三梁四柱式液壓機的總體設計及液壓系統(tǒng)【標稱壓力2500KN】【優(yōu)秀課程畢業(yè)設計含3張CAD圖紙+帶開題報告+外文翻譯】
三梁四柱式液壓機的總體設計及液壓系統(tǒng)【標稱壓力2500KN】
摘要
液壓機是制品成型生產(chǎn)中應用最廣的設備之一,也是理想的成型工藝設備,特別是當液壓機系統(tǒng)實現(xiàn)具有對壓力、行程、速度單獨調整功能后,不僅能實現(xiàn)對復雜工件以及不對稱工件的加工,而且,廢品率非常低,與機械加工系統(tǒng)相比,有極大的優(yōu)越性。近年來,隨著微電子技術、液壓技術等的發(fā)展,液壓機有了更進一步的發(fā)展,其高技術含量增多,眾多機型已采用CNC或PC機來控制,提高了產(chǎn)品加工質量和生產(chǎn)率。
首先,本論文從總體上對液壓機本體結構,及主要結構部件進行設計及必要的校核。其次,對整個液壓控制系統(tǒng)進行初步設計,對液壓機主缸主要參數(shù)進行計算,并對所得結果進行分析、驗算。從而力爭使液壓機主缸能夠滿足生產(chǎn)工藝要求,并從整體上提高液壓機的工藝水準,使液壓機設計水平更上一個新的臺階。本次設計主要針對不同工藝要求下,根據(jù)液壓機總體結構,主缸的推力大小及工作條件的要求來對液壓缸的部件類別進行選擇,同時涉及到液壓缸的支撐型式及活塞與活動橫梁的連接型式和導套及密封件等進行選擇,力求達到提高液壓機整體使用強度及壽命,同時使工藝精度符合生產(chǎn)要求的目的。
關鍵詞:液壓機;液壓控制系統(tǒng);主缸
Abstract
The hydraulic brake is one of the applied broadest equipment in the productions, and also the ideal forming technological equipment. Especially when the system of hydraulic brake realized the adjustment to the press, traveling schedule and speed, the equipment not only completes the processing of the complex and asymmetrical work-pieces, and moreover the rate of its rejection is very low, comparing with the machine-finishing system, which has the enormous superiority. In the resent years, with the development of the microelectronic and hydraulic technology, the hydraulic brake has the further development, whose high-tech content is increasing, and the numerous types had controlled by the CNC or PC machine which increases the processing quality and the productivity.
At first, this paper as a whole carries the design and the essential examination on the hydraulic brake. Second, it carries on the preliminary design to the entire hydraulic control system, and the computation to the main parameters of its master cylinder, then analyses the obtained results. Thus it enables the master cylinder of the hydraulic brake to satisfy the request of the product technique, and enhances its standard overall, which causes its design level on a new stair. This design is mainly in the view of different technological requests, according to the main structures of the equipment, the force sizes of the master cylinder and the request of the working conditions to choose the kinds of every part. At the same time, it involves the choices of hydraulic cylinder's support pattern and piston and active crossbeam connection pattern and guide sleeve and seal, enhancing the hydraulic press whole use intensity and the life and causing the craft precision to conform to the request goal productions.
Keywords: The hydraulic brake; the hydraulic controlling system; master cylinder
目錄
摘要 1
Abstract 2
前言 5
1 液壓機概述 6
1.1液壓機工作原理 6
1.2 液壓機的特點及分類 7
1.2.1液壓機的特點 7
1.2.2 液壓機的分類 8
1.3 液壓機典型結構 9
1.4液壓機技術的發(fā)展現(xiàn)狀 10
1.5液壓機技術發(fā)展趨勢 12
2 液壓機本體設計 13
2.1液壓機的基本參數(shù)及其選用 13
2.2四柱式組合機架的設計計算 14
2.2.1立柱的受力分析 14
2.2.2力柱尺寸的取值 16
2.2.3立柱的強度較核 16
2.2.4橫梁強度和剛度計算 17
2.2.5整體框架式機身強度、剛度計算 22
2.3 液壓機的液壓系統(tǒng) 24
2.3.1 液壓系統(tǒng)機構形式及特點 24
2.3.2一般通用液壓機的液壓系統(tǒng) 25
2.3.2 液壓系統(tǒng)工作過程 26
3 液壓機主缸設計 30
3.1液壓缸的主要性能參數(shù)的計算 31
3.1.1液壓缸的壓力值 31
3.1.2活塞的運動速度 31
3.1.3液壓缸的速比 32
3.1.4活塞的理論推力和拉力 32
3.2液壓缸缸筒設計 33
3.2.1液壓缸缸筒機構及材料的選擇 33
3.2.2 液壓缸缸筒的計算 34
3.2.3液壓缸缸筒部分較核 37
3.2.4 缸筒螺紋連接部分計算 37
3.3液壓缸活塞的設計 39
3.4活塞桿的設計計算 40
3.4.1活塞桿直徑的計算 40
3.4.2 活塞桿的強度計算 40
3.5活塞桿的導向套和密封 42
3.5.1 導向套結構及相關計算 42
3.6 緩沖裝置 43
3.7 排氣閥的設計 44
3.8 與液壓缸相關的連接結構設計 45
3.8.1 液壓缸與上橫梁連接結構設計 45
3.8.2 活塞桿與活動橫梁連接結構設計 46
4 結論 47
致謝 48
參考文獻 49
【詳情如下】【需要咨詢購買全套設計請加QQ1459919609】
A0-整體結構圖.dwg
A0-整體結構圖.exb
A2-液壓系統(tǒng)圖.dwg
A2-液壓系統(tǒng)圖.exb
三梁四柱式液壓機的總體設計及液壓系統(tǒng)【標稱壓力2500KN】開題報告.doc
三梁四柱式液壓機的總體設計及液壓系統(tǒng)【標稱壓力2500KN】說明書正文.doc
內(nèi)封.doc
實習報告.doc
摘要.doc
文件清單.txt
正文.doc
液壓缸A1.dwg
液壓缸A1.exb
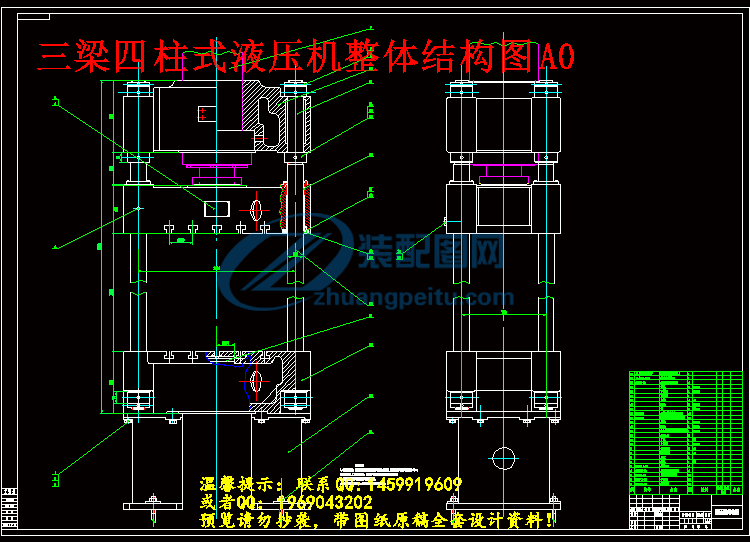
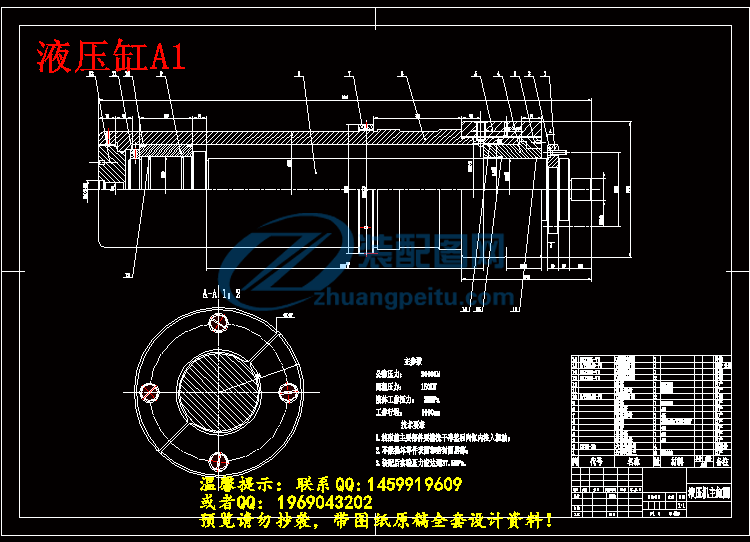
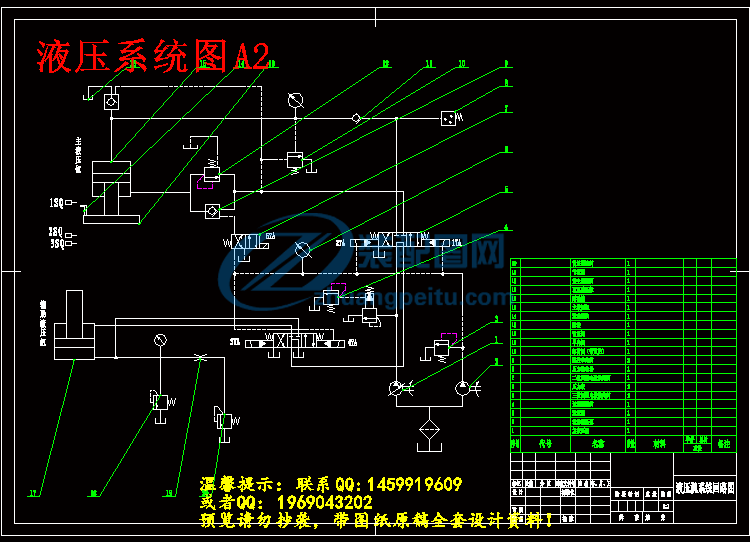
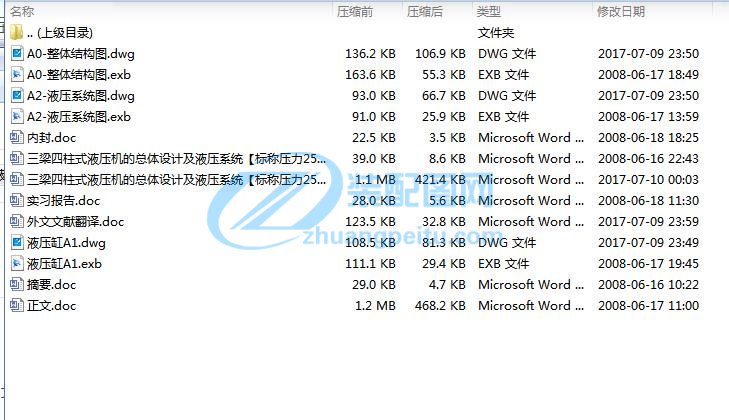
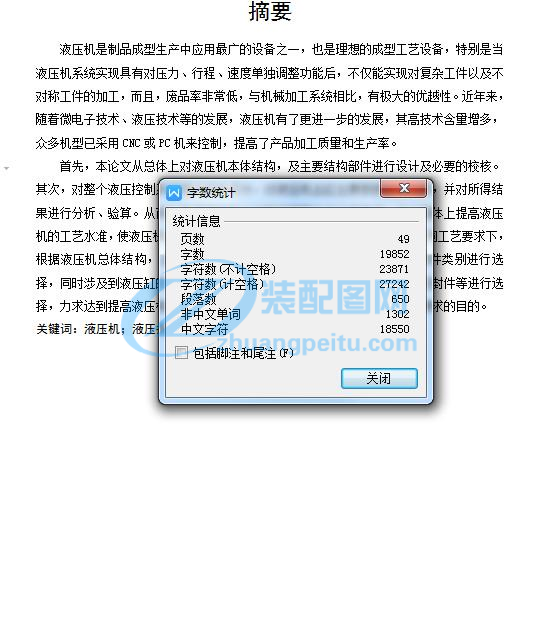
遼寧工程技術大學畢業(yè)設計 (論文 ) 1 前言 液壓機是制品成型生產(chǎn)中應用最廣的設備之一,也是理想的成型工藝設備,特別是當液壓機系統(tǒng)實現(xiàn)具有對壓力、行程、速度單獨調整功能后,不僅能實現(xiàn)對復雜工件以及不對稱工件的加工,而且,廢品率非常低,與機械加工系統(tǒng)相比,有極大的優(yōu)越性。近年來,隨著微電子技術、液壓技術等的發(fā)展,液壓機有了更進一步的發(fā)展,其高技術含量增多,眾多機型已采用 高了產(chǎn)品加工質量和生產(chǎn)率。 液壓機主缸是液壓機的主要工作部件,液壓機主缸的性能直接影響著液壓機整體工藝水平。通過細致的分析及理論研究解決易損部分設計結構中存在 的問題,可以使液壓缸整體上達到工藝強度要求,提高液壓缸應用的工藝水準及使用壽命。所以對液壓機主缸進行細致嚴謹?shù)脑O計計算對對液壓機的設計生產(chǎn)有著至關重要的作用。 本論文從總體上對液壓機本體結構,及主要結構部件進行設計及必要的校核,對液壓機主缸主要參數(shù)進行計算,并對所得結果進行分析、驗算。從而力爭使液壓機主缸能夠滿足生產(chǎn)工藝要求,并從整體上提高液壓機的工藝水準,使液壓機設計水平更上一個新的臺階。 李聳 : 液壓機及主缸設計 2 1 液壓機概述 本章著重對液壓機整體情況做出介紹,內(nèi)容涉及液壓機的原理,液壓機的特點、分 類,以及液壓機的典型結構介紹,目前國內(nèi)、外液壓機的發(fā)展現(xiàn)狀以及未來液壓機的大體發(fā)展趨勢等。 壓機工作原理 液壓機是根據(jù)靜態(tài)下液體壓力等值傳遞的帕斯卡原理制成的,它是一種利用液體壓力工作的機器。液體壓力傳遞原理為:在充滿液體的密閉容器中,施于任一點的單位外力,能傳播至液體全部,其數(shù)值不變,其方向垂直于容器的表面。 根據(jù)這一原理,制成了液壓機和其他液壓機械,如圖 1示 : p F 2A 2 A 1小 柱 塞大 柱 塞工 件圖 1壓機原理圖 1一個充滿液體的連通器內(nèi),一端裝有面積為1一端裝有面積為2塞和連通器之間設有密封裝置,使得連通器內(nèi)部形成一個完全密封的空間,液體不會外泄。當在小柱塞上施加一個外力1作用在液體上的單位壓力為11? 。按照液體靜壓力傳遞原理,這個單位壓力 值傳遞到液體的每一個質點,并且其遼寧工程技術大學畢業(yè)設計 (論文 ) 3 作用方向垂直于其作用面。這樣在連通器的另一端的大柱塞上作用著垂直于其底面的單位壓力 p,使其產(chǎn)生向上的推力22F 由此可見,只要增大柱塞的面積,就可以由小柱塞上一個較小的力1F,在大柱塞上獲得一個很大里力2F。這里的小柱塞相當于液壓泵中的柱塞,而大柱塞就相當于液壓機中的工作缸的柱塞。 壓機的特點及分類 壓機 的特點 液壓機是制品成型生產(chǎn)中應用最廣的設備之一。目前,液壓機的最大標稱壓力已達750于金屬的模鍛成型。隨著金屬壓制和拉伸制品的需求逐年增高,對產(chǎn)品品種的要求也日益增多;另一方面,產(chǎn)品的生產(chǎn)批量也逐漸縮小。為與中小批量生產(chǎn)相適應,需要能快速調整的加工設備,這使液壓機成為理想的成型工藝設備,特別是當液壓機系統(tǒng)實現(xiàn)具有對壓力、行程、速度單獨調整功能后,不僅能實現(xiàn)對復雜工件以及不對稱工件的加工,而且,廢品率非常低,與機械加工系統(tǒng)相比,有極大的優(yōu)越性。近年來,隨著微電子技術、液壓技術等的發(fā)展,液壓機有了更進 一步的發(fā)展,其高技術含量增多,眾多機型已采用 高了產(chǎn)品加工質量和生產(chǎn)率 [1]。 液壓機有以下幾個優(yōu)點: 1)液壓機最大的特點是容易獲得最大的壓力。在鍛造過程中鍛錘是靠沖擊力打擊鍛件,因而會產(chǎn)生較強的振動。為了提高打擊效率和減輕振動,需要有很大的砧座和良好的地基,因而鍛錘不可能造得很大。曲柄壓力機是靠曲柄連桿機構傳遞能量,由于受到曲柄連桿機構強度的限制,一般只制造到 100壓機利用靜壓力工作,不需要大的砧座和監(jiān)視的地基。由于采用了液壓傳動,其動力設備可以與主機分開,可以適當加大 柱塞的直徑或采用多缸聯(lián)合工作的方式來獲得更大的工作壓力。目前大型液壓機均已造到100 2)得更大的工作行程,并可在全行程的任意位置施加最大的工作壓力;在工作行程的任意位置都可以回程。機械傳動的曲柄壓力機的滑塊行程是不變的,并且只能在滑塊下止點前較小的行程內(nèi)產(chǎn)生標稱壓力。而且必須在下止點后才能回程,如果過載將會發(fā)生悶車現(xiàn)象,導致?lián)p壞。液壓機則與其相反,所以液壓機對要求工作行程較長而且變形均勻的工藝(如拉伸、積壓等)十分適應。 3)更大的工作空間。液壓機本體沒有龐大的機械傳動機構,其液壓缸可根據(jù)操作的李聳 : 液壓機及主缸設計 4 要求來布置,因而可以容易地獲得較大的工作空間。 4)作壓力可以調整,可以實現(xiàn)保壓,并可防止過載。例如,有三個缸的液壓機可以很容易地獲得三級不同的工作壓力。將高壓液體通入中間工作缸得到第一級壓力;通入兩側工作缸得到第二級壓力; 3 個工作缸同時通入高壓液體就得到第三級壓力。液壓機可以作長時間的保壓。液壓系統(tǒng)有調壓裝置,可以根據(jù)要求來調整液體的壓力。他的安全裝置,能可靠地防止過載。 5)調速方便。通過調整通入工作缸液體的流量,可以實現(xiàn)各種行程速度。例如,實現(xiàn)空程下降和回程時高速,工作行程時慢速,而且這種調速是無級的 。 6)液壓機結構簡單,操作方便。液壓機的本體結構很簡單,而且容易制造。特別是中、小型的液壓機,由于液壓元件的標準化、系列化和通用化程度的提高,使其設計與制造更為簡便,成本降低。液壓機還易于實現(xiàn)自動控制和遙控。 7)液壓機工作平穩(wěn)。碰撞、振動和噪聲都較小,有利于改善工人的勞動強度和工作條件。 8)液壓機的動力傳動為柔性傳動,較機械加工復雜的傳動系統(tǒng)簡單,可避免機械過載的情況。 9)液壓機基本的動作方式有三種:單動、雙動、三動。但其拉伸過程中只有單一的直線驅動力,是加工系統(tǒng)有較長的使用壽命和較高的工件成品率。 除了以上優(yōu)點外液壓機還有一些缺點,比如: 1) 液壓機采用液壓油為工作介質,因而對液壓元件的精度要求和密封條件要求較高。另外,不可避免的泄露會帶來環(huán)境的污染。 2) 液壓機的工作速度較其他設備低。由于液體流動時會產(chǎn)生較大的阻力損失,當液壓機高速運動時,這種損失就更為明顯。所以液壓機的最高工作速度受到限制。 由于液壓機具有以上特點,因此得到了廣泛的應用。除了大型的鍛件的鍛造、拉伸、剪切、擠壓等工序外,還應用于塑料壓型 、 層壓板、粉末冶金、廢金屬處理、棉花打包等工序。 壓機的分類 液壓機按照 機架結構形式分為梁柱式、組合框架式、整體框架式、單臂式等。按照功能用途分可分為手動液壓機、鍛造液壓機、沖壓液壓機、一般用途液壓機、校正包裝液壓機、層壓液壓機、擠壓液壓機、壓制液壓機、打包液壓機、專用液壓機等 10 余種類型。其各自類型對應的常見工藝如下: 遼寧工程技術大學畢業(yè)設計 (論文 ) 5 1)手動液壓機:用于一般壓制、壓裝等工藝。 2)鍛造液壓機:用于自由鍛、鋼錠開坯及金屬模鍛。 3)沖壓液壓機:用于各種薄板、厚板的沖壓。 4)一般用途液壓機:用于各種工藝,通常稱為萬能(通用)液壓機。 5)校正壓裝液壓機:用于零件的校正及裝配。 6)層壓液壓機 :用于膠合板、刨花板、纖維板及絕緣材料板的壓制。 7)擠壓液壓機:用于擠壓各種有色及黑色金屬材料。 8)壓制液壓機:用于各種粉末制品的壓制成型,如粉末冶金、人造金剛石、耐火材料的壓制。 9) 包、壓塊液壓機:用于將金屬碎屑及廢料壓成塊。 10)其它液壓機:包括輪軸壓裝、沖孔等專門用途的液壓機。 壓機典型結構 液壓機結構中較典型的主要有三梁四柱式、雙柱下拉式、框架式和單臂式等,其中三梁四柱式液壓機為通用型液壓機的常用型式,本次畢業(yè)設計采用此類型液壓機為設計對象,這里只對此型液壓機作以介紹。 三梁四柱式液壓 機結構如圖所示,它由上橫梁、下橫梁、 4個立柱和 16個內(nèi)外螺母組成一個封閉的框架,框架承受全部的工作載荷。工作缸固定在上橫梁上,工作缸內(nèi)有工作柱塞與活動橫梁相連接。活動橫梁以 4根立柱為導向,在上、下橫梁之間往復運動。活動橫梁下面固定有上砧,而下砧則固定與下橫梁上的工作臺上。當高壓液體進入工作缸后,對柱塞產(chǎn)生很大的壓力,推動柱塞、活動橫梁及上砧向下運動,使工件在上、下砧之間產(chǎn)生塑性變形。同時在完成工作之后實現(xiàn)回程運動。 李聳 : 液壓機及主缸設計 6 圖 1壓機典型結構圖 1梁四柱式液壓機的主要部件有: ⑴立柱:立柱是機架的主要支撐部件和主要受力件,又是活動橫梁的導向件,因此對立柱有較高的強度、剛度和精度要求。立柱所用的材料、結構尺寸、制造質量及其與橫梁之間的連接方式、預緊程度等因素,都對液壓機的工作性能甚至使用壽命有著很大的影響。 立柱通常用如下材料制成: 35鋼、 45鋼、 402020。 ⑵橫梁:橫梁包括上橫梁、下橫梁(或稱底座)和活動橫梁(或稱滑塊),是液壓機的重要部件。由于橫梁的輪廓尺寸很大,為了節(jié)約金 屬和減輕重量,一般都做成空心箱形結構,中間加設肋板,承載大的地方肋板較密,以提高剛度,減低局部應力,肋板一般按方格形或輻射形分布,在安裝各種缸、柱塞(或活塞)及立柱的地方做成圓筒形,以使其環(huán)行支撐面的剛度盡可能一致,并用肋板與外壁相互之間連接起來。 橫梁有鑄造結構和焊接結構兩種,生產(chǎn)批量較大的中、小型液壓機其橫梁多為鑄鐵件(材料多為 鑄鋼件(材料多為 近年來采用焊接結構的日漸增多,材料一般為 6板。 中、小型液壓機橫梁多數(shù)為整體結構,而大型液壓機橫梁由于受制造 和運輸能力的限制往往設計成組合形式,并利用鍵和拉緊螺栓連接。 壓機技術的發(fā)展現(xiàn)狀 液壓機的液壓系統(tǒng)和整機機構等方面發(fā)展已經(jīng)相當成熟,國內(nèi)外機型無較大差距,主遼寧工程技術大學畢業(yè)設計 (論文 ) 7 要差別在于加工工藝和安裝方面。良好的工藝使機器在過濾、冷卻及防止沖擊振動等方面有明顯的改善 [2]。 1)路設計方面,國內(nèi)外都趨向于集成化、封閉式設計,插裝閥、疊加閥和復合化元件及系統(tǒng)在液壓系統(tǒng)中得到了廣泛的應用。國外已廣泛采用封閉式循環(huán)油路設計,可有效地防止泄露和污染,更重要的是防止灰塵、空氣和化學物質侵入系統(tǒng),延長了機器的使用壽命。由于加 工工藝等方面的原因,國內(nèi)采用封閉式循環(huán)油路設計的系統(tǒng)還不多見。 2)在安全性方面,國外某些采用微處理器控制的高性能液壓機利用軟件實現(xiàn)故障的檢測和維修,產(chǎn)品可實現(xiàn)負載檢測、自動模具保護和錯誤診斷等功能。 3)液壓機的發(fā)展最主要體現(xiàn)在控制系統(tǒng)方面。微電子技術飛速發(fā)展,為改進液壓機的性能,提高穩(wěn)定性、加工效率等方面提供了前提條件。相比之下,國內(nèi)機型雖然品種齊全,但技術含量相比較低,缺乏高檔機型,這與機電液一體化和中小批量肉刑發(fā)展趨勢不相適應。 當前,國內(nèi)外液壓機產(chǎn)品中控制系統(tǒng)分為以下三種類型: 1)以繼電器為主控 制元件的傳統(tǒng)型控制系統(tǒng)。其電路結構簡單,技術要求不高,成本較低,相應控制功能簡單,適應性不強。主要用于單機工作,加工產(chǎn)品精度不高的大批量生產(chǎn),也可組成簡單的生產(chǎn)線?,F(xiàn)在國內(nèi)許多液壓機廠還以該機型為主,國外眾多廠家只是保留了對該機型的生產(chǎn)能力,而主要面向技術含量更高的機型組織生產(chǎn)。 2)采用可編程控制器( 控制系統(tǒng)。該系統(tǒng)是在繼電器控制和計算機控制發(fā)展的基礎上開發(fā)出來的并逐漸發(fā)展成為以微處理器為核心,將自動化技術、計算機技術、通訊技術溶為一體的新型工業(yè)自動控制裝置。目前,該機型廣泛應用于各種生產(chǎn)機械和 自動化生產(chǎn)過程中,早期的可編程控制器只能進行簡單的邏輯控制,隨著技術的不斷發(fā)展,一些廠家采用微電子處理器作為可編程控制器的中央處理單元( 不僅可以進行邏輯控制,還可以對模擬量進行控制,擴大了控制器的功能??删幊炭刂破饔休^高的穩(wěn)定性和靈活性,但還是介于繼電器控制和工業(yè)控制之間的一種控制方式,與工業(yè)控制機相比還有很大差距。當前,國內(nèi)有部分廠家采用該控制系統(tǒng),如天津鍛壓機械廠有 60%的產(chǎn)品采用 外的廠家如丹麥的 可編程控制器,實現(xiàn)對壓力和 位移的控制。 3)應用高級微處理機(或工業(yè)控制計算機)的高性能控制系統(tǒng)。該控制方式是在計算機控制技術成熟發(fā)展的基礎上采用的一種高科技含量的控制方式,以工業(yè)控制機或單片/單板機作為住控制單元,通過外圍數(shù)字接口器件(如 A/D 或 D/A 板等)或直接應用數(shù)字李聳 : 液壓機及主缸設計 8 閥實現(xiàn)對液壓系統(tǒng)的控制,同時利用各種傳感器組成閉環(huán)回路式的控制系統(tǒng),達到精確控制的目的。這種控制方式的主要特點為:具有友好的人機交互性;可順利實現(xiàn)對工件參數(shù)(如壓力、速度、行程)的單獨調整,能進行復雜工件、不對稱工件的加工;預存工作模式,縮短調整時間,,與柔性加工 要求相適應;可通過軟件來消除高速下的換向沖擊,以降低噪聲,提高系統(tǒng)的穩(wěn)定性;在安全方面可利用軟件進行故障診斷,并自動修復故障和顯示錯誤。 現(xiàn)在,國外眾多液壓機生產(chǎn)廠家都生產(chǎn)這種高性能的工業(yè)控制機控制方式的液壓機產(chǎn)品,如美國的 麥的 國內(nèi)少有該類產(chǎn)品。 壓機技術發(fā)展趨勢 目前,隨著科技發(fā)展的日新月異,液壓機的技術含量也在日益增高,其主要發(fā)展趨勢可分為如下幾點: 1)高速化 、 高效化 、 低能耗,提高液壓機的工作效率,降低生產(chǎn) 成本。 2)機電掖一體化,充分利用機械和電子方面的先進技術促進整個液壓系統(tǒng)的完善。 3)自動化、智能化。微電子技術的高速發(fā)展為液壓機的自動化和智能化提供了充分的條件,自動化不僅僅體現(xiàn)在加工方面,應能夠實現(xiàn)對系統(tǒng)的自動診斷和調整,具有故障預處理功能。 4)壓元件集成化,標準化。集成的液壓系統(tǒng)減少了管路連接,有效地防止泄露和污染,標準化的元件為機器的維修帶來方便。 遼寧工程技術大學畢業(yè)設計 (論文 ) 9 2 液壓機本體設計 本章主要針對通用型三梁四柱式液壓機進行本體設計,其主要內(nèi)容為對該型液壓機的主要參數(shù)進行選擇,對液壓機 主要部件尺寸進行計算,并對部件剛度、強度進行校核,以使所設計液壓機能夠達到生產(chǎn)工藝要求。 壓機的基本參數(shù)及其選用 液壓機的基本參數(shù)是基本技術數(shù)據(jù),是根據(jù)液壓機的工藝用途及結構類型來確定的,對于本次設計的三梁四柱式液壓機,主要設計參數(shù)如圖 2 圖 2壓機主要結構參數(shù)示意圖 2)標稱壓力( 標稱壓力是液壓 機的主要設計參數(shù)。它反映了液壓機的主要工作能力,是液壓機名義上能產(chǎn)生的最大壓力,數(shù)值上等于工作柱塞總的面積與液體壓力的乘積。 本次設計液壓機標稱壓力為給定原始數(shù)據(jù) 2500 2)最大工作行程:最大工作距離 h 是指活動橫梁在上限位置時從工作臺上面到活動橫梁下表面的距離。反映里液壓機高度方向上工作空間的大小,應根據(jù)模具及墊板高度工作行程大小以及放入取出工件所需空間的大小等工藝因素來確定。 本次設計液壓機工作行程 h=1250 3)最大凈空距(開口高度) H。最大凈空距是指活動橫梁在上限位置時從工作臺上表李聳 : 液壓機及主缸設計 10 面到 活動橫梁下表面的距離。反映了液壓高度方向上的工作空間的大小,應根據(jù)模具及墊板高度、工作行程大小以及所需空間的大小來確定。 本次設計液壓機最大凈空距 H=1370 4)工作臺尺寸:在如鍛造、模煅及沖壓等加工工藝中,往往設置移動工作臺。他的尺寸(長 l? 寬 b)取決于模具的的平面尺寸。 本次設計工作臺尺寸為給定原始數(shù)據(jù) 900? 900 5)立柱中心距 (在四柱式液壓機中,立柱寬邊中心距為 L,窄邊中心距為 B。立柱中心距反映了液壓機平面尺寸上工作空間的大小。 本次設計液壓機 立柱中心距 =1120? 700( 6)活動橫梁的運動速度( /mm s )活動橫梁運動速度分為工作行程速度及空載回程速度兩種。 本次設計液壓機工作形成速度1v=程速度2v= 7)頂出力。有些液壓機在下橫梁底部裝有頂出缸,以頂出工件在拉伸時產(chǎn)生的壓邊力。頂出力及行程由具體工藝要求來確定,在此不做要求。 柱式組合機架的設計計算 柱的受力分析 由于四柱式組合機架是一個高次超靜定空間框架 ,在進行受力分析時,需采取一些簡化假設:由于一般液壓機的機架結構對稱于中間平面,載荷也對稱于中間平面,因此可將空間框架簡化為平面框架;立柱與上、下橫梁為剛性連接;不考慮安裝應力及溫度應力。 1)中心載荷。假設上、下橫梁剛度很大,則可忽略上、下橫梁變形而施加與立柱的附加彎曲應力,則立柱只承受簡單的軸向拉應力,其 拉應力為: ? ?p ??(2式中 F—— 液壓機的公稱壓力; A—— 每根立柱的接面積; n—— 立柱的根數(shù); ??? —— 許用應力,本次設計立柱材料選擇為 45 鋼,其取值范圍為 6 0 ~ 7 0M P a M P a。 2)偏心載荷。液壓機工作時,由于模具不對稱、工作變形阻力不對稱(加工零件形遼寧工程技術大學畢業(yè)設計 (論文 ) 11 狀不對稱或加熱不均勻)、工件放置位置不正等多種因素都可能造成偏載受力狀態(tài)。 根據(jù)前面的簡化假設,將空間機架簡化為平面框架,如圖所示。在手偏心載荷時,活動橫梁發(fā)生傾斜,活塞隨之傾斜壓到 液壓缸導向套或內(nèi)壁上,而活動橫梁也與立柱相接觸??紤]到不同工藝條件及密封等,補充做如下假設:工件較窄,不妨礙活動橫梁轉動,因此在工件處沒有側向水平支反力;兩側立柱導套間隙一樣,因此在活動橫梁傾斜十,兩邊立柱均勻受力;各處的作用力及支反力均假定為集中力。 考慮到由于用一個兩柱的平面框架來代替原來對稱的四柱空間框架,因此載荷取為F/2。載荷的偏心距為 e,活動橫梁受到的偏心力矩 作用,給液壓缸內(nèi)壁以側推力為1F: ? ?1 2 Y h? ?(2式中 — 液壓缸的缸筒受力點或活塞中點至上橫梁下表面的距離; — 活動橫梁導向套支撐反力作用點到上橫梁下表面的距離。 這樣,四柱式組合液壓機機架即可簡化為如圖 2示的平面框架。 框架的寬度 b 為立柱中心線間的距 離??蚣芨叨?h 則與立柱和橫梁的剛度比有關。 1K、2橫梁的剛度比,則: 1 c I? (22 c I? (2式中cK、uK、 分別為立柱、上橫梁和下橫梁的彈性模量; 分別為立柱、上橫梁 和下橫梁的截面慣性矩。 如果1K、2必須考慮到剛度比的影響,框架高度應取為上橫梁中性層到下橫梁中性層間的距離。在計算中假設1K、2假設上、下橫梁剛度為無窮大, 因此框架高度 h 取為上橫梁下表面到下衡量上表面之間的距離。 李聳 : 液壓機及主缸設計 12 / 2F / 2F / 2F 1 / 2F 1 2 / 2F 1 / 2F 1Z 2壓機機架受力圖 2于假設上橫梁的剛度為無窮大,因此作用于缸壁處的推力1在上衡量上附加一力矩1M=1F 圖所示,該力矩1 12 b? ? ?2 b? ?(2由于軸向力在立柱內(nèi)不引起彎矩,因而在求解立柱彎矩時不予考慮。根據(jù)材料力學可知,這是個三次靜布定框架問題,可用變形法或力法求解。則可得出框架中的最大軸向力與彎曲力矩分別為: ? ?? ?m a ?柱尺寸的取值 本次設計由比較法,參照沈陽液壓機廠 3150壓機相關尺寸,立柱材料選擇為 45鋼,初步確定液壓機立柱尺寸值為: l=31601930h , 150d 柱的強度較核 1) 靜載合成應力 [3]。液壓機在偏心載荷作用下,立柱承受單純拉應力和彎曲應力聯(lián)合作用,其合成應力h?為: 遼寧工程技術大學畢業(yè)設計 (論文 ) 13 ? ?m a x m a ? ? ?(2式中 立柱所受最大軸向拉力; 立柱所受最大彎矩; A —— 立柱的截面面積; W —— 立柱截面系數(shù)。 帶入數(shù)值計算得 ? ?9 7 . 5 1 5 0h M P a M P a??? ? ? 所以立柱強度符合 靜載合成應力要求。 2)疲勞強度校核。對于中、小型液壓機,尤其是鍛造液壓機在工作過程中,立柱長期承受不規(guī)則的脈動載荷的作用,在每次加載時,立柱都出現(xiàn)較大的應力幅值,而在卸載后,由于立柱搖擺也還有若干個較小的應力幅值。 由于立柱的疲勞斷裂大部分發(fā)生在立柱根部截面變化的進度區(qū),為此在進行強度計算時,需考慮過渡區(qū)的應力集中,即: ? ?0? ???(2式中 k 為有效力集中系數(shù): ? ?11tk q k? ? ?式中 q —— 應力集中的敏感系數(shù),對于 45 鋼 q 值在 間; 彈 性狀態(tài)下理論應力集中系數(shù),取值在 間。 ? ?0?為許用脈動循環(huán)的疲勞極限: ? ?000n????? 式中0?—— 脈動循環(huán)時的疲勞極限,對大截面 45 鋼,取為 270 ? —— 尺寸系數(shù)冊中查得; ? —— 表面質量系數(shù),精車表面 ? 取值為 0n—— 安全系數(shù)。 代入數(shù)據(jù)計算得 ? ?01 9 9 2 7 0T M P a M P a??? ? ? 所以立柱強度符合疲勞強度要求。 梁強度和剛度計算 橫梁 雖通常設計成箱形構件,且其外形高跨比較大,在進行初步設計時,仍可將橫梁李聳 : 液壓機及主缸設計 14 簡化為簡支梁進行近似計算。 1) 上橫梁相關計算 上橫梁結構如圖 2一般經(jīng)驗公式,上橫梁鑄造箱體 告訴一般取值為橫梁跨度的( ,這里取橫梁高度 h =690取上橫梁鑄造箱體壁厚為a?= 肋板厚度為 0??: 圖 22橫梁受力分析如圖 2 b / 2b / 2D / 2 D / 2F / 2 F / 2 F / 2 F / 2圖 2橫梁受力示意圖 2大彎矩計算公式為: m a x 22F b ????????(2代入數(shù)值得 m a 0 0 1 1 2 0 5 8 022M ?????????遼寧工程技術大學畢業(yè)設計 (論文 ) 15 34 7 0 1 0 根據(jù)強度條件計算時,對截面變化不大 的箱形結構梁,主要計算最大彎矩處,即中心截面處強度: ? ?m a x 1m a x ??(2式中 最大彎矩; I —— 計算截面慣性矩, 2112 ; 1h—— 計算截面的形心 至最外點距離; ??? —— 許用應力,本次設計橫梁材料選擇為 270 500 鑄鋼 ??? ? ? ? 66 0 7 0 1 0 。 代入數(shù)值計算得 ? ?66m a x 4 3 . 6 1 0 6 5 1 0M P a M P a??? ? ? ? ? 上橫梁的剪切應力主要由立柱承受,因此截面可近似簡化成厚度是 ? 高度是 h 的矩形截面,其剪切應力在形心軸處最大: ? ?1 ????(2式中 F?—— 計算截面所受的剪力; ? —— 橫梁立板的厚度之和; h —— 橫梁立板的高度; ??? —— 剪切許用應力, 270 500 鑄鋼 ??? 650 10 。 代入數(shù)值計算得 ? ?662 8 . 3 1 0 5 0 1 0M P a M P a??? ? ? ? ? 所以上橫梁強度符合彎應力及剪應力強度要求。 2)下橫梁的相關計算 下橫梁結構如圖 2示,下橫梁高度取值一般為橫梁跨度的 ~ 倍,在此取下橫梁高度為 90? ,下橫梁壁厚取為 ?a?40肋板厚度取為 ?b?50 李聳 : 液壓機及主缸設計 16 圖 2橫梁結構圖 2橫梁受力分析如圖 2 F / 2F / 2橫梁受力圖 2于下橫梁彎矩計算,按均布載荷公式進行計算。 21m a x 48? (2式中 1Fq b? 則中心截面處強度: ? ?m a x 1m a x ??(2代入數(shù)值計算得: ? ?66m a x 5 0 . 7 1 0 6 5 1 0M P a M P a??? ? ? ? ? 形心處的剪切應力為: 遼寧工程技術大學畢業(yè)設計 (論文 ) 17 ? ?1 h ??????(2代入數(shù)值計算得: ? ?663 7 . 4 1 0 5 0 1 0M P a M P a??? ? ? ? ? 所以下橫梁強度符合彎應力及剪應力強度要求。 3)活動衡量的相關計算 活動橫梁結構 如圖 2示,活動橫梁高度一般為箱體跨度的( ,在此取活動橫梁箱體高度為 50? ,活動橫梁鑄造箱體壁厚取為 ?a?40板厚度為?b? 40 圖 2動橫梁結構圖 2動橫梁受力分析如圖 2 圖 2動橫梁受力圖 2則活動橫梁最大彎矩計算式為: m a x 42qF b a??? ? ?????(2李聳 : 液壓機及主缸設計 18 則中心截面處強度: ? ?m a x 1m a x ??(2代入數(shù)值計算得 ? ?66m a x 5 5 1 0 6 5 1 0M P a M P a??? ? ? ? ? 所以下橫梁強度 符合要求。 體框架式機身強度、剛度計算 1)受力分析 [4] 上橫梁有油缸接觸面積與柱塞間距比值較大時,上橫梁可視為受兩個集中應力2具與下橫梁接觸面較大,故視為在某個長度上作用一均勻分布載荷,如圖 2于機架受力情況直接影響著它的設計及生產(chǎn)工藝,對于本次設計的三梁四柱式液壓機機架仍才用此種受力分析模型,其受彎矩如圖 2示,可通過對機架的受彎矩的分析從而推導得出液壓機機身強度、剛度情況: 圖 2架受力圖 2架彎矩圖為: 遼寧工程技術大學畢業(yè)設計 (論文 ) 19 圖 2架彎矩圖 2)強度計算 根據(jù)上述受力分析可知,框架仍可采用變形法或力法求解 則其有關節(jié)點的彎矩值為: 232 3 1 1 3 2 2 3 1 3 28a K K a K K K K B????( 2 232 3 1 1 3 2 2 3 1 3 28a K K a K K K K B? ? ???( 2 ? ?1 1 14 F b ?? ? ?( 2 ? ?2 1 28 F b ?? ? ?( 2 式中 1K 、 2K —— 系數(shù),其中 21 1 / 3K ???, 22 1K ???; ? 、 ? —— 分別為均布載荷寬度和兩集中載荷的間距與支柱間距的比值; A 、 B —— 同前。 則框架強度為: ?? ??? ( 2 代入數(shù)值計算得: ? ? 6 101 3 01099 ????? ?? ? ? 6 ????? ?? 李聳 : 液壓機及主缸設計 20 ? ?661 2 9 . 1 1 0 6 5 1 0P a P a??? ? ? ? ? ? ?2 3 0 . 1 1 0 6 5 1 0P a P a? ? ? ? ? 所以液壓機框架部分強度符合強度要求。 壓機的液壓系統(tǒng) 壓系 統(tǒng)機構形式及特點 本次設計液壓系統(tǒng)采用泵直接傳動液壓機,其原理如圖 2壓液體直接有液壓泵送入工作缸,工作時液壓泵 6 打出的高壓液體經(jīng)分配器 5 進入工作缸 2,回程缸 1 中的液體則經(jīng)分配器 5 排入液箱 7;回程時液壓泵打出的高壓液體,經(jīng)分配器進入回程缸,而工作缸中的液體大部分經(jīng)充液閥 3排入充液罐 4。 泵直接傳動具有如下特點 [5]: 1)液壓機活動橫梁的行程速度取決于泵的供液量,而與工藝過程中鍛件變形阻力無關。理論形成速度 v 為: ??( 2 圖 2壓系統(tǒng)原理圖 2泵的供液量為常量時,則液壓機的工作速度不變,故易于實現(xiàn)恒速,適用于要求恒速的液壓機。 2) 高壓泵多消耗的功率(壓力 ? 流量)相當于液壓機作功的功率(速度 ? 力)。即泵的遼寧工程技術大學畢業(yè)設計 (論文 ) 21 供液壓力和消耗功率取決于加工工件的變形阻力。鍛件變形阻力大,供液壓力與消耗功率亦大;反之則小。 3)由于在工作行程中動梁速度恒定,而供液壓力與鍛件變形阻力存在相適應的變化規(guī)律,因此可利用該恒定的速度及變化的壓力作為操縱分配器的信號,實現(xiàn)液壓機的自動控制。泵直接傳動的優(yōu)點是:基本投資少,占地面積少,日常維護和保養(yǎng)簡單。 般通用液壓機的液壓系統(tǒng) 一般通用型液壓機的工藝用途廣泛 ,適用于金屬板料的沖壓工藝和金屬于非金屬粉末制品的壓 制成型工藝 ,并可用于校正和壓裝等工藝 型工廠產(chǎn)品種類較多而生產(chǎn)批量又不大的情況。主要有幾個優(yōu)點 [6]: 1)一般設又充液系統(tǒng),可實現(xiàn)空程快速運動,以減少輔助時間; 2)設有浮動的頂出缸; 3)結構簡單,容易維護。 圖 2用型液壓機液壓原理圖 22、 5、 7、 834、 106 911121314 15161718 李聳 : 液壓機及主缸設計 22 液壓系統(tǒng)工作過程 表 2磁鐵動作順序表 [7] 2作 1程快速下降 + + 慢速下降及加壓 + 保壓 卸壓和回程 + 停止 + 頂出 + 頂出活塞退回 + 停止 注: +表示電磁鐵通電 油路分析 1. 主缸的運動 1)快速下行。 按下啟動按鈕,電磁鐵 15電使電液動換向閥 6 切換至右位,電磁換向閥 8切換至右位,輔泵 2的控制壓力油經(jīng)閥 8液控單向閥 9打開。此時,主油路的流動路線如下: 進油: 主泵 1 電液換向閥 6(右) 向閥 13主缸 16上腔 回油:主缸下腔 液控單向閥 9電液換向閥 6(右) 電液換向閥 21油箱 在主缸快速下行的起初階段,尚未觸及工件時,主缸活塞在自重作用下迅速下行。這時泵1 的流量還不足以補充主 缸上腔孔處的體積,因而上腔形成真空。 所以置于液壓機頂部的副油箱 15中的油液在大氣壓及液位高度作用下,經(jīng)帶卸荷閥芯的液控單向閥 14進入主缸上腔。 2)減速加壓。 當滑塊 22上的活動擋塊 23 壓下行程開關 2磁鐵 5 復至左位,液控單向閥 9 關閉。此時主缸上腔壓力升高,閥 14 關閉,且主泵 1 的排量自動減小,主缸轉為慢速接近工件和加壓階段。系統(tǒng)油液流動線路圖如下: 進油: 主泵 1 電液換向閥 6(右) 向閥 13主缸 16上腔 回油:主缸下腔 背壓閥 10電液換向閥 6(右) 電 液換向閥 21(中) 油箱 。 接觸工件后,阻力增加,上腔油液升高,關閉液控單向閥 14。這是只有泵 3繼續(xù)向主遼寧工程技術大學畢業(yè)設計 (論文 ) 23 缸上腔供高壓油,推動活塞慢速下行,對工件加壓。主缸下腔排油將液控單向閥 9封閉,經(jīng)背壓閥 10 回油箱。這樣,當快速行程轉為工作行程時,速度減低,從而避免了液壓沖擊。系統(tǒng)中的遠程調壓閥 5可使液壓機在不同的壓力下工作:安全閥 4用于防止系統(tǒng)超載。 3)保壓延時。當主缸上腔的油液達到要求的數(shù)值時,由壓力繼電器 12 發(fā)信號,使電液換向閥 6 回復中位,將主缸上下腔油液封閉。這時泵 1 也泄荷,而單向閥 13 背高壓油自動關閉,主缸上腔進入保壓狀態(tài)。但這種實現(xiàn)保壓的方法要求主缸活塞、單向閥、(保壓閥)及其間的管道具有很高的密閉性能,若泄漏較大,壓力會迅速下降,無法實現(xiàn)保壓。在保壓過程中 主 泵 1的壓力油經(jīng)換向閥 6和 21 回油箱,使泵卸荷。 進油:無 。 回油: 主 泵 1電液換向閥 6電液換向閥 21油箱 4)泄壓回程。保壓時主缸上腔油液的壓縮和管道膨脹儲存了能量,而使其上腔的油壓很高,再加上主缸為差動油缸,所以當電液換向閥 6很快切換到回程位置,會使回程開始的短時間內(nèi)泵 1及主缸下腔的油壓升得很高,比保壓時主油路的壓力還要高得多,以致引起沖擊和振動。所以保壓后必須先逐漸泄壓然后再回程,以防沖擊和振動發(fā)生。該液壓系統(tǒng)保壓完畢,壓力繼電器 12 控制時間繼電器 信號 (定程成形時,由擋鐵壓行程開關3信號 ),使各閥處 于回程位置,回程開始。主缸上腔高壓油打開泄壓閥 11并且液控單向閥 14 也被打開,使泵 1 來的油經(jīng)泄壓閥 11 中的阻尼孔 (形成一定阻力 )回油箱,泵 1成為低負荷運轉。這時主缸活塞并不馬上回程,待上腔壓力降低,泄壓閥被關閉后,泵 1的油才能進入主缸下腔開始回程。 主油路:先卸壓: 進油: 主泵 1電液換向閥 6液控單向閥 14開 回油: 主 泵 1電液換向閥 6 泄壓閥 11 油箱 主缸上腔 液控單向閥 14 充液筒(大量) 5)泄壓回程 : 進油: 主 泵 1電液換向閥 5液控單向閥 9主缸下腔 回油:主缸上腔 液控單向閥 14充液筒(大量) 主缸驅動滑塊快速回程。 6)回程停止。當主缸擋鐵壓行程開關 1, 電磁鐵 2復至中位,被該閥 M 型機能的中位鎖 緊而停止運動 ,主缸活塞回程停止。 主 泵 1 經(jīng)電液換向閥 6 和 21 卸荷。 李聳 : 液壓機及主缸設計 24 進油:無 。 回油: 主 泵 1電液換向閥 6電液換向閥 21油箱 2、 頂出缸的運動 頂出缸的動作是在主缸停止時才能進行的,因為進入頂出缸的壓力油,經(jīng)過缸油路的電液換向閥 6后,才通入頂出缸油路的電液換向閥 21的。電液換向閥 6處在中間位置即主缸停止運動時,才能實現(xiàn)定出和頂退運動, 保證免除誤動作。 1) 頂出。按下按鈕, 電磁鐵 3使電液換向閥 21在左位工作,從泵 1來的壓力油進入頂出缸下腔,頂出缸 17的活塞上升將工件頂出。 進油: 主 泵 1電液換向閥 6(中位) 電液換向閥 21(左) 頂出缸 17下腔 回油:頂出缸 17上腔 電液換向閥 21油箱 活塞上升,將工件頂出。 2)頂退 . 3 4電時, 使電液換向閥 21在右位工作,從泵 1來的壓力油進入頂出缸 17上腔,頂出缸 17的活塞向下退回。 進油: 主 泵 1電液換向閥 6電液換向閥 21頂出缸 17上腔 回油:頂出缸 17下腔 電液換向閥 油箱 3)停止。按下按鈕,使各閥處于停止位置,頂出缸活塞停止運動。 進油:無 回油; 主 泵 1電液換向閥 6電磁換向閥 21油箱 頂出缸 17上腔 電液換向閥 21->油箱 4)壓邊。 作薄板拉伸時的壓邊動作,頂出缸 17停止在頂出位置。這時頂出缸 17下腔油液被電液換向閥 21封閉,所以當主缸活塞下壓時,頂出缸 17活塞 被迫隨之下行 (此時閥 21中位,泵 1卸荷 ),頂出缸 17 下腔的油液只能經(jīng)固定節(jié)流器和溢流閥 20緩慢流回油箱,從而建立起所需的溢流閥 20用來調節(jié)壓邊壓力;安全閥 18是當固定節(jié)流器 19 阻塞時起安全作用。 主油路: 進油: 主 泵 1電液換向閥 20背壓閥 10主缸上腔 回油:主缸下腔 背壓閥 10電液換向閥 6 電液換向閥 21油箱 輔助油路: 遼寧工程技術大學畢業(yè)設計 (論文 ) 25 開始:頂出缸處頂出位,油路同頂出 主缸活塞下行時,頂出缸活塞被迫下行,此時回油: 頂出缸下腔 固定節(jié)流器 19溢流閥 20油停止。按 下按鈕,使各閥處于停止位置,頂出缸活塞停止運動。 進油:無 。 回油 :主 泵 1電液換向閥 6電磁換向閥 21油箱頂出缸上腔 電液換向閥21油箱 液壓機主缸活塞及其所帶的滑塊往往很重,為防止活塞回程停止后,因泄漏或其它或其他原因 (如泵電機突然掉電 )而自動下滑,回路中裝有液控單向閥 9和背壓閥 10來封閉主缸下腔的油液,起支承平衡作用,保證主缸活塞可靠地停留在任何位置。但為防止因閥9失靈 (不通 )使主缸下腔產(chǎn)生超高壓事故,背壓閥 10起安全作用。其背壓所產(chǎn)生的抗力,足以支持活塞 及其所帶動的滑塊的自重,即光靠自重無法頂開背壓閥 10,所以活塞不會自動下落。 主液壓缸和頂出液壓缸的換向都由電液換向閥擔當。為使兩缸動作協(xié)調,兩個電液換向閥 21和 6這樣配置,即主缸油路的回油要經(jīng)過頂出缸油路的電液換向閥 21才能回油箱,從而保證了頂出缸停止動作時,主缸才能運動。而且頂出缸的進油要經(jīng)過控制主缸油路的閥 6,這就保證了主缸處于停止時,頂出缸才能運動。 當液壓機系統(tǒng)壓力高時,為避免換向沖擊,電液換向閥由外控供油,必須有低壓控制油路,不宜直接引用主油路的高壓油。該 系統(tǒng)采用單獨的小流量輔助液壓泵作為能源的低壓控制油路,壓力穩(wěn)定,工作可靠。 液壓系統(tǒng)的分析: 1)液壓機工作循環(huán)中,壓力、形成速度和流量變化較大,泵的輸出功率也較大。如何滿足液壓機工作循環(huán)要求,又使能量消耗最小,是液壓機的液壓系統(tǒng)中要考慮的問題。 通常有兩種供油方案:一種是采用高低壓泵組,用一個高壓小流量柱塞泵和一個低壓大流量齒輪泵組合起來向系統(tǒng)供油;另一種是采用恒功率變量柱塞泵向系統(tǒng)供油,以滿足低壓快速行程和高壓慢速行程的要求。 2)在不增加主油泵功率的前提下提高快速行程速度以提高生產(chǎn)率,其基本方法是 增加低壓供油的流量或減小活塞面積,可采用自重充液、蓄能器強制充液、快速缸、輔助缸或李聳 : 液壓機及主缸設計 26 差動回路宋提高低壓快速行程的速度。當快速行程轉為慢速工作行程時,為了避免沖擊,可通過減速回路減速。 3)立式液壓機為使滑塊可靠地停留在任何位置,須采用平衡回路,可根據(jù)具體要求選用各種基本回路來組合。 4)由于液壓機主油路壓力較高,為避免換向沖擊,電液換向閥一般由低壓、外控油路來控制,不宜直接引用主油路的高壓油。 5)液壓機工作循環(huán)中的保壓過程與制品質量密切相關,很多液壓機均要求保壓性能。保壓后必須逐漸泄壓,泄壓過快,將引 起液壓系統(tǒng)劇烈的沖擊,振動和噪聲。因此保壓和泄壓是液壓機系統(tǒng)必須考慮的兩個問題。 6)液壓機的液壓系統(tǒng)屬高壓、大流量和大功率系統(tǒng)。因此,合理利用功率以降低溫升非常重要。這類液壓系統(tǒng)是高壓,又有保壓要求,密封問題更為突出,應予以特別注意。 3 液壓機主缸設計 本章對液壓機主缸進行具體的設計計算,得出主缸的相關主要參數(shù)數(shù)值,并對數(shù)值進行校核計算,得出最終設計結構,并使設計所得液壓機主缸能夠滿足設計要求。 遼寧工程技術大學畢業(yè)設計 (論文 ) 27 壓缸的主要性能參數(shù)的計算 壓缸的壓力值 液壓缸的壓力 為油液作用在單位面積上的壓力 8]。 壓力值的建立是有負載力產(chǎn)生的,在同一個活塞的有效面積上負載力越大,克服負載力所需要的壓力就越大。額定壓力(公稱壓力) 次設計額定壓力數(shù)值為原始條件 2500 按主機類型選擇相、對應工作壓力,液壓機屬于高壓機械,工作壓力選擇范圍為 20—— 30步定本次設計工作壓力為 25 塞的運動速度 活塞的運動速度為 單位時間內(nèi)壓力油液推動活塞移動的距離。 運動速度可表示為 v= ( 3 當活塞桿伸出時 v= 324 10 ?? ( 3 由上式可得出對于已確定的液壓缸,伸出速度 。 可根據(jù)液壓 機整體工作需要選擇相應的流量泵,從而控制液壓缸速度 v。 同上伸出公式理,可得: 當活塞桿縮回時 v=3224 10() ???( 3 當 v=常數(shù),但實際上,活塞在行程兩端各有一個加、減速 階段(如下圖所示),故上式中計算的數(shù)值均為最高速度 李聳 : 液壓機及主缸設計 28 T sS a S iT 塞速度變化圖 [9] 3塞的最高運動速度 于活塞運動速度的選擇,當速度過低時可能造成爬行,液壓缸不能正常工作,故 綜合液壓機應用及公稱壓力值,參照法國 步確定 壓缸的速比 計算液壓缸的速比主要是為了確定活塞桿和直徑要否設置緩沖裝置,速比過大或過小,容易造成過大的背部壓或造成活塞桿太細,影響穩(wěn)定性 221 2221v A D d? ? ? ? ?(3查表選擇 ? =2 塞的理論推力和拉力 對于雙作用單活塞桿液壓缸來說,活塞受力如 下圖所示 [10]: 遼寧工程技術大學畢業(yè)設計 (論文 ) 29 A 1D P 1A 2圖 3塞受力示意圖 3塞桿伸出時的理論推力為 6 2 611 1 0 1 04P A p D p?? ? ? ?(3260 5 1 04?? ? ?2530 活塞桿縮回時的理論推力為 6 2 2 622 1 0 ( ) 1 04P A p D d p?? ? ? ? ?(32 2 6( 0 . 4 0 . 2 8 ) 2 5 1 04?? ? ?700 壓缸缸筒設計 液壓缸缸筒是液壓缸的主要零件,它與缸蓋、缸底、油口等零件構成密封的容腔,用以容納壓力油液,同時它還是活塞運動的“軌道”。缸筒的設計主要為正確確定各部 分尺寸,保證液壓缸有足夠的輸出力、運動速度和有效行程,同時還必須具有一定的強度,能足以承受液壓力、負載力和意外的沖擊了力;缸筒的內(nèi)表面應具有合適的配合公差等級、表面粗糙度和形位公差等級,以保證液壓缸的密封性、運動平穩(wěn)性和耐用性。 壓缸缸筒機構及材料的選擇 本次設計液壓缸缸筒機構選擇為內(nèi)螺紋連接形式,具體機構參照下圖。該結構具有構造簡單、重量較輕、外徑較小、安裝簡單等優(yōu)點;缺點是端部結構復雜、裝卸時需要專門李聳 : 液壓機及主缸設計 30 的工具、再者就是擰端部蓋時可能把密封圈擰扭。 圖 3壓缸缸筒結構圖 3壓缸缸筒材料要求有足夠的強度和沖擊韌性,對焊接不見還要求有良好的焊接性能。根據(jù)液壓缸的參數(shù)、用途和毛坯來源等可選用以下材料 :35 4525, , 5 , 3 5 , 3 8G r M o G r M o G r M o A 前市場上還有采用退火冷拔或熱軋的無縫鋼管,國際市場上已有內(nèi)孔經(jīng)衍磨或內(nèi)孔精加工,只需按所要求的長度切割無縫鋼管。其主要要求是 [11]: 1) 要有足夠的強度,能長期承受最高工作壓力及短期動態(tài)實驗壓力而不至產(chǎn)生永久變形; 2)有足夠的剛度,能承受活塞側向力和安裝的反作用力而不致產(chǎn)生彎曲; 3)內(nèi)表面與活塞密封件及導向環(huán)的摩擦力作用下,能長期工作而磨損少,尺寸公差等級和形位公差等級足以保證活塞密封件的密封性。 綜合以上各項要求初步確定缸筒材料選擇為 35材料參數(shù)為: s??1000[]? =2s?=850 壓缸缸筒的計算 1)缸筒內(nèi)徑的計算 [12] 液壓缸內(nèi)徑通常根據(jù)液壓缸的牽引力 壓缸的牽引力應能克服所受到的阻力。總阻力包括公稱壓力1F;密封裝置的摩擦力2F;回油腔因背壓作遼寧工程技術大學畢業(yè)設計 (論文 ) 31 用產(chǎn)生的阻力3最大牽引力 1 2 3 4F