀 5
1.2 課題的目的及意義 5
1.3課題的主要內(nèi)容和工作方法 6
1.4解決的重點(diǎn)問(wèn)題與創(chuàng)新 8
2 塑料制品分析 9
2.1 明確制品設(shè)計(jì)要求 9
2.2 明確制品批量 9
2.3 材料選擇及性能 9
2.3.1 材料選擇 9
2.3.2 材料品種 10
2.4 成型設(shè)備 10
2.5 拔模斜度 10
2.6 計(jì)算制品的體積和質(zhì)量 11
2.6.1表面質(zhì)量的分析 11
2.6.2塑件的體積重量 11
3 注射機(jī)及成型方案的確定 11
3.1 注射機(jī)的確定 12
3.2 成型方案的確定 12
3.2.1 成型設(shè)備的選擇 12
3.2.2 成型的特點(diǎn) 12
3.2.3 成型的原理 13
3.2.4 成型過(guò)程 13
4 型腔數(shù)的確定及分型面的選擇 13
4.1 型腔數(shù)的確定 14
4.2 分型面的選擇 14
4.2.1 分型面的主要選擇原則 14
4.3確定型腔的排列方式 15
4.4標(biāo)準(zhǔn)模架的選用 16
5 成型零部件的設(shè)計(jì)與計(jì)算 17
5.1 凸模設(shè)計(jì) 17
5.2 凹模的設(shè)計(jì) 17
5.3 成型零件工作尺寸的計(jì)算 18
5.3.1 模腔工作尺寸的計(jì)算 18
6 澆注系統(tǒng)的設(shè)計(jì) 20
6.1澆注系統(tǒng)設(shè)計(jì)的原則 20
6.2主流道設(shè)計(jì) 20
6.3分主流道的設(shè)計(jì) 20
6.4澆口的設(shè)計(jì) 21
6.5平衡進(jìn)料 21
6.6冷料穴設(shè)計(jì) 21
7 排氣與冷卻系統(tǒng)的設(shè)計(jì) 22
7.1 冷卻系統(tǒng)設(shè)計(jì)的原則 22
7.2 冷卻水路的計(jì)算 22
7.3 排氣系統(tǒng)的設(shè)計(jì) 23
8 頂出與抽芯機(jī)構(gòu)的設(shè)計(jì) 24
8.1 推桿復(fù)位裝置 24
8.2 抽芯機(jī)構(gòu)的選擇 25
8.3 抽芯距的計(jì)算 25
8.4 斜導(dǎo)柱抽芯的設(shè)計(jì) 25
8.5滑塊的設(shè)計(jì) 26
9 導(dǎo)向機(jī)構(gòu)的設(shè)計(jì) 26
9.1 導(dǎo)向、定位機(jī)構(gòu)的主要功能 27
9.2 導(dǎo)向機(jī)構(gòu)的設(shè)計(jì) 27
9.2.1 導(dǎo)柱的設(shè)計(jì) 27
9.2.2 導(dǎo)套的設(shè)計(jì) 27
10 注射機(jī)與模具各參數(shù)的校核 28
10.1 工藝參數(shù)的校核 29
10.2 模具安裝尺寸的校核 29
10.2.1 噴嘴的校核 29
10.2.2 定位圈尺寸的校核 29
10.2.3 模具外形尺寸的校核 30
10.2.4 模具厚度的校核 30
10.2.5 安裝參數(shù)的校核 30
10.3 開(kāi)模行程的校核 30
11 結(jié)論 31
謝 辭 32
參考文獻(xiàn) 33
附錄 34
【詳情如下】【需要咨詢購(gòu)買全套設(shè)計(jì)請(qǐng)加QQ1459919609】
1000110532.prt
1000110532.stp
充電器外殼的注塑注射模具設(shè)計(jì).doc
充電器外殼的注塑注射模具設(shè)計(jì)中期檢查表.doc
充電器外殼的注塑注射模具設(shè)計(jì)任務(wù)書(shū).doc
充電器外殼的注塑注射模具設(shè)計(jì)開(kāi)題報(bào)告.doc
動(dòng)模座板 A2.dwg
型腔 A2.dwg
型腔固定板 A1.dwg
型芯3 A2.dwg
型芯固定板 A1.dwg
墊塊 A2.dwg
塑件 A4.dwg
定模座板 A1.dwg
文件清單.txt
滑塊 A3.dwg
英文翻譯(原文).doc
英文翻譯(譯文).doc
裝配圖 A0.dwg


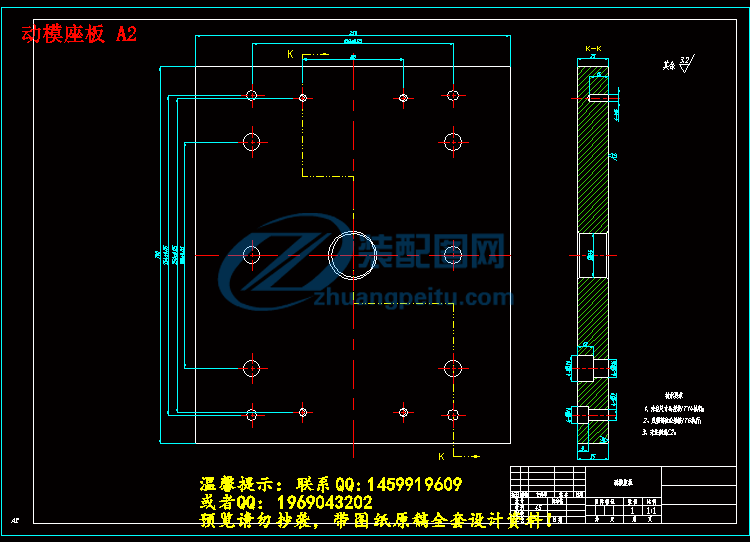

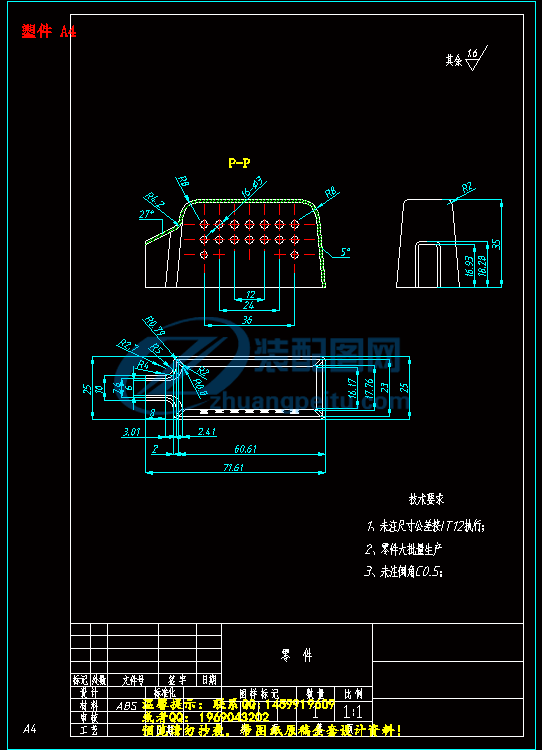

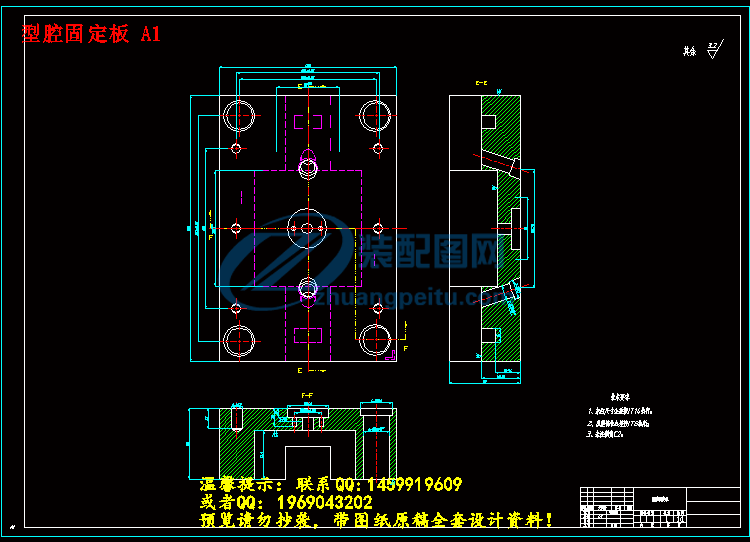
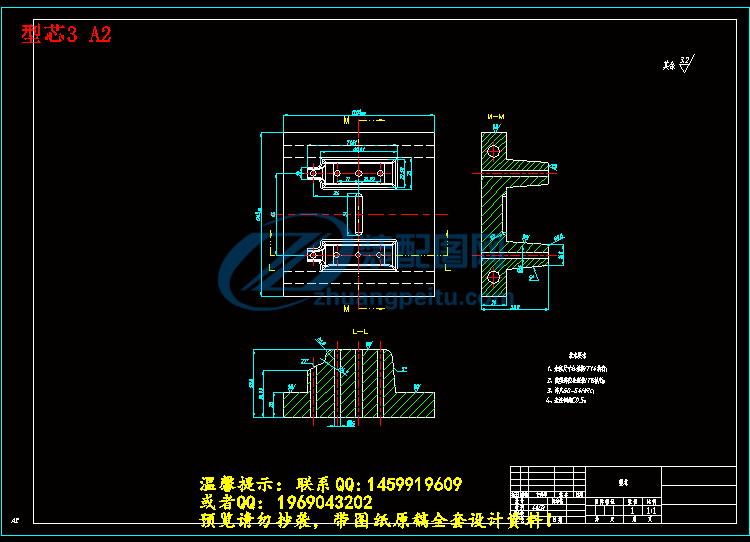
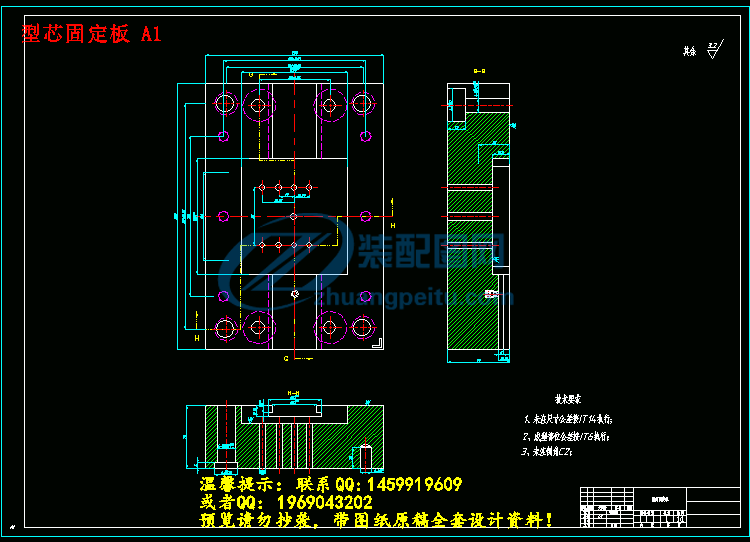
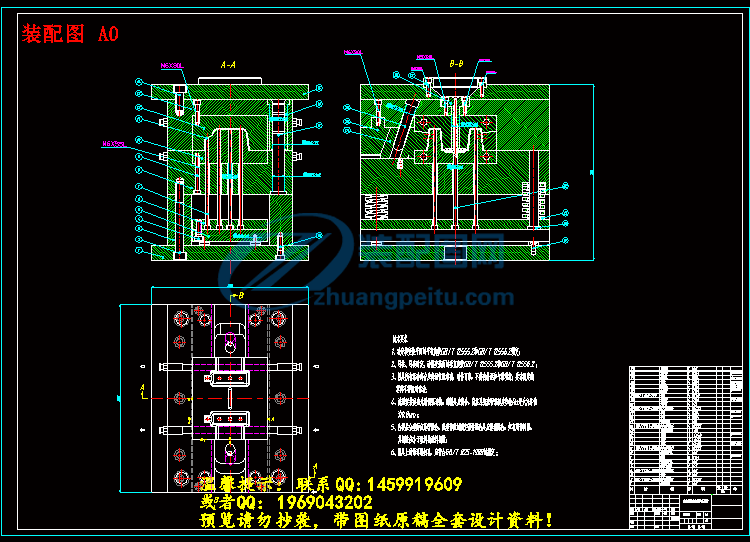

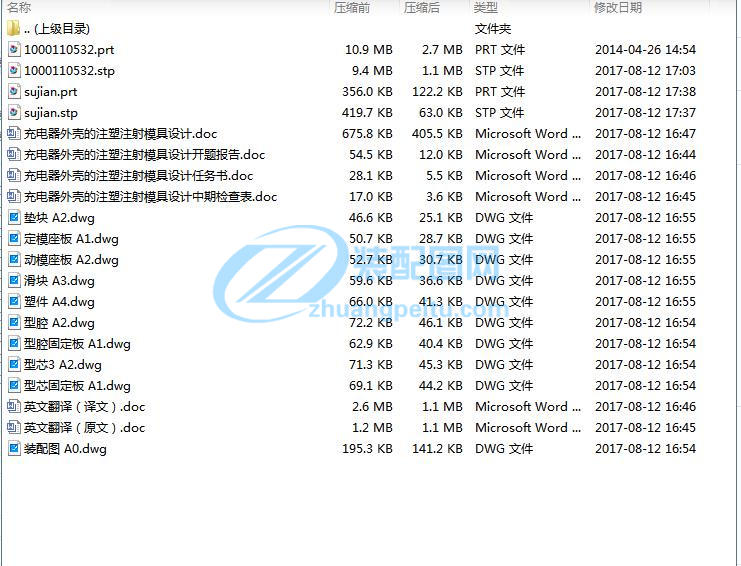


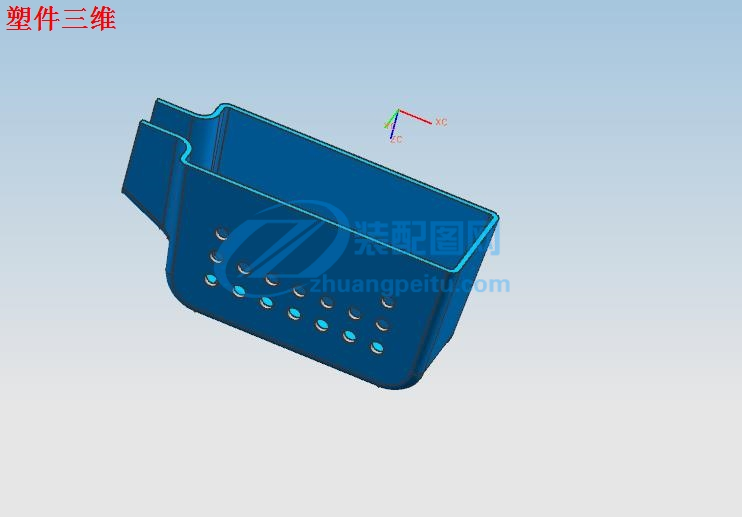
F N N F 13 8854 n of on in 13 of of of of on of of to be in to be in 1. 5be as in 1 in of in to of to 9 BN 1,8,20,21,22,28] of on of 23in of in BN on a 1. In as or to be in as or of of of in of be as BN of 2]. a to of on 23]. a or a or of 2 of BN to it is of on is 23 1. A of in et [24, 25], of an of of on in 2100 of ?26] BN to in et [28] BN on in 2100 BN to BN of on 2. of BN to in of of in 5]. a on of BN 1,2,8] of 23,25]. et [23] et [25] of on In a 27] of 2100 in of BN is on of 7]. of 22]. of in at BN is a at a of in of In et [24] is to In as BN BN 8]. to a of 9] of At is at is is 28]. et [24] by by In of an in of et [3] an in It is in of to or of is is In to it is is is an to It is be to It is is BN to 3, 7, 8, 14, 23]. It is in on It is To of it is to a To a of in to of to In to a of it is to of of It is to of in In it is to of on 2. in 13 is 13 in a at in to 0 5 by of .0 by of of in a) “(b) “as BN E 100 a 0 50 in a an m to 00 mm to an m. A to of on in 13 . in a 6 of in a 56 5.4 mm in on a NC 5E) at a of in a to of 5.4 mm to 6 (A of In to of of 03.2 8 06.4 16 a + a .8 a .8 at 5.4 mm of to a to on of by a 121) on of NC a 121) a at 814 is by on a at a 000 Hz of of as of 3. 3. 3. An of to in a of of to a of to in 13 BN a . In to of F) P2) A an of on of to is is it is is a of a as of 8]. is is is in In by -5 to of of to in of to in is by in of to in of to in of on a . to of on on of to be on a. 4 of on a 00 m/06.4 5 of on a RC 00 m/5.4 4. of on 5. of on at in it is it be to is as as to of 3. 3 of on 6 is to of on 00 m/.2 mm/06.4 on of to a in 6. of on of on of as of 7in in in in 7: of on 8: of on 9: of on of on 10 is to of