工業(yè)硅礦熱爐的設計
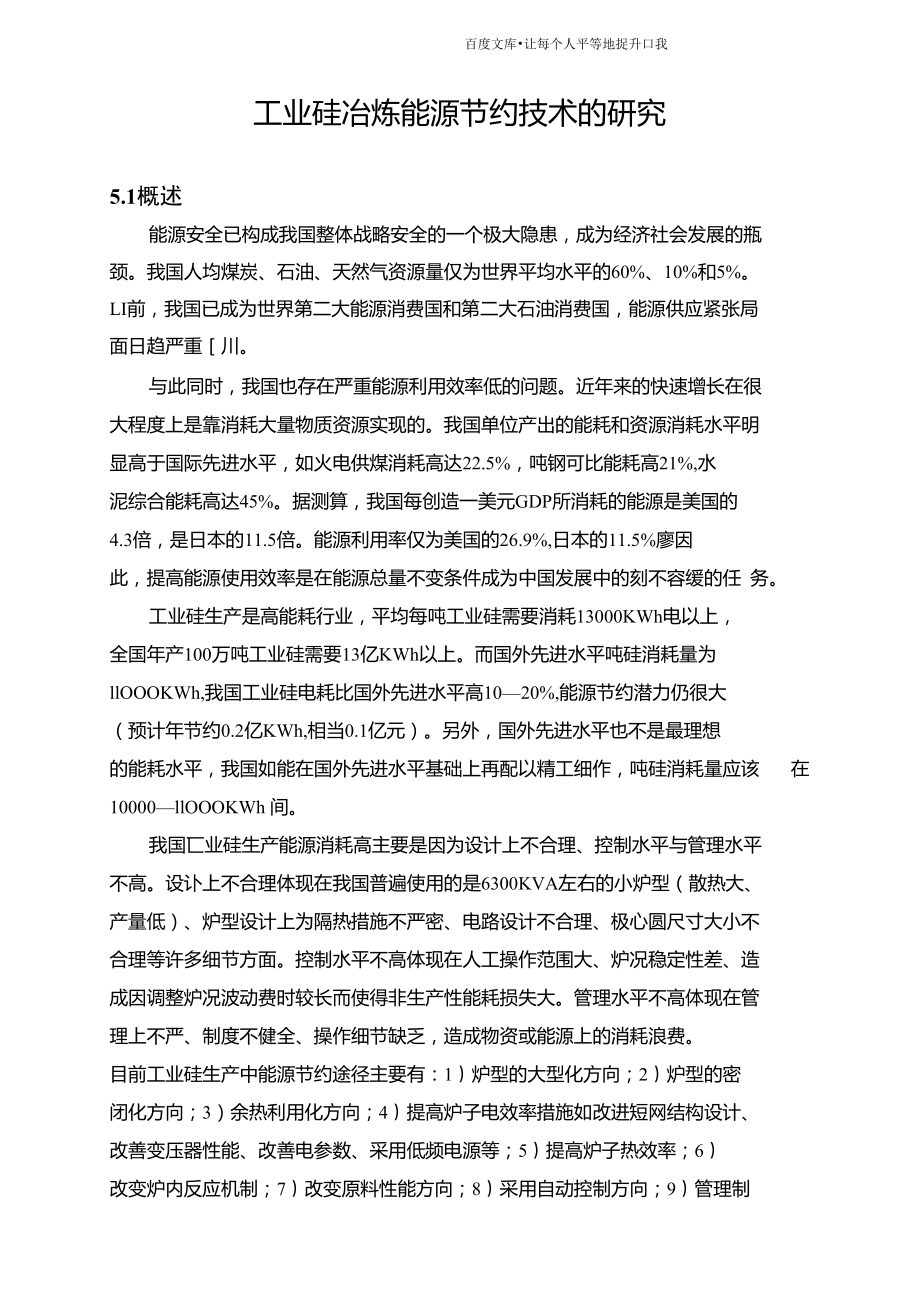


《工業(yè)硅礦熱爐的設計》由會員分享,可在線閱讀,更多相關《工業(yè)硅礦熱爐的設計(22頁珍藏版)》請在裝配圖網上搜索。
1、百度文郵-讓每個人平零地捉升口我 工業(yè)硅冶煉能源節(jié)約技術的研究 5.1概述 能源安全已構成我國整體戰(zhàn)略安全的一個極大隱患,成為經濟社會發(fā)展的瓶 頸。我國人均煤炭、石油、天然氣資源量僅為世界平均水平的60%、10%和5%。 LI前,我國已成為世界第二大能源消費國和第二大石油消費國,能源供應緊張局 面日趨嚴重[川。 與此同時,我國也存在嚴重能源利用效率低的問題。近年來的快速增長在很 大程度上是靠消耗大量物質資源實現的。我國單位產出的能耗和資源消耗水平明 顯高于國際先進水平,如火電供煤消耗高達22.5%,噸鋼可比能耗高21%,水 泥綜合能耗高達45%。據測算,我國每創(chuàng)造一美元GDP所消耗
2、的能源是美國的 4.3倍,是日本的11.5倍。能源利用率僅為美國的26.9%,日本的11.5%廖因 此,提高能源使用效率是在能源總量不變條件成為中國發(fā)展中的刻不容緩的任 務。 工業(yè)硅生產是高能耗行業(yè),平均每噸工業(yè)硅需要消耗13000KWh電以上, 全國年產100萬噸工業(yè)硅需要13億KWh以上。而國外先進水平噸硅消耗量為 llOOOKWh,我國工業(yè)硅電耗比國外先進水平高10—20%,能源節(jié)約潛力仍很大 (預計年節(jié)約0.2億KWh,相當0.1億元)。另外,國外先進水平也不是最理想 的能耗水平,我國如能在國外先進水平基礎上再配以精工細作,噸硅消耗量應該 在 10000—llOOOKWh 間。 我
3、國匸業(yè)硅生產能源消耗高主要是因為設計上不合理、控制水平與管理水平 不高。設訃上不合理體現在我國普遍使用的是6300KVA左右的小爐型(散熱大、 產量低)、爐型設計上為隔熱措施不嚴密、電路設計不合理、極心圓尺寸大小不 合理等許多細節(jié)方面??刂扑讲桓唧w現在人工操作范圍大、爐況穩(wěn)定性差、造 成因調整爐況波動費時較長而使得非生產性能耗損失大。管理水平不高體現在管 理上不嚴、制度不健全、操作細節(jié)缺乏,造成物資或能源上的消耗浪費。 目前工業(yè)硅生產中能源節(jié)約途徑主要有:1)爐型的大型化方向;2)爐型的密 閉化方向;3)余熱利用化方向;4)提高爐子電效率措施如改進短網結構設計、 改善變壓器性能、改善電參數、
4、采用低頻電源等;5)提高爐子熱效率;6) 改變爐內反應機制;7)改變原料性能方向;8)采用自動控制方向;9)管理制 度建設方向。山于上述諸多途徑尚處于討論階段,形成固定技術并推廣者僅有短 網改進、管理制度建設上,許多技術細節(jié)缺乏,因此真正意義上可以直接使用的 工業(yè)硅生產中能源節(jié)約技術還需要研究與試驗。 經過多年的摸索探討,目前我國工業(yè)硅電弧爐的電效率平均在92%以上,各 種提高電效率的技術或措施也比較成熟如改進短網結構設訃、使用優(yōu)質導電材 質、采用低壓補償技術、改善電參數等方面。但是,我國工業(yè)硅電弧爐的熱效率 普遍比較低,這是導致我國工業(yè)硅生產能耗高、能源利用效率低的主要原因,表 5-1是我
5、國某廠6300KVA電弧爐的熱平衡分析表【2嘰 表5-1我國某廠6300KVA電弧爐的熱平衡分析 熱收入項 熱量(千卡/h) 百分比 熱支出項 熱量(千 卡/h) 百分比 1、電熱能 4324940 95.98 1、氧化物還原耗熱 1834462 40.71 2、電極氧化熱 100680 2.234 2、金屬硅帶走熱 269456 5.98 3、還原劑反應放熱 80520 1.78 3、逸岀氣體帶龍熱 826633 18.35 4、爐而散熱 269333 5.97 5、爐體散熱 166448 3.69
6、 6、短網熱損失 336738 7.47 7、冷卻水帶走熱 750000 16.46 8、其他 53370 1」9 合計 4506140 100 4506140 100 從表5-1可以看出6300KVA電弧爐在工業(yè)硅生產過程中,電效率為92.21%, 熱效率為65%,能源大部分山于熱效率低而被損失掉,損失途徑主要是逸出氣 體帶走熱、爐面散熱、爐體散熱、短網熱損失、冷卻水帶走熱。因此,提高工業(yè) 硅電弧爐冶煉過程中的熱效率應當是今后研究的重點。 在本文研究中,我主要從提高工業(yè)硅礦熱爐冶煉過程中的熱效率角度來研究 工業(yè)硅冶煉能源節(jié)約
7、技術。 提高工業(yè)硅冶煉能源的熱效率是一項綜合性能源節(jié)約技術,它應當包括所有 能夠能夠提高熱效率、減少熱損失的技術或描施。但是在本文中只研究爐型的大 型化方向、爐型的密閉化方向、余熱利用化方向、隔熱設計技術四個方面來提高 工業(yè)硅冶煉過程中的熱效率。因為從表5-1可以看出,工業(yè)硅礦熱爐熱效率低就 是因為逸出氣體帶走熱、爐面散熱、爐體散熱、短網熱損失、冷卻水帶走熱這五 個方面熱損失大。 爐型大型化則單位熱容率增大,能量供應集中,通過外圉表面單位面積散熱 小、爐子熱穩(wěn)定增強,有利于降低熱損失。同時爐型大型化也是今后工業(yè)硅行業(yè) 發(fā)展的方向,大型爐具有熱容量大、產量高、有利于二次精煉提高產品質量、單
8、位產品成本低、便于煙氣余熱利用等諸多好處。因此,研究爐型大型化不僅是降 低熱損失的需要,也是滿足今后工業(yè)硅行業(yè)長期發(fā)展的需要,具有雙重意義。 爐型密閉化或近密閉化不僅可以減少爐面熱輻射損失,而且也可以減少煙氣 從6個爐門逸出帶走的熱,也是降低熱損失、增加煙氣回收能力、改善爐前操作 環(huán)境的有力措施。 從表5-1可以看出,煙氣帶走熱占據了供應總熱量的35%,這部分熱量 乂被散發(fā)到大氣中,造成了能源損耗,致使能源利用率低,國內包頭鋼鐵研究設 計院曾經依據鋼鐵行業(yè)余熱利用方式設訃過余熱回收裝置,在某廠應用取得較好 的使用效果,但是山于該余熱回收裝置初期投資過大,國內工業(yè)硅企業(yè)乂大多數 是私營企業(yè),
9、他們不愿意做這么大的投資,所以研究一種新型低造價、多用途、 適用于大多數企業(yè)的余熱利用裝置(熱材聯產裝置)很有必要,開辟一條已經被 浪費掉的巨大熱能集熱道路具有非常重要的現實意義。 科技每時每刻都在變化,上世紀60年代所作的設計不應當在這個世紀仍然 被當作模范來應用。當前,山于國內沒有實力研究機構來重新對上世紀60年代 所作的工業(yè)礦熱爐設訃作改進,致使大多數企業(yè)仍用老的設計來建爐子,并且施 工隊伍都非正規(guī)研究機構或有能力去開發(fā)建設新型爐子,所以我國U詢的工業(yè)硅 礦熱爐普遍都能耗高、設計未能跟上時代發(fā)展的需要。問題的重要一方面反映在 爐體隔熱設訃多年來沒有多大改變,普遍使用的是碳磚層、耐火磚層
10、、纖維板、 鋼板四層結構,隨著科技的發(fā)展這種結構應半革新,因為國際國內新材料領域發(fā) 生的一系列創(chuàng)新已經給我們帶來了重新設訃爐體結構的機遇。 上述四個以提高工業(yè)硅冶煉能源的熱效率為U的的研究是口前工業(yè)硅冶煉 能源節(jié)約方面尚未涉及完善但乂非常重要的領域,需要既具備豐富的科學理論知 識、乂掌握國際國內工業(yè)硅冶煉情況的人員才能完成,它涉及到的冶金、工藝、 傳熱、設備、設計等多方面的知識與創(chuàng)新要求,使得這方面的工作既具體乂復雜、 既藝術乂有意義。 5.2大容量半密閉式12500KVA工業(yè)硅礦熱爐的設計 5.2.1設計依據 本項工作采用如下設計規(guī)范: 《中國節(jié)能技術政策大綱》(2005); 《
11、冶金企業(yè)安全衛(wèi)生設汁暫行規(guī)定》(1988); 《建筑設計?防火規(guī)范》(GBJ16-87); 《工業(yè)爐窯大氣污染排放標準》(GB9078-1996); 《工業(yè)爐砌筑工程施工及驗收規(guī)范》(GB50211-2004)。 5.2.2設計內容 5.2.2.1變壓器選型 大容量礦熱爐具有單爐產量大、能量供應均衡性好、便于實現機械化、便于 余熱綜合利用、熱穩(wěn)定性好、便于操作等一系列優(yōu)點,是業(yè)界一致認可的礦熱爐 發(fā)展的方向。為了促進國內工業(yè)硅行業(yè)冶煉水平的提高和設備裝備的現代化,因 此此次設計采用125OOKVA容量的礦熱爐變壓器。 125OOKVA礦熱爐變壓器具體技術參數如下: 型號:HKS
12、SPZ2O-125OO/35殼式強油水冷礦熱爐變壓器: 額定容量:12500KVA,可超載30%; 冷卻方式:0FWF: 一次電壓(KV): 35; 二次額定電壓(V): 151: 二次電壓(V): 175,172,169,166,163,160,157, 154, 151, 148, 145, 142, 139, 136, 133 共 15 檔; 阻抗電壓(短路電壓):ex%M-6%o 5.2.2.2礦熱爐電氣參數的確定 在工業(yè)硅冶煉過程中礦熱爐的狀態(tài)與電氣參數的變化密切相關,控制最佳的 供電制度對保證取得好的經濟技術指標十分重要。 一般而言,提高礦熱爐的二次電壓在功率一定
13、情況下電流就可以降下來,這 有利于提高線路功率因數和減少電損失,但是過分提高礦熱爐電圧,電極就不能 39 百度文郵-讓每個人平零地捉升口我 深插,爐膛料面就會過熱,熱損失增加,硅回收率降低,因此每臺電爐都有其適 宜的二次電壓值。在設計電爐時往往利用米古林斯基公式宓、83】來確定礦熱爐正 常工作時的二次電壓: V2=KPUi 式中:K為電壓系數,取6.0-7.5; P是變壓器額定功率,KVAo 因此這次設計時取二次電壓V2=6.5X 12500,/3= 150.85151V, 二次電流/?= =47795.2Ao 5.2.2.3礦熱爐結構設計 正確設計礦熱爐的結
14、構是保障礦熱爐工作性能的先決條件,是設計工作者面 臨的最大困難。好的礦熱爐結構設計不僅有利于爐子保障高產、優(yōu)質、低能耗、 少故障的生產,而且有利于節(jié)約筑爐成本、方便其它設備布置、保證操作順暢。 1、電極直徑的選取 在確定礦熱爐其它結構尺寸之前,必須先確定電極直徑,它決定著礦熱爐其 它結構尺寸的大小。電極直徑有許多計算方法,一般根據電極電流和電極電流密 度確定: d= 2.1-^— = 102.4cm= 1024mm, 式中/2為電極電流,A, 4/為電極電流密度5.5-6.lA/cm2,取5.8計算。 根據國內廠家生產碳素電極的標準,取電極直徑為1050mmo 2、極心圓直徑計算
15、 極心圓直徑是一個對冶煉過程有很大影響的設備結構參數,電極極心圓直徑 選得適當(圖5-1),三根電極電弧作用區(qū)域部分剛好相交于爐心,各電極反應區(qū) 既相互相連乂重疊部分最小,在這種惜況下,爐內熱量分配合理,堆竭熔池最大, 吃料均勻,爐況穩(wěn)定,爐況也易于調節(jié)。如果一設計就不適當,則熱量不是過分 集中(圖5-2)就是熱量分散(圖5-3),這都會造成爐況調節(jié)頻繁或根本無法調 節(jié)的嚴重錯誤。 設計中極心圓直徑可按下式計算: Dg=ad=2.3 X 1050=2415mm 式中a為極心圓倍數,a=2.2-2.3,這里取2.3計算。 結合礦熱爐容量、可調極心圓范圉、實際電氣參數調節(jié)空間這里取極心圓
16、直 徑為 2500mm o 3、 爐膛內徑計算 在選擇爐膛內徑時,要保證電流流過電極一爐料一爐壁時所受的阻力大于經 過電極一爐料一電極或爐底時所受的阻力。否則,爐膛內徑選擇尺寸過大,礦熱 爐表面散熱面積大,還原劑燒損嚴重,出硅口溫度低,出硅困難,爐況會惡化。 爐膛內徑選擇過小,電極一爐料一爐壁回路上通過的電流增加,反應區(qū)偏向爐壁, 將使爐內熱量分散,爐心反應區(qū)溫度低,爐壁腐蝕嚴重,爐況也會惡化。 爐膛內徑可按下面經驗公式計算: Dn=rd=5.8 X 1050=6090mm 式中r為爐膛內徑倍數,r=5.8-6.0,這里取5& 爐膛內徑這次設訃中取為6200mmo 4、 爐膛
17、深度計算 在選擇爐膛深度時,要保證電極端部與爐底之間有一定的距離、電極有效插 入的深度和料層有一定的厚度。爐膛深度若過深,電極與爐底距離遠,電極不能 深插,高溫區(qū)上移,爐底溫度低,爐底SiC會沉積,爐底上抬,堵塞出硅口,爐 況變差。爐膛深度若太淺,料層卑度將很薄,爐口溫度升高,硅揮發(fā)損失增加, 容易露弧操作,能耗增大。 合適的爐膛深度可按下面經驗公式計算: h=Pd=2.5X1050=2625mm 式中B為爐膛深度倍數,B =2.528,這里取2.5。 爐膛深度這次設計中取為2700mm. 5、 爐襯與爐底的結構、尺寸及材料選擇 一般而言,爐襯、爐底結構包含了工作層、保溫層、隔熱
18、層、絕熱層、鋼板 層5個主要層次,但是每個層次的具體尺寸卻是很有技術含量的,因為這涉及到 筑爐成本、爐子性能、爐子壽命等許多經濟因素。 爐襯厚度過厚,引起筑爐成本上升,占地面積擴大,爐襯表面積增加,散熱 面積也增大;爐襯厚度過薄,抑或爐襯強度不夠,抑或無法保溫。爐底厚度亦是 如此。 國內外對爐襯、爐底散熱強度計算表明,保持爐襯與爐底熱損失為2-4%是 合理的范圍內⑻]或者保持爐襯表面溫度在70-120C是允許的。因此按照這個 條件以及結合所選擇材料的使用溫度,根據傳熱學知識可確定爐襯與爐底丄作 層、保溫層、隔熱層、絕熱層的厚度,鋼板層的厚度根據強度需要而定。 我們在這次設汁中,工作層都使
19、用自焙碳磚、保溫層選用新型隔熱耐火粘土 磚(熱導率vO.44W/m?k)、隔熱層使用納米隔熱材料、絕熱層使用復合硅酸鋁纖 維毯、鋼板層選用14mm療的普通鋼(爐底鋼板厚18mm),如圖5?4。 1電極孔2煙罩上蓋板3煙囪孔4冷卻水道5觀測孔6搗料爐門7紅磚8隔熱耐火磚 9納米絕熱材料10復合硅酸鋁纖維毯11鋼板12出硅口 13高鋁磚14自焙炭磚 圖5-4 125OOKVA工業(yè)硅礦熱爐結構圖 6、出硅口位置、結構、尺寸與材料選擇 出硅口是礦熱爐上非常重要的一個部位,它的位置、結構形狀.尺寸、材料 選擇都是需要仔細斟酌的。位置布置不當,出硅口部位溫度低,出硅不暢或者是 操作不方
20、便;結構形狀尺寸不當,也會導致出硅不暢或者封堵困難或者出硅時間 延長;材料選擇不當,容易氧化腐蝕,維修頻繁。 在這次設計中,出硅口設計二個,每個出硅口水平位置與爐底齊平并比爐底 水平線下傾斜3C,角度位置它處于爐心與電極中心兩點的延長線與爐壁的焦點 上。出硅口應當設計成圓形,便于燒穿與封堵,尺寸根據出硅時間要求計算并結 合實際操作需要來決定大小為直徑100- 120mm,材料選擇上容易氧化的外側使用 石英材料與碳糊。 7、 爐門結構、尺寸與材料選擇 大容量爐最大的問題是爐緣距離爐心遠,上料困難,特別是國內強調以人工 精細加料來取得好質量與低能耗產品的觀點下,普遍認為在大容量爐子在國內不
21、如6300KVA爐子的性能,因此一次乂一次的阻礙了投資方建造大容量爐子的熱 情。我們在這次設計中僅設計了 3個搗料爐門,上料操作通過釆用前述笫三章開 發(fā)設訃的自動上料系統來完成,克服了大容量爐存在的最大惱人的問題。自動上 料裝置將料布放在料面各處,搗爐功能通過窺視孔根據需要打開搗料爐門進行搗 爐操作。搗爐爐門門檻下部與爐沿等高,門檻長1200mm, A 1500mm,使用單 獨水冷結構。不需要搗爐時,爐門關上,密閉冶煉。 8、 煙罩結構、尺寸與材料選擇 大容量礦熱爐爐膛尺寸跨度大,煙罩設訃較困難,同時從煙罩通過的電流大, 處理不好渦流損失大。為了解決煙罩結構強度與防止渦流損失,我們采取用水
22、冷 鋼管(防磁)做骨架并起吊,上下蓋采用石板與水泥構筑,用細鋼筋做支撐,既 減輕了煙罩整體重量乂防止了筑砌或制作上的不便。煙罩高度離爐沿2300mm, 直徑與爐殼直徑等同,厚度160mm,上下蓋間通水冷卻。 5.2.3技術指標 設計完成以后有關該爐的技術參數與性能如下: 電極直徑:1050mm; 極心圓直徑:2500mm; 爐膛直徑:6200mm; 爐膛深度:2700mm; 爐殼直徑:8000mm; 爐殼高度:4618mm; 煙罩高度:2300mm; 理論日產量:20噸; 理論電單耗量:13000KVAh/噸。 5?3余熱利用化研究 5.3.1余熱利用思路 余能是在
23、一定經濟技術條件下,在能源利用設備中沒有被利用的能源,也就 是多余、廢棄的能源。它包括高溫廢氣余熱、冷卻介質余熱、廢汽廢水余熱、高 溫產品和爐渣余熱、化學反應余熱、可燃廢氣廢液和廢料余熱以及高壓流體余壓 等七種。其中最主要的是余熱。根據調查,各行業(yè)的余熱總資源約占其燃料消耗 總量的17%~67%,可回收利用的余熱資源約為余熱總資源的60%[陶。余熱的回 收利用途徑很多。一般說來,綜合利用余熱最好;其次是直接利用;第三是間接 利用(產生蒸汽、熱水和熱空氣)。余熱蒸汽的合理利用順序是:1)動力供熱聯 合使用;2)發(fā)電供熱聯合使用;3)生產工藝使用;4)生活使用;5)冷凝發(fā)電用。 余熱熱水的合理利用
24、順序是:1)供生產工藝常年使用;2)返回鍋爐使用;3)生活 用。余熱空氣的合理利用順序是:1)生產用;2)暖通空調用;3)動力用;4)發(fā)電 用。但是這不是絕對的,需要每個工廠根據自己實際生產條件和需要而定。 5.3.2工業(yè)硅冶煉中不同種類余熱的利用 在工業(yè)硅冶煉中所有能源供入項為電能和化學反應能,能源支出項為氧化物 還原、金屬硅潛熱、逸出氣體、爐面、爐體、短網、冷卻水帶走熱。由于國內外 在電能節(jié)約方面硏究得比較多和透切,U前工業(yè)硅冶煉電效率基本都在92%以 上。但是,電能最終要轉變?yōu)闊崮懿攀欠磻璧?,而從?-1可知,礦熱爐冶 煉系統的熱效率一般僅有60-70%,因此,整個冶煉系統能源利
25、用效率都低于 70%,這樣大量的熱被逸出氣體、爐面、爐體、短網、冷卻水、金屬硅所帶走和 散失。 從表5-1可知,金屬硅帶走的熱占熱量總供入量的5.98%,即269456千卡/h。 這部分熱是以金屬硅潛熱形式存在,硅液1600-1800C,硅錠為常溫20-30C, 其熱具有間斷性(出硅前后)、釋放緩慢性,存在能量密度低、不便于接觸、不 便于引出等特點。在U前經濟技術條件下,金屬硅的潛熱只能以熱輻射與對流的 方式將這部分熱引導出來,其可能的利用方式為烘干物料、預熱物料、加熱洗澡 用水(該余熱每小時能使2. 7噸水從0C升到100C)、加熱生活用水。 爐面損失的熱占總熱量的5.97%,即2693
26、3千卡/h,與金屬硅帶走的熱相當。 這部分熱總量大、能流持續(xù)平穩(wěn)、密度小,主要以熱輻射與對流形式損失,但是 由于在爐口損失,受制于場地無法加以再利用,只能想辦法減少其損失。節(jié)約辦 法是爐型密閉化、控制料面溫度、料面燃燒狀況、厚料操作與防止刺火大量、多 次發(fā)生。 爐體損失的熱占總熱量的3.69%,即166448千卡/h這部分熱與料面損失 的熱性質相同,它以熱傳導形式損失,利用也很困難,也只能想辦法減少其損失。 減少辦法是加強爐體隔熱性能。 短網損失的熱占總熱量的7.47%,即336738千卡/h。這部分熱主要損失在 電纜、銅瓦、電極對外熱輻射上,數量很大,但是受制于場地、能流密度小等限 制,
27、也是無法利用的熱損,只能想辦法減少。減少辦法就是縮短短網,使用適當 電流冶煉,選用制造后導電性能好的短網。注意不能使用保溫材料包裹的辦法, 這樣會適得其反。 冷卻水帶走的熱占總熱量的16.46%,即750000千卡/h。這部分熱產生于變 壓器、電纜母線、銅瓦,是種功能用水,一般要求入口 20-30C,出口 30-40C, 水在循環(huán)池中來回循環(huán)使用,所以冷卻水帶走的熱量雖然很大,但是不能夠被利 用。這部分熱可以想辦法減少,具體措施為:1)變壓器方面要求硅鋼片性能好, 材料、制造都要選技術好的廠家來做。減少短網閃變,避免過大電流操作。2) 電纜母線方面要求選用材料熱阻小并要求制造水平高的廠家來生
28、產,盡量減少電 纜布置長度,避免過大電流操作。3)銅瓦基本要求也如此,要求使用鍛造工藝制 造。 逸出氣體(煙氣)帶走的熱量占總熱量的18.35%,即826633千卡/h。煙氣 從爐內部產生,透過料面以后,溫度在400-600C, 6300KVA的礦熱爐煙氣流量 為4-8萬NM3/h,煙氣成分為N,、0:、CO,、比0及少量其他氣體。以往國內企業(yè)大 多數直接排放,不僅污染了環(huán)境,而且造成能源損失。近年來在環(huán)保部門要求下, 各企業(yè)相繼安裝了布袋除塵器。煙氣在進入布袋除塵器之前溫度必須降到120C 以下,降溫措施為混風冷卻、空冷、水冷,部分企業(yè)的水冷方式產生的熱水被用 于生產(洗原料、解凍)或生活
29、(洗澡、洗碗),但是混風方式占多數,空冷也 有少量,它們吸收或交換的熱都被再次損失掉。從當前煙氣處理來看,煙氣余熱 都沒有得到利用或很好的利用(利用價值不高)。 5. 3. 3工業(yè)硅冶煉中煙氣余熱的利用 煙氣余熱利用是余熱種類當中最便于利用的一種形式,一般煙氣具有較高的 溫度,流量較大,攜帶的熱量較多,回收利用方便(用對流換熱即可回收),不 受場地限制,轉換容易(轉換為蒸汽)。因此,對煙氣的余熱回收應好好的珍惜 與做文章。煙氣余熱回收得到的能量利用方向為生產用與主活用或者是二者聯合 使用。生產用一是為本工藝流程服務如預熱物料、解凍,二是為其他工藝服務如 余熱發(fā)電、烘干其他物料、加熱其他產品
30、或是二者的復合。生活用一是洗澡洗碗, 二是供暖制冷或是二者的復合。 在這里,我提出二種工業(yè)硅冶煉系統煙氣余熱利用方案:一是余熱發(fā)電綜合 利用方案,二是余熱加熱配套產品綜合利用方案。 5.33.1煙氣余熱發(fā)電綜合利用方案 從一臺6300KVA工業(yè)硅礦熱爐中逸出的煙氣流量為4-8萬NM*h,煙氣溫 度為400-600C, 400C煙氣比熱為1.12kJ/kgC,密度1.295 kg/Nm3,煙氣相對 于 300C時含熱量= CpX p X AT=1.12X4X 1.295X100=580.16 萬 KJ/h=1381333 千卡/h,此熱量能使13.8噸水從0C升到100 C,能使得5.5噸
31、水從40 C fl-到290C (此為蒸汽發(fā)電要求過熱溫度)。根據青島4308廠提供的BN型汽輪機技術參數: 進汽壓力0.35?0.7Mpa,進汽溫度250-290C,排汽壓力0.15Mpa,抽汽壓力0.5Mpa, 則發(fā)電量可達lOOOKWo由此計算,設電價0.5元/度,則一年(7000小時)發(fā) 電可創(chuàng)造經濟效益350萬元。 為實現煙氣余熱發(fā)電,需要投資余熱鍋爐2臺30萬、汽輪機1臺20萬、 發(fā)電機組1臺20萬、變壓器2臺40萬、控制柜若干100萬左右,總投資210 萬左右,承上述計算7個月即可收回投資。 對于上規(guī)模企業(yè),如有2臺以上6300KVA工業(yè)硅礦熱爐或者多臺12500KVA 工業(yè)
32、硅礦熱爐,則上馬煙氣余熱發(fā)電項忖更有價值與必要。因此,國內投資者應 盡快打消煙氣余熱利用是微不足道且費事的念頭,重視余熱利用與投身國家能源 節(jié)約行動當中。 按照上述煙氣余熱發(fā)電規(guī)劃,已經被利用過的煙氣從余熱鍋爐出來后,溫 度仍然有300C,由于溫度較低,其熱能品位降低,利用難度加大。為充分利用 好能源,提高能源利用效率,根據煙氣余熱梯級利用原理,其熱量可以被用來產 生余熱鍋爐補汽。但是從補汽鍋爐出來的煙氣溫度仍然有200C左右,這部分煙 氣仍包含熱量,對此,這部分熱量可以用來產生熱水用于預熱物料、解凍(北方 地區(qū))、洗澡、洗碗用,然后被冷卻到120C以下的煙氣可以符合標準的進入布 袋除塵器進
33、行處理。整個煙氣余熱發(fā)電綜合利用方案系統示意圖如圖5-5o O|)C 仁400 C煙厲2?余熱鍋爐3?300 C煙氣4、補汽鍋爐5、200C煙氣6、換熱器7. 100*C煙氣S.布袋除塵藩9、可排放煙氣10、循環(huán)水 11> 80X?熱水12.旗熱解凍13、洗澡洗碗14、2(FC補水15、150C補汽16、290C蒸汽17.汽輪機1S,變19>變爪曙2 20、用戶 圖5?5煙氣余熱發(fā)電綜合利用方案系統示意圖 該方案從能源利用與工藝角度來講,它能源利用比較充分,能源利用率高, 出口煙氣溫度能立即達到布袋塵除塵器的要求,不需要列外投資降溫裝置,工藝 配合性好。但是從經濟性角度來考慮,
34、也許還有更好的方案。 5.3.3.1煙氣余熱加熱配套產品綜合利用方案 工業(yè)硅礦熱爐煙氣寓含的大量熱量可以實現多種用途,除了發(fā)電之外,實際 上,電還只是一種低附加值產品(3600KJ熱量換成電為1度,產值為0.5元, 而曲于H前蒸汽發(fā)電效率為30-45%左右,所以要10000KJ熱量才換回0.5元)。 大家往往局限于原有的思維,一想到余熱利用就是發(fā)電、預熱產品、制冷供暖、 燒水洗澡,對于開拓創(chuàng)新利用余熱研究不夠。 我的看法是要用熱來轉換為另外一種產品,轉換形式并非一定是從一種能源 產品到另外一種能源產品,可以是一種能源產品到另外一種物質產品,只要該物 質產品能與熱存在一定的聯系。對于煙氣余
35、熱而言,就是要尋找到一種與這種中 溫、低溫熱能想適應的物質產品。這種產品在化工、輕紡等領域廣泛存在,例如 塑料生產、造紙、紡織、有色金屬蒸汽浸出等。另外要解放的一個思想是我本來 是生產工業(yè)硅的,如果我為了利用余熱而去生產另外一個物質產品造成投資過大 或不應有的多元化生產造成的精力分散問題。其實,生產該種產品如果叫投資過 大,則可以貸款融資解決(因為你本業(yè)已經立下基礎,當地貸款應該不會再成問 題,也可通過股東融資比例分配來解決),如果生產該種產品帶來精力分散(主 要是市場開拓上的分散),這可以通過掛靠形式來解決(比如自己主動掛靠到該 種產品行業(yè)中一個大型或中型廠家,山它解決市場問題,自己只管生產
36、)?,F在 這個時代是合作時代,要把合作(其實是資源合理組配)放在觀念更新的笫一位。 當投資者到某地去投資時,該地已經存在一定工業(yè)基礎,則可以把廠建造在該廠 附近,為其提供煙氣余熱以生產該產品?;蛘呓Y合當地政府招商行為,與被招進 來的企業(yè)聯合投資,本廠產生的煙氣余熱成為合作伙伴的供熱基礎。或者先聯系 某類投資者(比如塑料廠投資者),跟他協商好,共同投資于某地,共孕煙氣余 熱去生產一種新產品。總之,作為投資者應當在煙氣余熱問題上要全盤考慮,怕 麻煩的可以請研究所、行業(yè)專家、投資顧問、行業(yè)分析師代為考慮要結合產品的 具體類型。 5.4隔熱技術研究 在工業(yè)生產中節(jié)能渠道基本分為三大類。第一類是先進
37、的技術工藝流程,第 二類是先進精良生產設備,第三類是優(yōu)良的節(jié)能材料。在這里我將重點研究節(jié)能 材料在工業(yè)硅冶煉領域的應用,這是在工業(yè)硅冶煉領域近年較少涉及與更新的方 面,已經與新材料、新技術不斷更新的今天不相適應。 節(jié)能材料主要體現在材料的隔熱(絕熱)性能上,對于工業(yè)硅冶煉系統而言, 材料隔熱性能好壞直接影響到礦熱爐的熱效率。從表5-1可見,從礦熱爐爐體散 發(fā)的熱損失為166448千卡/h,占總熱量收入項的3.69% (這還是較低的,國內 大部分為6-8%),與國外相比存在1-2倍的差距。這主要是因為我國工業(yè)硅礦熱 爐爐體結構與材料通常是工作層用碳磚(上部用耐火磚),保溫層用耐火磚,絕 熱層用
38、石棉板或硅酸鋁纖維毯,保護層(爐殼)用鋼板的原因。這種結構和材料 構成在今天看來已經不合理(但許多單位缺乏設計能力,仍在使用),原因一方 面是我國礦熱爐使用的材料導熱系數大,隔熱性能差,另一方面山于在筑爐時沒 有對材料結構進行合理設置,在同樣大小導熱系數材料條件下隔熱效果也不理 想。因此,為提高礦熱爐熱效率而對礦熱爐爐體的結構和用材進行改革在LI前相 當必要。 改革開放以前,我國筑爐材料的品種非常單一,基本以天然礦物質加工制品 為主,工業(yè)硅礦熱爐筑爐時工作層主要是碳磚,保溫層主要是粘土磚,絕熱層主 要是硅藻土、石棉板,而且各材料的適用性能也比較落后。隨著節(jié)能、降低成本、 新技術的應用、其他領
39、域對材料的特定要求,我國科研人員在吸收消化國外材料 制造技術與經驗的基礎上,積極自主創(chuàng)新,發(fā)展研究了一大批筑爐材料如陶瓷纖 維、納米微孔隔熱材料、多層復合反射絕熱板、漂珠高強隔熱磚等。無論從高科 技的航天器、小到手中的保暖杯,人們都對材料的導熱性能、強度要求等方面進 行了廣泛的研究和改進,直至今日,筑爐材料品種已大大得到豐富、產品的性能 已得到大大提高,生產工藝不斷進步、品種不斷更新,材料發(fā)展逐漸走上科學精 細發(fā)展的道路。在工業(yè)硅礦熱爐筑爐中,我們應當積極應用當代科技成果,與時 俱進地革新改進礦熱爐的工作性能。 表5-2、表5-3、表5-4分別列出了當今工業(yè)硅礦熱爐筑爐時可供選用的工作 層、
40、保溫層、隔熱層與絕熱層用材。 49 百度文郵-讓每個人平零地捉升口我 表5?2當今工業(yè)硅礦熱爐筑爐時可供選用的工作層用材 名稱 2kgf/cm2 荷 重軟化點(C) 使用溫度 (C) 常溫耐壓強 度(kgf/cm2) 熱導率 (w/m?C) 熱膨脹系數(C) X 10( 硅磚 1520-1620 1600-1650 175-500 1.05+0.93t/1000 11.5-13 碳磚 2000 2000 250-500 23.26+3.49t/1000 3.7 石墨磚 1800-1900 2000 250 162.8-40.7t/
41、1000 5.2-5.8 碳化硅 磚 1500-1700 1600 550-750 14.2(600^) 11.9(800C) 10.9(10004C) 4.76 表5?3當今工業(yè)硅礦熱爐筑爐時可供選用的保溫層(堅固層)用材 名稱 密度(g/cirP ) 使用溫度 (C) 常溫耐壓強度 (kgf/cm2) 熱導率 (w/nrC) 粘土磚 2.07 1400 150-300 0.18-0.60 髙鋁磚 1500 390-490 1.4 剛玉磚 3.20 1700 200-700 0.70-1.50 硅磚 1.9 160
42、0-1650 175-500 1.05+0.93t/1000 碳化硅磚 2.4-2.5 1600 550-750 14.2(600C) 11 ?9(800C) 10.9(1000 C) 剛玉莫來石 磚 1.54.7 1800 200-500 0.35-0.80 普通型耐火 澆注料 2.0 1400 295 1.17-2.80 輕質隔熱磚 0.4-1.5 1400 9.8-59 0.25-0.70 高鋁質隔熱 耐火磚 0.4-1.5 1400 840 0.20-0.50 注:堿性耐火材料如鎂磚、鎂鋁磚、白云石磚、鎂珞磚、鎂橄欖右磚、氧化
43、鈣質磚等不能用 于工業(yè)硅礦熱爐。 表5?4當今工業(yè)硅礦熱爐筑爐時可供選用的隔熱層與絕熱層用材 名稱 導熱系數w/m.k 比重kg/m3 使用溫度C 石棉板 0.1-0.423 1100 1700 0.13-0.15 <1300 600 硅酸鋁纖維毯 0.09-0.16 128 1200 復合硅酸鋁纖維輕 0.036-0.092 45-100 600 硅藻土 0.13-0.40 500-700 1000 膨脹珍珠巖 0.447-0.07 40-500 800 蛭石 0.046-0.07 80-900 1100 泡沫玻璃
44、<0.058 155-200 450 泡沫石棉 <0.035 20-22 500 微孔硅酸鈣 0.065-0.13 140-270 1000 礦渣棉 0.048-0.14 77-160 650 巖棉制品 0.026-0.035 80-150 700 玻璃棉 0.043-0.11 48 350 陶瓷纖維毯 0.08-0.29 2600 1260-1600 空心微珠 0.028-0.054 50-200 800 納米微孔隔熱材料 0.025-0.038 400-500 1000 各種反射涂料 0.03,80-90% 的 反
45、射 率 450-1500 150-1800 表5-2、表5-3、表5-4中,有許多是上世紀80年代后開發(fā)制造出來的材料, 材料品種與性能與其80年代前有很大的改變,例如高鋁磚是德國奧托焦炭公司 1956年前后開發(fā)出來的,其強度與導熱系數與今天高鋁磚的性能相距較遠,當 時其高鋁磚作為煉焦爐槍其強度較松散,承受壓力大約為100-200 kgf/cm2,導 熱系數為3.47 w/m-Co硅酸鋁纖維毯作為廣泛應用的爐體保溫材料,我國1971 研制成功,到1990年代前,其品種單一,性能也不好,但是現在生產企業(yè)200 家左右,總生產能力超過4萬噸/年,品種繁多,包括普通硅酸鋁纖維、高純硅 酸鋁
46、纖維、高鋁纖維、多晶莫來石纖維、多晶氧化鋁纖維和多晶氧化誥纖維等。 空心微珠保溫材料是另一種最近開發(fā)出來的保溫材料,它是一種以電廠粉煤灰微 珠和膨脹珍珠巖為基料,配以專用粘結劑,經高溫燒結后制成的輕質成型料。據 近年來國內外文獻報道,粉煤灰中的一種空心微珠是在粉煤燃燒時,在爐溫超過 1350-1500C的高暖區(qū)域內產生的一種中空球形圓珠,其內部包含有氮和二氧化 碳等氣體,其表面耐磨性好,壓強高,并有很好的耐酸性,是一種新興的多功能 材料。經試驗研究表明,空心微珠具有顆粒小、質輕、中空、隔音、隔熱、耐高 溫、絕緣、耐低溫、耐磨、強度高等優(yōu)異的多功能特性。另外現代筑爐與建筑還 廣泛使用薄層隔熱保溫
47、材料一一反射絕熱涂料。上世紀90年代,美國國家航空航 天局的科技人員為解決航天飛行器的傳熱控制問題開發(fā)了一種太空絕熱瓷層 (Therma-Cover),我國于2001年也開發(fā)成功,在現代筑爐中已經開始廣泛使用。 這種材料山一些懸浮于惰性乳膠中的微小陶瓷顆粒構成,具有高反射率、高輻射 率、低導熱系數、低蓄熱系數等熱工性能,只要在表面噴涂0. 3-0. 5毫米涂層, 就能有效抑制露天常溫物體受太陽輻射熱和紅外輻射熱,抑制效率達90%左右。 科技進步為我們提供了更好的、更多的筑爐材料,我們必須切合順應當詢條件, 51 百度文庫?讓每個人平等地捉升口我 之間,導熱與承重性能都比較好,是
48、爐襯主要用材。 工業(yè)硅礦熱爐減少熱損失起關鍵作用的地方是隔熱層和絕熱層,因此,選擇 好隔熱材料與絕熱材料非常重要。工業(yè)硅礦熱爐隔熱層和絕熱層對材料的要求 是: 1、 導熱系數小。減少熱量損失,保證爐膛內溫度是隔熱層和絕熱層的主要 用途,只有導熱系數小,才能實現上述目的。 2、 彈性小。隔熱材料與絕熱材料一般是輕質、疏松、多孔的纖維狀材料, 膨脹收縮系數大,容易引起爐體松動,因此要求隔熱材料與絕熱材料收縮性小, 以保證保溫層與爐殼之間的嚴密性與整體性。 3、 能耐高溫。由于保溫層主要擔負骨架承受負荷用,它主要作用不是節(jié)能, 所以其外泄熱量相大,其冷面溫度也相當高,對緊貼其冷面的隔熱材料和
49、絕熱 材料來說,應半能夠耐受其高溫。 4、 價格便宜。 根據丄業(yè)硅礦熱爐隔熱層和絕熱層對材料的上述要求,可以選定納米微孔隔 熱材料作為隔熱層和絕熱層的用材。納米微孔隔熱材料是2000年以后我國相關 單位從美國引進并消化吸收后逐漸推廣應用起來的優(yōu)良隔熱、絕熱材料,它能耐 受較高的溫度,且導熱系數比通常用的隔熱材料、絕熱材料低1-4倍,節(jié)能效果 突出。如果為了強化保溫,還可以在納米微孔隔熱材料熱面噴涂某種反射涂料。 如果要求繼續(xù)使用硅酸鋁纖維毯,則應當使用硅酸鋁纖維毯+泡沫石棉或泡沫玻 璃或空心微珠結構,保溫效果將更好。 選用低熱導率的材料來增強保溫,是保溫方法的一種,砌筑時材料結構的合 理
50、設計也是一種重要的保溫方法。它包括材料厚度設計、材料間合理搭配使用、 材料使用位置三個方面的內容。好的結構設訃在同樣材料使用情況下,隔熱效果 與經濟性更好。 在材料厚度設計上,既要能保溫承重,同時使用量還要適當,才能保證經濟 性。材料過薄,起不到保溫承重效果,易折、易松動;材料過厚,雖然承重和整 體性增強,但是超過臨界厚度,保溫效果反而下降,同時造價也上去了。 在材料間合理搭配使用上,要注意材料使用溫度限制、材料導熱系數、材料 價格上的差異。使用溫度高的材料應當靠近高溫區(qū),在溫度一致情況下,導熱系 數低的應當在高溫區(qū)一側。材料合理搭配還能適當降低造價成本。 在材料使用位置上,在爐墻不同
51、位置應該使用不同材料,在溫度許可范圍內, 盡量選用導熱系數低、強度高、造價低的材料,在需要加強保溫措施部位應當考 慮追加絕熱材料的使用;對于容易腐蝕的出硅口位置,應當使用耐腐蝕的材料如 碳磚、碳化硅磚,而不是常規(guī)思路來安排材料使用;對于爐底基礎部位,在溫度 許可范圍內,應當選用強度高、導熱系數低、整體性好、造價低的材料。 有了上述研究基礎,用來指導礦熱爐爐體結構的設訃將才能真正的把隔熱技 術的作用發(fā)揮出來,制造出在國際上具有先進節(jié)能水平的礦熱爐。表5-5比較了 傳統爐體結構⑹)與按照上述思路設訃的爐體結構的隔熱性能。 表5-5傳統礦熱爐爐體結構與新設計的爐體結構隔熱性能的比較 項目 爐
52、墻內 表而溫 度(C) 爐殼鋼板 外表而溫 度 1 (C) 爐墻厚 度與結 構 爐壁熱 損失2 (kw) 爐底熱 損失3 (kw) 總損失 (kw) 節(jié)能差率 傳統爐襯結構 1420 178 圖5-5 69.78 27.17 96.95 0 新式爐襯結構 14201 137 圖5-6 43.74 17.33 61.07 37% 1注:取平均溫度。 2注:爐壁散熱而積、爐底散熱面積取該文中56.58m?、23.40 m?。 3注:計算方法同該文一致。 從表5?5和圖5?7可以看岀,新式爐襯結構不僅厚度少,而且爐體熱損失減 少37%,說明
53、研究總結出來的隔熱技術起到了明顯的作用。 53 百度文庫?讓每個人平等地捉升口我 圖2 爐襯佶構示適圖(改造后) L .鋼扳2.石棉根3?桂駅粘土杲富菸 4 f哇碳鋁殲維氈5 ?側部炭磚6?碑酸鋁混凝土 7 ?底謀沒苗8 ?底翩9 ?細硅石10?耐火沽土磚 表3 爐襯各部位嚴度(改造后)>mm 序V 幺 秣 : 爐墜 爐底 | 1 ??■?—??一? ? ? ? 制妖 ; B 15 2 石怖板 : 10 10 3 経質粘土保溫磚 ; 11S q 硅舷鋁纖雒若 5 20 5 他部炭磚 i *100 6
54、 磷酸鋁混彙土. - 41 7 底部淡磚 ! 1 SCO ?底?栩 S 80 9 細建石 〔技度 3 —Sittm) -14 10 ?;鹫惩链u j ? 230 750 11 ; 總厚度 1 8J0 1700 圖5-6傳統礦熱爐爐體結構 12 3 4 5 1、鋼板2、石棉板3、復合硅酸鋁纖維毯4.納米隔熱材料 5、粘土磚6、高鋁隔熱耐火磚7、廣|培炭磚 序號 名稱 爐璧厚度(mm) 爐底厚度(mm) 1 鋼板 14 14 2 石棉板 10 10 3 復合硅酸鋁纖維毯 10 0 4 納米隔熱
55、材料 10 10 5 粘土磚 240-760 240 6 高鋁隔熱耐火磚 120 240 7 自焙炭磚 400 800 合計 804 1304 圖5?7新式礦熱爐爐體結構 5.5結論 本章研究了工業(yè)硅冶煉過程中的能源節(jié)約技術,包括冶煉關鍵設備礦熱爐爐 體結構的設計、余熱利用方案研究、隔熱技術總計設計研究,從大的、主要的能 源節(jié)約方面進行了探索。 通過研究設計12500KVA大容量半密閉式工業(yè)硅礦熱爐,在爐體結構設計、 岀硅口設訃、爐門設訃、煙罩設計、隔熱技術等方面運用新技術,提高了礦熱爐 55 百度文郵-讓每個人平等地捉升口我 的性能水平,為高效利用能源打下了基礎和提供了實現方案。 通過余熱利用方案的研究,提出了二種新的余熱綜合利用方案,一是煙氣余 熱發(fā)電一鍋爐補汽一預熱物料一生活用水(洗澡、洗碗)梯級能源利用方案,二 是煙氣余熱加熱配套產品一生活用水綜合利用方案,為充分提高能源利用效率、 節(jié)約能源、降低企業(yè)生產成本提供了實現途徑。 通過隔熱技術的研究,總結了當今先進的隔熱材料,提出了在結構與材料方 面進行改善礦熱爐隔熱性能的思路,新設計出來的礦熱爐爐體結構隔熱性能優(yōu)于 傳統爐體結構30%以上。 #
- 溫馨提示:
1: 本站所有資源如無特殊說明,都需要本地電腦安裝OFFICE2007和PDF閱讀器。圖紙軟件為CAD,CAXA,PROE,UG,SolidWorks等.壓縮文件請下載最新的WinRAR軟件解壓。
2: 本站的文檔不包含任何第三方提供的附件圖紙等,如果需要附件,請聯系上傳者。文件的所有權益歸上傳用戶所有。
3.本站RAR壓縮包中若帶圖紙,網頁內容里面會有圖紙預覽,若沒有圖紙預覽就沒有圖紙。
4. 未經權益所有人同意不得將文件中的內容挪作商業(yè)或盈利用途。
5. 裝配圖網僅提供信息存儲空間,僅對用戶上傳內容的表現方式做保護處理,對用戶上傳分享的文檔內容本身不做任何修改或編輯,并不能對任何下載內容負責。
6. 下載文件中如有侵權或不適當內容,請與我們聯系,我們立即糾正。
7. 本站不保證下載資源的準確性、安全性和完整性, 同時也不承擔用戶因使用這些下載資源對自己和他人造成任何形式的傷害或損失。