機(jī)械加式技術(shù)
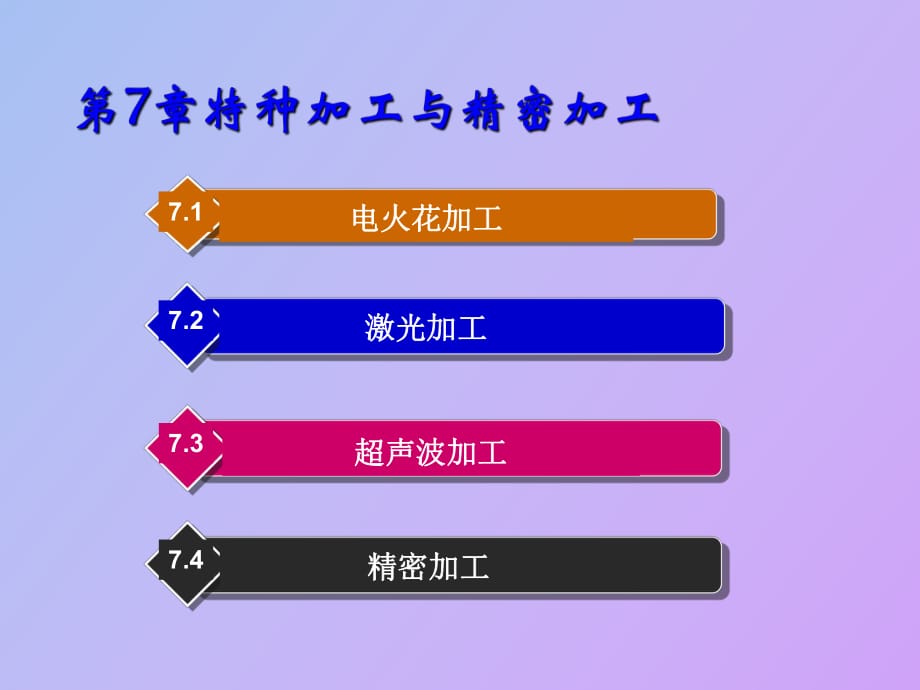


《機(jī)械加式技術(shù)》由會(huì)員分享,可在線閱讀,更多相關(guān)《機(jī)械加式技術(shù)(63頁珍藏版)》請(qǐng)?jiān)谘b配圖網(wǎng)上搜索。
1、電火花加工7.1激光加工7.2超聲波加工7.3精密加工7.4 電火花加工是在一定的介質(zhì)中,通過工具電極和工件電極之間脈沖放電的電蝕作用,對(duì)工件進(jìn)行加工的方法。從20世紀(jì)40年代開始對(duì)它進(jìn)行研究并逐步應(yīng)用于生產(chǎn)。初期的電火花加工由于放電頻率低,加工速度慢,電極損耗大,所以應(yīng)用范圍受到一定限制。隨著加工速度和電極損耗等加工特性的改善,而得到廣泛應(yīng)用。從1m大小的金屬模具到數(shù)微米的孔和槽都可以加工。 1電火花加工的基本原理如圖7-1所示,工具電極4與工件6一起置于介質(zhì)5(煤油或其他液體)中,并分別與脈沖電源1的負(fù)極和正極相連接。加工時(shí),送進(jìn)機(jī)構(gòu)2移動(dòng)工具電極使其逐漸趨近工件,當(dāng)工具電極與工件之間的間
2、隙小到一定程度時(shí),介質(zhì)被擊穿,在間隙中發(fā)生脈沖放電。放電的持續(xù)時(shí)間極短,只有108106s,而瞬時(shí)的電流密度極大,可達(dá)105107A/cm2,溫度可高達(dá)10 000以上,致使工件表面局部金屬材料被軟化、熔化甚至汽化。 在瞬時(shí)放電的爆炸力作用下,熔化、汽化了的金屬材料被拋入液體介質(zhì)冷凝成微小的顆粒,并從放電間隙中排除出去。每次放電即在工件表面形成一個(gè)微小的凹坑(稱為電蝕),連續(xù)不斷的脈沖放電,使工件表面不斷地被蝕除,因而逐漸完成加工要求。脈沖放電過程中,由間隙自動(dòng)調(diào)節(jié)器驅(qū)動(dòng)工具電極自動(dòng)進(jìn)給,保持其與工件的間隙,以維持持續(xù)的放電。 圖7.1 電火花加工原理1脈沖電源 2送進(jìn)機(jī)構(gòu)及間歇自動(dòng)調(diào)節(jié)器3床
3、身 4工具電極 5介質(zhì) 6工件 2電火花加工的特點(diǎn)(1)由于放電通道中電流密度很大,局部區(qū)域內(nèi)產(chǎn)生的高溫足以熔化甚至汽化任何導(dǎo)電材料,因此,利用電火花能加工各種具有導(dǎo)電性能的硬、脆、軟、韌材料。(2)加工時(shí)無切削力,適于加工小孔、薄壁、窄腔槽及各種復(fù)雜的型孔、型腔、曲線孔等,也適用于精密細(xì)微加工。 (3)加工時(shí),由于脈沖能量間斷地以極短的時(shí)間作用在工件上,整個(gè)工件幾乎不受熱的影響,有利于提高加工精度和加工表面質(zhì)量,也有利于加工熱敏感性強(qiáng)的材料。(4)便于實(shí)現(xiàn)加工過程自動(dòng)化。(5)電極(工具)消耗較大。 3電火花加工的應(yīng)用電火花加工的效率遠(yuǎn)比金屬切削加工低,因此,只有在難以進(jìn)行切削的情況下,如工
4、件形狀復(fù)雜、材料太硬等,才采用電火花加工。在工藝應(yīng)用上,電火花加工的常見形式如下。 (1)電火花成形加工包括穿孔和型腔加工兩類。電火花穿孔加工應(yīng)用最為廣泛,常用來加工沖裁模、復(fù)合模、級(jí)進(jìn)模等沖模的凹模和固定板、卸料板等零件的型孔,以及拉絲模、拉深模等零件的型孔。電火花型腔加工則常用于加工鍛模、壓鑄模、擠壓模、塑料壓模等模具型腔和葉片、整體式葉輪等復(fù)雜曲面零件。(2)電火花小孔加工可加工直徑為0.11mm、長徑比小于20的小孔,如噴嘴小孔、航空發(fā)動(dòng)機(jī)氣冷孔、輥筒、篩網(wǎng)上的小孔等。 (3)電火花精密細(xì)微加工一般指加工直徑小于0.1mm的孔或?qū)挾刃∮?.1 mm的槽。(4)電火花線電極切割(線切割)
5、,用于切割各種沖模和具有直紋面的零件,以及進(jìn)行下料、截割和窄縫加工。(5)電火花磨削平面、內(nèi)外圓、小孔等,如拉絲模、擠壓模、微型軸承內(nèi)環(huán)、偏心鉆套等。(6)電火花螺紋加工適用于加工螺紋環(huán)規(guī)和螺紋加工工具。 激光加工是指利用功率密度極高的激光束照射工件的被加工部位,使其材料瞬間熔化或蒸發(fā),并在沖擊波作用下,將熔融物質(zhì)噴射出去,從而對(duì)工件進(jìn)行穿孔、蝕刻、切割,或采用較小能量密度,使加工區(qū)域材料熔融黏合,對(duì)工件進(jìn)行焊接的一種加工方法。激光加工中常用的激光器有固體激光器和氣體激光器兩類。 1激光加工的基本原理激光加工的原理如圖7.3所示。固體激光器由激光工作物質(zhì)2(一般采用紅寶石或摻釹離子的釔鋁石榴石
6、)、激勵(lì)光源3(一般用脈沖氙燈)、全反射鏡1和部分反射鏡4構(gòu)成的光諧振腔組成。當(dāng)工作物質(zhì)被激勵(lì)光源照射時(shí),在一定條件下可使工作物質(zhì)中亞穩(wěn)態(tài)粒子數(shù)反轉(zhuǎn),引起受激輻射,形成光放大,并通過光諧振腔的作用產(chǎn)生光的振蕩,由部分反射鏡輸出激光,經(jīng)透鏡5聚焦到工件6的待加工表面,從而實(shí)現(xiàn)對(duì)工件的加工。 圖7.3 固體激光器加工原理圖1全反射鏡 2激光工作物質(zhì) 3激勵(lì)光源 4部分反射鏡 5透鏡 6工件 2激光加工的特點(diǎn)(1)加工范圍廣。激光的功率密度很高(可達(dá)1071010W/cm2),幾乎能加工所有材料,包括用普通方法難以加工的硬度高、脆性大、熔點(diǎn)高的金屬材料,以及陶瓷、金剛石、石英、寶石等非金屬材料。(2
7、)生產(chǎn)率高。激光加熱速度快,生產(chǎn)效率高,打一個(gè)小孔一般只需0.01s左右,特別是對(duì)金剛石、寶石等特硬材料,打孔時(shí)間不足切削加工的1%。由于加熱局限在很小的范圍,所以熱影響區(qū)小,工件熱變形小。 (3)無須工具。激光加工屬于非接觸加工,不需要工具,無切削加工的受力變形。(4)能加工細(xì)微小孔、窄縫。激光能聚焦成極細(xì)的光束,可以加工直徑為10.01mm的小孔和窄縫。(5)可控性好。激光束調(diào)制方便,易于實(shí)現(xiàn)計(jì)算機(jī)數(shù)字控制和自動(dòng)化加工。 3激光加工的應(yīng)用(1)激光打孔。激光打孔是激光加工在機(jī)械制造中最主要的應(yīng)用,多用于小孔、窄縫的細(xì)微加工,孔徑可小至0.005mm,孔深與孔徑之比可達(dá)5以上。對(duì)與工件表面成
8、各種角度(1590)的傾斜小孔、薄壁零件及復(fù)合材料零件上的小孔、難加工材料上的小孔等,用激光打孔更具優(yōu)越性。目前,激光打孔已廣泛應(yīng)用于金剛石拉絲模、鐘表寶石軸承、化學(xué)纖維硬質(zhì)合金噴絲板、火箭發(fā)動(dòng)機(jī)和柴油機(jī)的噴嘴、渦輪葉片、集成電路陶瓷襯套、手術(shù)用針等零件或產(chǎn)品的小孔加工。 (2)激光切割。利用激光束聚焦后極高的功率密度,可切割任何難加工的高熔點(diǎn)材料、高溫材料、高強(qiáng)度硬脆材料,如鈦合金、鎳合金、不銹鋼,以及各種非金屬材料。激光切割為非接觸切割,工件變形極??;切縫狹窄(一般為0.10.2mm)且切口質(zhì)量優(yōu)良;切割速度高。激光切割大多采用CO2激光器及同軸吹氣工藝(沿激光束的同軸方向吹送輔助氣體,如
9、氧、氮、二氧化碳、氬、壓縮空氣等),以提高切割效率和改善切口質(zhì)量。激光切割多用于半導(dǎo)體硅片切割、型孔加工、精密零件的窄縫切割、刻線、雕刻等。 (3)激光焊接。激光焊接主要用于高熔點(diǎn)材料和快速氧化材料及異種材料的焊接。由于激光能透過玻璃等透明物體進(jìn)行焊接,因此,可用于真空儀器元件的焊接。激光焊接分脈沖激光焊接(采用紅寶石激光器和釹玻璃激光器)和連續(xù)激光焊接(采用CO2激光器和釔鋁石榴石激光器)兩種,前者適用于點(diǎn)焊,后者適用于縫焊。 超聲波加工是利用產(chǎn)生超聲振動(dòng)的工具,帶動(dòng)工件和工具間的磨料懸浮液,沖擊和拋磨工件的被加工部位,使其局部材料破壞而成粉末,以進(jìn)行穿孔、切割和研磨等的加工方法。超聲加工不
10、僅能加工高熔點(diǎn)的硬質(zhì)合金、脆火鋼等脆硬合金材料,而且更適合于加工玻璃、陶瓷、半導(dǎo)體鍺和硅片等不導(dǎo)電的非金屬脆硬材料,同時(shí)還可用于清洗、焊接和探傷等。 1超聲波加工的基本原理超聲波的加工原理如圖7.4所示。工具4的超聲頻振動(dòng)是通過超聲換能器1在高頻電源作用下產(chǎn)生的高頻機(jī)械振動(dòng),經(jīng)變幅桿2使工具沿軸線方向作高速振動(dòng)。工具的超聲頻振動(dòng),除了使磨粒獲得高頻撞擊和拋磨作用外,還可使工作液受工具端部的超聲振動(dòng)作用而產(chǎn)生高頻、交變的液壓正負(fù)沖擊波。正沖擊波迫使工作液鉆入被加工材料的細(xì)微裂縫處,加強(qiáng)機(jī)械破壞作用;負(fù)沖擊波造成局部真空,形成液體空腔,液體空穴閉合時(shí)又產(chǎn)生很強(qiáng)的爆裂現(xiàn)象,而強(qiáng)化加工過程,從而逐步地
11、在工件上加工出與工具斷面形狀相似的孔穴。 圖7.4 超聲波加工原理圖1超聲換能器 2變幅桿 3磨料懸浮液 4工具 5工件 2超聲波加工的特點(diǎn)(1)超聲波主要適于加工各種硬脆材料,如玻璃、石英、陶瓷(氧化鋁、氧化硅等)、硅、鍺、瑪瑙、寶石、金剛石等。對(duì)于質(zhì)硬的金屬材料如淬火鋼、硬質(zhì)合金等也能加工,但生產(chǎn)率較低。 (2)能加工各種形狀復(fù)雜的型孔、型腔、成形表面等。采用中空形狀的工具還可以實(shí)現(xiàn)各種形狀的套料加工。(3)加工過程中,工具對(duì)工件的宏觀作用力小,熱影響小,適于加工不能承受較大機(jī)械應(yīng)力的薄壁、薄片等零件。(4)超聲波加工的生產(chǎn)率低于電火花加工,但加工精度高,表面粗糙度值小。 3超聲波加工的應(yīng)
12、用(1)型孔、型腔加工工具的形狀和尺寸,取決于被加工面的形狀和尺寸。加工孔徑范圍為0.190mm,深度可達(dá)200mm。(2)超聲波切割加工主要用于切割脆硬的半導(dǎo)體材料。(3)超聲波焊接用于焊接尼龍、塑料以及表面易生成氧化膜的鋁制品等。此外,還可在陶瓷等非金屬表面掛錫、掛銀和涂熔化的金屬薄層。 (4)超聲波復(fù)合加工與電解復(fù)合加工小孔、深孔可大大提高加工速度與加工質(zhì)量;在切削加工中引入超聲振動(dòng)(如對(duì)耐熱鋼等硬韌材料進(jìn)行車削、鉆孔、攻螺紋),可降低切削力,改善表面質(zhì)量,提高加工速度和延長刀具壽命。(5)超聲波清洗。 7.4.1 精密加工的概念7.4.2 精密車削7.4.3 精密磨削7.4.4 光整加
13、工 精密加工的實(shí)施及其加工質(zhì)量的保證,受工件材料的特性、精密加工時(shí)基準(zhǔn)面的精度、技術(shù)設(shè)施(機(jī)床、刀具、技術(shù)測量手段)、環(huán)境條件及工人技術(shù)水平等諸多因素的制約。而機(jī)床設(shè)備和環(huán)境條件是精密加工的兩項(xiàng)最基本的條件。 1機(jī)床設(shè)備條件精密加工必須在精密機(jī)床上進(jìn)行。機(jī)床應(yīng)具有高的運(yùn)動(dòng)精度、剛度和轉(zhuǎn)速,以及小的進(jìn)給量。2環(huán)境條件(1)消除工藝系統(tǒng)內(nèi)部和外部的振動(dòng)干擾。加工表面的表面粗糙度與振動(dòng)的頻率和振幅有關(guān)。(2)創(chuàng)造恒溫條件。精密機(jī)床應(yīng)置在恒溫室內(nèi),應(yīng)在201的條件下對(duì)零件進(jìn)行加工和測量。超精密加工還要求工作間超凈。 加工外圓表面時(shí),用很小的刃口圓弧半徑的車刀進(jìn)行高速、微量切削而獲得高精度的工藝方法稱為
14、精密車削。 1精密車削的應(yīng)用精密車削主要用于銅、鋁及其合金制件的最終加工,其他如純金屬、塑料、玻璃纖維、合成樹脂及石墨等不宜采用磨削而加工要求較高的零件,也常使用精密車削。對(duì)于表面粗糙度值要求很小的銅、鋁及其合金制件的外圓表面或反射鏡的曲面,使用金剛石車刀進(jìn)行鏡面車削,表面粗糙度Ra值可小于0.05m。精密車削還用做黑色金屬或其他表面硬度高的精密零件光整加工前的預(yù)加工工序。 2精密車削的刀具及切削用量精密車削除必須在精密車床上進(jìn)行外,還需要對(duì)所用的三爪自定心卡盤、彈簧夾頭、心軸等回轉(zhuǎn)組件進(jìn)行動(dòng)平衡,并精密測定其跳動(dòng)量,以及仔細(xì)選取刀具材料和切削用量。精密車削所用刀具主要有金剛石車刀和硬質(zhì)合金精
15、密車刀兩種。 (1)金剛石車刀。金剛石刀具材料有天然單晶金剛石和人造聚晶金剛石兩種。金剛石具有硬度高、耐磨性好、刃口鋒利和摩擦系數(shù)小等優(yōu)點(diǎn),但韌性很差,刃磨困難。圖7.5所示為在精密車床上加工黃銅H62所用的金剛石精密車刀,工件要求表面粗糙度Ra值為0.03m。為加強(qiáng)刀尖和刃口部位強(qiáng)度,采用前角o= 510過渡刃為0.05mm,后角為23。 圖7.5 金剛石精密車刀 金剛石刀具適用于有色金屬及其合金(如鋁、紫銅、黃銅、巴氏合金、鈹銅、鋅等)及非金屬材料(如酚醛塑料、陶瓷等)的精密車削。由于金剛石與鐵的親和力很強(qiáng),所以金剛石刀具不適于加工黑色金屬。用金剛石車刀進(jìn)行精密車削,可以采用很高的切削速度
16、,也可以低速進(jìn)行切削,如在CGM6125車床上加工H62材料時(shí)可選切削速度vc68m/min或vc17m/min。 精密車削的進(jìn)給量一般選f = 0.010.04mm/r;雙面加工余量為0.30.5mm;半精加工的背吃刀量ap= 0.050.1mm,精加工的背吃刀量ap= 0.020.05mm。超精密加工時(shí),背吃刀量ap一般為0.0030.006mm。 (2)硬質(zhì)合金精密車刀。用細(xì)顆粒的硬質(zhì)合金(如YG6X、YG6A、YG3X等)車刀進(jìn)行精密車削,可以達(dá)到的表面粗糙度Ra值為0.05m左右;用超細(xì)顆粒的硬質(zhì)合金(如YH1、YH2、YG10H等)車刀進(jìn)行精密車削,可以達(dá)到的表面粗糙度Ra值為0.
17、03m。 圖7.6所示為YG6A或YG6X硬質(zhì)合金精密車刀。車刀前面、后面的表面粗糙度Ra值應(yīng)0.02m;刃傾角為10,以利排屑;車刀采用6后角和3副后角,可以減小振動(dòng)并使刀具后面對(duì)工件有輕微的擠壓作用。該精密車刀用于精密車削銅料。 圖7.6 硬質(zhì)合金精密車刀 用硬質(zhì)合金精密車刀進(jìn)行精密車削時(shí),一般采用高的切削速度:車鋁合金材料vcmax = 350m/min,車青銅等銅合金材料vcmax = 400m/rain;車鎂合金材料vcmax = 1 000m/min。切削速度越高,獲得的表面粗糙度值越小,但刀具磨損及振動(dòng)也隨之加劇,所以應(yīng)根據(jù)實(shí)際情況來合理選擇。進(jìn)給量一般取f = 0.020.04
18、mm/r;背吃刀量一般取ap = 0.20.3mm。 在精密磨床上用經(jīng)過精細(xì)修整的細(xì)粒度砂輪進(jìn)行的一種磨削方法稱為精密磨削。精密磨削一般指加工精度為10.1m,表面粗糙度Ra為0.160.006m的磨削方法。 1精密磨削的應(yīng)用精密磨削是一種高精度、小表面粗糙度值的精密加工方法,主要用于淬硬的黑色金屬材料精密加工,它可以獲得IT5級(jí)的尺寸精度和高的幾何形狀精度,如圓度誤差小于0.5m,圓柱度誤差小于0.001mm/300mm,平面度誤差小于0.003mm/1 000mm,還可使同軸度誤差小于1m。表面粗糙度Ra值一般在0.16m以下,最小可達(dá)到0.008m。 精密磨削按磨削后所獲得的表面粗糙度值
19、的大小,通??杉?xì)分為精密磨削(Ra值為0.160.04m)、超精密磨削Ra值0.040.01m)和鏡面磨削(Ra值小于或等于0.01m)三種。精密磨削主要用于機(jī)床主軸、高精度軸承、液壓滑閥、標(biāo)準(zhǔn)量具、量儀、半導(dǎo)體硅片,以及航空、航天工業(yè)中的精密零件、計(jì)算機(jī)磁盤等元件的磨削。 2精密磨削用機(jī)床及砂輪(1)對(duì)精密磨床的要求。砂輪主軸的回轉(zhuǎn)精度高于1m,內(nèi)圓磨具采用靜壓;應(yīng)有對(duì)傳動(dòng)部分的減振措施;橫向進(jìn)給機(jī)構(gòu)的重復(fù)精度高,誤差小于2m,刻度值不得大于0.005mm,最好配有數(shù)字控制或其他控制尺寸的裝置;工作臺(tái)運(yùn)動(dòng)平穩(wěn),在一定范圍內(nèi)無爬行。 (2)精密磨削用砂輪。 磨料。鋼和鑄鐵零件進(jìn)行精密磨削時(shí),砂
20、輪磨料應(yīng)選用剛玉(單晶剛玉最好),而不選用碳化硅。超精密磨削和鏡面磨削不宜用微晶剛玉。銅合金和鋁合金材料的精密磨削,砂輪磨料選用剛玉或碳化硅均可。對(duì)于精密磨削含有大量硬質(zhì)點(diǎn)的耐熱鋼、高強(qiáng)度而難加工材料,砂輪磨料可采用立方氮化硼,但應(yīng)注意其晶粒的粗細(xì)。精密磨削硬質(zhì)合金及其他硬脆材料,則應(yīng)采用人造金剛石磨料。 粒度。應(yīng)選用粒度號(hào)為60或更細(xì)的磨?;蛭⒎?。 硬度。砂輪硬度根據(jù)工件硬度而定,對(duì)于淬火后鋼件,一般用K、L(中軟)級(jí),對(duì)鏡面磨削應(yīng)使用D、E、F(超軟)級(jí)砂輪,以利于充分發(fā)揮摩擦拋光作用。 結(jié)合劑。一般采用陶瓷結(jié)合劑,以利于充分發(fā)揮粗粒度磨料的微刃切削作用。鏡面磨削時(shí),一般選用樹脂結(jié)合劑,并
21、加入一定量的石墨添加劑。 組織。砂輪組織應(yīng)均勻且緊密,一般選用組織號(hào)為03號(hào)。精密磨削用砂輪需經(jīng)精細(xì)修整,以使砂輪表面上的微刃等高。 精加工后,從工件上不切除或切除極薄金屬層,用以減小工件表面粗糙度值,提高工件表面質(zhì)量或強(qiáng)化工件表面的加工過程稱為光整加工。常用的光整加工方法有:超精加工、珩磨、研磨、拋光等。 1超精加工超精加工是用細(xì)粒度的磨具對(duì)工件施加很小的壓力,并作往復(fù)振動(dòng)和慢速縱向進(jìn)給運(yùn)動(dòng),以實(shí)現(xiàn)微量磨削的一種光整加工方法。超精加工主要適用于軸類零件外圓表面的光整加工,通過精加工可以獲得表面粗糙度Ra值為0.10.01m的表面,但不能提高工件的形狀和位置精度。超精加工只能切去工件表面微觀不
22、平的凸峰,加工余量很小,只有0.0050.01mm。由于切削速度低,油石壓力小,加工時(shí)發(fā)熱少,不會(huì)使工件表面燒傷或產(chǎn)生殘余拉應(yīng)力。 超精加工的磨具為油石,選用細(xì)粒度,以較低的壓力和切削速度對(duì)工件表面進(jìn)行加工,加工時(shí)有3種運(yùn)動(dòng)(見圖7.7),即工件的低速回轉(zhuǎn)、磨具的軸向進(jìn)給運(yùn)動(dòng)和油石的高速往復(fù)振動(dòng)。油石振動(dòng)的頻率為1025Hz,振幅為15mm,油石對(duì)工件表面的壓力P = 15 104Pa。圖7.7 超精加工外圓表面超精加工必須加注充分的潤滑油,一方面清洗極細(xì)的磨屑,另一方面使被加工表面上形成一層很薄的油膜,在工件表面的凸峰被磨去后,油石被油膜所阻隔,自動(dòng)停止切削作用,超精加工完成。 超精加工可以
23、在普通車床、外圓磨床上增加專用磨具進(jìn)行。成批生產(chǎn)時(shí)可采用專門的超精加工機(jī)床。超精加工廣泛應(yīng)用于加工內(nèi)燃機(jī)的曲軸、凸輪軸、軋輥、軸承、刀具、精密量儀及電子儀器等的精密零件,能對(duì)不同的材料進(jìn)行加工。除外圓外,還能加工內(nèi)圓、平面及特殊輪廓表面。 2珩磨 珩磨是利用珩磨工具對(duì)工件表面施加一定壓力,珩磨工具同時(shí)作相對(duì)旋轉(zhuǎn)和直線往復(fù)運(yùn)動(dòng),切除工件上極小余量的光整加工方法。珩磨主要用于孔加工,通過珩磨可以獲得很高的尺寸精度和形狀精度,孔的尺寸精度可達(dá)IT5級(jí),孔的圓度誤差可控制在0.0030.005 mm;表面粗糙度一般為Ra0.200.04m,最小可達(dá)Ra0.020.01m。 珩磨孔的工具為珩磨頭,由幾根
24、(一般為46根)粒度很細(xì)的油石沿圓周均勻分布組成(見圖7.8)。珩磨時(shí),珩磨頭有3種運(yùn)動(dòng),即旋轉(zhuǎn)運(yùn)動(dòng)、軸向往復(fù)運(yùn)動(dòng)和垂直于工件加工表面的徑向加壓運(yùn)動(dòng)。珩磨頭的旋轉(zhuǎn)和軸向往復(fù)運(yùn)動(dòng)是主運(yùn)動(dòng),使油石上的磨粒在孔表面上的切削軌跡呈交叉而不重復(fù)的網(wǎng)紋(見圖7.9)。徑向加壓運(yùn)動(dòng)是油石的進(jìn)給運(yùn)動(dòng),可由彈簧、氣壓或液壓的方式施壓,加壓力越大,即進(jìn)給量越大。 圖7.8 珩磨原理 圖7.9 珩磨運(yùn)動(dòng)軌跡 珩磨時(shí),珩磨頭與機(jī)床主軸間采用浮動(dòng)連接,因此,油石能很好地與零件孔壁貼合,加工中不會(huì)改變孔的軸線位置。珩磨不能修正孔的位置偏差。珩磨時(shí),油石與工件孔壁的接觸面積較大,參加切削的磨粒很多,加工效率較高。由于每個(gè)磨
25、粒的磨削力很小,且珩磨的切削速度較低,所以珩磨過程中發(fā)熱少,孔的表面不易燒傷,因而可獲得很高的表面質(zhì)量。 3研磨研磨是用研磨工具和研磨劑,從工件上研去一層極薄表面層的光整加工方法。研磨方法簡便可靠,尺寸精度可達(dá)到IT6級(jí)以上,表面粗糙度Ra值為0.20.012m。研磨的應(yīng)用范圍較廣,可加工各種鋼、鑄鐵、銅、鋁、硬質(zhì)合金、半導(dǎo)體、玻璃、陶瓷、塑料等。研磨可加工各種形狀的表面,內(nèi)、外圓柱面,圓錐面,凸、凹球面,螺紋,齒輪及其他成形表面。 研磨的原理是在研具和工件之間加研磨劑,并在一定壓力下使研具與加工表面作相對(duì)運(yùn)動(dòng),使磨粒在工件表面滾動(dòng)、滑動(dòng),起切削、刮擦和擠壓作用。研磨外圓時(shí),使用研具為研套,如
26、圖7.10所示。粗研套孔內(nèi)有油槽,可儲(chǔ)存研磨劑,而精研套孔內(nèi)無油槽。 圖7.10 外圓研具 研磨內(nèi)孔時(shí),使用的研具為研磨棒,如圖7.11所示。研磨棒表面開有螺旋槽以儲(chǔ)存研磨劑。圖7.11 研磨棒 研套、研磨棒的內(nèi)孔、外圓直徑常制成可調(diào)節(jié)結(jié)構(gòu),以適應(yīng)研磨需要。用研套研磨外圓和用研磨棒研磨內(nèi)孔的運(yùn)動(dòng)簡圖如圖7.12和圖7.13所示。 圖7.12 研磨外圓柱面 圖7.13 研磨內(nèi)圓柱面 研具在一定程度上把本身的幾何形狀復(fù)制給工件,另一方面又是研磨劑的載體。因此,研磨對(duì)研具有較高的要求。研磨劑為磨料、研磨液及輔助材料的混合劑。按研磨劑使用的條件,研磨分濕研、半干研和干研三種類型。 4拋光拋光是利用機(jī)械、化學(xué)或電化學(xué)的作用,使工件獲得光亮、平整表面的加工方法。拋光不能改善工件的尺寸精度和形狀精度。拋光利用高速回轉(zhuǎn)(3040m/s)、涂有拋光膏的彈性磨輪對(duì)工件表面進(jìn)行光整加工。拋光時(shí),帶有磨粒的彈性輪與工件表面產(chǎn)生劇烈摩擦,導(dǎo)致高溫并形成滾壓和切除作用,用以去除前工序的加工痕跡,減小工件表面粗糙度值,增加工件表面光亮,并提高工件的抗疲勞和抗腐蝕性能。拋光膏通常由氧化鉻、氧化鐵磨料與油脂混合調(diào)制而成。
- 溫馨提示:
1: 本站所有資源如無特殊說明,都需要本地電腦安裝OFFICE2007和PDF閱讀器。圖紙軟件為CAD,CAXA,PROE,UG,SolidWorks等.壓縮文件請(qǐng)下載最新的WinRAR軟件解壓。
2: 本站的文檔不包含任何第三方提供的附件圖紙等,如果需要附件,請(qǐng)聯(lián)系上傳者。文件的所有權(quán)益歸上傳用戶所有。
3.本站RAR壓縮包中若帶圖紙,網(wǎng)頁內(nèi)容里面會(huì)有圖紙預(yù)覽,若沒有圖紙預(yù)覽就沒有圖紙。
4. 未經(jīng)權(quán)益所有人同意不得將文件中的內(nèi)容挪作商業(yè)或盈利用途。
5. 裝配圖網(wǎng)僅提供信息存儲(chǔ)空間,僅對(duì)用戶上傳內(nèi)容的表現(xiàn)方式做保護(hù)處理,對(duì)用戶上傳分享的文檔內(nèi)容本身不做任何修改或編輯,并不能對(duì)任何下載內(nèi)容負(fù)責(zé)。
6. 下載文件中如有侵權(quán)或不適當(dāng)內(nèi)容,請(qǐng)與我們聯(lián)系,我們立即糾正。
7. 本站不保證下載資源的準(zhǔn)確性、安全性和完整性, 同時(shí)也不承擔(dān)用戶因使用這些下載資源對(duì)自己和他人造成任何形式的傷害或損失。
最新文檔
- 設(shè)備采購常用的四種評(píng)標(biāo)方法
- 車間員工管理須知(應(yīng)知應(yīng)會(huì))
- 某公司設(shè)備維護(hù)保養(yǎng)工作規(guī)程
- 某企業(yè)潔凈車間人員進(jìn)出管理規(guī)程
- 企業(yè)管理制度之5S管理的八個(gè)口訣
- 標(biāo)準(zhǔn)化班前會(huì)的探索及意義
- 某企業(yè)內(nèi)審員考試試題含答案
- 某公司環(huán)境保護(hù)考核管理制度
- 現(xiàn)場管理的定義
- 員工培訓(xùn)程序
- 管理制度之生產(chǎn)廠長的職責(zé)與工作標(biāo)準(zhǔn)
- 某公司各級(jí)專業(yè)人員環(huán)保職責(zé)
- 企業(yè)管理制度:5S推進(jìn)與改善工具
- XXX公司環(huán)境風(fēng)險(xiǎn)排查及隱患整改制度
- 生產(chǎn)車間基層管理要點(diǎn)及建議
相關(guān)資源
更多