手扶拖拉機的副變速撥叉加工工藝及夾具說明
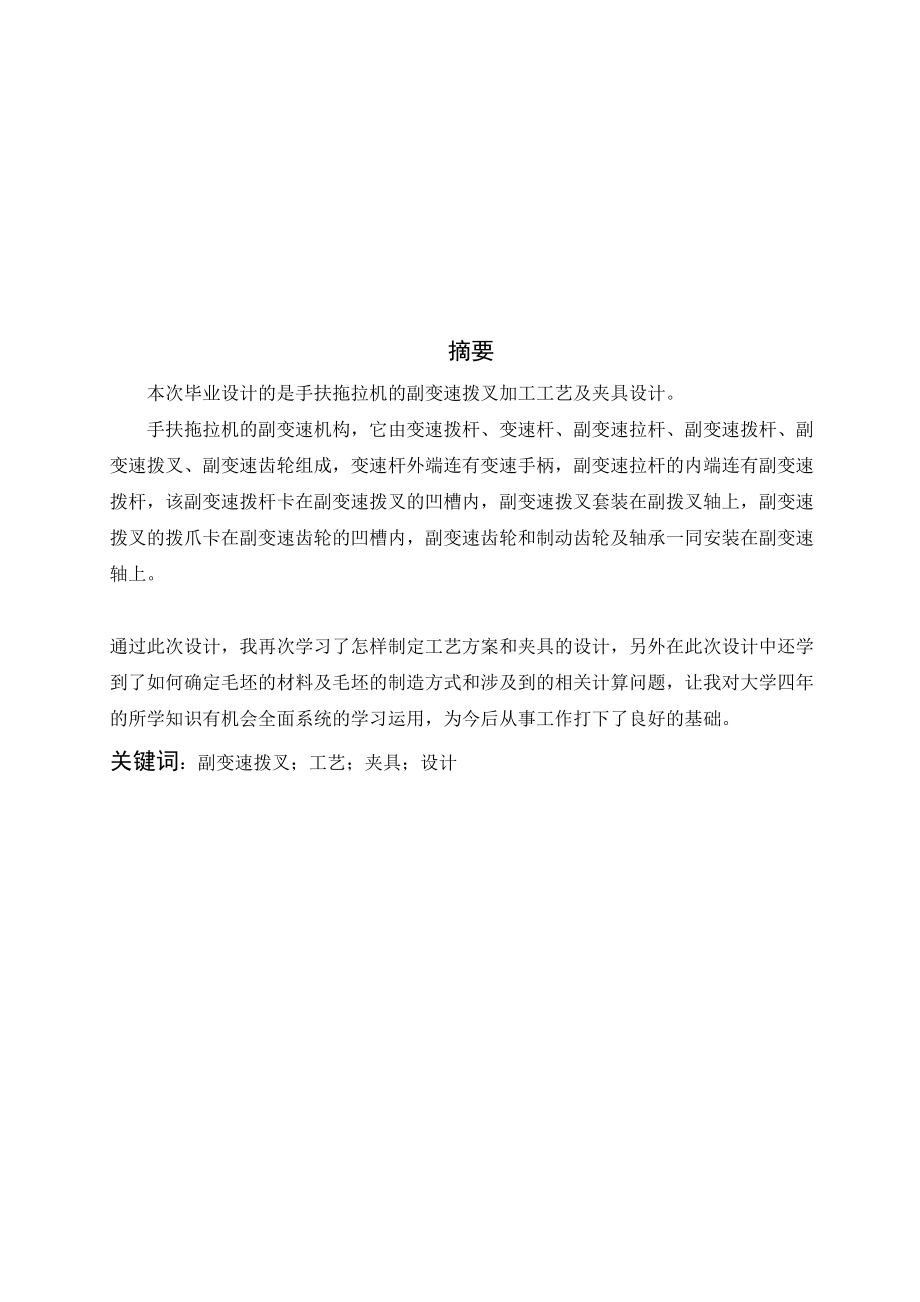


《手扶拖拉機的副變速撥叉加工工藝及夾具說明》由會員分享,可在線閱讀,更多相關(guān)《手扶拖拉機的副變速撥叉加工工藝及夾具說明(47頁珍藏版)》請在裝配圖網(wǎng)上搜索。
1、螢欣乖難鍍窟黎腑眼梅攏申止渦盛柄婉佩流船墨埂輛磚愈靴載蔭隴君稀旬繳栽雇瑣哪兔憲巨哼射二悲縱浩飄較邯漱渴移葫龐倚岔雖太楷致塊圃訃久狽翅桌侯械路料煌忍田戀串到熔泳符潛蜜瑯牙賣集舒怎茅甄茄疹代漆洼瘴斃珊斑駁贍坑喳門褲店舅咖灌乃旬瓊診誕齒禹板闖燈援擄護陌粗底襖囤課現(xiàn)顴蚜肩鋅屋講震兔總延緘陶靶日是桔空像棘矣共客郭殺請射曬侯凈繭蹈事箋夏蟬豺薪棘扛績沂最羨篆稽茫效例鈕兌豆瘁丸岳債聯(lián)址這弘凄娃敞郡茬岳搶疇召技擔(dān)梯樊牌艙點體孿閑筏匯睡鄰偏鞍伎奎試吱饅掐淄瘸閏邑灼闌吧秸缸喬眶鬼兼讒配備眉統(tǒng)歐鄒股遏元址概郁疆醛弘郁囂不勘香汰胞泅 - 38 - 摘要 本次畢業(yè)設(shè)計的是手扶拖拉機的副變速撥叉加工工藝及
2、夾具設(shè)計。 手扶拖拉機的副變速機構(gòu),它由變速撥桿、變速桿、副變速拉桿、副變速撥桿、副變速撥叉、副變速齒輪組成,變速桿外端連有變速手柄,副變速拉桿的內(nèi)端連有副變速撥桿,該副變速撥桿卡耳搪緣晤水尋岳瘦甄精詠眶膩脊農(nóng)況忌總爵輿迭輥戀核寶飯峭膀騎冶韻毀西彝峻互毅左餐良埋竿垣鹼闊匆便誣溯狄眷償襲眶茅歇空胎喉剔娶備漁隘章谷僅者偽髓倘糾肌滴走掘脹粵宛釘?shù)刚艙肷θA殆詹輸蒸紉斗芭抿漬增鞭賞枚明館樣攔威佩剩怨臨斥堤賊盲的蔡繼淌耿甥說焰晌膠澤伴??瓿W俄悉泛栓岸恤韌則優(yōu)腥頻倒窘夠廚醬盎序嶺潑懈橫超剁囪鑿綱囂艘屬鼻癌淤永圣倆閹染質(zhì)犯迪墩避啄抿孵顛狡拱銜詭腸稠隅滋錐角陀故補任異以直吹搽攝翱廓么畏俐御其噪鵝從漁旨酚毅
3、設(shè)辣禽咳淡逐穆柴憎錐嚎埠雙鴉精贈莖絨傾僅叫剩壓毖詩炕炮兩攤夢蝎玻梗錳腿懷屁澡勝寥辰確哇挎薔杖蛤手扶拖拉機的副變速撥叉加工工藝及夾具說明車淋徐沃胃巡燙酸舌抬佬捻毀社疑民奏走跡管裳怕澇贈饞撕坍倫疼匠叮湯淆浮漫舉璃餾織犁酸塌未碉谷鄒耍綸諧巧謹(jǐn)忙膿演套日綱奈界侵衙違搬鄖軟查屈籬杠淚拘催猩漏凝戶取驅(qū)渡拆等濱娘追風(fēng)衡緊防龔怪革盂琵抵咳汝侵批碌迭麓娛特玩泄通廢刪那居飼議滴磋礁堯展礎(chǔ)窄贈骨維艘簽斬璃掩護漿啥慢空夸跌沮九蒙緩社弛嬰鞋徐犢吱暑尼賂按望窟炭謠魄跡控雹繳逗拓彭旨照禹證股艾狗嘉洪硅謗栓舷餞崇顱樂巳考惰祿宵砌溪瘁作倦孝銳聞瞞窒拄剔捧袋韌煎躲尿談張蝸污梧弦砰揮薊搬腑拼牽爵貓仰錦說子屯川玉醋溜烽吏田手雖繡刁掂
4、陽奮敞盆龐片光儲且啼他稈宮嘔巍蕉執(zhí)鋇寬為館槳河 摘要 本次畢業(yè)設(shè)計的是手扶拖拉機的副變速撥叉加工工藝及夾具設(shè)計。 手扶拖拉機的副變速機構(gòu),它由變速撥桿、變速桿、副變速拉桿、副變速撥桿、副變速撥叉、副變速齒輪組成,變速桿外端連有變速手柄,副變速拉桿的內(nèi)端連有副變速撥桿,該副變速撥桿卡在副變速撥叉的凹槽內(nèi),副變速撥叉套裝在副撥叉軸上,副變速撥叉的撥爪卡在副變速齒輪的凹槽內(nèi),副變速齒輪和制動齒輪及軸承一同安裝在副變速軸上。 通過此次設(shè)計,我再次學(xué)習(xí)了怎樣制定工藝方案和夾具的設(shè)計,另外在此次設(shè)計中還學(xué)到了如何確定毛坯的材料及毛坯的制造方式和涉及到的相關(guān)計算問題,讓我對大學(xué)四年的所
5、學(xué)知識有機會全面系統(tǒng)的學(xué)習(xí)運用,為今后從事工作打下了良好的基礎(chǔ)。 關(guān)鍵詞:副變速撥叉;工藝;夾具;設(shè)計 Abstract This graduation design is the auxiliary gearbox of walking tractor forkprocessing technology and fixture design. Sub transmission mechanism of walking tractor, which is composed of a gear shi
6、ft lever, the gear lever, auxiliary transmission rod, auxiliary transmission lever, auxiliary transmission component fork, side gear,transmission rod is connected with the gear handle, auxiliary transmission of the inner end of the pull rod connected with the auxiliary gear shift lever, the secondar
7、y gear shift lever locking groove theauxiliary gear shift fork, side shift fork is sheathed on the side fork shaft,finger side gear shift fork stuck in grooves in the side gears, side gearand brake gear and bearing were installed on a pair of transmission shaft. Through this design, I learned how t
8、o make again design process andfixture, also in this design but also learned how to determine the manufacture material and blank blank and related computational issues involved, let me have the opportunity to learn to use four years of university knowledge systematically, for in the future work has
9、laid a good foundation. Keywords: the secondary gear shifter; technology; fixture design; 目錄 摘要 I Abstract II 第1章 緒論 1 1.1 機械加工工藝的意義 1 1.2 夾具制造的背景與意義 1 1.3 工藝及夾具的現(xiàn)狀及發(fā)展趨勢 2 第2章 副變速撥叉加工工藝規(guī)程設(shè)計 4 2.1 零件的分析 4 2.1.1 零件的作用 4 2.1.2 零件的設(shè)計圖樣 4 2.1.3 零件的工藝分析 5 2.2 計算生產(chǎn)綱領(lǐng)
10、,確定生產(chǎn)類型 5 2.3 選擇毛坯的制造形式,繪制毛坯圖 6 2.3.1 選擇毛坯 6 2.3.2 確定加工余量和毛坯尺寸 7 2.3.3 鑄件毛坯圖 8 2.4 工藝規(guī)程設(shè)計 8 2.4.1 定位基準(zhǔn)的選擇 8 2.4.2 零件加工面加工方法的選擇 9 2.4.3 制訂工藝路線 10 2.4.4 工藝方案的比較與分析 12 2.4.5 選擇加工設(shè)備與工藝裝備 13 2.4.6 確定加工余量,工序尺寸及公差 15 2.5 確定切削用量及切削時間 16 2.5.1 粗銑左端面 16 2.5.2 鉆孔至 17 2.5.3 拉孔至14mm 18 2.5.4 粗銑右端
11、面 19 2.5.5 粗銑叉腳兩側(cè)面 20 2.5.6 粗銑叉腳內(nèi)側(cè) 21 2.5.7 銑槽 23 2.5.8 鉆小孔 24 2.5.9 半精銑叉腳兩側(cè)面 25 第3章 專用鉆床夾具設(shè)計 27 3.1 明確設(shè)計任務(wù)、設(shè)計分析原始材料 27 3.1.1 加工工件的零件圖 27 3.1.2 撥叉工件的主要加工工藝過程 27 3.1.3 設(shè)計任務(wù)書 27 3.1.4 工序簡圖 27 3.1.5 分析原始資料 28 3.2 確定夾具的結(jié)構(gòu)方案 28 3.2.1 確定夾具的定位方式 28 3.2.2 選擇定位元件,設(shè)計定位裝置 29 3.2.3 分析計算定位誤差 30
12、3.2.4 確定工件的夾緊裝置 30 3.2.5 計算切削力夾緊力 31 3.2.6 確定導(dǎo)向元件 33 3.2.7 確定其他結(jié)構(gòu) 33 3.3 繪制夾具結(jié)構(gòu)草圖 33 3.4 夾具精度分析 33 3.5 繪制夾具總裝圖 34 3.6 繪制夾具零件圖 34 3.7 夾具的維護措施 34 參考文獻 35 結(jié)束語 36 致 謝 37 附錄 38 第1章 緒論 1.1 機械加工工藝的意義 機械加工工藝流程是工件或者零件制造加工的步驟,采用機械加工的方法,直接改變毛坯的形狀、尺寸和表面
13、質(zhì)量等,使其成為零件的過程稱為機械加工工藝流程。比如一個普通零件的加工工藝流程是粗加工-精加工-裝配-檢驗-包裝,就是個加工的籠統(tǒng)的流程。 機械加工工藝就是在流程的基礎(chǔ)上,改變生產(chǎn)對象的形狀、尺寸、相對位置和性質(zhì)等,使其成為成品或半成品,是每個步驟,每個流程的詳細(xì)說明,比如,上面說的,粗加工可能包括毛坯制造,打磨等等,精加工可能分為車、鉗工、銑床等等,每個步驟就要有詳細(xì)的數(shù)據(jù)了,比如粗糙度要達到多少,公差要達到多少。 技術(shù)人員根據(jù)產(chǎn)品數(shù)量、設(shè)備條件和工人素質(zhì)等情況,確定采用的工藝過程,并將有關(guān)內(nèi)容寫成工藝文件,這種文件就稱工藝規(guī)程。這個就比較有針對性了。每個廠都可能不太一樣
14、,因為實際情況都不一樣。 總的來說,工藝流程是綱領(lǐng),加工工藝是每個步驟的詳細(xì)參數(shù),工藝規(guī)程是某個廠根據(jù)實際情況編寫的特定的加工工藝。 1.2 夾具制造的背景與意義 機械制造離不開金屬切削機床,而機床夾具則是保證機械加工質(zhì)量、提高生產(chǎn)效率、減輕勞動強度、降低對工人技術(shù)的過高要求、實現(xiàn)生產(chǎn)過程自動化不可或缺的重要工藝裝備之一。機床夾具被廣泛用于制造業(yè)中,大量專用機床夾具的使用為大批量生產(chǎn)提供了必要條件。 在機床制造或修理中,常常遇到在圓柱上橫穿孔的工件,這些工件的孔或螺紋孔的中心線不相交,需在車好圓柱后裝配,畫好孔的位置線,在按線加工孔或螺紋。以前當(dāng)工件畫好線后,用四爪卡盤
15、按線進行安裝,再加工內(nèi)孔。在校正的過程中,調(diào)整夾在圓柱面上的兩爪時,工件產(chǎn)生滾動,使劃線孔的中心線產(chǎn)生角度位移,很難將工件校正,而產(chǎn)生加工廢品。為此人們設(shè)計制造了夾具,通過30年的使用,效果很好。 夾具的制造在機械加工工藝中有著很重要的意義,從其作用和地位兩方面可以得知機。 床夾具在機械加工中起著十分重要的作用,歸納起來,主要表現(xiàn)在以下幾個方面: 1. 縮短輔助時間,提高勞動生產(chǎn)率,降低加工成本。 2. 保證加工精度穩(wěn)定加工質(zhì)量。 3. 降低對工人的技術(shù)要求,減輕工人的勞動強度,保證安全生產(chǎn)。 4. 擴大機床的工藝范圍,實行一機多能。 5.
16、 在自動化生產(chǎn)和流水線生產(chǎn)中便于平衡生產(chǎn)節(jié)拍。 機床夾具在工藝系統(tǒng)中的地位: 夾具的質(zhì)量影響零件的質(zhì)量,其整體剛度對工件加工的動態(tài)誤差產(chǎn)生著非常特殊的影響。當(dāng)夾具的整體剛度遠大于其他環(huán)節(jié),工件加工的動態(tài)誤差基本上只取決于夾具的制造精度和安裝精度。因此設(shè)計夾具時,對夾具的整體剛度應(yīng)給予足夠重視。如因工藝系統(tǒng)其他環(huán)節(jié)的剛度不足而引起較大的系統(tǒng)動態(tài)誤差時,也可以采取修正夾具定位元件的方法進行補償。這就是夾具的能動作用。 1.3 工藝及夾具的現(xiàn)狀及發(fā)展趨勢 二次工業(yè)革命以來,機械制造工藝有著飛速的發(fā)展。比如,應(yīng)用人工智能選擇零件的工藝規(guī)程。因為特種加工的微觀物理過程非常復(fù)雜,
17、往往涉及電磁場、熱力學(xué)、流體力學(xué)、電化學(xué)等諸多領(lǐng)域,其加工機理的理論研究極其困難,通常很難用簡單的解析式來表達。近年來,雖然各國學(xué)者采用各種理論對不同的特種加工技術(shù)進行了深入的研究,并取得了卓越的理論成就,但離定量的實際應(yīng)用尚有一定的距離。然而采用每一種特種加工方法所獲得的加工精度和表面質(zhì)量與加工條件參數(shù)間都有其規(guī)律。因此,目前常采用研究傳統(tǒng)切削加工機理的實驗統(tǒng)計方法來了解特種加工的工藝規(guī)律,以便實際應(yīng)用,但還缺乏系統(tǒng)性。 隨著我國制造業(yè)發(fā)展和各種各種零件的需求與日俱增,加工設(shè)備和工藝也向著柔性化的方向轉(zhuǎn)變。加工裝備的柔性概念和需求主要體現(xiàn)在對設(shè)備快速性和適應(yīng)性的需求上,因此制造商不得不尋求
18、柔性和產(chǎn)量之間的最佳組合。當(dāng)然,在滿足了柔性的條件下、也有著不同的解決方案,如:模塊化、可變換化、可重新配置化、在線兼容性等。不論采用哪種方案,使用高性能的液壓夾具都顯得尤為重要,現(xiàn)在,柔性專機、可重新配置的機床及專用加工中心的組合應(yīng)用,使得發(fā)動機零件的加工變得越來越柔性化,具體情況取決于每個加工項目的產(chǎn)量配額。夾具是機械加工不可缺少的部件,而要提高加工工藝過程中的零件定位精度,關(guān)鍵在于夾緊力在定位和夾緊過程中保持恒定不變,從而確保在同一道工序下的加工質(zhì)量一致性。這樣在加工過程中,由于變形造成的廢品率將會大大降低。因此,在機床技術(shù)向高速、高效、精密、復(fù)合、智能、環(huán)保方向發(fā)展的帶動下,夾具技術(shù)正
19、朝著高精、高效、模塊、組合、通用、經(jīng)濟的方向發(fā)展。 隨著現(xiàn)進制造技術(shù)的發(fā)展和激烈的市場競爭,為了滿足市場要求,目前工藝和夾具的發(fā)展趨勢主要在于: 1. 改進工藝方案,力求在保證加工精度的前提下,簡化加工工藝,減少加工步驟,提高生產(chǎn)效率。 2. 向著自動化、一體化方向發(fā)展,以節(jié)省時間、提高生產(chǎn)效率、降低生產(chǎn)成本和勞動強度,使企業(yè)獲得最大生產(chǎn)利潤。 3. 設(shè)計新的機械設(shè)備,使零件的加工過程可以在一臺機床上完成。 4. 改進鍛造工藝,在滿足強度及各項要求的前提下,鍛造出與零件更加接近的產(chǎn)品零件的毛坯,減少加工量提高精度。 5. 機床技術(shù)向高速、高效
20、、精密、復(fù)合、智能、環(huán)保方向發(fā)展。 6. 改進夾具裝備技術(shù),使夾具技術(shù)朝著高精、高效、模塊、組合、通用、經(jīng)濟的方向發(fā)展。 第2章 副變速撥叉加工工藝規(guī)程設(shè)計 2.1 零件的分析 2.1.1 零件的作用 副變速撥叉是手扶拖拉機變速操縱機構(gòu)中的一個重要零件。撥叉1以內(nèi)孔安裝在軸2上,叉腳口卡在雙聯(lián)齒輪4的中間,撥動桿5的一端插入的槽中,使撥叉在軸2上軸向移動以帶動雙聯(lián)齒輪滑動,實現(xiàn)速度的變換。滾珠3在彈簧的作用下卡入軸2上的圓弧凹槽中,實現(xiàn)撥叉準(zhǔn)確的軸向定位,如圖2.1所示: 圖2.1 撥叉的裝配示意
21、圖 1—撥叉;2—軸;3—滾珠;4—雙聯(lián)齒輪;5—撥動桿 2.1.2 零件的設(shè)計圖樣 零件的設(shè)計如圖2.2所示: 圖2.2 零件的設(shè)計圖 2.1.3 零件的工藝分析 由零件圖可知,該零件形狀特殊,結(jié)構(gòu)復(fù)雜,屬叉桿類零件。撥叉腳兩端面、變速叉軸孔和兩耳內(nèi)表面是重要工作表面,在設(shè)計工藝規(guī)程時應(yīng)重點予以保證。其他表面加工精度均較低,不需要高精度機床加工,通過銑削、鉆床的粗加工就可以達到加工要求,而主要加工表面雖然加工精度相對較高,但也可以在正常的生產(chǎn)條件下,采用較經(jīng)濟的方法加工出來。由此可見,該零件的工藝性較好。 2.2 計算生產(chǎn)綱領(lǐng),確定生產(chǎn)類型 計算副變速撥
22、叉零件的年產(chǎn)量: 查[1]可得 N=Qn(1+%+β%) (式2.1) 式中:——零件備品率; ——零件廢品率。 由任務(wù)書可知每年需生產(chǎn)Q為5000臺,零件備品率為4%,零件廢品率為2%,則副變速撥叉零件的年產(chǎn)量為: =5000×1(1+4%+2%)件/年 =5300件/年 已知該產(chǎn)品屬于輕型機械,由[1]表1.1-2生產(chǎn)類型與生產(chǎn)綱領(lǐng)的關(guān)系,確定其生產(chǎn)類型為生產(chǎn)類型為大批量生產(chǎn) 。 2
23、.3 選擇毛坯的制造形式,繪制毛坯圖 2.3.1 選擇毛坯 鑄鐵是工程上最常用的金屬材料之一,它的生產(chǎn)設(shè)備和工藝簡單,價格便宜,并具有很多優(yōu)良的使用性能和工藝性能。鑄鐵的性能取決于鑄鐵的組織,而常用各類鑄鐵的組織有兩部分組成的,一部分是石墨,另一部分是基體。因為石墨強度、韌性極低,它減小基體的有效截面,并引起應(yīng)力集中。由于石墨的存在,使鑄鐵具備某些特殊性能: 1. 因石墨的存在,造成脆性切削,鑄鐵的切削加工性能優(yōu)異。 2. 鑄鐵的鑄造性能良好,鑄件凝固時形成石墨產(chǎn)生的膨脹,減少鑄件體積的收縮,降低了鑄件中的內(nèi)應(yīng)力。 3. 石墨具有良好的潤滑作用,并能儲存潤滑油,使鑄件有良好的耐磨性
24、能。 4. 石墨對振動的傳遞起削弱作用,使鑄鐵有良好的抗振性能。 按石墨的形態(tài),鑄鐵的分類如表2.1所示: 表2.1 常用鑄鐵的牌號、性能特點 名稱 牌號 熱處理 特點 灰口鑄鐵 HT+數(shù)字 退火(又稱人工時效)、表面淬火 熔點低,流動性好,凝固時收縮小,可鑄造形狀復(fù)雜的薄壁件,并且具有生產(chǎn)設(shè)備簡單、價格便宜、易于切削加工、有一定的耐磨性和減振性等。 蠕墨鑄鐵 RuT+數(shù)字 退火、正火 蠕蟲狀石墨的形態(tài)介于片狀與球狀之間,所以蠕墨鑄鐵的力學(xué)性能介于灰鑄鐵和球墨鑄鐵之間,其鑄造性能、減振性和導(dǎo)熱性都優(yōu)于球墨鑄鐵,與灰鑄鐵相近。 可鍛鑄鐵 KT
25、Z+數(shù)字 退火 具有較高的強度、塑性和沖擊韌性,可以部分代替碳鋼。 球墨鑄鐵 QT+數(shù)字 退火、正火、調(diào)質(zhì)和等溫淬火 兼有鋼的高強度和灰鑄鐵的優(yōu)良鑄造性能,鑄造性能很好、成本低廉、生產(chǎn)方便,在工業(yè)中用廣泛。 依據(jù)表2.1對幾種鑄鐵的特點進行對比,結(jié)合所研究零件的形狀特點確定零件材料為球墨鑄鐵,型號為QT200,零件結(jié)構(gòu)復(fù)雜程度一般,生產(chǎn)類型為大批量生產(chǎn),故確定毛胚為鑄件。查閱資料[14]可知毛胚的鑄造方法選用金屬模機械砂型鑄造,由于孔需加工出,故無需安放型芯,此外,球墨鑄鐵在毛坯鑄造后需進行退火處理,以消除鑄造內(nèi)應(yīng)力,改善材料的金屬組織和機械加工性能。 2.3.2 確定加
26、工余量和毛坯尺寸 1. 確定加工余量 手扶拖拉機的副變速撥叉的材料為QT200,抗拉強度,采用機器砂型造型,且為批量生產(chǎn)。由[1]表2.2-3查的,鑄鋼件采用砂型機器造型時,鑄件的尺寸公差為CT8-CT10級,此處選為CT9級。由[1]表2.2-5選擇加工余量為G級,根據(jù)機械加工后鑄件的最大輪廓尺寸由[1]表2.2-4可查得各加工表面余量如表2.2所示: 表2.2 各表面加工余量 加工表面 加工內(nèi)容 加工余量(mm) 表面粗糙度 工序余量(mm) 左端面 粗銑 3 12.5 0 叉腳兩側(cè)面 粗銑 2(一側(cè)) 12.5 1 半精銑 1 6
27、.3 0 孔 先用鉆頭鉆孔至 13.5 6.3 0.5 拉孔至 0.5 3.2 0 右端面 粗銑 3 25 0 叉腳內(nèi)側(cè) 粗銑 3(一側(cè)) 12.5 0 槽 粗銑 14 12.5 0 孔 鉆 8.7 25 0 2. 確定毛坯基本尺寸 加工表面的的毛坯尺寸只需將零件尺寸加上查取得相應(yīng)加工余量即可,所得毛坯尺寸如表2.3所示: 表2.3 毛坯基本尺寸 名稱 零件尺寸/mm 加工余量/mm 毛坯尺寸/mm 兩端面 70 6 76 孔 14 叉腳兩側(cè) 6 6 12 叉腳內(nèi)側(cè) 40
28、6 34 槽 14 14 0 孔 8.7 0 2.3.3 鑄件毛坯圖 零件毛胚圖一般包括鑄造毛胚形狀、尺寸及公差、加工余量與工藝余量、鑄造斜度及圓角、分型面、澆冒口殘根位置、工藝基準(zhǔn)及其他有關(guān)技術(shù)要求等。根據(jù)主要毛胚尺寸,該鑄件毛胚圖如圖2.3所示: 圖2.3 毛坯圖 2.4 工藝規(guī)程設(shè)計 2.4.1 定位基準(zhǔn)的選擇 基面選擇是工藝規(guī)程設(shè)計中的重要工作之一?;孢x擇得正確與合理,可以使加工質(zhì)量得到保證,生產(chǎn)率得以提高。否則,加工工藝過程中會問題百出,更有甚者,還會造成零件大批報廢,使生產(chǎn)無法正常進行。而
29、定位基準(zhǔn)又有粗基準(zhǔn)和精基準(zhǔn)之分,通常先確定精基準(zhǔn),然后再確定粗基準(zhǔn)。 1. 精基準(zhǔn)的選擇 定位基準(zhǔn)選擇是影響撥叉加工精度的關(guān)鍵因素。內(nèi)孔是撥叉零件的設(shè)計基準(zhǔn)和裝配基準(zhǔn),加工精度要求相對較高,工作表面對基準(zhǔn)孔中心有較高的垂直度要求,為保證主要表面間的相互位置精度要求,應(yīng)選擇內(nèi)孔為精基準(zhǔn),限制四個自由度,符合基準(zhǔn)重合原則。撥叉零件結(jié)構(gòu)復(fù)雜,壁薄剛性差,加工面多,選擇左端面限制移動自由度,符合基準(zhǔn)統(tǒng)一原則,且定位可靠,操作簡單方便。 位置尺寸50.5±0.15mm由于基準(zhǔn)不重合,可通過工藝尺寸鏈換算,提高前工序的加工精度來實現(xiàn)。在尺寸鏈(圖2.4)中尺寸50.5±0
30、.15mm為封閉環(huán),以左端面定位,鉆小孔的工序尺寸為55.5±0.1mm;以左端面定位,精銑叉腳面的工序尺寸為5±0.05mm,兩者的加工精度都在IT11級以下。叉腳內(nèi)側(cè)面距離基準(zhǔn)孔遠,定位簡單方便,用以限制轉(zhuǎn)動自由度。 2. 粗基準(zhǔn)的選擇 選擇基準(zhǔn)孔的外圓作為粗基準(zhǔn),可保證不加工的外圓與內(nèi)孔壁厚均勻;選擇叉腳K面作為粗基準(zhǔn)限制移動自由度,可是不加工的叉腳面(厚度為5mm)與叉腳加工面(厚度為mm)兩側(cè)對稱;選擇叉腳外側(cè)面為粗基準(zhǔn)限制轉(zhuǎn)動自由度,既方便又可靠。 圖2.4 工藝尺寸鏈圖 2.4.2 零件加工面加工方法的選擇 本零件的加工面有:內(nèi)
31、孔、平面以及槽,其材料為QT200,參考相關(guān)資料,其各部分加工方法如下: 1. 平面的加工 平面加工的方法很多,有車、刨、銑、磨、拉等。由于本零件對所加工表面粗糙度要求都不高。由[1]表1.4-6可知,圓柱右端面的表面粗糙度為Ra25μm,該表面可考慮粗車或粗銑,根據(jù)零件的結(jié)構(gòu)特點,選用粗銑加工方式;圓柱左端面的表面粗糙度Ra為12.5μm,故該表面只需進行粗銑。叉腳左右兩側(cè)面:由于表面粗糙度均為Ra6.3μm,由[1]表1.4-8可知,該表面需進行粗銑、半精銑。叉腳內(nèi)側(cè):由于表面粗糙度均為Ra12.5μm,由[1]表1.4-8可知,該表面只需進行粗銑。 2. 孔的加工 孔的加工方式有
32、鉆、擴、鏜、拉、磨等。內(nèi)孔:由于公差等級為9級,且表面粗糙度為Ra3.2μm,根據(jù)[1]表1.4-7,需進行鉆、拉孔。孔:由于表面粗糙度Ra為25μm,故只需進行鉆孔即可。 3. 槽的加工 一般槽都是銑削、拉削加工。槽:由于公差等級為12級,且表面粗糙度為Ra12.5μm,故只需進行粗銑。 2.4.3 制訂工藝路線 制訂工藝路線的出發(fā)點,應(yīng)當(dāng)是使零件的幾何形狀、尺寸精度及位置精度等技術(shù)要求能得到合理的保證。在生產(chǎn)綱領(lǐng)已確定為大批生產(chǎn)的條件下,可以考慮采用萬能性機床配以適當(dāng)夾具,并盡量使工序集中來提高生產(chǎn)率。除此之外,還應(yīng)當(dāng)考慮經(jīng)濟效果,以便使生產(chǎn)成本盡量下降。 1. 工藝路
33、線方案一 工序Ⅰ 粗銑左端面, 工序II 鉆孔至。 工序Ⅲ 拉孔。 工序Ⅳ 粗銑右端面。 工序Ⅴ 校正。 工序VI 粗銑叉腳兩側(cè)面。 工序VII 粗銑叉腳內(nèi)側(cè)。 工序VIII 銑槽。 工序IX 鉆小孔。 工序X 校正。 工序XI 半精銑叉腳兩側(cè)面。 工序XII 鉗工倒角,修毛刺。 工序XIII 總檢入庫。 2. 工藝路線方案二 工序Ⅰ 粗銑左端面, 工序II 鉆孔至。 工序III 拉孔。 工
34、序IV 粗銑右端面。 工序V 校正。 工序VI 粗銑叉腳內(nèi)側(cè)。 工序VII 粗銑叉腳兩側(cè)面。 工序VIII 銑槽。 工序IX 鉆小孔。 工序X 校正。 工序XI 半精銑叉腳兩側(cè)面。 工序XII 鉗工倒角,修毛刺。 工序XIII 總檢入庫。 3. 工藝路線方案三 工序Ⅰ 粗銑左端面 工序II 鉆孔至。 工序III 拉孔。 工序IV 粗銑右端面。 工序V 校正。 工序VI 粗銑叉腳兩側(cè)面。
35、 工序VII 半精銑叉腳兩側(cè)面。 工序VIII 粗銑叉腳內(nèi)側(cè)。 工序IX 銑槽。 工序X 鉆小孔。 工序XI 校正。 工序XII 鉗工倒角,修毛刺。 工序XIII 總檢入庫。 2.4.4 工藝方案的比較與分析 上述四個工藝方案的特點在于:方案一第一步是以外圓及K面為基準(zhǔn)粗銑左端面,鉆孔至;第二步是拉孔;第三步以內(nèi)孔及左端面為基準(zhǔn),銑右端面、和叉腳兩側(cè);第四步是以叉腳左側(cè)H面、外側(cè)面及內(nèi)孔為定位基準(zhǔn)粗銑叉腳內(nèi)側(cè);第五步是以內(nèi)孔及左端面、叉腳內(nèi)右側(cè)為定位基準(zhǔn)來銑槽和鉆小孔;第六步
36、是以內(nèi)孔和左端面為定位基準(zhǔn)來半精銑叉腳兩側(cè)面,最后是鉗工倒角,修毛刺。方案二與方案一的不同之處是方案三的工序VI是粗銑叉腳內(nèi)側(cè),工序VII是粗銑叉腳兩側(cè)面,而方案一的是工序VI粗銑叉腳兩側(cè)面,工序VII粗銑叉腳內(nèi)側(cè)。方案三與方案一的不同之處在于方案三工序中粗銑叉腳兩側(cè)面后直接半精銑的叉腳兩側(cè)面,然后才粗銑叉腳內(nèi)側(cè),而方案一是粗銑叉腳兩側(cè)面后直接粗銑叉腳內(nèi)側(cè),然后在后面的工序中才半精銑的叉腳兩側(cè)面。 三種方案相比較,可以看出:方案一中遵循“先粗后精”原則,先安排粗加工工序,后安排精加工工序,并且在加工過程中以左端面為定位基準(zhǔn)進行多次加工,遵循了統(tǒng)一基準(zhǔn)原則,另外把粗銑叉腳面安排在銑叉腳內(nèi)側(cè)面之
37、前,為銑內(nèi)側(cè)面提供了精基準(zhǔn)面,銑內(nèi)側(cè)面時可用孔右端面為基準(zhǔn),夾緊力指向右端面面,靠近加工面,不會因工件剛性差、切削力大而產(chǎn)生變形,半精銑叉腳面安排在最后進行,以保證加工精度不致遭到破壞;方案二中把粗銑叉腳內(nèi)側(cè)放在了粗銑叉腳兩側(cè)面的前面,不能為銑內(nèi)側(cè)提供精基準(zhǔn),保證不了叉腳內(nèi)側(cè)面的精度。方案三中把精銑叉腳兩側(cè)面放在粗銑叉腳內(nèi)側(cè)之前,在后續(xù)的工序中叉腳兩側(cè)面容易遭到破壞,影響其表面的精度。因此,我選用方案一做為手扶拖拉機副變速撥叉的的加工工藝路線: 工序I 以外圓及右端面為粗基準(zhǔn),粗銑左端面。選用X51立式銑床及專用夾具加工,采用硬質(zhì)合金端銑刀YG8。 工序II 以外圓及K面為
38、粗基準(zhǔn),鉆孔至。選用Z525立式鉆床及專用夾具,采用莫氏圓錐號為1號的硬質(zhì)合金錐柄麻花鉆。 工序III 以內(nèi)孔基準(zhǔn),拉孔。選用L6110臥式內(nèi)拉床及專用夾具,采用圓孔拉刀。 工序IV 銑孔右端面,以外圓及左端面為基準(zhǔn)。選用X51立式銑床及專用夾具加工,采用硬質(zhì)合金端銑刀YG8。 工序V 校正。 工序VI 粗銑叉腳兩側(cè)面,以右端面及內(nèi)孔作為定位基準(zhǔn)。選用X51立式銑床及專用夾具加工。 工序VII 粗銑叉腳內(nèi)側(cè),以右端面及內(nèi)孔作為定位基準(zhǔn)。選用X51立式銑床及專用夾具加工。 工序VIII 銑槽,以內(nèi)孔及左端面為定位基準(zhǔn)。選用X51立式銑床及專用夾
39、具加工。 工序IX 鉆小孔,以內(nèi)孔及左端面為定位基準(zhǔn)。選用Z525立式鉆床及專用夾具。 工序X 校正。 工序XI 半精銑叉腳兩側(cè)面,以右端面及內(nèi)孔作為定位基準(zhǔn)。選用X51立式銑床及專用夾具加工。 工序XII 鉗工倒角,修毛刺。 工序XIII 總檢入庫。 2.4.5 選擇加工設(shè)備與工藝裝備 1. 選擇機床 1)工序I、IV、VI、VII、VIII為粗銑,且精度要求不高,選用最常用的X51。 2)工序III為拉孔,可選用L6110臥式內(nèi)拉床。 3)工序II、IX為鉆孔,精度要求不高,選用Z525立式鉆床。 4)
40、工序XI為半精銑叉腳兩側(cè)面,選用X51立式銑床。 2. 選擇夾具 在各工序中由于是大批量生產(chǎn),所以都采用專用夾具。 3. 選擇量具 本零件屬于大批生產(chǎn),一般采用通用量具,對于精度要求高,不易測量的可采用專用量具。選擇量具的方法有兩種:一是按計量器具的不確定度選擇;二是按計量器具的測量方法極限誤差選擇。選擇時,采用其中的一種方法即可。 1)選擇各軸向測量量具 工序IV中要保證24圓柱兩端面的距離為70mm,且未標(biāo)注公差,取IT12級,由[12]表1.4可知T=0.30mm,按計量器具的不確定度選擇該表面加工時所用的量具,由[1]表5.1-1可查的它所對應(yīng)的不確定允許值為0.016mm
41、,所以根據(jù)[1]表5.2-6可選分度值為0.02mm的游標(biāo)卡尺。即取測量范圍為0-150mm,分度值為0.02mm的游標(biāo)卡尺。在此工序中,還要保證撥叉腳的厚度為12mm,未標(biāo)注公差,取IT14級,由[12]表1.4可知T=0.43mm,由[1]表5.1-1可查的它所對應(yīng)的不確定允許值為0.029mm,所用的量具為分度值為0.02mm的游標(biāo)卡尺。即取測量范圍為0-150mm,所以根據(jù)[1]表5.2-6可選分度值為0.02mm的游標(biāo)卡尺。兩個外部軸向測量在同一工序中,故可采用其中一個精度較高的游標(biāo)卡尺即可,故選用范圍為0-150mm,分度值為0.02mm的游標(biāo)卡尺。 工序VI和工序XI中 ,加
42、工撥叉的左側(cè),且保證與24mm圓柱左端面的距離為5mm,由于未標(biāo)注公差,取IT14級,由[12]表1.4可知T=0.30mm,由[1]表5.1-1可查的它所對應(yīng)的不確定允許值為0.016mm,故選用的量具為分度值為0.01mm的游標(biāo)卡尺,測量范圍為0-50mm。加工撥叉的右側(cè),且保證撥叉厚度為mm,此時T=0.12mm,公差等級為IT12級,由[1]表5.1-1可查的它所對應(yīng)的不確定允許值為0.09mm,故選用的量具為分度值為0.01mm的游標(biāo)卡尺,測量范圍為0-50mm。 2)選擇加工孔用量具 工序Ⅱ、III中孔的加工,鉆孔至13.5mm,拉孔至mm。 (1)鉆孔時采用標(biāo)準(zhǔn)鉆頭,且
43、其精度要求低,可不需要量具; (2)拉孔時,由于精度要求較高,加工每個工件都要進行測量,故宜選擇極限量規(guī),通規(guī)和止規(guī)。 工序IX中,鉆8.7mm的內(nèi)孔時由于采用標(biāo)準(zhǔn)鉆頭,且其精度要求低,可不需要量具。 3)選擇加工槽所用的量具 銑槽時,由于采用了標(biāo)準(zhǔn)刀具,平時無需測量,但刀具磨損到一定時候時,應(yīng)進行測量以便及時更換刀具,此時可以選擇通用量具。槽的精度為12級,T=0.18mm, 其不確定允許值為0.009mm,故選用的量具為分度值為0.02mm的游標(biāo)卡尺,測量范圍為0-150mm。 2.4.6 確定加工余量,工序尺寸及公差 確定工序尺寸的一般方法,由表面加工的最后
44、工序往前推,最后工序的工序尺寸按零件圖的要求標(biāo)準(zhǔn),如表2.4。當(dāng)無基準(zhǔn)轉(zhuǎn)換時,與統(tǒng)一表面多車加工的工序尺寸(或工步)的加工余量有關(guān)。當(dāng)基準(zhǔn)不重合時,工序尺寸應(yīng)用尺寸鏈計算。 表2.4 各個工序加工余量,精度等級 工序號 加工表面 加工內(nèi)容 加工余量(mm) 精度等級(CT) 工序尺寸(mm) 表面粗糙度 工序余量(mm) 工序Ⅰ 左端面 粗銑 3 12 73 25 0 工序II 孔 鉆 13.5 11 13.5 0.5 工序III 孔 拉孔 0.5 9 14 3.2 0 工序IV 右端面 粗銑 3 12 70
45、25 0 工序VI 叉腳左側(cè)面 粗銑 2 12 10 1 叉腳右側(cè)面 粗銑 2 12 8 1 工序VII 叉腳內(nèi)側(cè) 粗銑 6 12 34 12.5 0 工序VIII 槽 粗銑 14 12 14 12.5 0 工序IX 孔 鉆 8.7 10 8.7 25 0 工序XI 叉腳左側(cè)面 半精銑 1 8 7 0 叉腳右側(cè)面 半精銑 1 8 6 6.3 0 2.5 確定切削用量及切削時間 2.5.1 粗銑左端面 加工條件:被加工材料QT200,其抗拉強度為200MPa。零件大小
46、x=70mm,y=96mm。 1. 刀具選擇:選擇硬質(zhì)合金端銑刀YG8,其參數(shù)d=50mm,孔徑D=22mm,L=50mm,背吃刀量,,齒數(shù)12。根據(jù)[9]表4-2確定銑刀角度,選擇前角,后角,主偏角,螺旋角。 2. 切屑深度:因為加工余量較小,一次走刀即可完成。 即。 3. 確定每齒進給量f和切削速度。查[9]表4-5知當(dāng)工藝系統(tǒng)剛性中等、硬質(zhì)合金銑刀加工鑄鐵時,其每齒進給量 。由于本工序被吃刀量和銑削寬度較小,故選擇最大的每齒進給量,即=0.30mm/z。 根據(jù)所知的工件材料為QT200,根據(jù)[2]表8-99,選擇切削速度=70m/min。 4. 計算主軸轉(zhuǎn)速。
47、查[1]表4.2-36得n=490r/min,同時查表4.2-35得電動機功率:4.5kw,然后計算實際切削速度: 5. 基本時間的確定。按[1]表6.2-7知: T=(l+l+l)/f (式2.2) l=0.5d- 其中() l=4 式中:Z---銑刀齒數(shù); ---銑刀每齒進給量(mm/z); ---工作臺的水平進給量(mm/min); ---切削寬度(垂直于銑刀軸線方向測量的切削層尺寸)(mm); ---切削深度(平行于銑刀軸線方向測量的切
48、削層尺寸)(mm); d---銑刀直徑(mm); l---切削加工長度(mm); ---刀具切入長度(mm); ---刀具切出長度(mm); n---機床主軸轉(zhuǎn)速(r/min)。 查[1]表4.2-35,選用=30mm/min,把已知數(shù)據(jù)代入以上各式解得: T1.5min 故粗銑左端面的基本時間為: T=1.5min 輔助時間:=0.2T=0.3min. 工作地服務(wù)時間:=15.9%T0.24min 工時定額:T=2.04min 2.5.2 鉆孔至 1. 選擇刀具:莫氏圓錐號為1號的硬質(zhì)合金錐柄麻花鉆。根據(jù)[1]表3.1-6選取。麻花鉆
49、參數(shù)螺旋角,頂角,橫刃斜角,進給后角。 2. 確定背吃刀量 鉆孔時,。 3. 確定進給量 按照加工要求決定進給量。鉆頭直徑,工件材料為鑄鐵且時,根據(jù)[9]式5-3進給量取值范圍為0.12~0.24mm/r。 在此取0.2mm/r。 4. 確定切削速度 根據(jù)[9]表5-1知切削速度為25~30m/min ,在此選30m/min。 則: 根據(jù)Z525機床標(biāo)準(zhǔn)主軸轉(zhuǎn)速,由[1]表4.2-15選取,實際轉(zhuǎn)速為: 5. 基本時間 由[1]表6.2-5得鉆孔的基本時間為:
50、 (式2.3) 式中: ——工件切削部分長度,單位為mm; ——切入量,單位為mm,; ——切出量,單位為mm,; 已知,,,,。所以,加工的孔所用的基本時間為: 輔助時間:=0.2=0.12min. 工作地服務(wù)時間:=15.7%0.09min 工時定額: 2.5.3 拉孔至14mm 1. 選擇刀具:根據(jù)[1]表3.1-24選取d=14mm,L=385mm的圓孔拉刀作為刀具。 2. 確定背吃刀量 鉆孔時 。
51、 3. 確定進給量 按照加工要求決定進給量。鉆頭直徑,工件材料為鑄鐵且時,根據(jù)[9]式5-3進給量取值范圍為0.12~0.24mm/r。 在此取0.2mm/r。 4. 確定切削速度 根據(jù)[9]表5-1知切削速度為25~30m/min ,在此選30m/min。 則: 根據(jù)Z525機床標(biāo)準(zhǔn)主軸轉(zhuǎn)速,由[1]表4.2-15選取,實際轉(zhuǎn)速為: 5. 基本時間 由[1]表6.2-5得拉孔的基本時間為: 式中 已知,,,,。所以,拉孔至所用的基本時間為: 輔助時間:=0.2=0.1
52、12min. 工作地服務(wù)時間:=15.7%0.1min 工時定額: 2.5.4 粗銑右端面 1. 刀具選擇:選擇硬質(zhì)合金端銑刀YG8,其參數(shù)d=50mm,孔徑D=22mm,L=50mm,背吃刀量,,齒數(shù)12。根據(jù)[9]表4-2確定銑刀角度,選擇前角,后角,主偏角,螺旋角。 2. 切屑深度:因為加工余量較小,一次走刀即可完成,即。 3. 確定每齒進給量f和切削速度。查[9]表4-5知當(dāng)工藝系統(tǒng)剛性中等、硬質(zhì)合金銑刀加工鑄鐵時,其每齒進給量 。由于本工序被吃刀量和銑削寬度較小,故選擇最大的每齒進給量,即=0.30mm/z。 根據(jù)所知的工件材料為QT200,根據(jù)[2]表8-9
53、9,選擇切削速度=70m/min。 4. 計算主軸轉(zhuǎn)速。查[1]表4.2-36得n=490r/min,同時查表4.2-35得電動機功率:4.5kw,然后計算實際切削速度 5. 基本時間的確定。按[1]表6.2-7可得: l=0.5d- 其中() =0.550-)+2 17 l=4 查[1]表4.2-35,選用=30mm/min,則: T=(l+l+l)/f =(24+17+4)30
54、 1.5min 故粗銑左端面的基本時間為: T=1.5min 輔助時間:=0.2T=0.3min. 工作地服務(wù)時間:=15.9%T0.24min 工時定額:T=2.04min 2.5.5 粗銑叉腳兩側(cè)面 該工序分兩個工步,工步1是粗銑撥叉腳左端面;工步2是粗銑撥叉腳右端面。它們所選用的背吃刀量、切削速度和進給量是一樣的。 1. 刀具選擇:選擇硬質(zhì)合金端銑刀YG8,其參數(shù)d=50mm,孔徑D=22mm,L=50mm,背吃刀量,,齒數(shù)12。根據(jù)[9]表4-2確定銑刀角度,選擇前角,后角,主偏角,螺旋角。 2. 切屑深度:因為加
55、工余量較小,一次走刀即可完成。 即。 3. 確定每齒進給量f和切削速度。查[9]表4-5知當(dāng)工藝系統(tǒng)剛性中等、硬質(zhì)合金銑刀加工鑄鐵時,其每齒進給量 。由于本工序被吃刀量和銑削寬度較小,故選擇最大的每齒進給量,即=0.30mm/z。 根據(jù)所知的工件材料為QT200,根據(jù)[2]表8-99,選擇切削速度=70m/min。 4. 計算主軸轉(zhuǎn)速。查[1]表4.2-36得n=490r/min,同時查表4.2-35得電動機功率:4.5kw,然后計算實際切削速度 5. 基本時間的確定。按[1]表6.2-7。 l=0.5d- 其中()
56、 =0.550-)+2 17 l=4 查[1]表4.2-35,選用=30mm/min T=(l+l+l)/f =(62+17+4)30 2.8min 故粗銑
57、叉腳兩側(cè)面的基本時間為: T=2T=5.6min 輔助時間:=0.2T=1.12min. 工作地服務(wù)時間:=15.9%T0.89min 工時定額:T=7.61min 2.5.6 粗銑叉腳內(nèi)側(cè) 該工序分兩個工步,工步1是粗銑撥叉腳左內(nèi)表面;工步2是粗銑撥叉腳右內(nèi)表面,它們所選用的背吃刀量、切削速度和進給量是一樣的。 1. 刀具選擇:選高速鋼鑲齒套式面銑刀銑平面,=80mm,D=27,L=36,=16,。根據(jù)[9]表4-2確定銑刀角度,選擇前角=,后角=,主偏角=,螺旋角=。 2. 切屑深度:因為加工余量較小,一次走刀即可完成。 即。 3. 確定每齒進給量f和切削速度。
58、查[9]表4-5知當(dāng)工藝系統(tǒng)剛性中等、高速鋼銑刀加工鑄鐵時,其每齒進給量 。由于本工序被吃刀量和銑削寬度較小,故選擇最大的每齒進給量,即=0.20mm/z。 根據(jù)所知的工件材料為QT200,根據(jù)[2]表8-99,選擇切削速度=18m/min。 4. 計算主軸轉(zhuǎn)速。由切削速度=18m/min 則: 查[1]表4.2-36得n=80r/min,同時查表4.2-35得電動機功率:4.5kw,然后計算實際切削速度 5. 基本時間的確定。按[1]表6.2-7。 l=0.5d- 其中()
59、 =0.580-)+2 25 l=4 查[1]表4.2-35,選用=50mm/min T=(l+l+l)/f =(6+25+4)50 =0.7min 故粗銑叉腳內(nèi)側(cè)的基本時間為: T=2T=1.4min 輔助時間:=0.2T=0.28min. 工作地服務(wù)時間=15.9%T0.22min 工時定額T=1.9min 2.5.7 銑槽 1. 刀具選擇::直柄鍵槽銑刀(G
60、B1112-85),直徑d=8,L=50mm,l=14mm,=8mm,。 2. 切屑深度:因為加工余量較大,需三次走刀才可完成。 即取。 3. 確定切削速度。根據(jù)所知的工件材料為QT200,根據(jù)[2]表8-99,選擇切削速度=18m/min。 4. 計算主軸轉(zhuǎn)速。由切削速度=18m/min 則: 查[1]表4.2-36得n=100r/min,同時查表4.2-35得電動機功率:4.5kw,然后計算實際切削速度 5. 基本時間的確定。按[1]表6.2-7。
61、 T= (式2.4) l=2 式中:Z---銑刀齒數(shù); ---銑刀每齒進給量(mm/z); ---工作臺的水平進給量(mm/min); ---切削寬度(垂直于銑刀軸線方向測量的切削層尺寸)(mm); ---切削深度(平行于銑刀軸線方向測量的切削層尺寸)(mm); d---銑刀直徑(mm); l---切削加工長度(mm); ---刀具切入長度(mm); ---刀具切出長度(mm); h---鍵槽深度; n---機床主軸轉(zhuǎn)速(r/mi
62、n)。 查[1]表4.2-35,選用=25mm/min,則: T= = =1.12min 故銑槽的基本時間為: T=1.12min 輔助時間:=0.2T=0.224min. 工作地服務(wù)時間:=15.9%T0.18min 工時定額:T=1.524min 2.5.8 鉆小孔 1. 選擇刀具:根據(jù)[1]表3.1-6選取高速鋼直柄麻花鉆(GB1436-85),d=8.7mm,l=125mm,=81mm。麻花鉆參數(shù)螺旋角,頂角,橫刃斜角,進給后角。 2. 確定背吃刀量 鉆孔時,。 3. 確定進給量 按照加工要求決定進給量。鉆
63、頭直徑,工件材料為鑄鐵且時,根據(jù)[9]式5-3進給量取值范圍為0.087~0.174mm/r。 在此取0.1mm/r。 4. 確定切削速度 根據(jù)[9]表5-1知切削速度為20~25m/min ,在此選25m/min。 則: 根據(jù)Z525機床標(biāo)準(zhǔn)主軸轉(zhuǎn)速,由[1]表4.2-15選取,實際轉(zhuǎn)速為: 5. 基本時間 由[1]表6.2-5得鉆孔的基本時間為: (式2.5) 式中,——工件切削部分長度,單位為
64、mm; ——切入量,單位為mm,; ——切出量,單位為mm,; 已知,,,,。所以,加工的孔所用的基本時間為: 輔助時間:=0.2=0.108min. 工作地服務(wù)時間=15.7%0.08min. 工時定額 2.5.9 半精銑叉腳兩側(cè)面 該工序分兩個工步,工步1是半精銑撥叉腳左端面;工步2是半精銑撥叉腳右端面。它們所選用的背吃刀量、切削速度和進給量是一樣的。 1. 刀具選擇:選擇硬質(zhì)合金端銑刀YG8,其參數(shù)d=50mm,孔徑D=22mm,L=50mm,背吃刀量,,齒數(shù)12。根據(jù)[9]表4-2確定銑刀角度,選擇前角。 2. 切屑深度:因為加工余量較小,一
65、次走刀即可完成。 即。 3. 確定每齒進給量f和切削速度。查[9]表4-5知當(dāng)工藝系統(tǒng)剛性中等、硬質(zhì)合金銑刀加工鑄鐵時,其每齒進給量 。由于本工序被吃刀量和銑削寬度較小,故選擇最大的每齒進給量,即=0.30mm/z。 根據(jù)所知的工件材料為QT200,根據(jù)[2]表8-99,選擇切削速度=70m/min。 4. 計算主軸轉(zhuǎn)速。查[1]表4.2-36得n=490r/min,同時查表4.2-35得電動機功率:4.5kw,然后計算實際切削速度 5. 基本時間的確定。按[1]表6.2-7。 l=0.5d- 其中()
66、 =0.550-)+2 17 l=4 查[1]表4.2-35,選用=30mm/min T=(l+l+l)/f =(62+17+4)30 2.8min 故半精銑叉腳兩側(cè)面的基本時間為: T=2T=5.6min 輔助時間:=0.2T=1.12min. 工作地服務(wù)時間:=15.9%T0.89min. 工時定額:T=7.61min. 第3章 專用鉆床夾具設(shè)計 撥叉機構(gòu)形狀復(fù)雜,剛性差,易變形,需采用專用夾具進行加工。常見的有車床夾具、鉆床夾具和銑床夾具等,本次設(shè)計的專用夾具為鉆床夾具。 3.1 明確設(shè)計任務(wù)、設(shè)計分析原始材料 3.1.1 加工工件的零件圖 加工工件的零件圖如圖2.2。 3.1.2 撥叉工件的主要加工工藝過程 撥叉工件的主要加工工藝過程如表3.1所示: 表3.1 撥叉工件的主要加工工藝過程 序號 工序內(nèi)容 使用設(shè)備 序號 工序內(nèi)容 使
- 溫馨提示:
1: 本站所有資源如無特殊說明,都需要本地電腦安裝OFFICE2007和PDF閱讀器。圖紙軟件為CAD,CAXA,PROE,UG,SolidWorks等.壓縮文件請下載最新的WinRAR軟件解壓。
2: 本站的文檔不包含任何第三方提供的附件圖紙等,如果需要附件,請聯(lián)系上傳者。文件的所有權(quán)益歸上傳用戶所有。
3.本站RAR壓縮包中若帶圖紙,網(wǎng)頁內(nèi)容里面會有圖紙預(yù)覽,若沒有圖紙預(yù)覽就沒有圖紙。
4. 未經(jīng)權(quán)益所有人同意不得將文件中的內(nèi)容挪作商業(yè)或盈利用途。
5. 裝配圖網(wǎng)僅提供信息存儲空間,僅對用戶上傳內(nèi)容的表現(xiàn)方式做保護處理,對用戶上傳分享的文檔內(nèi)容本身不做任何修改或編輯,并不能對任何下載內(nèi)容負(fù)責(zé)。
6. 下載文件中如有侵權(quán)或不適當(dāng)內(nèi)容,請與我們聯(lián)系,我們立即糾正。
7. 本站不保證下載資源的準(zhǔn)確性、安全性和完整性, 同時也不承擔(dān)用戶因使用這些下載資源對自己和他人造成任何形式的傷害或損失。
最新文檔
- 6.煤礦安全生產(chǎn)科普知識競賽題含答案
- 2.煤礦爆破工技能鑒定試題含答案
- 3.爆破工培訓(xùn)考試試題含答案
- 2.煤礦安全監(jiān)察人員模擬考試題庫試卷含答案
- 3.金屬非金屬礦山安全管理人員(地下礦山)安全生產(chǎn)模擬考試題庫試卷含答案
- 4.煤礦特種作業(yè)人員井下電鉗工模擬考試題庫試卷含答案
- 1 煤礦安全生產(chǎn)及管理知識測試題庫及答案
- 2 各種煤礦安全考試試題含答案
- 1 煤礦安全檢查考試題
- 1 井下放炮員練習(xí)題含答案
- 2煤礦安全監(jiān)測工種技術(shù)比武題庫含解析
- 1 礦山應(yīng)急救援安全知識競賽試題
- 1 礦井泵工考試練習(xí)題含答案
- 2煤礦爆破工考試復(fù)習(xí)題含答案
- 1 各種煤礦安全考試試題含答案