【溫馨提示】壓縮包內(nèi)含CAD圖有下方大圖片預覽,下拉即可直觀呈現(xiàn)眼前查看、盡收眼底縱觀。打包內(nèi)容里dwg后綴的文件為CAD圖,可編輯,無水印,高清圖,壓縮包內(nèi)文檔可直接點開預覽,需要原稿請自助充值下載,所見才能所得,請見壓縮包內(nèi)的文件及下方預覽,請細心查看有疑問可以咨詢QQ:11970985或197216396

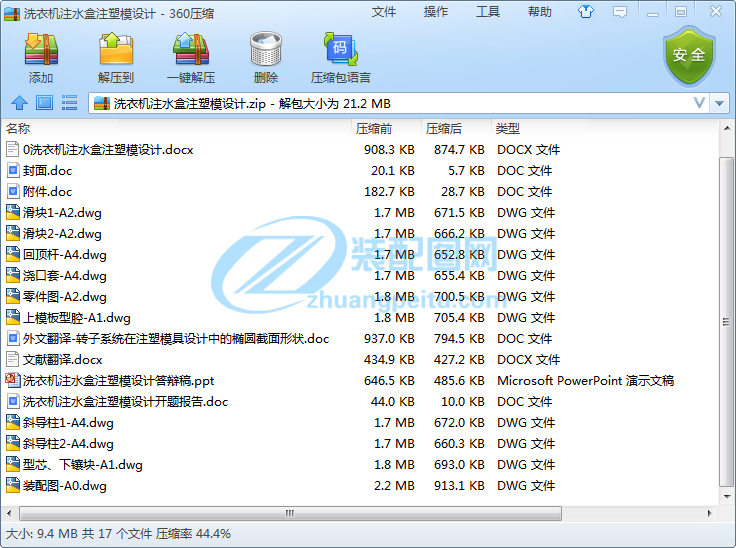
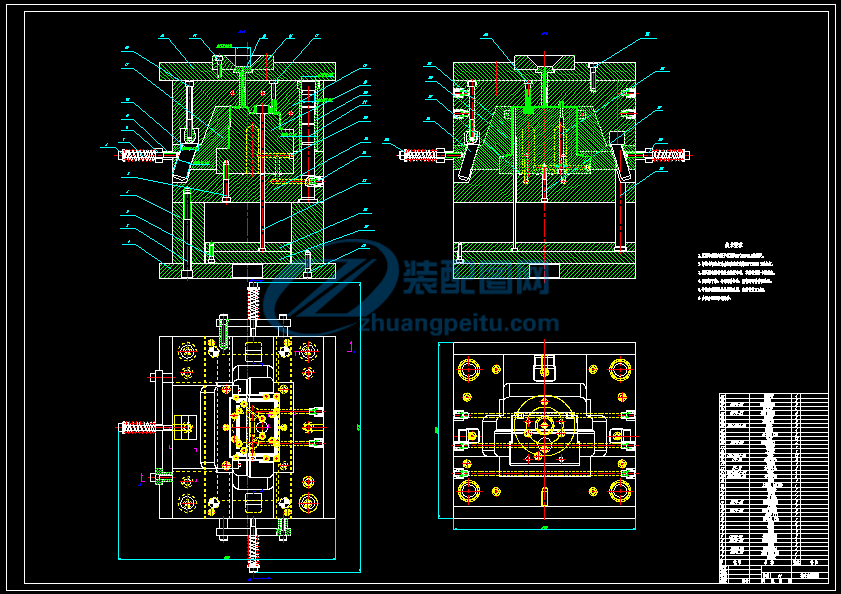
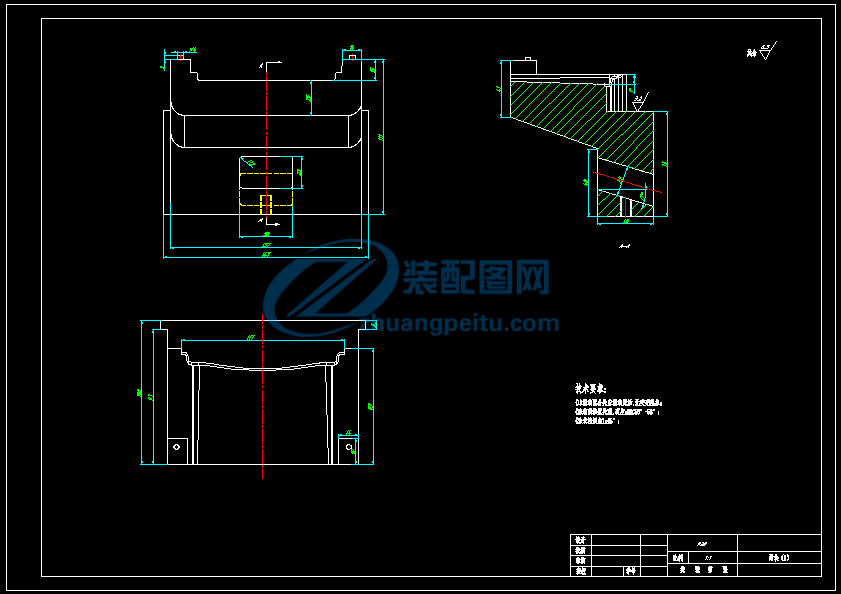
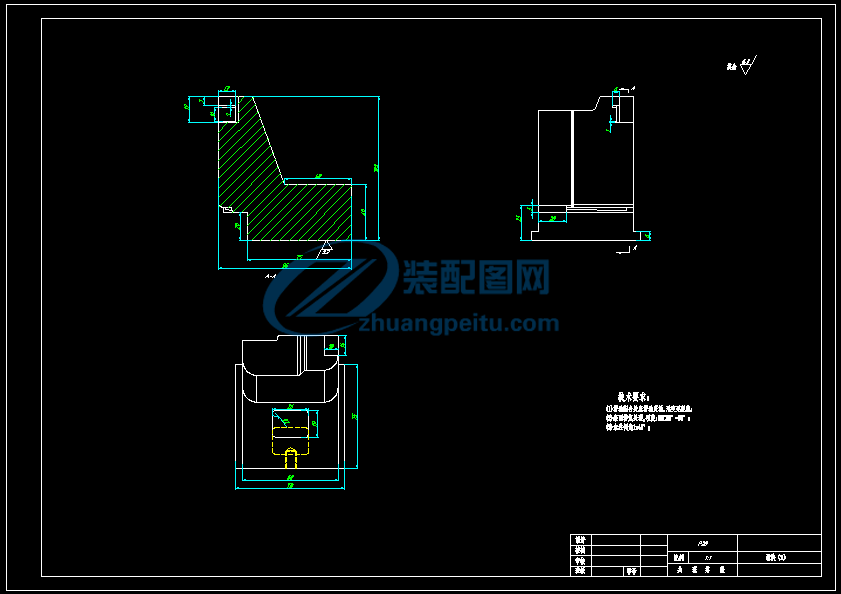

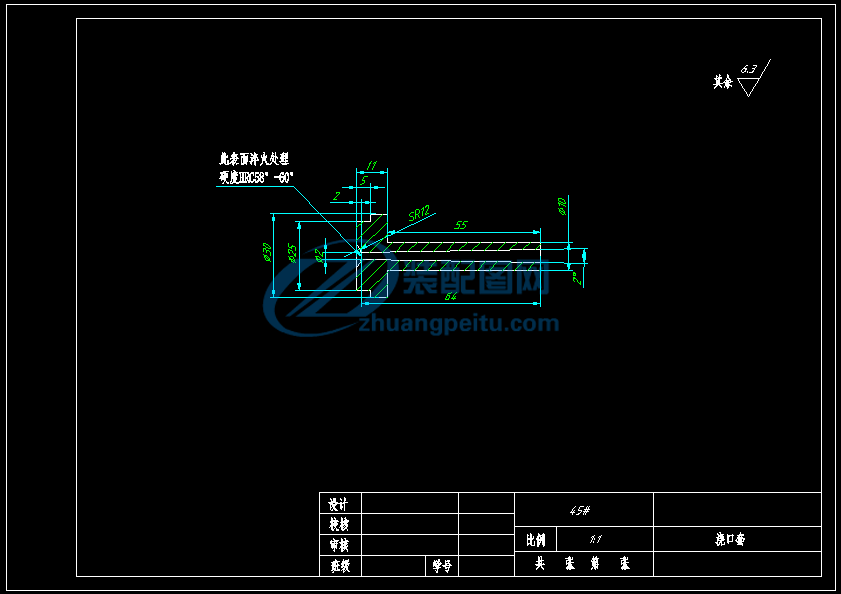
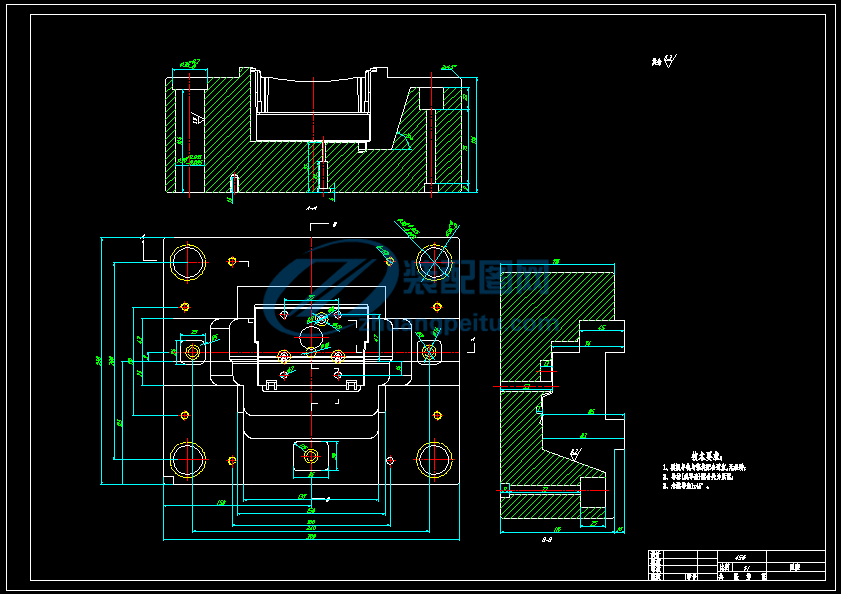
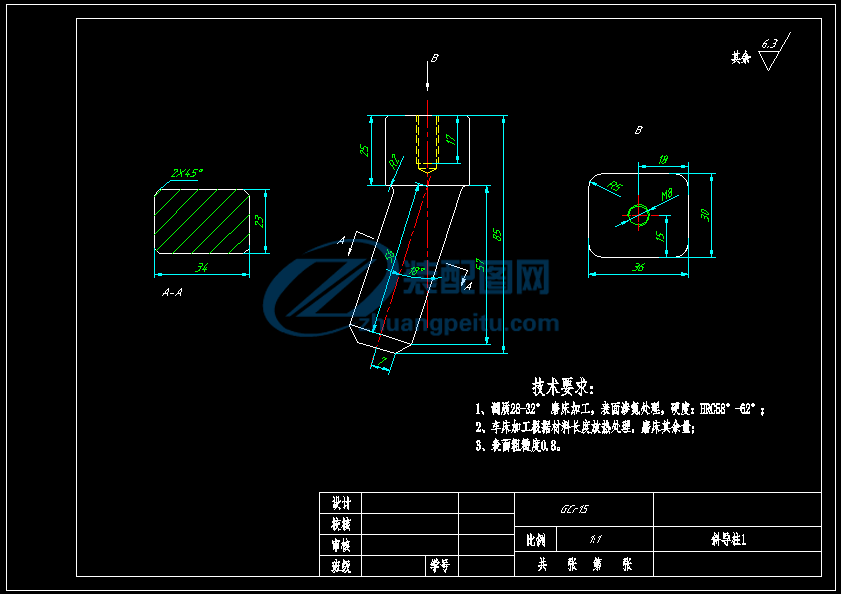
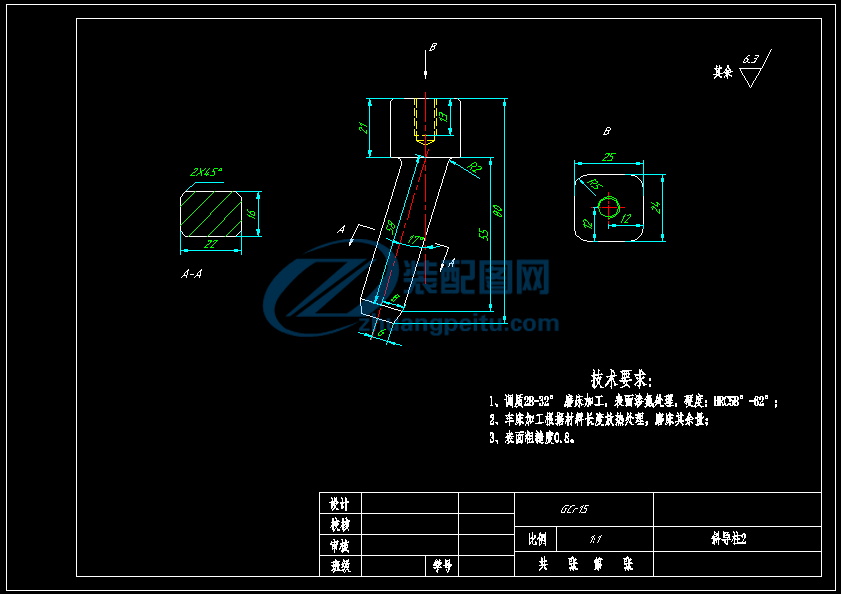

畢業(yè)設(shè)計說明書
轉(zhuǎn)子系統(tǒng)在注塑模具設(shè)計中的橢圓截面形狀
摘要
本文介紹了注射成型工藝模具設(shè)計中流道系統(tǒng)的一種新的橫截面形狀。新幾何結(jié)構(gòu)的目標是減少廢料,縮短周期時間,并減輕模具工具的流道系統(tǒng)彈出。針對兩個厚度為1mm的圓形平板,提出了具有不同比例的橢圓橫截面形狀。 SolidWorks Plastic采用有限元法(FEM)來模擬注塑零件。 SolidWorks Plastic分析了注塑成型過程中塑料零件的短缺缺陷,以驗證新建議的幾何結(jié)構(gòu)。對新的幾何結(jié)構(gòu)進行了聚丙烯圓形平板注射成型工藝的實驗研究。所選擇的輸入機器參數(shù)是填充時間,熔體溫度,模具溫度,壓力保持時間和純冷卻時間。研究結(jié)果顯示,與新的幾何形狀相比,沒有短路缺陷,與圓形截面相比,廢鋼和冷卻時間分別顯著減少25%和2.5%。流道系統(tǒng)與模具壁的接觸表面的減少也改善了流道系統(tǒng)從模腔排出的容易性。這項研究的貢獻是設(shè)計冷流道系統(tǒng)的新幾何結(jié)構(gòu),以減少廢料,循環(huán)時間,并提供注射成型中流道系統(tǒng)的簡單排出。
關(guān)鍵詞 注塑工藝;模具設(shè)計;澆道幾何形狀;短缺缺陷
介紹
在過去的一個世紀里,塑料的迅速增長及其在所有市場的擴散。根據(jù)世界原料重量的消耗,塑料是最高的與其他舊材料,如鋁,鋼,橡膠,銅和鋅相比。它是由塑料的特殊性能和較低的生產(chǎn)成本造成的[1,2]。注塑是制造塑料制品最重要的工藝之一,大約三分之一的塑料通過注塑成型轉(zhuǎn)化為零件[3]。注塑成型工藝在包裝,航空航天,建筑,汽車零部件,家居用品等行業(yè)的應用越來越廣泛[1,3,4]。注塑件的質(zhì)量取決于材料特性,模具設(shè)計和工藝條件[4-7]。注塑成型的三個基本操作是:(1)將塑料顆粒轉(zhuǎn)化為熔體; (2)將熔融塑料通過澆口,流道和澆口系統(tǒng)注入模具型腔或型腔中,(3)打開模具將部件推出模腔[1,8,9]。
決定注入部件最終質(zhì)量的因素之一是澆口系統(tǒng),它是澆口和澆口之間的連接線[10]。轉(zhuǎn)輪系統(tǒng)的主要目的是將熔融塑料從澆口轉(zhuǎn)移到澆口[11,12]。在冷流道系統(tǒng)中,廢鋼的主要來源是去水后來自澆道和澆口系統(tǒng)的廢料。因此,評估跑步者系統(tǒng)設(shè)計的不同規(guī)則以證明跑步者系統(tǒng)在注射中的重要性(a)較小的轉(zhuǎn)輪尺寸以最小化廢品; (b)容易從模具中取出并從模制部件上取下; (c)用最小的凹痕和焊縫快速填充模腔[13-16]。轉(zhuǎn)輪系統(tǒng)設(shè)計的三個基本因素是橫截面形狀,直徑和腔體布局[13]。七種類型的橫截面形狀可用于不同應用的轉(zhuǎn)輪系統(tǒng)[13,14,17](圖1)。根據(jù)要求,選擇不同類型的轉(zhuǎn)輪橫截面[18]。
圖1不同的流道橫截面形狀
本文的貢獻在于為轉(zhuǎn)輪系統(tǒng)定義橢圓形或半橢圓形幾何形狀作為一種有效的橫截面形狀,針對較小的轉(zhuǎn)輪尺寸將廢料與圓形相比減少到最小,從而減少注射的總周期時間和噴射來自模具的零件更容易。此外,在這項研究中,已經(jīng)檢測到與轉(zhuǎn)輪系統(tǒng)的過程參數(shù)和新幾何形狀有關(guān)的顯著現(xiàn)象,這將在另一篇論文中提出。
本文介紹了轉(zhuǎn)輪系統(tǒng)的橢圓形橫截面形狀的設(shè)計標準,并考慮了轉(zhuǎn)輪系統(tǒng)的圓形和半橢圓形之間的比較。對作者而言,有許多論文研究了注射成型的工藝參數(shù)和材料特性,其中一些包括澆道,澆口和澆口,但就作者的最佳知識而言,沒有參考分析和模擬橢圓轉(zhuǎn)輪系統(tǒng)的橫截面形狀。
根據(jù)注入部件的尺寸和幾何形狀進行流道和澆口系統(tǒng)的設(shè)計。然后,通過SolidWorks設(shè)計帶澆道和澆口系統(tǒng)的注塑零件。為了準確模擬結(jié)果,采用了SolidWorks Plastic中的有限元法(FEM)。最后,為了驗證模型,對兩個圓形注射板進行了實驗方法。
轉(zhuǎn)輪系統(tǒng)的橫截面形狀澆道系統(tǒng)的主要目的是通過澆口將熔融塑料從澆道轉(zhuǎn)移到所有模腔。流道系統(tǒng)有不同的橫截面形狀,每個都有不同的應用[11,17](圖1)。設(shè)計師應該評估不同的因素,為特定產(chǎn)品選擇合適的澆道系統(tǒng)幾何形狀。用于雙板模具的最流行的形狀也是最高效率的圓形。對于三板模具工具,如果澆道僅在模具的一半中制造,則梯形和改型梯形是最佳選擇,但仍然不能接受,因為澆口不能與中心線一致流動流[14]。由于尖角,從矩形,正方形和多邊形形狀的腔體中彈出流道系統(tǒng)是具有挑戰(zhàn)性的。如果設(shè)計人員無法確定所需流道系統(tǒng)的適當橫截面形狀及其尺寸,則會導致壓力下降,導致模腔不完全填充以及高度向模具壁傳遞熱量[13,17,19]。因此,可以考慮流道系統(tǒng)的各種橫截面積來調(diào)節(jié)通向更好注入部分的流動。最后,形狀以及通道的長度對于實現(xiàn)最佳流動是重要的,因此具有較少缺陷的最佳產(chǎn)品[20]。
具有橢圓橫截面形狀的流道系統(tǒng)
在注射成型中,流道系統(tǒng)最常見的橫截面形狀是圓形。在選擇特定零件設(shè)計的圓形時,三個主要因素是(a)較小的流道尺寸以最小化廢料;(b)容易從模具中彈出;(c)以最小凹痕,焊縫和短射線快速填充模腔[13-15]。這里的目的是研究一種新的幾何形狀的流道系統(tǒng),這種流道系統(tǒng)可以產(chǎn)生最少的廢料,與澆口的中心流動流線對齊,適當填充模腔,并且便于將模具從模具中彈出。為此目的,正在研究橢圓形或半橢圓形橫截面形狀,并與圓形橫截面形狀的流道系統(tǒng)進行了精確比較。
為了證明跑步者的橢圓橫截面形狀的重要性,對跑步者系統(tǒng)的其他幾何形狀的評估是必要的。這兩者的最佳現(xiàn)有比較是矩形和方形。矩形是一種寬度不同的正方形。在寬度方面,矩形澆道系統(tǒng)的尺寸與正方形澆道系統(tǒng)的尺寸相比有三種不同的比率[17](圖2)。根據(jù)不同的應用,選擇不同寬度比的矩形流道系統(tǒng)。長方形形狀的優(yōu)點是減少了轉(zhuǎn)輪系統(tǒng)的廢料,并且更容易從模具中取出。壓降是通過減小方形寬度而發(fā)生的這種幾何形狀的缺點之一[17]。
圓和橢圓之間的比較與正方形和矩形的比較相似。如圖3所示,D是圓的直徑,a是長軸長度,b是橢圓的短軸長度。根據(jù)不同的工業(yè)應用,主軸長度是固定的,短軸長度是不同的速率(圖3)。因為這會導致廢料的進一步減少,更容易將部件從模腔中排出,并進一步減少循環(huán)時間。對于不同的部分,這個因素將會改變。因此,提出不同的b比例取決于零件設(shè)計的諸多因素,如尺寸和厚度。
圖2 轉(zhuǎn)輪系統(tǒng)的正方形和矩形形狀之間的比較
圖3轉(zhuǎn)輪系統(tǒng)的圓形和橢圓形狀之間的比較
橢圓形轉(zhuǎn)輪系統(tǒng)的優(yōu)點如下:
1.廢品減量:轉(zhuǎn)輪和門系統(tǒng)的大小和體積是產(chǎn)品廢品的根本原因。 因此,與圓跑者相比,橢圓跑步者導致更少的報廢。
2.從模腔:橢圓形流道系統(tǒng)中,部分射出更加容易,冷卻后與圓形相比,與模具壁接觸的表面更少,從而更容易將注射部件從模腔中排出。
3.縮短循環(huán)時間:橢圓流道所需熔融塑料量較少; 因此包括注入和冷卻階段時間的循環(huán)時間將減少。
與亞軍系統(tǒng)的門的中央流程流。 橢圓流道具有中心流動流,其中大部分澆口設(shè)計減少了熔融塑料至腔體的湍流。
模擬
在為這個應用程序設(shè)計兩個圓形零件作為兩個樣品之后,下一步是通過SolidWorks Plastic來模擬零件。對于模擬,需要定義注射系統(tǒng)。因此,應考慮考慮事先計算來設(shè)計澆道,澆道和澆口系統(tǒng)(圖4)。設(shè)計橢圓截面形狀的比例為0.7b。
為確保分析結(jié)果的準確性,F(xiàn)EM將在模擬中發(fā)揮重要作用。根據(jù)樣品的幾何形狀,將選擇有限元的三角形形狀(圖5)。用于此模擬的選定材料是聚丙烯(PP)。對表面網(wǎng)格和表面網(wǎng)格的不同三角形尺寸評估不同的尺寸,為注入部分選擇1毫米的三角形尺寸。對于包括澆口,流道和澆口的注射系統(tǒng),考慮更小的尺寸。它是由注射系統(tǒng)的靈敏度作為此模擬的關(guān)鍵區(qū)域而產(chǎn)生的。因此,澆道和澆道的三角形尺寸分別為0.3mm和澆口的三角形尺寸分別為橢圓形和圓形橫截面形狀。網(wǎng)格的精度通過網(wǎng)格細化研究來確定。對于直徑為100毫米的兩個圓形部件,澆道和澆口總長度為28毫米。此外,澆道的長度為60毫米,拔模角度為1.5°。
圖4澆口,流道和澆口系統(tǒng)的注射樣品
圖5 轉(zhuǎn)輪橢圓橫截面形狀的FEA
圖6 用橢圓交叉容易填充注射部分
下一步是設(shè)置適當?shù)墓に噮?shù)。根據(jù)所選用的材料和注塑機進行該模擬,填充時間為0.59秒,熔體溫度為230℃,模具溫度為50℃,保壓時間為2.04秒,純冷卻時間3.9秒。如前所述,包括澆道,澆道和澆口的注射系統(tǒng)的幾何形狀和尺寸對操作循環(huán)時間,冷卻時間以及不同的缺陷(如凹痕,短射等)具有顯著影響[25]。在運行模擬之后,根據(jù)新的幾何形狀和尺寸檢查新的流道系統(tǒng)的可接受性。檢查的主要因素包括易于填充,填充時間分析和匯痕分析;并在注射結(jié)束時注射壓力。如圖6所示,橢圓形橫截面的容易填充是處于最可接受水平的綠色區(qū)域。
注塑成型中的一個常見缺陷是如果流動距離較長,將發(fā)生在薄壁或遠離澆口的短射[26]。根據(jù)模擬結(jié)果,該部分可以成功填充,甚至如圖7a所示的橢圓截面的填充時間低于流道的圓形截面形狀的填充時間(圖7b)。
圖7 a橢圓形橫截面的填充時間,b圓形橫截面的填充時間
圖8 a橢圓截面的流動前沿中心溫度,b圓形截面的流動前沿中心溫度
防止噴射部件短射的另一個因素是評估流動前沿中心溫度,該溫度代表注入部件每個區(qū)域的流動前沿溫度。根據(jù)模擬結(jié)果,注射部件的每個區(qū)域的流動前端中心溫度對于轉(zhuǎn)輪的橢圓橫截面形狀為230.15°C(圖8a)。流道的圓形橫截面形狀的模擬結(jié)果是相同的(圖8b)。這意味著橢圓形橫截面形狀的轉(zhuǎn)子在腔內(nèi)短射的可能性很低。
評估澆道和澆口系統(tǒng)合適尺寸所需的最重要因素之一是注射壓力。根據(jù)模擬,這部分可以成功注入壓力42.1MPa。注射壓力小于滿足最大注射壓力極限的66%(圖9)。圓形截面的注射壓力為39.6 MPa,接近橢圓形截面。
實驗裝置
使用商用注塑顆粒聚丙烯(PP)制造兩個圓形板,其具有100mm直徑和1mm厚度。 所選材料的聚合物材料參數(shù)列于表2中。用于制造模具的機器有鉆孔機,數(shù)控銑床和磨床。 實驗采用全電動臥式注塑機-Poolad-Bch系列。
圖9 澆道系統(tǒng)的圓形和橢圓形橫截面形狀的注射壓力
表2 材料屬性PP
熔體溫度
230℃
最高熔化溫度
280℃
最低熔融溫度
200℃
Mod溫度
50℃
熔體流動速率
20厘米3/10分鐘
最大剪切應力
250,000 pa
模具設(shè)計
模具制造有不同的設(shè)計概念。在這項研究中,選擇了雙板模具,該模具具有一個帶有雙腔的分模線和一個供料系統(tǒng)并且沒有頂針。模具由碳鋼CK45制成,表面硬度為56 HRC。磨削后的橢圓形橫澆道,澆口系統(tǒng)和澆口襯套分配到模腔板中(圖10a)。還展示了磨削前帶有導桿的型腔板(圖10b)。
在設(shè)計模具時,另一個要素是導致塑料部件固化的冷卻系統(tǒng)?;谒芰喜考膸缀涡螤?,冷卻系統(tǒng)的設(shè)計是不同的。因此,選擇腔板冷卻系統(tǒng)的圓形幾何形狀(圖11)。
制造模具時要考慮的另一個因素是通風孔。它們的功能是在關(guān)閉模具之后從模腔中釋放空氣;否則如果空氣被困在模具內(nèi),會發(fā)生短射擊。兩個腔體在腔板的左側(cè)和右側(cè)具有單獨的通氣孔(圖12)。
圖10磨削后具有橢圓橫截面的空腔板,b磨削之前具有橢圓橫截面的空腔盤
圖11模腔板內(nèi)的冷卻系統(tǒng),用于注入部件的凝固
圖12 通風孔避免注入部件的空氣陷阱
實驗結(jié)果
根據(jù)不同的工藝參數(shù)設(shè)置模具和注塑機后,從制造過程的不同角度評估流道系統(tǒng)新的橫截面形狀是本實驗的目標。為了確保本研究橢圓截面轉(zhuǎn)輪的有效性,需要實施基于不同工藝參數(shù)的填充腔體和注射過程的顯著性測試。短射擊分析的結(jié)果(圖13)顯示,具有新的流道橫截面形狀的兩個腔體被適當?shù)靥畛洹?
當注入壓力高于最大入口壓力并且注入時間高于注入機器的輸入時,會發(fā)生短射擊。這些實驗中最重要的部分是,與圖14所示的模擬結(jié)果相比,即使在較低的入口壓力和填充時間下,腔體也能夠正確填充。模擬和實驗結(jié)果的比較顯示在表4中。表4中的百分比變化預測和實際的入口壓力和填充時間結(jié)果分別為7.36和3.38%,這證明了轉(zhuǎn)輪系統(tǒng)的新幾何結(jié)構(gòu)的穩(wěn)健性。
通過定義轉(zhuǎn)輪系統(tǒng)的新幾何形狀,這項研究的新穎之處在于減少廢料和冷卻時間,并且實現(xiàn)從腔體中最終注射部件的更容易的噴射。因此,就廢品率和冷卻時間而言,需要在圓形和橢圓形橫截面之間進行比較。表5顯示了對于100,000個注射部件的流道系統(tǒng)的圓形和橢圓形橫截面的廢料率和冷卻時間。圓形橫截面的冷卻時間為每次注射4 s,橢圓截面每次注射3.9 s。與圓形橫截面相比,橢圓形橫截面的廢鋼和鋁合金減少了25%,注入部件的冷卻時間為2.5%。
圖13 最后注射部分具有橢圓形流道橫截面形狀
圖14 橢圓跑步者的每個因素水平較低的注射部位
結(jié)論
冷流道系統(tǒng)注塑廢料的主要原因是由澆口,流道和澆口系統(tǒng)組成的供料系統(tǒng)。跑步者對于不同的應用具有不同的橫截面。本文介紹了橢圓形橫截面與圓形橫截面比較的流道系統(tǒng)新幾何的成功開發(fā)。這種幾何形狀是通過模擬和實驗開發(fā)的,以生產(chǎn)兩個1mm厚的圓形板。工藝參數(shù)為填充時間,熔體溫度,模具溫度,壓力保持時間和純冷卻時間。
為了驗證模型,進行了實驗測試。預測和實際結(jié)果的入口壓力和填充時間的百分比變化分別為7.36和3.38%。結(jié)果證明了轉(zhuǎn)輪系統(tǒng)的新幾何結(jié)構(gòu)的穩(wěn)健性。與圓形橫截面相比,橢圓形橫截面對于注射部件具有25%的廢料減少和2.5%的冷卻時間。模擬和實驗測試的結(jié)果表明,橢圓形截面形狀是一種有效的幾何形狀,可以減少廢料和總循環(huán)時間,并且還可以使模制件更容易從模腔中彈出。模具設(shè)計的進一步研究將為設(shè)計師和模具制造商創(chuàng)造更具包容性和適當?shù)闹笇Х结槨?
參考文獻
[1] Zhou H (2013) Computer modeling for injection molding. Wiley, Hoboken
[2] Salimi A, Subas?? M, Buldu L, Karatas? C? (2013) Prediction of flow length in injection molding for engineering plastics by fuzzy logic under different processing conditions. Iran Polym J 22(1):33–41
[3] Tang SH, Kong YM, Sapuan SM, Samin R, Sulaiman S (2006) Design and thermal analysis of plasticinjection mould. J Mater Process Technol 171(2):259–267
[4] Altan M (2010) Reducing shrinkage in injection moldings via the Taguchi, ANOVA and neural network methods. Mater Des 31(1):599–604
[5]Khoshooee N, Coates PD (1998) Application of the Taguchi method for consistent polymer melt production in injection moulding. Proc Inst Mech Eng Part B J Eng Manuf 212(8):611–620
[6]Ni S (2002) Reducing shrinkage and warpage for printer parts by injection molding simulation analysis. J Inject Molding Technol 6(3):177–186
[7]Mok CK, Chin KS, Ho JKL (2001) An interactive knowledge-based CAD system for mould design in injection moulding processes. Int J Adv Manuf Technol 17:27–38
[8]Dai W, Liu P, Wang X (2002) An improved mold pin gate and its flow pattern in the cavity. J Inject Molding Technol 6(2):115
[9]Hassan H, Regnier N, Pujos C, Arquis E, Defaye G (2010) Modeling the effect of cooling system on the shrinkage and temperature of the polymer by injection molding. Appl Therm Eng 30(13):1547–1557
[10] Tsai KM (2013) Runner design to improve quality of plastic optical lens. Int J Adv Manuf Technol 66(1–4):523–536
[11]Zhen-Yong Z, Zheng-Chao G, Jiao-Ying S (2000) Research on integrated design techniques for injection mold runner system. J Comput Aided Des Comput Graph 12(1):6–10
[12] Bejgerowski W, Gupta SK (2011) Runner optimization for in-mold assembly of multi-material compliant mechanisms. In: Proceedings of the ASME Design Engineering Technical Conference.
[13] Jones P (2008) The mould design guide. Smithers Rapra Technology
[14] Goodship V (ed) (2004) ARBURG practical guide to injection moulding. iSmithers Rapra Publishing
[15] Calhoun DAR, Golmanavich J (2002) Plastics technicians toolbox-extrusion-fundamental skills and polymerscience. Ron Jon, Addison
[16] Zhang Y, Deng YM, Sun BS (2009) Injection molding warpage optimization based on a mode- pursuing sampling method. Polym-Plast Technol Eng 48(7):767–774
[17]Pye RGWte (1989) Injection mould design: a textbook for the novice and a design manual for the thermoplastice industry. Longman Scientific & Technical, Harlow
12