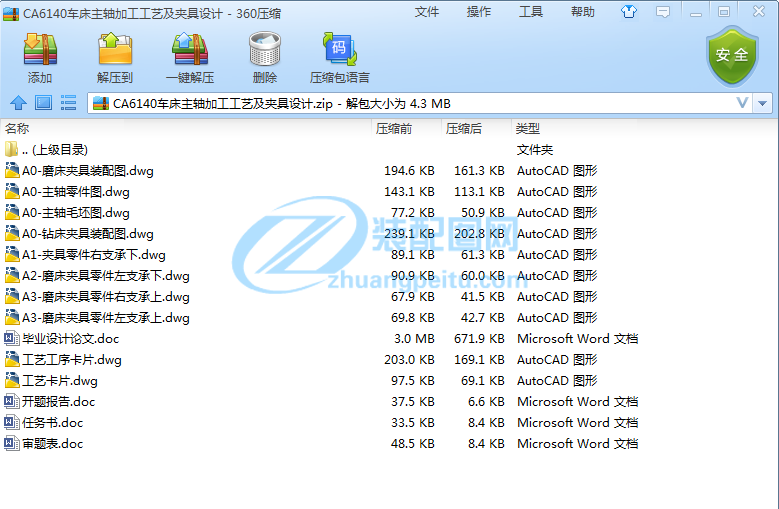

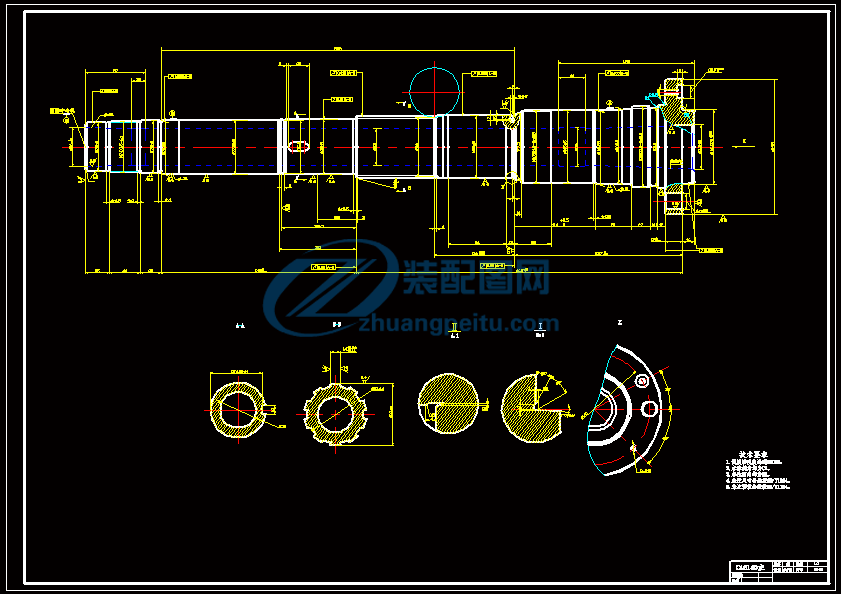
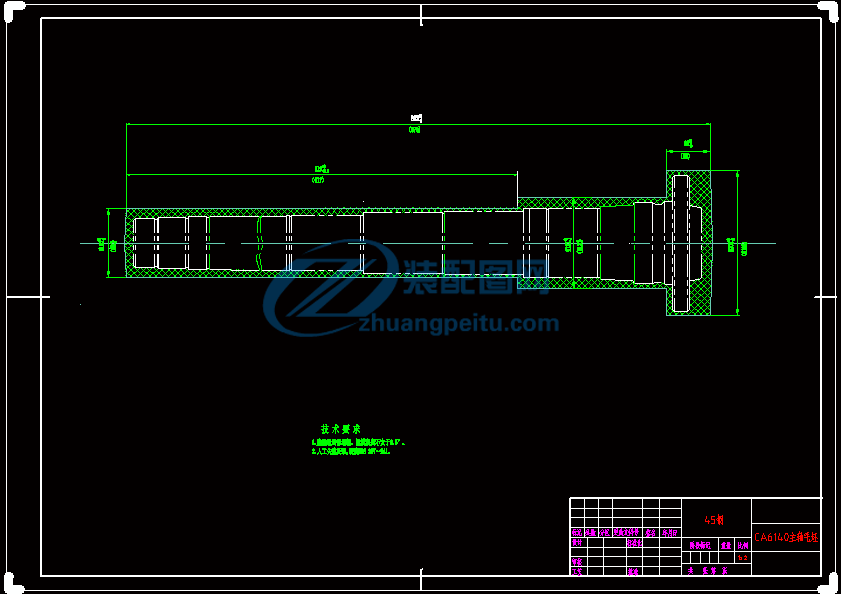
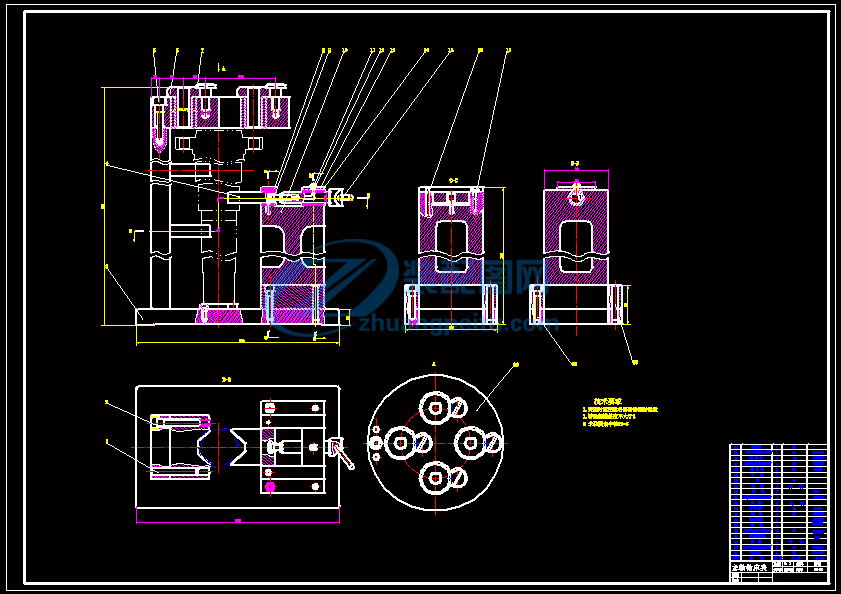

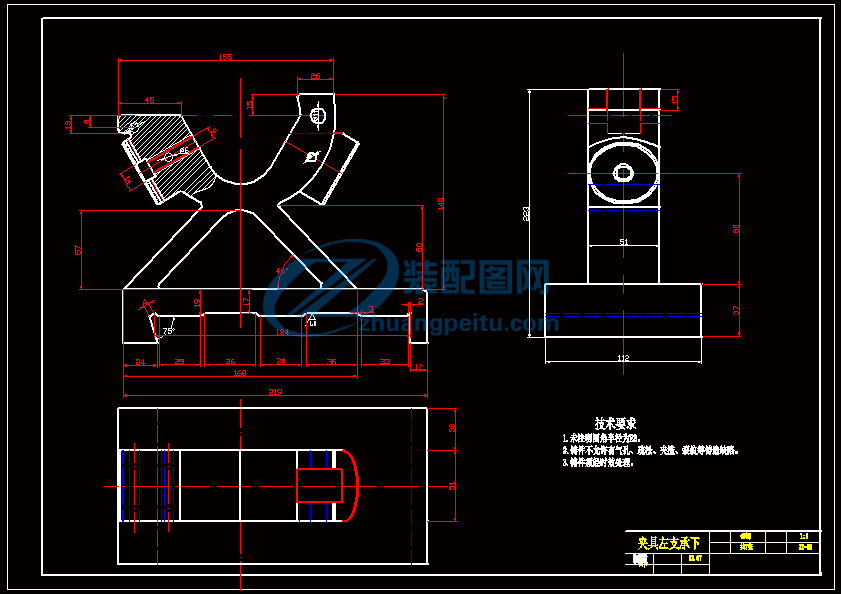
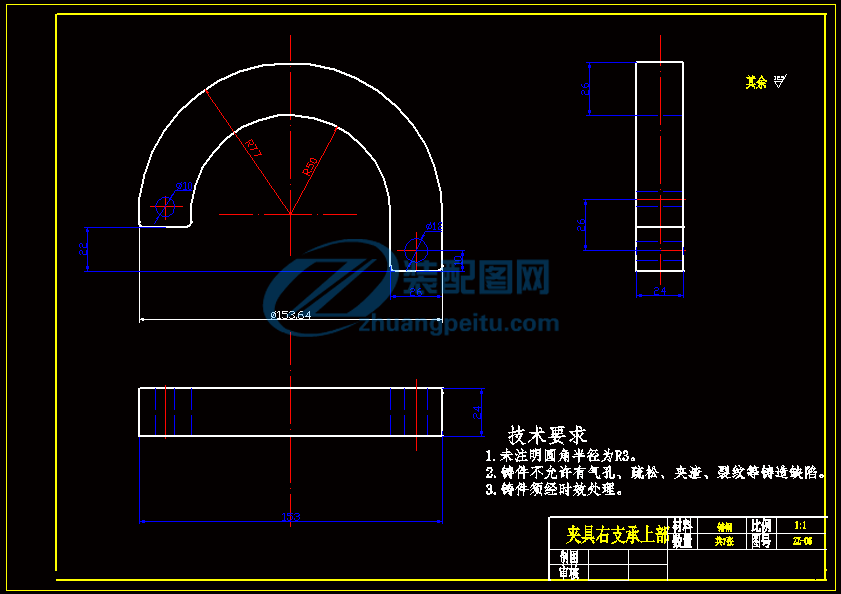

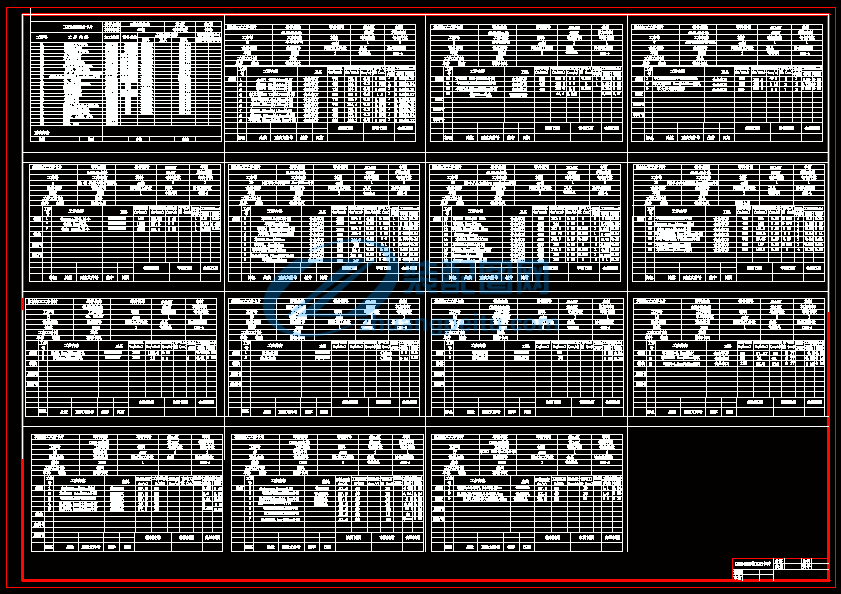
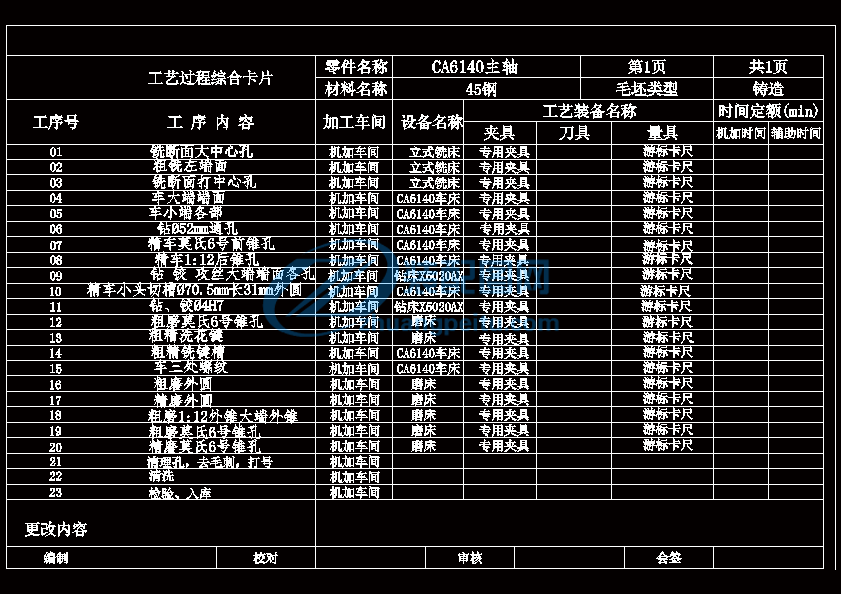
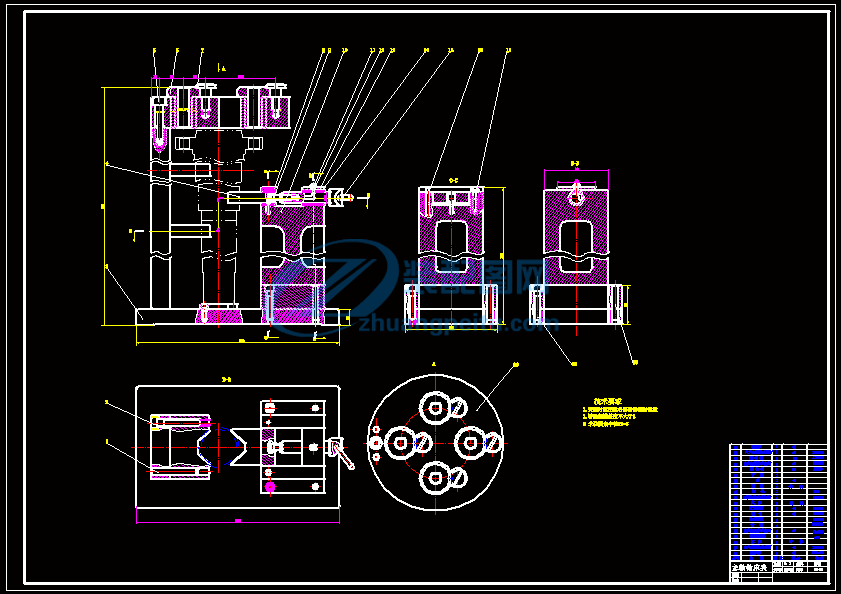

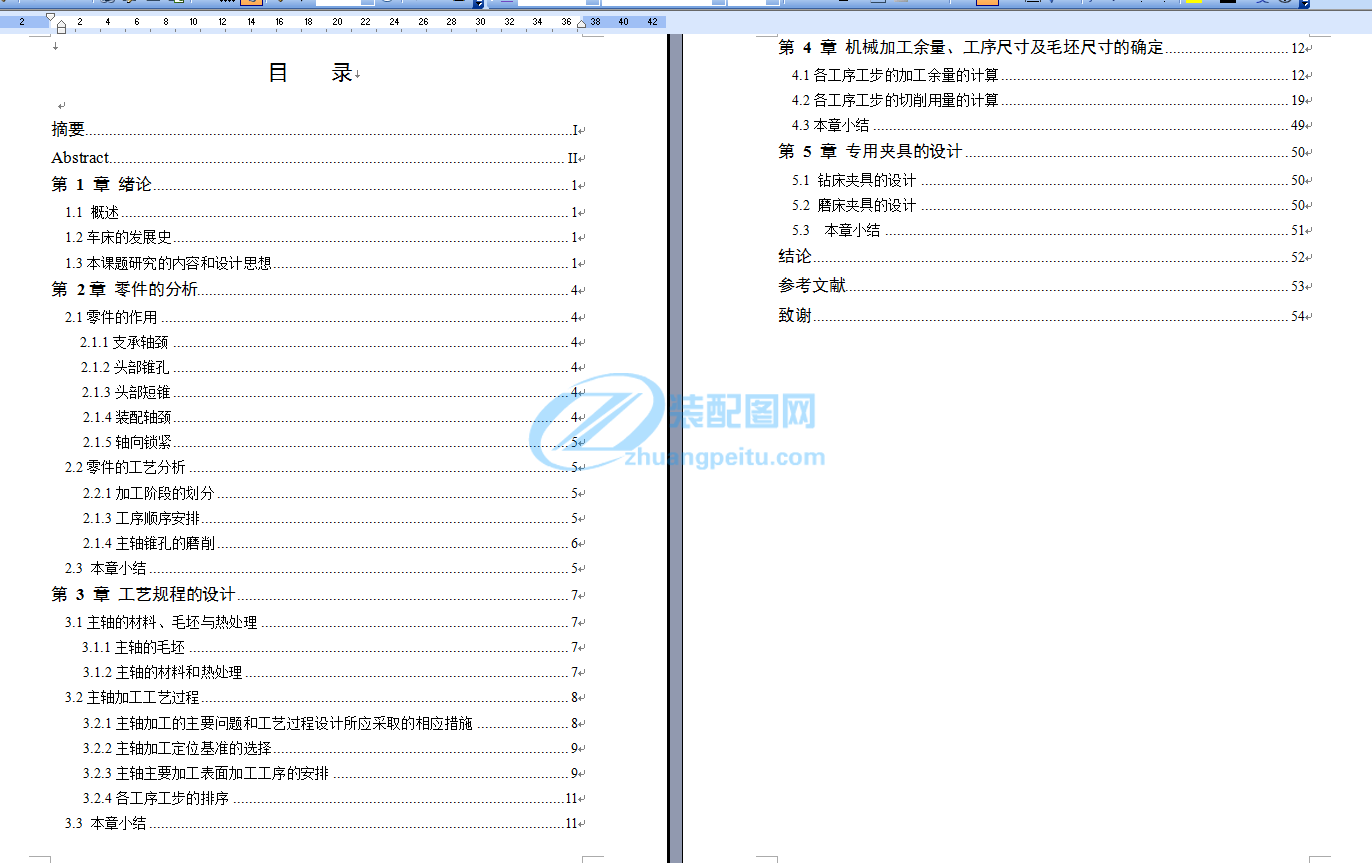
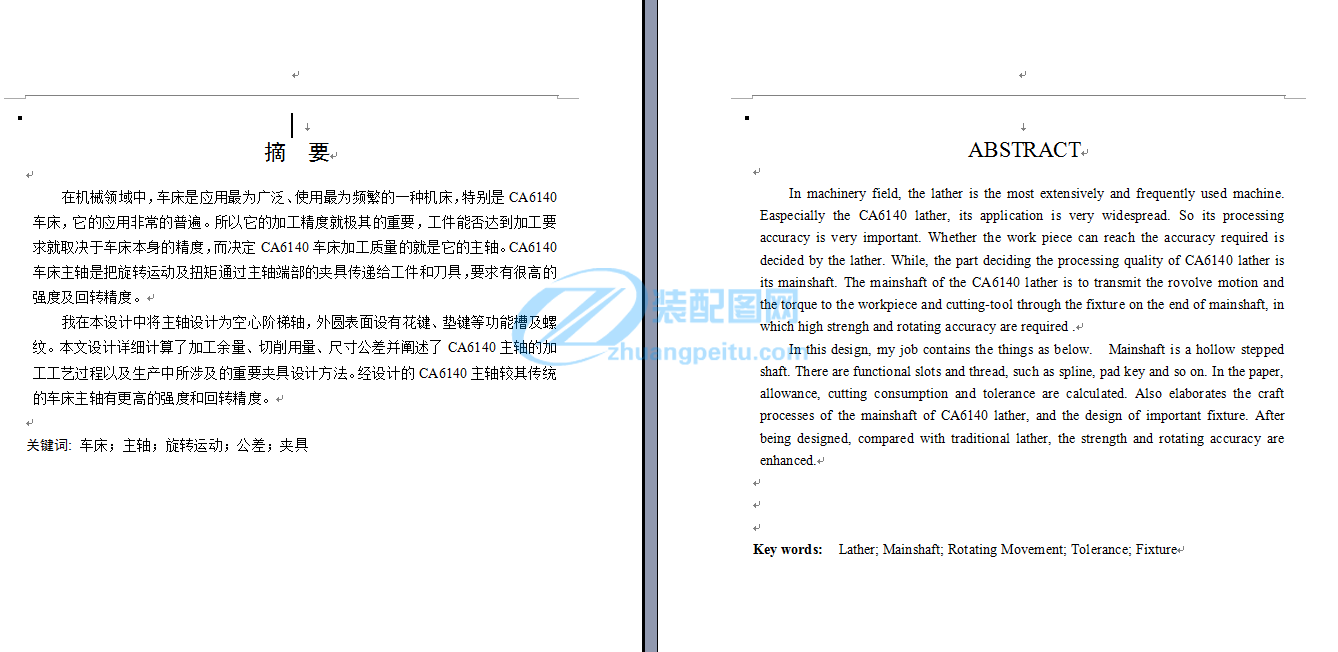
畢業(yè)設(shè)計(論文)任務(wù)書學生姓名 系部 機電工程系 專業(yè)、班級指導教師姓名 職稱 從事專業(yè) 機械設(shè)計 是否外聘 □是□否題目名稱 CA6140 主軸工藝與夾具的設(shè)計一、設(shè)計(論文)目的、意義1.設(shè)計目的:車床是機械制造中使用最廣泛的一種機床,它的加工精度極其重要,工件能否達到加工要求就取決于車床本身的精度,而決定車床的加工質(zhì)量的就是它的主軸。 CA6140 主軸的設(shè)計為空心階梯軸,表面設(shè)花鍵.墊鍵等功能槽及及螺紋,可以使它具有更高的強度和回轉(zhuǎn)精度。2.設(shè)計意義:通過本次設(shè)計,使我將大學四年所學習到的知識應(yīng)用到了理論設(shè)計中,鞏固了機械設(shè)計的基礎(chǔ)知識,提高了設(shè)計的能力 ,為以后的工作學習打下了堅實的基礎(chǔ)。二、設(shè)計(論文)內(nèi)容、技術(shù)要求(研究方法)1. 設(shè)計內(nèi)容對 CA6140 主軸的加工工藝的分析計算:確定加工工序;設(shè)計加工過程中夾具的裝夾。主軸長 815mm;小端軸徑 70mm;?大端軸徑 115mm; 倒角 C2;中間內(nèi)徑 52mm.2. 技術(shù)要求1. 設(shè)計計算的正確性;2. 主要構(gòu)件的結(jié)構(gòu)具有經(jīng)濟性.合理性;3. 設(shè)計的工藝性,裝配的可行性,主要裝配精度的合理性,主要參數(shù)的可檢查性。SY-025-BY-2三、設(shè)計(論文)完成后應(yīng)提交的成果1.計算說明書部分計算說明書打印版 1 份,電子版 1 份2.圖紙部分0 號圖紙兩張,零件圖紙若干張,總合成四張 0 號圖紙。四、設(shè)計(論文)進度安排1—4 周 進行實踐調(diào)查,并查閱相關(guān)文獻,觀察實物,確定設(shè)計方案;5—8 周 對所收集資料整理、匯編,寫文獻綜述各開晤面報告,繪制草圖;9—10 周 進行總體設(shè)計,確定各部分的組成,工作方式,CAD 出圖;11—12 周 整理修改設(shè)計說明書和圖;13 周 對說明書和圖紙進行最后修改。五、主要參考資料[1]王季琨 沈中偉 劉錫珍.機械制造設(shè)計工藝學 [M].天津大學出版社 ,1984[2]倪森壽.機械制造工藝與裝備[M].化學工業(yè)出版社,2002 [3]魏抗民 王曉宏 .機械制造工藝裝備 [M].重慶大學出版社 ,1998[4]梁炳文 .機械加工工藝與竅門[M] .機械工業(yè)出版社,2001[5]王啟平.機械機造工藝學 [M].哈工大工業(yè)大學出版社,2000[6]王光斗 王春福 .機床夾具設(shè)計手冊 [S].燕山大學 洛陽工學院 ,1999[7]符煒.切削加工手冊 [S] 湖南科學技術(shù)出版社 ,2001[8]吳宗澤.機械零件設(shè)計手冊[S].機械工業(yè)出版社,2004六、備注指導教師簽字:年 月 日教研室主任簽字: 年 月 日SY-025-BY-3畢業(yè)設(shè)計(論文)題目審定表指導教師姓名 職稱 從事專業(yè) 機械設(shè)計 是否外聘 □是□否題目名稱 CA6140 主軸工藝與夾具的設(shè)計課題適用專業(yè) 機械設(shè)計制造及其自動化 課題類型 X課題簡介:(主要內(nèi)容、意義、現(xiàn)有條件、預(yù)期成果及表現(xiàn)形式。)主要內(nèi)容:本文設(shè)計主要闡述了 CA6140 主軸的加工工藝過程,在設(shè)計中詳細計算了在加工中的加工余量.切削用量.尺寸公差以及并設(shè)計了在生產(chǎn)中所涉及的重要夾具的裝夾方法。意義:本設(shè)計中 CA614 主軸為空心階梯軸, 外圓表面設(shè)有花鍵、墊鍵等功能槽螺紋 ,較其傳統(tǒng)的車床主軸,有更高的強度和回轉(zhuǎn)精度?,F(xiàn)有條件: 通過查閱文獻,獲得相關(guān)資料,加之對機械原理與設(shè)計的學習,并已掌握繪圖軟件的應(yīng)用,有條件進行該課題的設(shè)計。時間安排:1~4 周調(diào)研收集資料,并查閱相關(guān)文獻,確定設(shè)計方案;5~8 周初步進行總體設(shè)計,確定各部分組成,繪制草圖;9~10 周各零部件的校核,CAD 出圖;11~12 周整理打印設(shè)計說明書,并讓老師對圖紙和說明書審查;13 周對圖紙和說明書,做最后修改,準備答辯提交成果:設(shè)計圖紙 5~6 張、說明書一份、光盤一張指導教師簽字: 年 月 日1 選題與專業(yè)培養(yǎng)目標的符合度 □好 □較好 □一般 □較差2 對學生能力培養(yǎng)及全面訓練的程度 □好 □較好 □一般 □較差3 選題與生產(chǎn)、科研、實驗室建設(shè)等實際的結(jié)合程度 □好 □較好 □一般 □較差4 論文選題的理論意義或?qū)嶋H價值 □好 □較好 □一般 □較差5 課題預(yù)計工作量 □較大 □適中 □較小6 課題預(yù)計難易程度 □較難 □一般 □較易教研室意見教研室主任簽字: 年 月 日SY-025-BY-1系(部)教學指導委員會意見:負責人簽字: 年 月 日注:課題類型填寫 W.科研項目;X. 生產(chǎn)(社會)實際; Y.實驗室建設(shè);Z.其它。畢業(yè)設(shè)計(論文)開題報告學生姓名 系部 機電工程系 專業(yè)、班級指導教師姓名 職稱 從事專業(yè) 機械設(shè)計 是否外聘 □是□否題目名稱 CA6140 主軸工藝與夾具的設(shè)計一、 課題研究現(xiàn)狀,選題的目的、依據(jù)和意義研究現(xiàn)狀:在機械領(lǐng)域中,車床是應(yīng)用最為廣泛、使用最為頻繁的一種機床,它的加工精度就極其的重要,工件能否達到加工要求就取決于車床本身的精度,而車床主軸是把旋轉(zhuǎn)運動及扭矩通過主軸端部的夾具傳遞給工件和刀具,因此要求有很高的強度及回轉(zhuǎn)精度。選題目的、依據(jù)和意義:本次設(shè)計選用此課題,主要是對主軸與夾具的設(shè)計過程,是對大學四年所學知識的檢測、總結(jié)與應(yīng)用。這次的設(shè)計過程是提高機械設(shè)計與創(chuàng)新能力的體現(xiàn),同時是對所學習過的理論知識與設(shè)計過程的結(jié)合。二、 設(shè)計(論文)的基本內(nèi)容,擬解決的主要問題基本內(nèi)容:CA6140 主軸加工工藝過程,加工過程中的具體用量的計算,加工中鉆床.磨床夾具的設(shè)計。擬解決的主要問題:加工過程中加工余量和切削用量的計算,夾具裝夾的計算,零件的選擇。三、 技術(shù)路線(研究方法)1.查閱相關(guān)文獻資料了解課題。2.對比分析現(xiàn)有幾個設(shè)計方案,選擇最適合本次設(shè)計的方案。3.計算各層臺體部分的質(zhì)量和轉(zhuǎn)動慣量,選擇驅(qū)動裝置和驅(qū)動方式。4.根據(jù)選擇的設(shè)計方案,進行總體設(shè)計。5.完成設(shè)計圖紙和說明書,準備答辯。四、 進度安排1~4 周調(diào)研收集資料,并查閱相關(guān)文獻,確定設(shè)計方案;5~8 周初步進行總體設(shè)計,確定各部分組成,繪制草圖;9~10 周各零部件的校核,CAD 出圖;11~12 周整理打印設(shè)計說明書,并讓老師對圖紙和說明書審查;13 周對圖紙和說明書,做最后修改,準備答辯。五、 參考文獻[1]王季琨 沈中偉 劉錫珍.機械制造設(shè)計工藝學[M].天津大學出版社,1984[2]倪森壽.機械制造工藝與裝備[M].化學工業(yè)出版社,2002 [3]魏抗民 王曉宏.機械制造工藝裝備[M].重慶大學出版社,1998[4]梁炳文 .機械加工工藝與竅門[M] .機械工業(yè)出版社,2001[5]王啟平.機械機造工藝學[M].哈工大工業(yè)大學出版社,2000[6]王光斗 王春福.機床夾具設(shè)計手冊[S].燕山大學 洛陽工學院,1999[7]符煒.切削加工手冊[S] 湖南科學技術(shù)出版社,2001[8]吳宗澤.機械零件設(shè)計手冊[S]. 機械工業(yè)出版社,2004六、備注指導教師意見:簽字: 年 月 日I摘 要在機械領(lǐng)域中,車床是應(yīng)用最為廣泛、使用最為頻繁的一種機床,特別是CA6140 車床,它的應(yīng)用非常的普遍。所以它的加工精度就極其的重要,工件能否達到加工要求就取決于車床本身的精度,而決定 CA6140 車床加工質(zhì)量的就是它的主軸。CA6140 車床主軸是把旋轉(zhuǎn)運動及扭矩通過主軸端部的夾具傳遞給工件和刀具,要求有很高的強度及回轉(zhuǎn)精度。我在本設(shè)計中將主軸設(shè)計為空心階梯軸,外圓表面設(shè)有花鍵、墊鍵等功能槽及螺紋。本文設(shè)計詳細計算了加工余量、切削用量、尺寸公差并闡述了 CA6140 主軸的加工工藝過程以及生產(chǎn)中所涉及的重要夾具設(shè)計方法。經(jīng)設(shè)計的 CA6140 主軸較其傳統(tǒng)的車床主軸有更高的強度和回轉(zhuǎn)精度。關(guān)鍵詞: 車床;主軸;旋轉(zhuǎn)運動;公差;夾具ABSTRACTIn machinery field, the lather is the most extensively and frequently used machine. Easpecially the CA6140 lather, its application is very widespread. So its processing accuracy is very important. Whether the work piece can reach the accuracy required is decided by the lather. While, the part deciding the processing quality of CA6140 lather is its mainshaft. The mainshaft of the CA6140 lather is to transmit the rovolve motion and the torque to the workpiece and cutting-tool through the fixture on the end of mainshaft, in which high strengh and rotating accuracy are required .In this design, my job contains the things as below. Mainshaft is a hollow stepped shaft. There are functional slots and thread, such as spline, pad key and so on. In the paper, allowance, cutting consumption and tolerance are calculated. Also elaborates the craft processes of the mainshaft of CA6140 lather, and the design of important fixture. After being designed, compared with traditional lather, the strength and rotating accuracy are enhanced.Key words: Lather; Mainshaft; Rotating Movement; Tolerance; Fixture目 錄摘要 IAbstract II第 1 章 緒論.11.1 概述11.2 車床的發(fā)展史.11.3 本課題研究的內(nèi)容和設(shè)計思想.1第 2 章 零件的分析 42.1 零件的作用.42.1.1 支承軸頸 .42.1.2 頭部錐孔 .42.1.3 頭部短錐 .42.1.4 裝配軸頸 .42.1.5 軸向鎖緊 .52.2 零件的工藝分析.52.2.1 加工階段的劃分 .52.1.3 工序順序安排 .52.1.4 主軸錐孔的磨削 .62.3 本章小結(jié)5第 3 章 工藝規(guī)程的設(shè)計 .73.1 主軸的材料、毛坯與熱處理.73.1.1 主軸的毛坯 .73.1.2 主軸的材料和熱處理 .73.2 主軸加工工藝過程.83.2.1 主軸加工的主要問題和工藝過程設(shè)計所應(yīng)采取的相應(yīng)措施 .83.2.2 主軸加工定位基準的選擇 .93.2.3 主軸主要加工表面加工工序的安排 .93.2.4 各工序工步的排序 .113.3 本章小結(jié)11第 4 章 機械加工余量、工序尺寸及毛坯尺寸的確定 .124.1 各工序工步的加工余量的計算.124.2 各工序工步的切削用量的計算.194.3 本章小結(jié).49第 5 章 專用夾具的設(shè)計 .505.1 鉆床夾具的設(shè)計505.2 磨床夾具的設(shè)計505.3 本章小結(jié)51結(jié)論 .52參考文獻 53致謝 .541第 1 章 緒 論1.1 概述精密機床的關(guān)鍵部件是進給系統(tǒng)和主軸系統(tǒng),不同類型的機床主軸,對所選用軸承的精度要求既有相同點,也有不同之處。數(shù)控機床和軸承磨床可以歸于精密機床一類。 現(xiàn)代精密機床和傳統(tǒng)機床的結(jié)構(gòu),從原理上來說,沒有太大的變化,主要還是區(qū)別于導軌加工技術(shù)的改進和主軸系統(tǒng)精度的提高。1.2 車床的發(fā)展史車床的發(fā)展大致可區(qū)分成四個階段,雛型期,基本架構(gòu)期、獨立動力期與數(shù)值控制期,底下將針對其發(fā)展的過程加以介紹。車床的誕生不是發(fā)明出來的,而是逐漸演進而成,早在四千年前就記載有人利用簡單的拉弓原理完成鉆孔 的工作,這是有記錄最早的工具機,即使到目前仍可發(fā)現(xiàn)以人力做為驅(qū)動力的手工鉆床,之后車床衍生而出,并被用于木材的車削與鉆孔,英文中車床的名稱 Lathe(Lath 是木板的意思 ) 就是由此而來,經(jīng)過數(shù)百年的演進,車床的進展很慢,木質(zhì)的床身,速度慢且扭力低,除了用在木工外,并不適合做金屬切削,直到工業(yè)革命前。這段期間可稱為車床的雛型期。18 世紀開始的工業(yè)革命,象征著以工匠主導的農(nóng)業(yè)社會結(jié)束,取而代之的是強調(diào)大量生產(chǎn)的工業(yè)社會,由于各種金屬制品被大量使用,為了滿足金屬另件的加工,車床成了關(guān)鍵性設(shè)備,18 世紀初車床的床身已是金屬制,結(jié)構(gòu)強度變大更適合做金屬切削,但因結(jié)構(gòu)簡單,只能做車削與螺旋方面的加工,到了 19 世紀才有完全以鐵制零件組合完成的車床,再加上諸如螺桿等傳動機構(gòu)的導入,一部具有基本功能的車床總算開發(fā)出來。但因動力只能靠人力、獸力或水力帶動,仍無法滿足需求,只能算是剛完成基本架構(gòu)的建構(gòu)。瓦特發(fā)明了蒸氣機,使得車床可藉由蒸氣產(chǎn)生動力用來驅(qū)動車床運轉(zhuǎn),此時車床的動力是集中一處,再藉由皮帶與齒輪的傳遞分散到工廠各處的車床,20 世紀初擁有獨立動力源的動力車床(Engine Lathe)終于被開發(fā),也將車床帶到新的領(lǐng)域。此期間拜福特公司大量生產(chǎn)汽車所賜,許多汽車零件必須以車床加工,為了確保零件供應(yīng)充足,供貨商必須大量采購車床才能應(yīng)付所需,即使到今天車床的發(fā)展仍受到汽車產(chǎn)業(yè)的榮枯所左右。1.3 本課題研究的內(nèi)容和設(shè)計思想2保證主軸支承軸頸的尺寸、形狀、位置精度和表面粗糙度,主軸前端內(nèi)、外錐面的形狀精度、表面粗糙度以及它們對支承軸頸的位置精度。主軸支承軸頸的尺寸精度、形狀精度以及表面粗糙度要求,可以采用精密磨削方法保證。磨削前應(yīng)提高精基準的精度。保證主軸前端內(nèi)、外錐面的形狀精度、表面粗糙度同樣應(yīng)采用精密磨削的方法。為了保證外錐面相對支承軸頸的位置精度,以及支承軸頸之間的位置精度,通常采用組合磨削法,在一次裝夾中加工這些表面。主軸加工中,為了保證各主要表面的相互位置精度,選擇定位基準時,應(yīng)遵循基準重合、基準統(tǒng)一和互為基準等重要原則,并能在一次裝夾中盡可能加工出較多的表面。由于主軸外圓表面的設(shè)計基準是主軸軸心線,根據(jù)基準重合的原則考慮應(yīng)選擇主軸兩端的頂尖孔作為精基準面。用頂尖孔定位,還能在一次裝夾中將許多外圓表面及其端面加工出來,有利于保證加工面間的位置精度。所以主軸在粗車之前應(yīng)先加工頂尖孔。為了保證支承軸頸與主軸內(nèi)錐面的同軸度要求,宜按互為基準的原則選擇基準面。如車小端 1∶20 錐孔和大端莫氏 6 號內(nèi)錐孔時, 以與前支承軸頸相鄰而它們又是用同一基準加工出來的外圓柱面為定位基準面(因支承軸頸系外錐面不便裝夾) ;在精車各外圓(包括兩個支承軸頸)時,以前、后錐孔內(nèi)所配錐堵的頂尖孔為定位基面;在粗磨莫氏 6 號內(nèi)錐孔時,又以兩圓柱面為定位基準面;粗、精磨兩個支承軸頸的 1∶12 錐面時,再次用錐堵頂尖孔定位;最后精磨莫氏 6 號錐孔時,直接以精磨后的前支承軸頸和另一圓柱面定位。定位基準每轉(zhuǎn)換一次,都使主軸的加工精度提高一步。對車床主軸的精確要求,就顯示出其加工過程中夾具的重要性。夾具的主要功能是裝夾工件,使工件在夾具中定位和夾緊。在機械加工中,使用機床夾具的目的主要有以下六個方面:1.保證加工精度;2.提高勞動生產(chǎn)率;3.改善工人勞動條件;4.降低生產(chǎn)成本;5.確保工藝紀律;6.夸大機床工藝范圍。設(shè)計夾具時,應(yīng)滿足下列四項要求:1.保證工件的加工精度要求;2.保證工人的操作方面安全;3.達到加工的生產(chǎn)率要求;4.滿足夾具一定的使用壽命和經(jīng)濟性要求。34第 2 章 零件的分析2.1 零件的作用CA6140 車床主軸是把旋轉(zhuǎn)運動及扭矩通過主軸端部的夾具傳遞給工件和刀具,要求有很高的強度及回轉(zhuǎn)精度,其結(jié)構(gòu)為空心階梯軸,外圓表面有花鍵、電鍵等功能槽及螺紋。2.1.1 支承軸頸主軸兩主支承軸頸 A、B 和 1:12 錐度與雙列向心短圓錐磙子軸承配合,并支承在主軸箱孔上是主軸部件的裝配基準。其圓度和同軸度將引起主軸回轉(zhuǎn)誤差,影響被加工工件的精度,必須嚴格控制。主支承軸頸圓跳動公差為 0.005mm,1:12 錐面接觸率 70%,表面粗糙度 Ra 為 0.4μm。?主軸中間輔助支承為單列滾子軸承,用以提高主軸剛性和回轉(zhuǎn)精度。其徑向圓跳動公差為 0.01mm;表面粗糙度 Ra 為 0.4μm。尺寸公差等級為 IT6。2.1.2 頭部錐孔主軸頭部莫氏 6 號錐孔是用來安裝夾具的定位面的??砂惭b頂尖,也可安裝刀具。其對支承軸頸 A、B 的圓跳動,近軸端公差為 0.005mm,離軸端 300 公差為0.01mm。錐面的接觸率≥70%表面粗糙度為 0.4μm,硬度要求 HRC52。主軸錐孔的軸線與支承軸頸線不重合,將使被加工工件產(chǎn)生相對位置誤差。2.1.3 頭部短錐主軸頭部短錐 C 和大臺階面 D 是安裝卡盤的定位面。其圓跳動為 0.008μm,表面粗糙度 Ra 為 0.8μm。頭部短錐 C 對支承軸頸的圓跳動將卡盤產(chǎn)生同軸度誤差。大臺階端面 D 對支承軸頸軸線跳動將卡盤產(chǎn)生垂直度誤差。2.1.4 裝配軸頸主軸上共安裝三個齒輪,其中一個空套,一個單鍵連接,另一個是花鍵連接。裝配軸頸對支承軸頸徑向圓跳動公差為 0.015mm~0.9mm。表面粗糙度 Ra 為0.4~0.6μm,尺寸公差等級為 IT5。裝配軸頸對支承軸頸的同軸度誤差,會引起主軸傳動齒輪嚙合不良,當主軸轉(zhuǎn)速很高時,還會影響齒輪的傳動平穩(wěn)性,產(chǎn)生噪生。加工工件時,會在工件表面產(chǎn)生重復(fù)出現(xiàn)的震紋,精加工是尤為明顯。52.1.5 軸向鎖緊主軸外圓上有三段螺紋,用于軸承等鈴部件的軸向鎖緊。當主軸螺紋的軸線與支承軸頸歪斜時,會引起主軸上瑣緊螺母端面傾斜,造成主軸內(nèi)圈軸線的同向傾斜,引起主軸的徑向跳動。因此,控制螺紋軸線與支承軸頸軸線的同軸度≤0.025mm。從上面分析看出:CA6140 車床主軸加工面較多,包括內(nèi)外圓、內(nèi)外錐、單鍵和花鍵、螺紋等,而且尺寸精度、性為精度以及表面粗糙度要求均較高,部分表面還需要表面淬火,但主要加工表面是以上五種,其中兩主支承軸頸本身的尺寸精度、形狀精度,兩支承之間的同軸度和主支承軸頸與其它表面相互位置精度以及表面粗糙度,則是主軸加工的關(guān)鍵。2.2 零件的工藝分析在擬定 CA6140 車床主軸工藝工藝過程時,應(yīng)考慮一些問題。2.2.1 加工階段的劃分加工過程大致劃分為四個階段: 頂尖孔之前是預(yù)加工階段;打頂尖孔之后至調(diào)質(zhì)前的工序為粗加工階段調(diào)質(zhì)處理后至表面淬火前的工序為半精加工階段;表面淬火后工序為精加工階段。要求較高的支承軸頸和莫氏 6 號錐孔的精加工,則應(yīng)在最后進行。整個主軸加工的工藝過程,是以主要表面(特別是支承軸頸)的加工為主線,穿插其它表面的加工工序組成的。這樣安排的優(yōu)點是:粗加工時切除大量金屬是產(chǎn)生的變形,可以在半精加工和精加工中去掉。而主要表面放在最后,可不受其它表面加工的影響,并方便安排熱處理工序,有利于機床的選擇。2.1.3 工序順序安排工序順序的安排主要根據(jù)基面先行、先粗后精、先主后次的原則,并注意下列幾點:主軸毛坯鍛造后,一般安排正火處理。其目的是,消除鍛造殘余應(yīng)力,改善金屬組織,降低硬度,改善切削加工性能。棒料毛坯可不進行該道熱處理工序。粗加工后,安排調(diào)質(zhì)處理。其目的是獲得均勻細致的索氏體組織,提高零件的綜合力學性能,以便在表面淬火時得到均勻致密的硬度層,并使硬化層的硬度由表面向中心逐漸降低。同時索氏體的金屬結(jié)構(gòu)經(jīng)加工后,表面粗糙度較細。最后,還須對有相對運動的軸頸表面和經(jīng)常與夾具接觸的錐面進行淬火或氮處理,以提高其耐磨性。一般高頻淬火安排在粗磨之前;氮化安排在粗磨之后,精磨之前。(一)外圓表面的加工順序6先加工大直徑外圓,以免一開始就降低工件剛度。(二)深孔加工應(yīng)安排在調(diào)質(zhì)以后進行,因為調(diào)質(zhì)處理變形大,深孔產(chǎn)生彎曲變形,不僅影響棒料通過,還會造成主軸高速轉(zhuǎn)動的不平衡。深孔加工應(yīng)安排在外圓粗車或半精車之后,以便有一個較精確的軸頸作定位基面,保證孔與外圓同軸度時主軸壁厚均勻。如果僅從定位基準考慮,希望始終用頂尖孔定位,避免使用錐堵,深孔加工安排在最后為好。但是深孔加工是粗加工,發(fā)熱量大,會破壞外圓加工的精度,而且鉆偏時,要有余量糾正。所以,深孔加工只能在半精加工階段進行。(三)次要表面的加工安排主軸上的花鍵、鍵槽等次要表面,一般都放在外圓精車時,由于斷續(xù)切削而產(chǎn)生振動,既影響加工質(zhì)量,又容易損壞刀具;同時也難以控制鍵槽的尺寸要求。但是,它們的加工也不宜放在主要表面精磨之后進行,以免銑花鍵產(chǎn)生的變形影響主要表面精度。主軸上的螺紋均有較高的要求,如安排在淬火前加工,淬火后產(chǎn)生的變形,會影響螺紋和支承軸頸的同軸度。因此,車螺紋宜放在主軸局部淬火之后進行。2.1.4 主軸錐孔的磨削主軸錐孔對主軸支承軸頸的圓跳動和錐孔與錐柄接觸率是機床的主要精度指標,因此錐孔磨削是主軸加工的關(guān)鍵之一。影響錐孔磨削精度的主要因素是定位基準、定位元件選擇的合理性和帶動工件旋轉(zhuǎn)的平穩(wěn)性。所以,加工 CA6140 主軸的關(guān)鍵是錐孔的加工,亦即加工錐孔是的夾具的設(shè)計。 2.3 本章小結(jié)本章主要介紹了主軸的作用,以及它在加工中的工藝分析。7第 3 章 工藝規(guī)程的設(shè)計3.1 主軸的材料、毛坯與熱處理3.1.1 主軸的毛坯主軸屬于外圓直徑相差較大的階梯軸,為了節(jié)省材料和減少加工的勞動量,毛坯常采用鍛件。在熱鍛過程中金屬纖維按軸向排列,組織細密,具有較高的抗拉、抗彎和抗扭強度。鍛件在鑄造方法上又分自由鍛和模鍛兩種。自由鍛使用的設(shè)備比較簡單,但毛坯的精度較低、余量大、生產(chǎn)率低,只適用于單件、小批生產(chǎn)。模鍛一般在模鍛壓力機上進行,設(shè)備比較昂貴,并須專用鍛模,但毛坯精度高、加工余量小、生產(chǎn)率高。目前國內(nèi)精鍛毛坯公差外徑可達±0.3mm,內(nèi)徑達±0.1mm,表面粗糙度 Ra 可達 3.2~1.6um。它適于在大批條件下鍛造形狀復(fù)雜、精度要求高的主軸。3.1.2 主軸的材料和熱處理根據(jù)主軸的功用,主軸應(yīng)具有良好的機械強度和剛度;主軸工作表面應(yīng)具有高的耐磨性與加工后尺寸精度的穩(wěn)定性。這些都與主軸的材料與所選用的熱處理方法有關(guān)。(一)主軸材料45 鋼是主軸常用的材料,價格較便宜。它經(jīng)過調(diào)質(zhì)(或正火) 、局部加熱淬火后回火,表面硬度 HRC45~ 52,一般能滿足普通機床要求。但與 65Mn、40Cr 等合金鋼比較,45 鋼淬透性差、淬火后變形大、加工后尺寸穩(wěn)定性差,故高精度主軸常用合金鋼。40Cr 是含碳量為 0.37%~0.45%的合金結(jié)構(gòu)鋼,經(jīng)調(diào)質(zhì)淬火后具有較高的綜合機械性能。38CrMnAlA 是中碳合金氮化鋼,由于氮化溫度(540~550℃)比淬火溫度低,變形小。此材料硬度高(中心硬度大于 HRC28) ,并具有優(yōu)良的耐疲勞性能、尺寸穩(wěn)定性好,是制造高精度主軸的理想材料。(二)主軸熱處理1. 改善切削加工性能、消除鍛造殘余應(yīng)力的熱處理 主軸毛坯在鍛造過程中,若溫度過高,則將使金屬組織的晶粒粗大;若鍛造溫度過低,則造成組織不均勻和過大的殘余應(yīng)力,甚至出現(xiàn)裂紋。這兩種情況在主軸8鍛造過程中往往同時存在,致使主軸強度降低,并由于表面泠硬而不易切削。因此在粗加工前需進行熱處理,以改善切削性能,消除鍛造殘余應(yīng)力,細化晶粒,并使金屬組織均勻。通常采用退火或正火處理。2. 預(yù)備熱處理主軸在粗加工后,最終熱處理以前常進行預(yù)備熱處理,通常為調(diào)質(zhì)或正火。調(diào)質(zhì)處理是淬火后高溫回火(回火溫度為 500~ 650℃) ,調(diào)質(zhì)后可得到均勻細密的回火索氏體組織,使主軸獲得較高的強度和韌性等綜合機械性能。調(diào)質(zhì)時由于回火溫度高,故主軸容易變形并產(chǎn)生較多的氧化皮。3. 最終熱處理 主軸最終熱處理包括局部加熱淬火后回火(鉛浴爐加熱淬火、火焰加熱淬火、電感應(yīng)加熱淬火等) 、滲碳淬火、淡化等。其目的是在保持心部韌性的同時提高表面硬度,使主軸各工作表面獲得較高的耐磨性和抗疲勞強度,以保持主軸的工作精度和提高使用壽命。最終熱處理一般放在半精加工之后,因局部淬火后總會有些變形,故需在淬火后安排磨削加工工序以消除淬火變形。3.2 主軸加工工藝過程3.2.1 主軸加工的主要問題和工藝過程設(shè)計所應(yīng)采取的相應(yīng)措施主軸加工的主要問題是如何保持主軸支承軸頸的尺寸、形狀、位置精度和表面粗糙度,主軸前端內(nèi)、外錐面的形狀精度、表面粗糙度以及它們對支承軸頸的位置精度。主軸支承軸頸的尺寸精度、形狀精度以及表面粗糙度要求,可以采用精密磨削方法保證,磨前應(yīng)提高精基準的精度。保證主軸前端內(nèi)、外錐面的形狀精度、表面粗糙度同樣應(yīng)采用精密磨削的方法。為了保證外錐面相對支承軸頸的位置精度,以及支承軸頸之間的位置精度,通常采用組合磨削法,在一次裝夾中加工這些表面。主軸錐孔相對于支承軸頸的位置精度是靠采用支承軸頸 A、B 作為定位基準,而讓被加工主軸裝夾在磨床工作臺上(不是裝夾在磨床頭架主軸上)加工保證的。以支承軸頸作為定位基準加工內(nèi)錐面,符合“基準重合”原則。讓被加工主軸裝夾在磨床工作臺上而不裝夾在磨床頭架主軸上,可以避免磨床主軸回轉(zhuǎn)誤差對錐孔形狀精度的影響;因為磨床頭架主軸與被加工主軸零件只是柔性連接,磨床頭架主軸只起帶動工件回轉(zhuǎn)的作用,而工件的回轉(zhuǎn)軸心,則取決于定位基準面 A、B 與定位元件的精度。在精磨前端錐孔之前,應(yīng)使作為定位基準的支承軸頸 A、B 達到一定精度。主軸外圓表面的加工,應(yīng)該以頂尖孔作為統(tǒng)一的定位基準。如果主軸上有通孔,9一旦通孔加工完畢,就要用帶頂尖孔的工藝錐堵塞到主軸兩端孔中,讓錐堵的頂尖孔起附加定位基準的作用。既然工藝錐堵要起定位作用,所以工藝錐堵與主軸錐孔的配合質(zhì)量就十分重要了。隨著被加工主軸加工精度的逐步提高,也要相應(yīng)提高工藝錐堵的精度。主軸上的通孔,雖然加工精度要求不高,但深孔的加工比較困難,排屑方式都是不可忽視的問題。主軸深孔的加工屬于粗加工,應(yīng)安排在工藝過程的前部。3.2.2 主軸加工定位基準的選擇主軸加工中,為了保證各主要表面的相互位置精度,選擇定位基準時,應(yīng)遵循“基準重合”與“互為基準”的原則,并能在一次裝夾中盡可能加工出較多的表面。由于主軸外圓表面的設(shè)計基準主軸軸心線,根據(jù)基準重合的原則考慮選擇主軸兩端的頂尖孔作為精基準面。用頂尖孔定位,還能在一次裝夾中把許多外圓表面及其端面加工出來,有利于保證加工面間的位置精度。所以實心軸在粗加工之前先打頂尖孔。對于空心軸則以外圓定位,加工通孔,并在兩端孔口加工出 60 度倒角或內(nèi)錐孔(工藝錐面) ,用兩個帶頂尖孔的錐堵或帶錐堵的心軸裝夾工件。為了保證支承軸頸與主軸內(nèi)錐面的同軸度要求,宜按“互為基準”的原則選擇基準面。例如車小端 1:20 錐孔和大端莫氏 6 號內(nèi)錐孔時,以與前支承軸頸相鄰而它們又是用同一基準加工出來的外圓柱面為定位基準面(因支承軸頸系外錐面不便裝夾) ;在精車各外圓(包括兩個支承軸頸)時,以前、后錐孔內(nèi)所配錐堵的頂尖孔為定位基面;在粗磨莫氏 6 號內(nèi)錐孔時,又以兩圓柱面為定位基準面;粗、精磨兩個支承軸頸的 1:12 錐面時,再次用錐堵頂尖孔定位;最后精磨莫氏 6 號內(nèi)錐孔時,直接以精莫后的前支承軸頸和另一圓柱面定位。定位基準每轉(zhuǎn)換一次,都使主軸的加工精度提高一步。3.2.3 主軸主要加工表面加工工序的安排要達到高精度要求,在機械加工工序中間尚需插入必要的熱處理工序,這就決定了主軸加工各主要表面總是循著以下順序進行的,即粗車 調(diào)質(zhì)(預(yù)備熱處理)?半精車 精車 淬火(最終熱處理) 粗磨 精磨。?主軸加工工藝過程可劃分為三個加工階段,即粗加工階段(包括銑端面打頂尖孔、粗車外圓等) ;半精加工階段(半精車外圓,鉆通孔,車錐面、錐孔,鉆大頭端面各孔,精車外圓等) ;精加工階段(包括精銑鍵槽,粗、精磨外圓、錐面、錐孔等) 。車床主軸主軸表面的加工順序有如下幾種方案:(一) 通孔 (以毛坯外圓定位,加工后配錐堵) 外圓表面粗加工(以錐堵頂尖孔定位) 錐孔粗加工(以半精加工后外圓定位,加工后配錐堵) 外圓精加?10工(以錐堵頂尖孔定位) 錐孔粗加工以精加工后的外圓定位) 。?(二)圓表面粗加工(以頂尖孔定位) 外圓表面半精加工(以頂尖孔定位)鉆通孔(以半精加工后外圓定位,加工后配錐堵) 外圓表面精加(以錐堵頂尖??孔定位) 錐孔粗加工(以精加工后外圓表面定位) 錐孔精加工(以精加工后外圓表面定位) 。(三)外圓表面粗加工(以頂尖孔定位) 外圓表面半精加工(以頂尖孔定位)鉆通孔(以半精加工后外圓表面定位) 錐孔粗加工(以精加工后外圓表面定位)錐孔精加工(以精加工后外圓表面定位,加工后配錐堵) 外圓表面精加(以錐堵頂尖孔定位)(四)外圓表面粗加工(以頂尖孔定位) 外圓表面半精加工(以頂尖孔定位)?鉆通孔(以半精加工后外圓表面定位) 錐孔粗加工(以精加工后外圓表面定位,?加工后配錐堵) 外圓表面精加(以錐堵頂尖孔定位) 錐孔精加工(以精加工外圓表面定位) 。上述四種加工方案各有優(yōu)缺點,現(xiàn)簡要分析如下:方案 1:鉆通孔放在外圓表面粗加工之前,則需在鉆通孔后增加配錐堵的工作;另外,粗加工外圓表面時,加工余量大,切削力、夾緊力也相應(yīng)較大,所以用錐堵頂尖孔定位不如用實心軸頂尖孔定位穩(wěn)定可靠。故此方案對毛坯是實心軸的情況則不適宜,對于實心軸在成批生產(chǎn)情況下是可行的。方案 2:錐孔粗加工在外圓表面精加工之后,錐孔粗加工時以精加工外圓表面定位,會破壞外圓表面的精度,故此方案不可行。方案 3:錐孔精加工放在外圓精加工前,錐孔精加工時以半精加工 外圓表面定位,這會影響錐孔加工精度(內(nèi)孔磨削條件比外圓磨削條件差) ;另外精加工外圓時以錐堵頂尖孔定位,有可能破壞錐孔精度,同時錐堵的加工誤差還會使外圓表面和內(nèi)錐表面產(chǎn)生較大的同軸誤差,故此方案也不行。方案 4:錐孔精加工方在外圓精加工之后,錐孔精加工時以精加工過的外圓定位,錐孔精加工工序的加工余量小,磨削力不大,故不會破壞外圓表面的精度。此外,以外圓表面定位,定位穩(wěn)定可靠,相比之下此方案最佳。當主要表面加工順序確定后,就要合理地插入非主要表面加工工序。對主軸來說非主要表面指的是螺孔、鍵槽、螺紋等。這些表面的加工一般不易出現(xiàn)廢品,所以盡量安排在后邊進行,主要表面加工一旦出了廢品,非主要表面就不需要加工了,這樣可以避免工時的浪費。但是也不能放在最后,以防在加工非主要表面過程中損害已精加工過程的主要表11面。對凡是需要在淬硬表面上加工的螺孔、鍵槽等,都應(yīng)安排在淬火前加工完畢,否則表面淬硬后就不易加工。在非淬硬表面上的螺孔、鍵槽等一般在外圓精車之后精磨之前進行。如果在精車之前就加工出這些表面,精車就將在斷續(xù)表面上進行,容易產(chǎn)生震動,影響表面質(zhì)量,還容易損壞車刀,加工精度也難以保證。至于主軸螺紋,因它與主軸支承軸頸之間有一定的同軸度要求,所以螺紋應(yīng)安排在最終熱處理之后的精加工階段進行,這樣半精加工后殘余應(yīng)力重新分布所引起變形和熱處理后的變形,就不會影響螺紋的加工精度了。檢驗工序的合理安排是保證產(chǎn)品質(zhì)量的重要措施。每道工序除操作者自檢外,還必須安排單獨的檢驗工序。一般在粗加工結(jié)束后安排檢驗工序以檢查主軸是否出現(xiàn)氣孔、裂紋等毛坯缺陷。對重要工序前后安排檢驗工序,以便及時發(fā)現(xiàn)廢品。在主軸從一個車間到另 一個車間時要安排檢驗工序,使后續(xù)車間內(nèi)產(chǎn)生的廢品不致誤認為是前車間產(chǎn)生的。在主軸全部加工結(jié)束之后要經(jīng)全面檢驗方可入庫。3.2.4 各工序工步的排序工序 1 銑端面打中心孔安裝 1:工步 1 粗銑右端面,保證尺寸 486 mm;工步 2 打中心孔。01?安裝 2:工步 1 粗銑左端面,保證總尺寸 874 mm;工步 2 打中心孔。工序 2 粗車外圓3.3 本章小結(jié)本章主要介紹主軸材料的前期處理以及在加工過程中采取的措施和相應(yīng)的加工工序。12第 4 章 機械加工余量、工序尺寸及毛坯尺寸的確定4.1 各工序工步的加工余量的計算CA6140 主軸零件材料為 45 鋼 HBS207~241,生產(chǎn)類型為小批生產(chǎn),采用摸鍛毛坯。根據(jù)上述原始資料及加工工藝,分別確定各加工表面的機械加工余量、工序尺寸及毛坯尺寸如下:1.加工大端莫氏 6 號錐孔精磨:大端為 ?63.348mm 的錐孔查參考文獻[1]表 5.22 確定余量為0.010~0.040mm。則,63.348-0.010=63.338mm;63.348-0.04=63.308mm。即 粗車后的直徑為 ?63.308~63.338mm,取 ?63.3mm粗磨:?63.3mm 查表 5.44 確定余量為 0.40~0.55mm 則 63.3-0.4=62.9mm;63.3-0.55=62.7mm。即 精車后的直徑為 ?62.75~62.9mm,根據(jù)表 5.32 取 ?62.898mm 按照精度等級 H12 其公差為 mm01?2.加工錐孔 ? mm.256精車:? mm 查表 5.32 精車后的直徑為 ?55.6 ~?55.45mm 按照 H11 公差0.?等級其公差為 。.13.加工 1:12 外錐精磨:大端 ?77.5mm,小端 ?75.2 5mm。表 5.22,零件基本尺寸 50~80mm,直徑余量 2Z=0.008~0.012mm 。則,77.2+0.008=77.508mm;77.5+0.012=77.512mm。取 ?75.5mm。75.25+0.008=75.258mm;75.25+0.012=75.262 。取 ?75.35mm。即 m粗磨后的直徑為大端 ?75.5mm,小端 ?75.35mm。粗磨 1:20 外圓:大端 ?75.5mm,小端 ?75.35mm。查[1]表 5.15 零件基本尺寸50~80mm 折算長度 200mm。磨削余量 0.25mm 則,?77.5+0.25=77.75mm;75.35+0.25=75.55mm 即 精車后的直徑尺寸為大端 77.75mm,小端 75.55mm。精車:根據(jù)表 5.21,直徑 100mm,加工余量為 0.2mm。則,77.5-?0.2=77.55mm;75.55-0.2=75.53mm。即粗車后的直徑大端為 ?77.55mm,小端?75.53mm半精車:查表 5.14 半精車余量為 2.0mm。則,大端 77.55+2.0=79.55mm 即粗車前的最小直徑為 79.55mm13粗車:查表 5.21,加工余量 2Z=2.8mm。則 79.55+2.8=82.35mm 即粗車前毛坯的最小直徑為 82.35mm。4.加工 1:12 外錐,小端 ?105.25mm,大端 ?108.5mm精磨:查表 5.22 知,直徑在 80~120mm,直徑余量為 0.010~0.014mm 則105.25+0.010=105.260mm,105.25+0.014=105.264mm,108.5+0.010=108.51mm,108.25+0.014=108.514mm 即粗磨后的直徑為大端為 ?108.6mm,小端為 ?105.3mm粗磨:根據(jù)表 5.15 查得粗磨余量為 0.30mm 則105.3+0.30=105.60mm,108.6+0.30=108.9mm 即粗磨后的直徑為大端 108.9mm,小端105.6mm精車:查表 5.21 知得精車余量為 0.50mm 則108.9+0.5=109.4mm,105.6+0.5=106.1mm 即半精車后的短錐直徑大端直徑為109.4mm,小端為 106.1mm半精車:根據(jù) 5.14 查得直徑為 80~120mm 且折算長度200~400mm 知其余量2.0mm 則 109.4+2.0=111.40mm,106.1+2.0=108.1mm 即粗車后的直徑為,大端?111.40mm,?108 mm粗車:由表 5.14 知粗車余量為 2.8mm 即粗車前毛坯的最小直徑為110.4+2.8=113.7mm5 .加工 短錐,大端為 106.373 mm730?。 0.13?精磨:按照表 5.22 直徑在 80~120mm 時直徑余量是 0.010~0.014mm 則106.373+0.010=106.383mm,106.373+0.014=106.387mm 取 ?106.4 mm 。即粗磨后0.13?的直徑為 ?106.4 mm。0.13?粗磨:查表 5.15 知粗磨的余量為 0.30mm 則 106.4+0.50=106.90 ,公差等級為mH11 即精車后的直徑為 106.9 mm0.1?精車:查表 5.21,基本尺寸100mm 知直徑加工余量為 0.5mm 則,106.9+0.5=107.4mm,取 107.5mm。且公差等級為 H11 即半精車后的尺寸為107.5 mm0.2?半精車:由表 5.14 查得直徑半精車余量為 2.0mm 則 107.5+2.0=109.5mm 即粗車后的直徑為 ?109.5mm粗車: 根據(jù)表 5.14 知粗車余量是 2.8mm 則, 109.5+2.8=112.3mm 即粗車前毛坯的最小直徑為 112.3mm6.精磨外圓設(shè)計尺寸為 ?70 mm0.13?14精磨: 按照表 5.22 直徑在 80~120mm 時直徑余量是 0.008~0.012m 即粗磨后的直徑為 ?70 mm。粗磨 :查表 5.15 知粗磨的余量為 0.50mm 則,70+0.50=70.5mm 直02.8?徑偏差為 0~0.046mm 即精車后的直徑為 70.5 mm046.?精車:查表 5.21,基本尺寸100 mm 知直徑加工余量為 0.5mm 則, 70.5+0.5=71mm即半精車后的尺寸為 71mm半精車:由表 5.14 查得直徑半精車余量為 2.0mm 則, 71+2.0=73mm 即 粗車后的直徑為 ?73mm粗車: 根據(jù)表 5.14 知粗車余量是 2.8mm 則, 73+2.8=76.3mm 即粗車前毛坯的最小直徑為 75.8mm7.精磨 ?75 mm0.13?精磨: 按照表 5.20 直徑余量是 0.15mm 則,75+0.15=75.15mm 即粗磨后的直徑為75.15mm粗磨:查表 5.15 知粗磨的余量為 0.30mm 則 75.15+0.30=75.45mm,取 75.5mm 即精車后的直徑為 75.5 mm,直徑偏差046.?041.精車: 查表 5.21,基本尺寸100mm 知直徑加工余量為 0.8mm 則75.5+0.80=76.3mm 即半精車后的尺寸為 76.3mm半精車:由表 5.14 查得直徑半精車余量為 2.0mm 則 76.3+2.0=78.3mm 即粗車后的直徑為 ?78.3粗車: 根據(jù)表 5.14 知粗車余量是 2.8mm 則 78.3+2.8=81.1mm 即粗車前毛坯的最小直徑為 81.8mm8.精磨 ?80 mm0.13?精磨: 按照表 5.20 直徑余量是 0.15mm 則,80+0.15=80.15mm 即粗磨后的直徑為80.1mm粗磨:查表 5.15 知粗磨的余量為 0.30mm 則 80.1+0.30=80.40mm,取 80.5mm 直徑偏差 0~0.0540mm 即精車后的直徑為 75.5 mm,直徑偏差046.?041.精車:查表 5.21,基本尺寸100mm 知直徑加工余量為 0.8mm 則 80.5+0.80=81.3mm即半精車后的尺寸為 81.3mm半精車:由表 5.14 查得直徑半精車余量為 2.0mm 則 81.3+2.0=83.3mm,即粗車后的直徑為 ?83.3mm粗車: 根據(jù)表 5.14 知粗車余量是 2.8mm 則 83.3+2.8=96.1mm 即粗車前毛坯的最小直徑為 96.1mm159.精磨 ?89 mm036.51?精磨: 按照表 5.20 直徑余量是 0.15mm 則 89+0.15=89.15 mm 直徑偏差為 即015.?粗磨后的直徑為 89.15mm粗磨: 查表 5.15 知粗磨的余量為 0.40mm 則 89.15+0.40=89.50mm,直徑偏差0~0.0540mm 即精車后的直徑為 89.5mm精車: 查表 5.21,基本尺寸100mm 知直徑加工余量 0.8m,則 89.5+0.75=90.25mm,直徑偏差 ,即半精車后的尺寸為 90.25mm15.0?半精車:由表 5.14 查得直徑半精車余量為 2.0m 則 90.25+2.0=92.25mm 即粗車后的直徑為 ?92.25mm粗車: 根據(jù)表 5.14 知粗車余量是 2.8mm 則 92.25+2.8=95.05mm 即粗車前毛坯的最小直徑為 95.05mm(10) 精磨 ?90 mm012.7?精磨:按照表 5.20,直徑余量是 0.015mm 則 90+0.015=90.15mm,且直徑偏差為mm。即粗磨后的直徑為 90.15mm。05.?粗磨:查表 5.15 知粗磨的余量為 0.40mm 則 90.1+0.40=90.5mm, 直徑偏差為即精車后的直徑為 90.5mm054.?精車:查表 5.21,基本尺寸100mm 知直徑加工余量為 0.75mm 則 90.5+0.8=91.3mm, 且直徑偏差為 即半精車后的尺寸為 91.3mm。15.0?半精車:由表 5.14 查得直徑半精車余量為 2.0m 則,91.25+2.0=109.5mm 即粗車后的直徑為 ?109.5mm。粗車:根據(jù)表 5.14 知粗車余量是 2.8mm 則 109.5+2.8=112.3mm 即粗車前毛坯的最小直徑為 112.3mm。(11)精磨外圓 ?105 mm0.12?精磨:按照表 5.22 直徑余量是 0.015mm 則 105+0.15=105.15mm, 直徑偏差為即粗磨后的直徑為 ?105.15mm。0.5?粗磨:查表 5.15 知粗磨的余量為 0.40mm 則 105.1+0.40=105.15mm, 直徑偏差為即精車后的直徑為 105.15mm。0.51?精車:查表 5.21,基本尺寸100mm 知直徑加工余量為 0.75mm;則105.5+0.75=106.25mm, 直徑偏差為 即半精車后的尺寸為 106.25 mm。0.15? 0.15?半精車:由表 5.14 查得直徑半精車余量為 2.0mm;則 10.25+2.0=108.25mm 即粗車16后的直徑為 ?109.5mm。粗車:根據(jù)表 5.14 知粗車余量是 2.8mm 則 108.25+2.8=110.05mm 即粗車前毛坯的最小直徑為 110.05mm。(12)車螺紋:M74 1.5g 由表 5.58 查得車螺紋前軸的直徑為 ?74,螺距?p=1.5mm,內(nèi)徑為 d=73.376mm。精車:查表 5.21 直徑余量為 1.25mm 則 74+1.25=75.25mm 即半精車后直徑?75.25mm。半精車:查表 5.14 直徑余量為 2.0mm 則 75.25+2.0=77.25mm 即粗車后直徑?77.25mm。粗車:根據(jù)表 5.14 知粗車余量是 2.5mm 則 77.25+2.5=79.25mm 即粗車前毛坯的最小直徑為 79.25mm。(13)車螺紋:M105 1.5g 由表 5.58 查得車螺紋前軸的直徑為 ?105mm,螺距?為 p=1.5mm,內(nèi)徑為 d=103.335mm。精車:查表 5.21 直徑余量為 1.25mm 則 105+1.25=106.25mm 即半精車后直徑?106.25mm。半精車:查表 5.14 直徑余量為 2.0mm 則 106.25+2.0=108.25mm 即粗車后直徑?108.25mm。粗車:根據(jù)表 5.14 知粗車余量是 2.8mm 則 108.25+2.8=110.03mm 即粗車前毛坯的最小直徑為 110.03mm。(14)車螺紋:M1151 5g 由表 5.58 查得車螺紋前軸的直徑 ?115mm,螺距為?p=1.5mm,內(nèi)徑為 d=113.335mm精車:查表 5.21 直徑余量為 1.25mm 則 115+1.25=116.25mm 即半精車后直徑?106.25mm。半精車:查表 5.14 直徑余量為 1.8mm 則 116.25+1.8=108.05mm 即粗車后直徑?108.05mm。粗車:根據(jù)表 5.14 知粗車余量是 2.0mm 則 108.25+2.0=110.25mm 即粗車前毛坯的最小直徑為 110.25mm。(15)粗精銑鍵槽粗銑鍵槽:查表 5.29 知槽寬 B〈10mm 則加工余量 2Z=1mm,Z=0.5mm,公差為 0.20mm。精銑鍵槽:查表 5.29 知槽寬 B〈10mm 則加工余量 2Z=0.3mm,Z=0.15mm,公差為 0.10mm。17(16)粗精銑花鍵(17)精車 ?69.5mm 長 4mm 的外圓粗銑花鍵:加工余量為 1.0-1.2mm精銑花鍵:根據(jù)參考文獻[20]知,加工余量為 0.8-1.0mm精車:查表 5-21 得 2Z=0.2mm,Z=0.1mm 則 69.5+0.2=69.7mm 即半精車后直徑為 69.7mm半精車:查表 5.14 2Z=2.0mm 則 69.7+2.0=71.7mm 即粗車前的直徑為 71.7mm粗車:查表 5.14 2Z=2.5mm 則 71.2+2.5=73.5mm 即粗車前最小直徑為 73.5mm(18)精車 ?73.5mm 長 4mm 的外圓精車:查表 5.21 得 2Z=0.2mm ,Z=0.1mm 則 73.5+0.2=73.7mm 即半精車后直徑為 73.7mm半精車:查表 5.14 2Z=2.0mm 則 73.7+2.0=75.7mm 即粗車前的直徑為 75.7mm粗車:查表 5.14 2Z=2.5mm 則 75.7+2.5=78.2mm 即粗車前最小直徑為 78.2mm(19)精車 ?74.5mm 長 4mm 的外圓精車:查參考文獻[1]表 5.21 得 2Z=0.2mm,Z=0.1mm 則 74.5+0.2=74.7mm 即半精車后直徑為 74.7mm半精車:查表 5.14 2Z=2.0mm 則 74.7+2.0=75.7mm 即粗車前的直徑為 76.7mm粗車:查表 5.14 2Z=2.5mm 則 76.7+2.5=79.2mm 即粗車前最小直徑為 79.2mm(20)精車 ?80mm 長 3.5mm 的外圓精車:查表 5.21 得 2Z=0.2mm,Z=0.1mm 則 80+0.2=80.2mm 即半精車后直徑為80.2mm半精車:查表 5.14 2Z=2.0mm 則 80.2+2.0=82.2mm 即粗車前的直徑為 82.2mm粗車:查表 5.14 2Z=2.5mm 則 82.2+2.5=84.7mm 即粗車前最小直徑為 84.7mm(21)精車 ?76.5mm 長 3mm 的外圓精車:查表 5.21 得 2Z=0.2mm, Z=0.1mm 則 76.5+0.2=76.7mm 即半精車后直徑為 76.7mm半精車:查表 5.14 2Z=2.0mm 則 76.7+2.0=78.7mm 即粗車前的直徑為 78.7mm粗車:查表 5.14 2Z=2.5mm 則 78.7+2.5=81.2mm 即粗車前最小直徑為 81.2mm(22)精車 ?79.5mm 長 3mm 的外圓精車:查表 5.21 得 2Z=0.2mm,Z=0.1mm 則 79.5+0.2=79.7mm 即半精車后直徑為 79.7mm半精車:查表 5.14 2Z=2.0mm 則 79.7+2.0=81.7mm 即粗車前的直徑為 81.7mm粗車:查表 5.14 2Z=2.5mm 則 81.7+2.5=84.2mm 即粗車前最小直徑為 84.2mm18(23)精車 ?86mm 長 3mm 的外圓精車:查表 5.21 得 2Z=0.2mm,Z=0.1mm 則 86+0.2=86.2mm 即半精車后直徑為86.2mm半精車:查表 5.14 2Z=2.0mm 則 86.2+2.0=88.2mm 即粗車前的直徑為 88.2mm粗車:查表 5.14 2Z=2.5mm 則 88.2+2.8=91mm 即粗車前最小直徑為 91mm(24)精車 ?89.5mm 長 4mm 的外圓精車:查表 5.21 得 2Z=0.2mm,Z=0.1mm 則 89.5+0.2=89.7mm 即半精車后直徑為 89.7mm半精車:查表 5.14 2Z=2.0mm 則 89.7+2.0=91.7mm 即粗車前的直徑為 91.7mm粗車:查表 5.14 2Z=2.8mm 則 91.7+2.8=94.5mm 即粗車前最小直徑為 94.5mm(25)精車 ?97.5 長 4mm 的外圓精車:查表 5.21 得 2Z=0.2mm,Z=0.1mm 則 97.5+0.2=87.7mm 即半精車后直徑為 97.7mm半精車:查表 5.14 2Z=2.0mm 則 97.7+2.0=99.7mm 即粗車前的直徑為 99.7mm粗車:查表 5.14 2Z=2.8mm 則 99.7+2.8=102.5mm 即粗車前最小直徑為 102.5mm(26)精車 ?103.5 長 4mm 的外圓精車:查表 5.21 得 2Z=0.3mm,Z=0.1mm 則 103.5+0.3=103.8mm 即半精車后直徑為 103.8mm半精車:查表 5.14 2Z=2.0mm 則 103.8+2.0=105.78mm 即粗車前的直徑為105.8mm粗車:查表 5.14 2Z=2.8mm 則 105.8+2.8=108.6mm 即粗車前最小直徑為 108.6mm(25)精車 ?104.5mm 長 4mm 的外圓精車:查表 5.21 得 2Z=0.3mm,Z=0.1mm 則 104.5+0.3=104.8mm 即半精車后直徑為 104.8mm半精車:查表 5.14 2Z=2.0mm 則 104.8+2.0=106.8mm 即粗車前的直徑為 106.8mm粗車:查表 5.14 2Z=2.8mm 則 106.8+2.8=109.6mm 即粗車前最小直徑為 109.6mm(27)精車 ?104.5mm 長 4mm 的外圓精車:查表 5.21 得 2Z=0.3mm,Z=0.1mm 則 104.5+0.3=104.8mm 即半精車后直徑為 104.8mm半精車:查表 5.14 2Z=2.0mm 則 104.8+2.0=106.8mm 即粗車前的直徑為 106.8mm粗車:查表 5.14 2Z=2.8mm 則 106.8+2.8=109.6mm 即粗車前最小直徑為 109.6mm(28)精車 ?112 長 4mm 的外圓精車:查表 5.21 得 2Z=0.3mm,Z=0.1mm 則 112+0.3=112.3mm 即半精車后直徑19為 112.3mm半精車:查表 5.14 2Z=2.0mm 則 112.3+2.0=114.3mm 即粗車前的直徑為 114.3mm粗車:查表 5.14 2Z=2.8mm 則 114.3+2.8=117.1mm 即粗車前最小直徑為 117.1mm(29)精車 ?120mm 長 4mm 的外圓精車:查表 5.21 得 2Z=0.3mm,Z=0.1mm 則 120+0.3=120.3mm 即半精車后直徑為 120.3mm半精車:查表 5.14 2Z=2.3mm 則 20.3+2.3=122.6mm 即粗車前的直徑為 122.6mm粗車:查表 5.14 2Z=2.8mm 則 122.6+2.8=125.4mm 即粗車前最小直徑為 125.4mm(30)精車 ?195mm 長 25mm 外圓精車:查表 5.21 得 2Z=mm,Z=0.1mm 則 195+0.3=195.3mm 即半精車后直徑為195.3mm半精車:查表 5.14 2Z=2.3mm 則 195.3+2.3=197.6mm 即粗車前的直徑為 197.6mm粗車:查表 5.14 2Z=2.8mm 則 197.6+2.8=200.4mm 即粗車前最小直徑為 200.4mm(31)鉆通孔 ?52mm查表 5.33 知鉆孔的直徑余量為 2mm(32)鉆 ?23mm 孔查表 5.30 知鉆孔:?21mm; 擴孔:?22.8mm; 鉸孔:?22.94mm;精鉸?23H7(33)鉆 ?6mm 孔查表 5.30 知鉆孔:?5.8mm; 精鉸 6H7(34)鉆 ?19.0mm 孔查表 5.30 知鉆孔:?18.85mm; 粗鉸:?18.94mm;精鉸 ?19H7(35)鉆 ?9mm 孔查表 5.30 知鉆孔:?8.8mm; 粗鉸:?8.96mm;精鉸 ?9H7(36)鉆、鉸 4H7 孔查表 5.30 知鉆孔:?3.7mm; 精鉸 ? 4H7(37)銑端面1)銑大端使大端短錐達到尺寸要求,根據(jù)表 5.47,查得銑削余量為 2.0mm2)銑大端使大端短錐達到尺寸要求,根據(jù)表 5.47,查得銑削余量為 1.5mm,即在加工前毛坯長度的最小尺寸為 877.5mm4.2 各工序工步的切削用量的計算工序 3 銑斷面打中心孔20加工材料:45 鋼正火、模鍛加工條件:銑斷面保證總體長度為 874 mm:刀具:高速鋼斷面銑刀01?確定斷面最大加工余量:一直毛坯長度方向的加工余量為 4 mm 考慮 7 度的模01?鍛拔模斜度,則毛坯長度方向的最大加工余量 Z=9.5mm,故,斷面最大加工余量可按 Z=5.5mm 考慮工步 1:銑削大端端面根據(jù)參考文獻[7]表 3.3 知 =0.08~0.15m/z,取 =0.10m/zzf zf切削速度:參考有關(guān)手冊,確定 =0.45m/s,即,27m/minf工序 4:車大端斷面工步 1:粗車大端 ?107.5 mm0.2?確定進給量 :根據(jù)參考文獻[1]表 10.9 刀桿尺寸為 16×25mm, 3mm。以f pa?及工件直徑 100mm 時 =1.8~2.0r/min。?f切削深度:余量 2Z=113-107.5=5.5mm,即單邊余量 Z=2.75mm,可一次切除。計算切削速度:見表 1.27= =56.8m/minvcxympkTaf?0.20.15.430.81.970467???(4.01)確定主軸轉(zhuǎn)速: = r/min (4.02)cswvnd??633.?按機床選取 所以實際切削速度230/ir= m/min (4.03)3.14ndv?7.5.6?切削工時: ,根據(jù)表 11.1, =2mm, =1mm12flt?1l2l所以 =0.041 (4.04)6.30t???min工步 2:粗車大端 ?197mm確定進給量 :根據(jù)表 10.9 刀桿尺寸為 16 25mm, 3mm。以及工件直徑f pa?100 時 =1.8~2.0mm/r 。?f切削深度:余量 2Z=2000-197=3mm,即單邊余量 Z=1.5mm,可一次切除。計算切削速度:見參考文獻[18]表 1.2721= =62.2